Information injection-pump assembly
BOSCH
9 400 618 683
9400618683
ZEXEL
106971-2030
1069712030
MITSUBISHI
ME091100
me091100
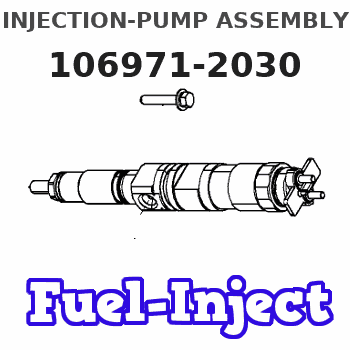
Rating:
Service parts 106971-2030 INJECTION-PUMP ASSEMBLY:
1.
_
7.
COUPLING PLATE
8.
_
9.
_
11.
Nozzle and Holder
ME066565
12.
Open Pre:MPa(Kqf/cm2)
17.7{180}/21.6{220}
15.
NOZZLE SET
Include in #1:
106971-2030
as INJECTION-PUMP ASSEMBLY
Cross reference number
BOSCH
9 400 618 683
9400618683
ZEXEL
106971-2030
1069712030
MITSUBISHI
ME091100
me091100
Zexel num
Bosch num
Firm num
Name
106971-2030
9 400 618 683
ME091100 MITSUBISHI
INJECTION-PUMP ASSEMBLY
10DC9T2 * K 14CE INJECTION PUMP ASSY PE10P PE
10DC9T2 * K 14CE INJECTION PUMP ASSY PE10P PE
Calibration Data:
Adjustment conditions
Test oil
1404 Test oil ISO4113 or {SAEJ967d}
1404 Test oil ISO4113 or {SAEJ967d}
Test oil temperature
degC
40
40
45
Nozzle and nozzle holder
105780-8140
Bosch type code
EF8511/9A
Nozzle
105780-0000
Bosch type code
DN12SD12T
Nozzle holder
105780-2080
Bosch type code
EF8511/9
Opening pressure
MPa
17.2
Opening pressure
kgf/cm2
175
Injection pipe
Outer diameter - inner diameter - length (mm) mm 8-3-600
Outer diameter - inner diameter - length (mm) mm 8-3-600
Overflow valve
131424-4620
Overflow valve opening pressure
kPa
255
221
289
Overflow valve opening pressure
kgf/cm2
2.6
2.25
2.95
Tester oil delivery pressure
kPa
157
157
157
Tester oil delivery pressure
kgf/cm2
1.6
1.6
1.6
Direction of rotation (viewed from drive side)
Right R
Right R
Injection timing adjustment
Direction of rotation (viewed from drive side)
Right R
Right R
Injection order
1-2-7-8-
5-6-3-4-
9-10
Pre-stroke
mm
4.8
4.75
4.85
Beginning of injection position
Governor side NO.1
Governor side NO.1
Difference between angles 1
Cyl.1-2 deg. 45 44.5 45.5
Cyl.1-2 deg. 45 44.5 45.5
Difference between angles 2
Cal 1-7 deg. 72 71.5 72.5
Cal 1-7 deg. 72 71.5 72.5
Difference between angles 3
Cal 1-8 deg. 117 116.5 117.5
Cal 1-8 deg. 117 116.5 117.5
Difference between angles 4
Cal 1-5 deg. 144 143.5 144.5
Cal 1-5 deg. 144 143.5 144.5
Difference between angles 5
Cal 1-6 deg. 189 188.5 189.5
Cal 1-6 deg. 189 188.5 189.5
Difference between angles 6
Cal 1-3 deg. 216 215.5 216.5
Cal 1-3 deg. 216 215.5 216.5
Difference between angles 7
Cal 1-4 deg. 261 260.5 261.5
Cal 1-4 deg. 261 260.5 261.5
Difference between angles 8
Cal 1-9 deg. 288 287.5 288.5
Cal 1-9 deg. 288 287.5 288.5
Difference between angles 9
Cal 1-10 deg. 333 332.5 333.5
Cal 1-10 deg. 333 332.5 333.5
Injection quantity adjustment
Adjusting point
-
Rack position
12.8
Pump speed
r/min
700
700
700
Each cylinder's injection qty
mm3/st.
173
167.8
178.2
Basic
*
Fixing the rack
*
Standard for adjustment of the maximum variation between cylinders
*
Injection quantity adjustment_02
Adjusting point
C
Rack position
6.6+-0.5
Pump speed
r/min
225
225
225
Each cylinder's injection qty
mm3/st.
20
17
23
Fixing the rack
*
Standard for adjustment of the maximum variation between cylinders
*
Injection quantity adjustment_03
Adjusting point
A
Rack position
R1(12.8)
Pump speed
r/min
700
700
700
Average injection quantity
mm3/st.
173
172
174
Basic
*
Fixing the lever
*
Boost pressure
kPa
53.3
53.3
Boost pressure
mmHg
400
400
Injection quantity adjustment_04
Adjusting point
B
Rack position
11.7
Pump speed
r/min
1100
1100
1100
Average injection quantity
mm3/st.
155
152
158
Fixing the lever
*
Boost pressure
kPa
53.3
53.3
Boost pressure
mmHg
400
400
Injection quantity adjustment_05
Adjusting point
D
Rack position
-
Pump speed
r/min
100
100
100
Average injection quantity
mm3/st.
140
120
160
Fixing the lever
*
Boost pressure
kPa
0
0
0
Boost pressure
mmHg
0
0
0
Boost compensator adjustment
Pump speed
r/min
650
650
650
Rack position
R1-1.5
Boost pressure
kPa
6.7
6.7
6.7
Boost pressure
mmHg
50
50
50
Boost compensator adjustment_02
Pump speed
r/min
650
650
650
Rack position
R1-0.6
Boost pressure
kPa
26.7
25.4
28
Boost pressure
mmHg
200
190
210
Boost compensator adjustment_03
Pump speed
r/min
650
650
650
Rack position
R1(12.8)
Boost pressure
kPa
40
33.3
46.7
Boost pressure
mmHg
300
250
350
Timer adjustment
Pump speed
r/min
750--
Advance angle
deg.
0
0
0
Remarks
Start
Start
Timer adjustment_02
Pump speed
r/min
700
Advance angle
deg.
0.5
Timer adjustment_03
Pump speed
r/min
1100
Advance angle
deg.
3
2.5
3.5
Remarks
Finish
Finish
Test data Ex:
Governor adjustment

N:Pump speed
R:Rack position (mm)
(1)Lever ratio: RT
(2)Target shim dimension: TH
(3)Boost compensator cancel stroke: BSL
(4)Boost compensator stroke: BCL
(5)Damper spring setting: DL
----------
RT=1 TH=2.1mm BSL=1.6mm BCL=1.5+-0.1mm DL=4.8-0.2mm
----------
----------
RT=1 TH=2.1mm BSL=1.6mm BCL=1.5+-0.1mm DL=4.8-0.2mm
----------
Speed control lever angle

F:Full speed
----------
----------
a=15deg+-5deg
----------
----------
a=15deg+-5deg
0000000901

F:Full load
I:Idle
(1)Stopper bolt setting
----------
----------
a=10deg+-5deg b=34.5deg+-3deg
----------
----------
a=10deg+-5deg b=34.5deg+-3deg
Stop lever angle

N:Pump normal
S:Stop the pump.
(1)Rack position = aa
(2)Stopper bolt setting
(3)Rack position bb
(4)Free (at shipping)
----------
aa=4-0.5mm bb=14.6mm
----------
a=1.5deg+7deg-5deg b=35deg+-5deg c=(62deg)
----------
aa=4-0.5mm bb=14.6mm
----------
a=1.5deg+7deg-5deg b=35deg+-5deg c=(62deg)
0000001501 MICRO SWITCH
Adjustment of the micro-switch
Adjust the bolt to obtain the following lever position when the micro-switch is ON.
(1)Speed N1
(2)Rack position Ra
----------
N1=325+-5r/min Ra=6.1mm
----------
----------
N1=325+-5r/min Ra=6.1mm
----------
Timing setting

(1)Pump vertical direction
(2)Coupling's key groove position at No 1 cylinder's beginning of injection
(3)-
(4)-
----------
----------
a=(40deg)
----------
----------
a=(40deg)
Information:
Use of the Pickup During Wet Conditions
If the pickup becomes wet, it may operate intermittently or not at all. Although the pickup is water resistant, it is not waterproof. Water spray from rain or other sources may cause the pickup to stop producing an output signal.If this happens, the pickup should be removed from the engine and allowed to dry out thoroughly. If necessary, the pickup can be dried in an oven at approximately 50°C (122°F). After drying, the pickup should operate correctly.If it is not possible to keep the pickup dry, use the following procedure: If the pickup must be used during wet conditions, it may be possible to protect it from moisture by using a water displacing spray such as WD-40®.Remove the pickup from the engine. Thoroughly spray the pickup from all directions. Make sure the pickup is completely covered with the spray. Reinstall the pickup on the engine and check its operation.When water first contacts the pickup, the unit may stop working temporarily, but will start working again after the water has been displaced by the solution. If necessary, spray the solution on the pickup after installation on the injection line.Permanent Installation on the Engine
If the pickup is to be permanently installed on the engine, install the pickup on the fuel injection line in the usual manner. Make sure that the thumbscrew is hand tightened securely, but not over tightened. Run the engine and check the operation of the pickup.Make sure that the pickup and line are clean and dry. If the pickup is working correctly, use a can of spray paint to thoroughly paint the pickup from all directions. Several coats should be applied. Let the paint dry thoroughly before operating the engine.Checking the Operation of the Amplifier and Pickup
(1) 6V2100 Multitach. (2) 5P9698 Calibrator. (3) 5P7366 Power Cable. (4) Digital Multimeter. (5) Screwdriver. (6) 6V6152 Adapter. Screwdriver (5) should have a blade approximately 150 mm (6 in) long with 6 mm (.25 in) diameter shaft of round bare metal (not anodized or insulated).The 6V6152 Adapter (6) is a phono plug-to-BNC connector. Modifications must be made to the 5P9698 Calibrator (2). Refer to Special Instruction, SMHS7504-01.Checking the 4C6812 Amplifier
(1) 6V6152 Adapter Plug. (2) 5P9698 Calibrator. (3) 4C6812 Amplifier. (4) Connector. (5) 5P7366 Power Cable. (6) Knob. (7) Battery Indicator. (8) No Input Signal Light.1. Install 6V6152 Adapter Plug (1) on the end of the output cable on 5P9698 Calibrator (2). Plug the adapter into 4C6812 Amplifier (3).2. Check the operation of the multitach being used by performing the CHECKING PHOTO OPERATION test procedure contained in Special Instruction SEHS7807. (This is to ensure it is operating correctly on PHOTO operation.)3. Plug connector (4), on the end of the amplifier output cable, into the PH (photo) connector on the multitach. Attach 5P7366 Power Cable (5) to the multitach and to a suitable power source. Refer to SEHS7807.4. Program the multitach for .5 P/REV and to read R/MIN on the PH (photo) input. Turn knob (6) on
If the pickup becomes wet, it may operate intermittently or not at all. Although the pickup is water resistant, it is not waterproof. Water spray from rain or other sources may cause the pickup to stop producing an output signal.If this happens, the pickup should be removed from the engine and allowed to dry out thoroughly. If necessary, the pickup can be dried in an oven at approximately 50°C (122°F). After drying, the pickup should operate correctly.If it is not possible to keep the pickup dry, use the following procedure: If the pickup must be used during wet conditions, it may be possible to protect it from moisture by using a water displacing spray such as WD-40®.Remove the pickup from the engine. Thoroughly spray the pickup from all directions. Make sure the pickup is completely covered with the spray. Reinstall the pickup on the engine and check its operation.When water first contacts the pickup, the unit may stop working temporarily, but will start working again after the water has been displaced by the solution. If necessary, spray the solution on the pickup after installation on the injection line.Permanent Installation on the Engine
If the pickup is to be permanently installed on the engine, install the pickup on the fuel injection line in the usual manner. Make sure that the thumbscrew is hand tightened securely, but not over tightened. Run the engine and check the operation of the pickup.Make sure that the pickup and line are clean and dry. If the pickup is working correctly, use a can of spray paint to thoroughly paint the pickup from all directions. Several coats should be applied. Let the paint dry thoroughly before operating the engine.Checking the Operation of the Amplifier and Pickup
(1) 6V2100 Multitach. (2) 5P9698 Calibrator. (3) 5P7366 Power Cable. (4) Digital Multimeter. (5) Screwdriver. (6) 6V6152 Adapter. Screwdriver (5) should have a blade approximately 150 mm (6 in) long with 6 mm (.25 in) diameter shaft of round bare metal (not anodized or insulated).The 6V6152 Adapter (6) is a phono plug-to-BNC connector. Modifications must be made to the 5P9698 Calibrator (2). Refer to Special Instruction, SMHS7504-01.Checking the 4C6812 Amplifier
(1) 6V6152 Adapter Plug. (2) 5P9698 Calibrator. (3) 4C6812 Amplifier. (4) Connector. (5) 5P7366 Power Cable. (6) Knob. (7) Battery Indicator. (8) No Input Signal Light.1. Install 6V6152 Adapter Plug (1) on the end of the output cable on 5P9698 Calibrator (2). Plug the adapter into 4C6812 Amplifier (3).2. Check the operation of the multitach being used by performing the CHECKING PHOTO OPERATION test procedure contained in Special Instruction SEHS7807. (This is to ensure it is operating correctly on PHOTO operation.)3. Plug connector (4), on the end of the amplifier output cable, into the PH (photo) connector on the multitach. Attach 5P7366 Power Cable (5) to the multitach and to a suitable power source. Refer to SEHS7807.4. Program the multitach for .5 P/REV and to read R/MIN on the PH (photo) input. Turn knob (6) on
Have questions with 106971-2030?
Group cross 106971-2030 ZEXEL
Mitsubishi
106971-2030
9 400 618 683
ME091100
INJECTION-PUMP ASSEMBLY
10DC9T2
10DC9T2