Information injection-pump assembly
BOSCH
F 019 Z10 897
f019z10897
ZEXEL
106891-1271
1068911271
ISUZU
1156025244
1156025244
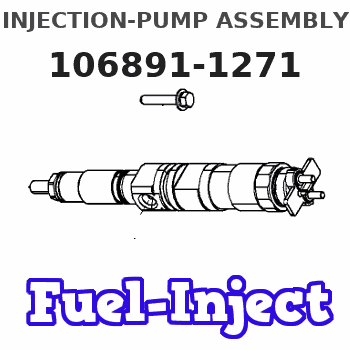
Rating:
Service parts 106891-1271 INJECTION-PUMP ASSEMBLY:
1.
_
6.
COUPLING PLATE
7.
COUPLING PLATE
8.
_
9.
_
11.
Nozzle and Holder
12.
Open Pre:MPa(Kqf/cm2)
15.7(160)/22.1(225)
15.
NOZZLE SET
Include in #1:
106891-1271
as INJECTION-PUMP ASSEMBLY
Cross reference number
BOSCH
F 019 Z10 897
f019z10897
ZEXEL
106891-1271
1068911271
ISUZU
1156025244
1156025244
Zexel num
Bosch num
Firm num
Name
Calibration Data:
Adjustment conditions
Test oil
1404 Test oil ISO4113 or {SAEJ967d}
1404 Test oil ISO4113 or {SAEJ967d}
Test oil temperature
degC
40
40
45
Nozzle and nozzle holder
105780-8140
Bosch type code
EF8511/9A
Nozzle
105780-0000
Bosch type code
DN12SD12T
Nozzle holder
105780-2080
Bosch type code
EF8511/9
Opening pressure
MPa
17.2
Opening pressure
kgf/cm2
175
Injection pipe
Outer diameter - inner diameter - length (mm) mm 8-3-600
Outer diameter - inner diameter - length (mm) mm 8-3-600
Overflow valve (drive side)
134424-4020
Overflow valve opening pressure (drive side)
kPa
255
221
289
Overflow valve opening pressure (drive side)
kgf/cm2
2.6
2.25
2.95
Overflow valve (governor side)
134424-2720
Overflow valve opening pressure (governor side)
kPa
255
221
289
Overflow valve opening pressure (governor side)
kgf/cm2
2.6
2.25
2.95
Tester oil delivery pressure
kPa
157
157
157
Tester oil delivery pressure
kgf/cm2
1.6
1.6
1.6
Direction of rotation (viewed from drive side)
Right R
Right R
Injection timing adjustment
Direction of rotation (viewed from drive side)
Right R
Right R
Injection order
1-8-7-3-
6-5-4-2
Pre-stroke
mm
4.2
4.17
4.23
Rack position
Point A R=A
Point A R=A
Beginning of injection position
Governor side NO.1
Governor side NO.1
Difference between angles 1
Cal 1-8 deg. 45 44.75 45.25
Cal 1-8 deg. 45 44.75 45.25
Difference between angles 2
Cal 1-7 deg. 90 89.75 90.25
Cal 1-7 deg. 90 89.75 90.25
Difference between angles 3
Cal 1-3 deg. 135 134.75 135.25
Cal 1-3 deg. 135 134.75 135.25
Difference between angles 4
Cal 1-6 deg. 180 179.75 180.25
Cal 1-6 deg. 180 179.75 180.25
Difference between angles 5
Cal 1-5 deg. 225 224.75 225.25
Cal 1-5 deg. 225 224.75 225.25
Difference between angles 6
Cal 1-4 deg. 270 269.75 270.25
Cal 1-4 deg. 270 269.75 270.25
Difference between angles 7
Cyl.1-2 deg. 315 314.75 315.25
Cyl.1-2 deg. 315 314.75 315.25
Injection quantity adjustment
Adjusting point
A
Rack position
8.5
Pump speed
r/min
800
800
800
Average injection quantity
mm3/st.
110
108.5
111.5
Max. variation between cylinders
%
0
-2
2
Basic
*
Fixing the lever
*
Injection quantity adjustment_02
Adjusting point
B
Rack position
8.8
Pump speed
r/min
500
500
500
Average injection quantity
mm3/st.
111.6
109.6
113.6
Fixing the lever
*
Injection quantity adjustment_03
Adjusting point
C
Rack position
7.9
Pump speed
r/min
1150
1150
1150
Average injection quantity
mm3/st.
117.4
115.4
119.4
Fixing the lever
*
Injection quantity adjustment_04
Adjusting point
D
Rack position
4.9+-0.5
Pump speed
r/min
225
225
225
Average injection quantity
mm3/st.
8.8
7.5
10.1
Max. variation between cylinders
%
0
-13
13
Fixing the rack
*
Timer adjustment
Pump speed
r/min
600--
Advance angle
deg.
0
0
0
Remarks
Start
Start
Timer adjustment_02
Pump speed
r/min
550
Advance angle
deg.
0.3
Timer adjustment_03
Pump speed
r/min
800+-30
Advance angle
deg.
2
1.5
2.5
Timer adjustment_04
Pump speed
r/min
-
Advance angle
deg.
2
1.5
2.5
Remarks
Measure the actual speed.
Measure the actual speed.
Timer adjustment_05
Pump speed
r/min
1150
Advance angle
deg.
5.5
5
6
Remarks
Finish
Finish
Test data Ex:
Governor adjustment
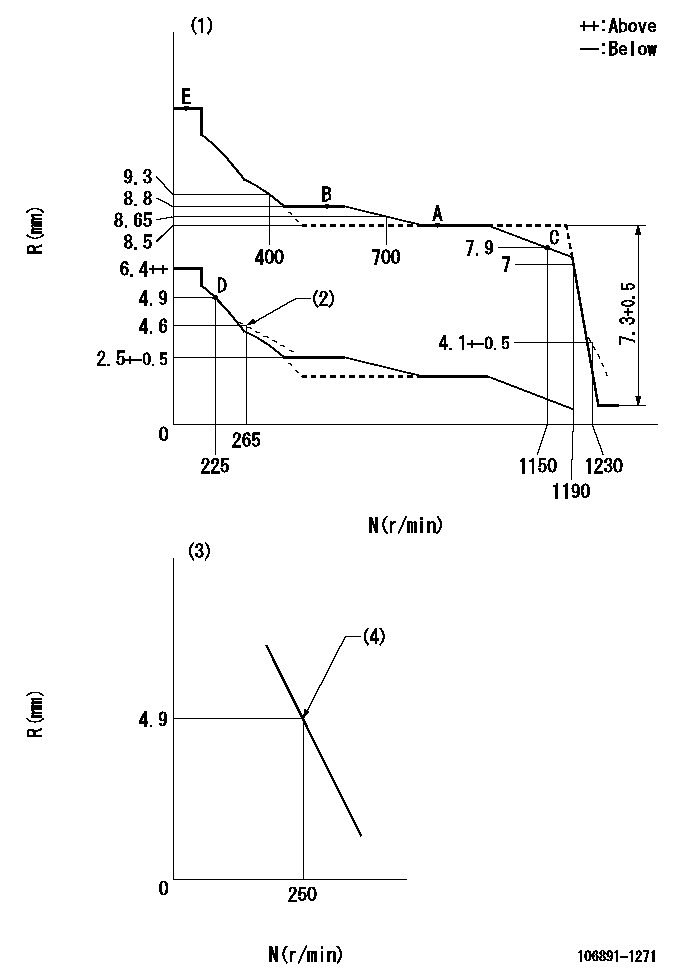
N:Pump speed
R:Rack position (mm)
(1)Tolerance for racks not indicated: +-0.05mm.
(2)Damper spring setting
(3)Variable speed specification: idling adjustment
(4)Main spring setting
----------
----------
----------
----------
Speed control lever angle
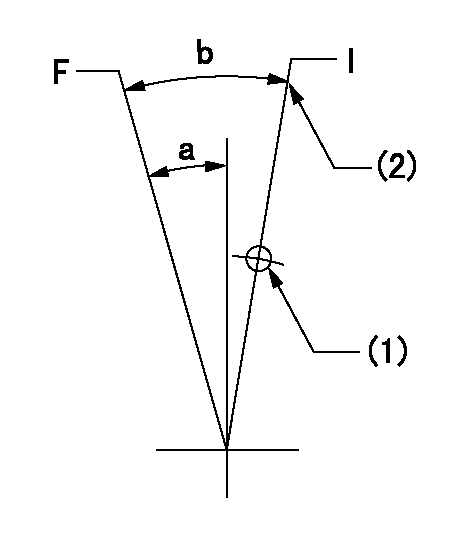
F:Full speed
I:Idle
(1)Use the hole at R = aa
(2)Stopper bolt setting
----------
aa=150mm
----------
a=6deg+-5deg b=(21deg)+-5deg
----------
aa=150mm
----------
a=6deg+-5deg b=(21deg)+-5deg
0000000901
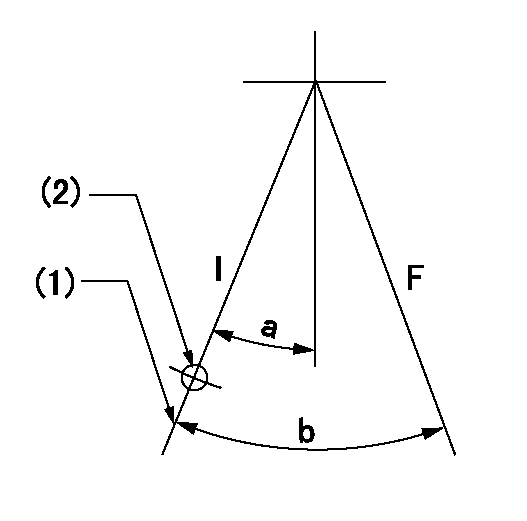
F:Full load
I:Idle
(1)Stopper bolt setting
(2)Use the hole at R = aa
----------
aa=40mm
----------
a=10deg+-5deg b=34deg+-3deg
----------
aa=40mm
----------
a=10deg+-5deg b=34deg+-3deg
Stop lever angle
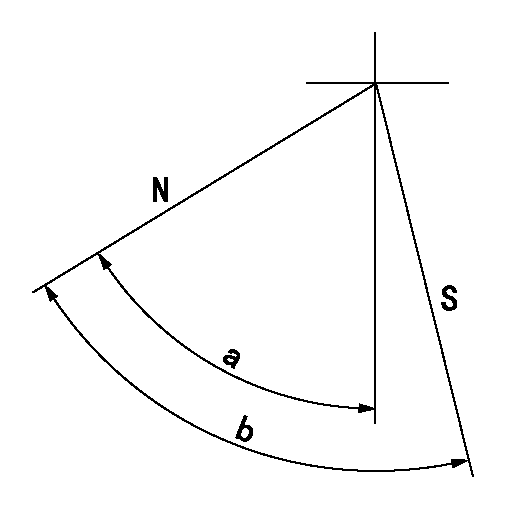
N:Pump normal
S:Stop the pump.
----------
----------
a=60deg+-5deg b=73deg+-5deg
----------
----------
a=60deg+-5deg b=73deg+-5deg
0000001201
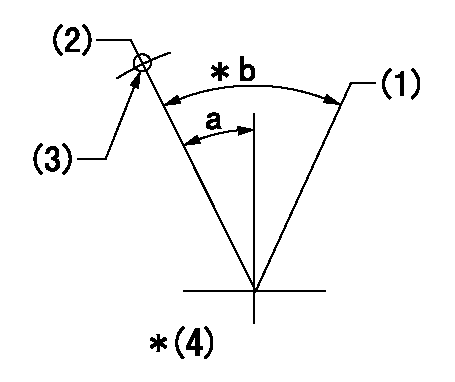
(1)Variable speed specification
(2)Minimum - maximum speed specification
(3)Use the hole at R = aa
(4)Lever angle = c or less
----------
aa=130mm
----------
a=13deg+-5deg b=(20deg) c=26deg
----------
aa=130mm
----------
a=13deg+-5deg b=(20deg) c=26deg
0000001501 LEVER
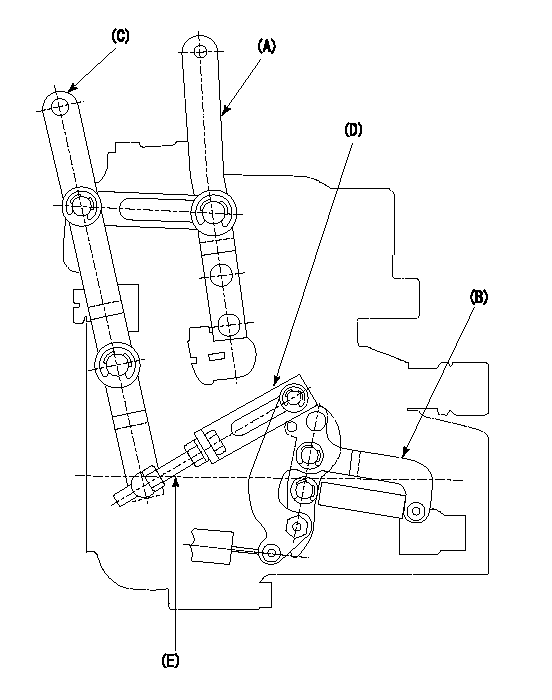
2-stage changeover lever adjustment
(A) Speed lever
(B) Load lever
(C) 2-stage changeover lever
(D) Link
(E) Bolt
1. Minimum-maximum speed specification adjustment (when running)
(1)After completing governor adjustment, hold the 2-stage changeover lever (C) so that the speed lever (A) contacts the full speed stopper.
(2)In this condition, the load lever is held in the idle position.
(3)Adjust bolt (E) so that the clearance between the pin underneath lever (C) and the end of the long groove in link (D) is L.
(4)Lock using the nut.
2. Variable speed specification adjustment (at operation)
(1)Hold the 2-stage changeover lever (C) so that the load lever (B) contacts the full load stopper. (When the load lever is equipped with a cancel mechanism, move it so that it contacts the stopper without canceling.)
(2)In this condition, confirm that the speed lever (A) moves from idle to full speed.
----------
L=1~2mm
----------
----------
L=1~2mm
----------
Timing setting

(1)Pump vertical direction
(2)Position of "Z" mark at the No 1 cylinder's beginning of injection (governor side)
(3)B.T.D.C.: aa (set timing)
(4)-
----------
aa=8deg
----------
a=(180deg)
----------
aa=8deg
----------
a=(180deg)
Information:
Typical Example1. Disconnect wire (1) from Jake Brake. Remove three bolts (2) and remove the Jake Brake.
Typical Example2. Remove Jake Brake exhaust bridge assemblies (3). The following steps are for the installation of the Jake Brake.3. Install Jake Brake exhaust bridge assemblies (3) in the same orientation as illustrated.4. Position Jake Brake assembly and install bolts (2). Connect wire (1).End By:a. install valve cover assemblies as they are illustrated.Disassemble & Assemble Jake Brake
Remove the control valve and slave piston carefully. Control valves are under load from the control valve springs. The slave piston is retained by springs that are under heavy compression. Remove with care to avoid injury.
Start By:a. remove Jake Brake 1. Apply finger pressure to the control valve cover (2). Rotate retaining ring (1) to the slot in the housing. Remove the retaining ring. Release finger pressure slowly. Remove insert (3), spring (4), spring (5), collar (6) and control valve (7).2. Remove solenoid valve (8). Remove three O-ring seals (9) from housing.3. Remove locknut (11). Back out adjusting screw (10) until slave piston is fully retracted.4. Clamp and depress retainer (18) until retainer is 1 mm (.030 in) below the retaining ring groove. Remove retaining ring (19). Back out clamp until springs are loose. Remove clamp. Remove retainer (18), spring (17), spring (16) and slave piston (15).5. Remove anti-rotation pin (13) and washer (12). Remove master piston assembly (14).The following steps are for the assembly of the Jake Brake.6. Inspect master piston assembly (14) for damage. The piston surface must be free of score or wear marks. The piston must move freely in the housing bore. Inspect the spring to insure it is not broken.7. Compress the return spring in the master piston assembly with a pick or probe. While compressed, insert a small pin into the access hole and remove pick or probe. Insert the master piston assembly. Install anti-rotation pin (13) and washer (12) into the housing and remove small pin. The return spring will then be retained by the anti-rotation pin.8. Install slave piston (15), spring (16), spring (17), and retainer (18). Clamp and compress the slave piston retainer until retainer is about 1 mm (.030 in) below the retaining ring groove. Install retaining ring (19). Release clamp.9. Screw adjusting screw (12) in until touching slave piston assembly. Install locknut (11).10. Check the O-ring seals for the solenoid valve for wear or damage. Replace as required. Install three O-ring seals (9) on the solenoid valve. Install solenoid valve (8). Tighten the solenoid to a torque of 7 N m (60 lb in). Be sure O-ring seals are seated properly. Be careful not to twist or unseat O-ring seals while installing.11. Install control valve (7). Install collar (6) with longer sleeve area up. Install spring (4), spring (5), retainer (3) and control valve cover (2). Depress control valve cover with finger. Install retaining ring (1). Rotate retaining ring so the retaining ring ears are located away from the slot in the housing. Release finger