Information injection-pump assembly
BOSCH
F 019 Z10 744
f019z10744
ZEXEL
106991-1296
1069911296
ISUZU
1156029942
1156029942
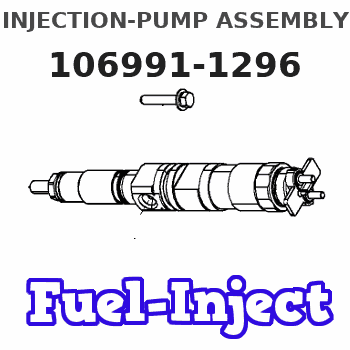
Rating:
Service parts 106991-1296 INJECTION-PUMP ASSEMBLY:
1.
_
6.
COUPLING PLATE
7.
COUPLING PLATE
8.
_
9.
_
11.
Nozzle and Holder
12.
Open Pre:MPa(Kqf/cm2)
15.7(160)/22.1(225)
15.
NOZZLE SET
Include in #1:
106991-1296
as INJECTION-PUMP ASSEMBLY
Cross reference number
BOSCH
F 019 Z10 744
f019z10744
ZEXEL
106991-1296
1069911296
ISUZU
1156029942
1156029942
Zexel num
Bosch num
Firm num
Name
Calibration Data:
Adjustment conditions
Test oil
1404 Test oil ISO4113 or {SAEJ967d}
1404 Test oil ISO4113 or {SAEJ967d}
Test oil temperature
degC
40
40
45
Nozzle and nozzle holder
105780-8140
Bosch type code
EF8511/9A
Nozzle
105780-0000
Bosch type code
DN12SD12T
Nozzle holder
105780-2080
Bosch type code
EF8511/9
Opening pressure
MPa
17.2
Opening pressure
kgf/cm2
175
Injection pipe
Outer diameter - inner diameter - length (mm) mm 8-3-600
Outer diameter - inner diameter - length (mm) mm 8-3-600
Overflow valve (drive side)
134424-4320
Overflow valve opening pressure (drive side)
kPa
255
221
289
Overflow valve opening pressure (drive side)
kgf/cm2
2.6
2.25
2.95
Overflow valve (governor side)
134424-2720
Overflow valve opening pressure (governor side)
kPa
255
221
289
Overflow valve opening pressure (governor side)
kgf/cm2
2.6
2.25
2.95
Tester oil delivery pressure
kPa
157
157
157
Tester oil delivery pressure
kgf/cm2
1.6
1.6
1.6
Direction of rotation (viewed from drive side)
Right R
Right R
Injection timing adjustment
Direction of rotation (viewed from drive side)
Right R
Right R
Injection order
1-8-7-6-
5-4-3-10
-9-2
Pre-stroke
mm
4.2
4.17
4.23
Rack position
Point A R=A
Point A R=A
Beginning of injection position
Governor side NO.1
Governor side NO.1
Difference between angles 1
Cal 1-8 deg. 27 26.75 27.25
Cal 1-8 deg. 27 26.75 27.25
Difference between angles 2
Cal 1-7 deg. 72 71.75 72.25
Cal 1-7 deg. 72 71.75 72.25
Difference between angles 3
Cal 1-6 deg. 99 98.75 99.25
Cal 1-6 deg. 99 98.75 99.25
Difference between angles 4
Cal 1-5 deg. 144 143.75 144.25
Cal 1-5 deg. 144 143.75 144.25
Difference between angles 5
Cal 1-4 deg. 171 170.75 171.25
Cal 1-4 deg. 171 170.75 171.25
Difference between angles 6
Cal 1-3 deg. 216 215.75 216.25
Cal 1-3 deg. 216 215.75 216.25
Difference between angles 7
Cal 1-10 deg. 243 242.75 243.25
Cal 1-10 deg. 243 242.75 243.25
Difference between angles 8
Cal 1-9 deg. 288 287.75 288.25
Cal 1-9 deg. 288 287.75 288.25
Difference between angles 9
Cyl.1-2 deg. 315 314.75 315.25
Cyl.1-2 deg. 315 314.75 315.25
Injection quantity adjustment
Adjusting point
A
Rack position
8.5
Pump speed
r/min
800
800
800
Average injection quantity
mm3/st.
110
108.5
111.5
Max. variation between cylinders
%
0
-2
2
Basic
*
Fixing the lever
*
Injection quantity adjustment_02
Adjusting point
C
Rack position
7.9
Pump speed
r/min
1150
1150
1150
Average injection quantity
mm3/st.
117.4
115.4
119.4
Fixing the lever
*
Injection quantity adjustment_03
Adjusting point
D
Rack position
4.9+-0.5
Pump speed
r/min
225
225
225
Average injection quantity
mm3/st.
8.8
7.5
10.1
Max. variation between cylinders
%
0
-13
13
Fixing the rack
*
Timer adjustment
Pump speed
r/min
600--
Advance angle
deg.
0
0
0
Remarks
Start
Start
Timer adjustment_02
Pump speed
r/min
550
Advance angle
deg.
0.3
Timer adjustment_03
Pump speed
r/min
800+-30
Advance angle
deg.
2
1.5
2.5
Timer adjustment_04
Pump speed
r/min
870
Advance angle
deg.
2
1.7
2.3
Timer adjustment_05
Pump speed
r/min
(1050)
Advance angle
deg.
3.5
3
4
Timer adjustment_06
Pump speed
r/min
1150
Advance angle
deg.
5.5
5
6
Remarks
Finish
Finish
Test data Ex:
Governor adjustment
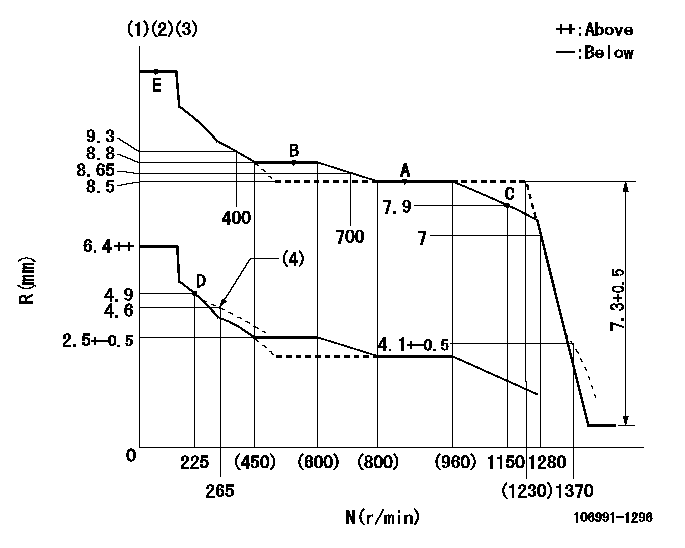
N:Pump speed
R:Rack position (mm)
(1)Lever ratio: RT
(2)Target shim dimension: TH
(3)Tolerance for racks not indicated: +-0.05mm.
(4)Damper spring setting
----------
RT=0.8 TH=2mm
----------
----------
RT=0.8 TH=2mm
----------
Speed control lever angle

F:Full speed
----------
----------
a=7deg+-5deg
----------
----------
a=7deg+-5deg
0000000901
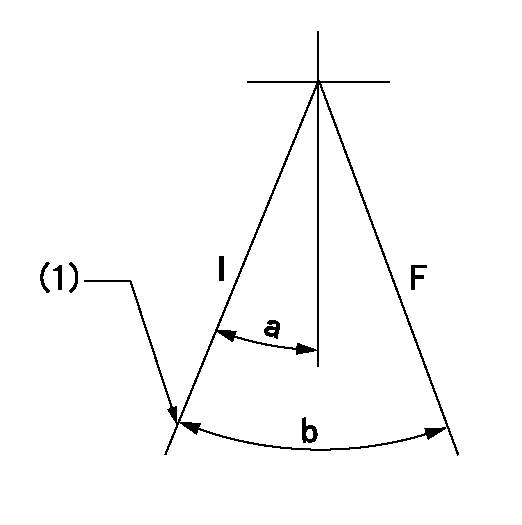
F:Full load
I:Idle
(1)Stopper bolt setting
----------
----------
a=10deg+-5deg b=34deg+-3deg
----------
----------
a=10deg+-5deg b=34deg+-3deg
Stop lever angle

N:Pump normal
S:Stop the pump.
(1)Use the hole at R = aa
----------
aa=25mm
----------
a=64deg+-5deg b=51deg+-5deg
----------
aa=25mm
----------
a=64deg+-5deg b=51deg+-5deg
Timing setting

(1)Pump vertical direction
(2)Position of "Z" mark at the No 1 cylinder's beginning of injection (governor side)
(3)B.T.D.C.: aa (set timing)
(4)-
----------
aa=8deg
----------
a=(180deg)
----------
aa=8deg
----------
a=(180deg)
Information:
Altitude Operation
The fuel system settings and altitude limits are stamped on the engine information plate. When an engine is moved to a higher altitude, these settings must be changed by your Caterpillar dealer in order to prevent damaging the turbocharger, and to provide maximum engine efficiency. If the engine is moved to a lower altitude than that which is stamped on the engine information plate, the engine can be operated safely; however, it will deliver less than rated horsepower, and the fuel settings should be changed by your Caterpillar dealer to obtain rated horsepower.Stopping
1. Flywheel clutch operation: Quickly pull the clutch lever to the released position. For electric set operation, see the GENERATOR SET OPERATION instructions. For Woodward Governor operation, see the topic, WOODWARD GOVERNORS, Stopping the Engine. 2. Reduce engine speed to half speed. Run for 5 minutes to cool engine.3. Reduce engine speed to low idle.4. Observe the crankcase oil level while the engine is idling. Maintain the oil level between the ADD and FULL marks on the side of the dipstick stamped, CHECK WITH ENGINE RUNNING. See the LUBRICATION AND MAINTENANCE SECTION.5. Stop the engine. After Stopping Checks And Procedures
1. Fill the fuel tank. See the LUBRICATION AND MAINTENANCE SECTION: Fuel Tank Maintenance.2. Drain the raw water system if below freezing temperatures are expected; see: Draining Raw Water System.3. If below freezing temperatures are expected, allow the engine jacket water expansion tank to cool; then check the coolant for proper antifreeze protection. Add permanent-type antifreeze, if required.4. Repair any leaks, make major adjustments, tighten loose bolts, etc.5. Observe the Service Meter reading. Perform the periodic maintenance as instructed in the LUBRICATION AND MAINTENANCE CHART.
SERVICE METER
The fuel system settings and altitude limits are stamped on the engine information plate. When an engine is moved to a higher altitude, these settings must be changed by your Caterpillar dealer in order to prevent damaging the turbocharger, and to provide maximum engine efficiency. If the engine is moved to a lower altitude than that which is stamped on the engine information plate, the engine can be operated safely; however, it will deliver less than rated horsepower, and the fuel settings should be changed by your Caterpillar dealer to obtain rated horsepower.Stopping
1. Flywheel clutch operation: Quickly pull the clutch lever to the released position. For electric set operation, see the GENERATOR SET OPERATION instructions. For Woodward Governor operation, see the topic, WOODWARD GOVERNORS, Stopping the Engine. 2. Reduce engine speed to half speed. Run for 5 minutes to cool engine.3. Reduce engine speed to low idle.4. Observe the crankcase oil level while the engine is idling. Maintain the oil level between the ADD and FULL marks on the side of the dipstick stamped, CHECK WITH ENGINE RUNNING. See the LUBRICATION AND MAINTENANCE SECTION.5. Stop the engine. After Stopping Checks And Procedures
1. Fill the fuel tank. See the LUBRICATION AND MAINTENANCE SECTION: Fuel Tank Maintenance.2. Drain the raw water system if below freezing temperatures are expected; see: Draining Raw Water System.3. If below freezing temperatures are expected, allow the engine jacket water expansion tank to cool; then check the coolant for proper antifreeze protection. Add permanent-type antifreeze, if required.4. Repair any leaks, make major adjustments, tighten loose bolts, etc.5. Observe the Service Meter reading. Perform the periodic maintenance as instructed in the LUBRICATION AND MAINTENANCE CHART.
SERVICE METER