Information injection-pump assembly
BOSCH
9 400 618 529
9400618529
ZEXEL
106873-7981
1068737981
MITSUBISHI
ME163602
me163602
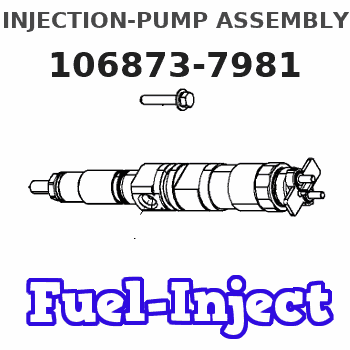
Rating:
Service parts 106873-7981 INJECTION-PUMP ASSEMBLY:
1.
_
7.
COUPLING PLATE
8.
_
9.
_
11.
Nozzle and Holder
ME161933
12.
Open Pre:MPa(Kqf/cm2)
15.7{160}/24.5{250}
14.
NOZZLE
Include in #1:
106873-7981
as INJECTION-PUMP ASSEMBLY
Cross reference number
BOSCH
9 400 618 529
9400618529
ZEXEL
106873-7981
1068737981
MITSUBISHI
ME163602
me163602
Zexel num
Bosch num
Firm num
Name
106873-7981
9 400 618 529
ME163602 MITSUBISHI
INJECTION-PUMP ASSEMBLY
8M20 K 14CD INJECTION PUMP ASSY PE8P PE
8M20 K 14CD INJECTION PUMP ASSY PE8P PE
Calibration Data:
Adjustment conditions
Test oil
1404 Test oil ISO4113 or {SAEJ967d}
1404 Test oil ISO4113 or {SAEJ967d}
Test oil temperature
degC
40
40
45
Nozzle and nozzle holder
105780-8250
Bosch type code
1 688 901 101
Nozzle
105780-0120
Bosch type code
1 688 901 990
Nozzle holder
105780-2190
Opening pressure
MPa
20.7
Opening pressure
kgf/cm2
211
Injection pipe
Outer diameter - inner diameter - length (mm) mm 8-3-600
Outer diameter - inner diameter - length (mm) mm 8-3-600
Overflow valve
131425-0220
Overflow valve opening pressure
kPa
157
123
191
Overflow valve opening pressure
kgf/cm2
1.6
1.25
1.95
Tester oil delivery pressure
kPa
255
255
255
Tester oil delivery pressure
kgf/cm2
2.6
2.6
2.6
Direction of rotation (viewed from drive side)
Right R
Right R
Injection timing adjustment
Direction of rotation (viewed from drive side)
Right R
Right R
Injection order
1-2-7-3-
4-5-6-8
Pre-stroke
mm
3.9
3.85
3.95
Beginning of injection position
Governor side NO.1
Governor side NO.1
Difference between angles 1
Cyl.1-2 deg. 45 44.5 45.5
Cyl.1-2 deg. 45 44.5 45.5
Difference between angles 2
Cal 1-7 deg. 90 89.5 90.5
Cal 1-7 deg. 90 89.5 90.5
Difference between angles 3
Cal 1-3 deg. 135 134.5 135.5
Cal 1-3 deg. 135 134.5 135.5
Difference between angles 4
Cal 1-4 deg. 180 179.5 180.5
Cal 1-4 deg. 180 179.5 180.5
Difference between angles 5
Cal 1-5 deg. 225 224.5 225.5
Cal 1-5 deg. 225 224.5 225.5
Difference between angles 6
Cal 1-6 deg. 270 269.5 270.5
Cal 1-6 deg. 270 269.5 270.5
Difference between angles 7
Cal 1-8 deg. 315 314.5 315.5
Cal 1-8 deg. 315 314.5 315.5
Injection quantity adjustment
Adjusting point
-
Rack position
12.7
Pump speed
r/min
700
700
700
Each cylinder's injection qty
mm3/st.
144
139.7
148.3
Basic
*
Fixing the rack
*
Standard for adjustment of the maximum variation between cylinders
*
Injection quantity adjustment_02
Adjusting point
Z
Rack position
8+-0.5
Pump speed
r/min
445
445
445
Each cylinder's injection qty
mm3/st.
16.5
14
19
Fixing the rack
*
Standard for adjustment of the maximum variation between cylinders
*
Injection quantity adjustment_03
Adjusting point
A
Rack position
R1(12.7)
Pump speed
r/min
700
700
700
Average injection quantity
mm3/st.
144
143
145
Basic
*
Fixing the lever
*
Injection quantity adjustment_04
Adjusting point
B
Rack position
R1+0.8
Pump speed
r/min
1100
1100
1100
Average injection quantity
mm3/st.
139
135
143
Fixing the lever
*
Injection quantity adjustment_05
Adjusting point
C
Rack position
(R1-0.8)
Pump speed
r/min
500
500
500
Average injection quantity
mm3/st.
139.5
135.5
143.5
Fixing the lever
*
Test data Ex:
Governor adjustment
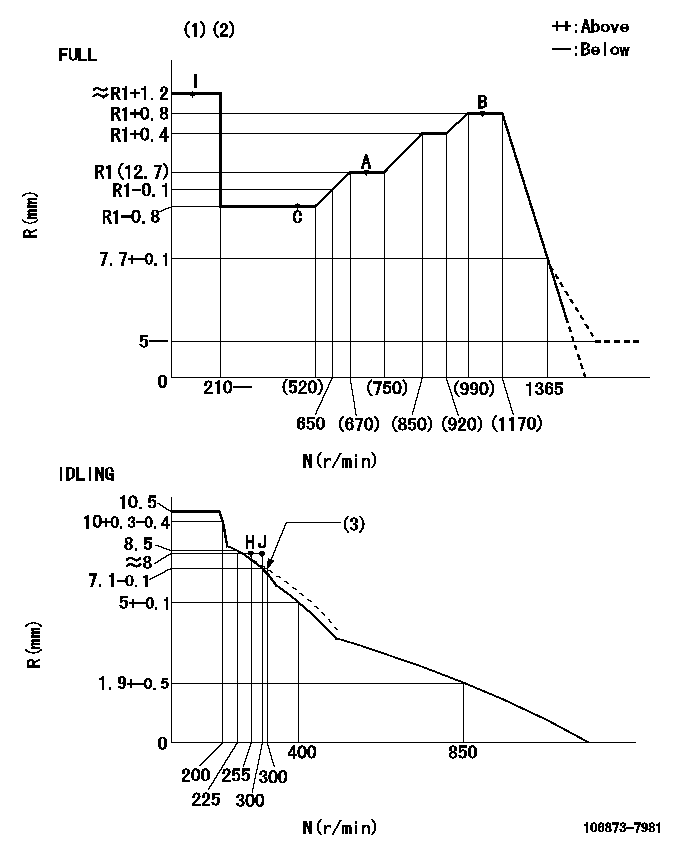
N:Pump speed
R:Rack position (mm)
(1)Torque cam stamping: T1
(2)Tolerance for racks not indicated: +-0.05mm.
(3)Damper spring setting
----------
T1=AD95
----------
----------
T1=AD95
----------
Timer adjustment

(1)Adjusting range
(2)Step response time
(N): Speed of the pump
(L): Load
(theta) Advance angle
(Srd1) Step response time 1
(Srd2) Step response time 2
1. Adjusting conditions for the variable timer
(1)Adjust the clearance between the pickup and the protrusion to L.
----------
L=1-0.2mm N2=800r/min C2=(10)deg t1=2.5--sec. t2=2.5--sec.
----------
N1=750++r/min P1=0kPa(0kgf/cm2) P2=392kPa(4kgf/cm2) C1=10+-0.3deg R01=0/4load R02=4/4load
----------
L=1-0.2mm N2=800r/min C2=(10)deg t1=2.5--sec. t2=2.5--sec.
----------
N1=750++r/min P1=0kPa(0kgf/cm2) P2=392kPa(4kgf/cm2) C1=10+-0.3deg R01=0/4load R02=4/4load
Speed control lever angle
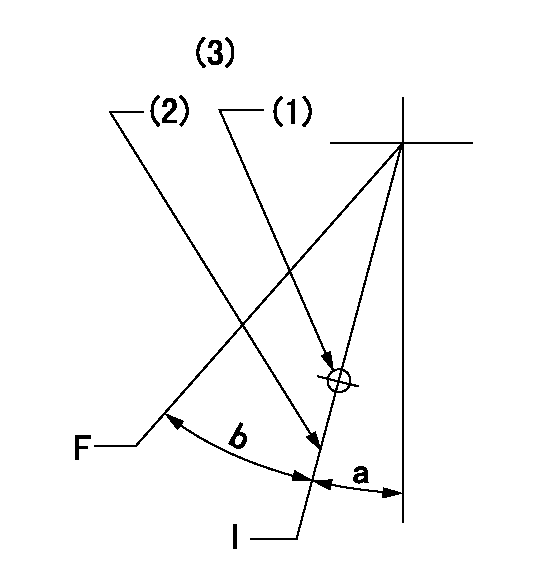
F:Full speed
I:Idle
(1)Use the hole at R = aa
(2)Stopper bolt set position 'H'
(3)Viewed from feed pump side.
----------
aa=37.5mm
----------
a=30deg+-5deg b=(37deg)+-3deg
----------
aa=37.5mm
----------
a=30deg+-5deg b=(37deg)+-3deg
Stop lever angle
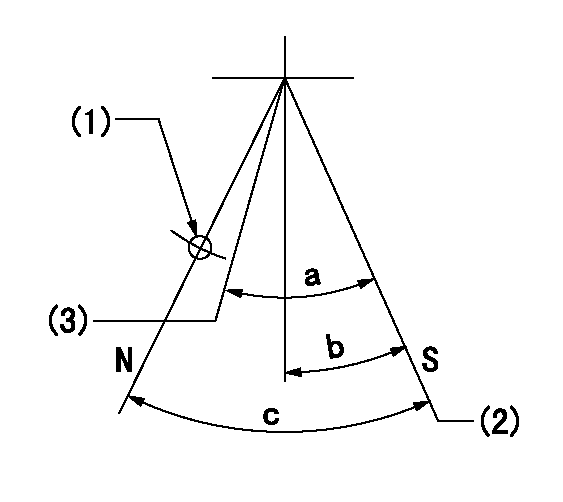
N:Pump normal
S:Stop the pump.
(1)Use the hole at R = aa
(2)Set the stopper bolt so that speed = bb and rack position = cc. (Confirm non-injection.)
(3)Normal engine position (equivalent to R = dd).
----------
aa=54mm bb=1100r/min cc=3.5+-0.3mm dd=20mm
----------
a=(39deg) b=35.5deg+-5deg c=45deg+-5deg
----------
aa=54mm bb=1100r/min cc=3.5+-0.3mm dd=20mm
----------
a=(39deg) b=35.5deg+-5deg c=45deg+-5deg
0000001501 RACK SENSOR
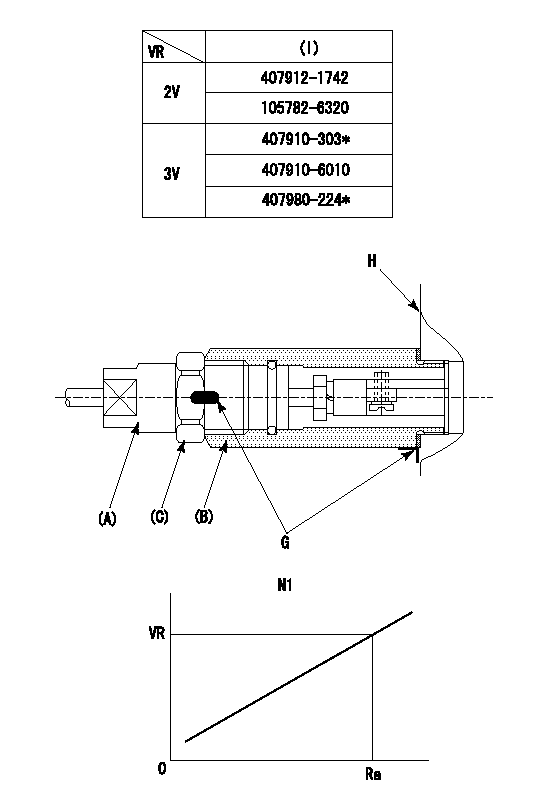
(VR) measurement voltage
(I) Part number of the control unit
(G) Apply red paint.
(H): End surface of the pump
1. Rack sensor adjustment (-0620)
(1)Fix the speed control lever at the full position
(2)Set the speed to N1 r/min.
(If the boost compensator is provided, apply boost pressure.)
(3)Adjust the bobbin (A) so that the rack sensor's output voltage is VR+-0.01.
(4)At that time, rack position must be Ra.
(5)Apply G at two places.
Connecting part between the joint (B) and the nut (F)
Connecting part between the joint (B) and the end surface of the pump (H)
----------
N1=1100r/min Ra=R1+0.8mm
----------
----------
N1=1100r/min Ra=R1+0.8mm
----------
Timing setting

(1)Pump vertical direction
(2)Coupling's key groove position at No 1 cylinder's beginning of injection
(3)B.T.D.C.: aa
(4)-
----------
aa=6deg
----------
a=(50deg)
----------
aa=6deg
----------
a=(50deg)
Information:
(1) End play for shaft (new) ... 0.100 0.018 mm (.0039 .0007 in)Maximum permissible end play (worn) ... 0.20 mm (.008 in)(2) Thickness of thrust bearing (where thrust rings contact bearing) ... 5.372 0.013 mm (.2115 .0005 in)(3) Tighten both band clamps with procedure that follows:a. Tighten to ... 10.2 0.7 N m (90 6 lb in)b. Tap (hit) clamp lightly all around.c. Tighten again to ... 10.2 0.7 N m (90 6 lb in)
Do not overtighten the clamps.
(4) Diameter of shaft (new) ... 11.570 to 11.577 mm (.4555 to .4558 in)Bore in the bearing (new) ... 11.608 to 11.618 mm (.4570 to .4574 in)Maximum permissible clearance between bearing and shaft (worn) ... 0.05 mm (.002 in)(5) Maximum permissible gap of oil seal ring, measured in bore of housing ... 0.25 mm (.010 in)(6) Install the compressor wheel (at room temperature) as follows:a. Put compressor wheel on the shaft.
Do not bend or add stress to the shaft when nut is loosened or tightened.
b. Remove nut from shaft and apply 6V1541 Quick Cure Primer on the threads of the shaft and nut followed by application of 9S3265 Retaining Compound.c. Tighten nut to ... 24.4 1.4 N m (144 4 lb in)(7) Thickness of each thrust ring ... 2.5463 0.0064 mm (.10025 .00025 in)(8) Bore in housing (new) ... 19.050 to 19.075 mm (.7500 to .7510 in)Outside diameter of the bearing (new) ... 18.936 to 18.948 mm (.7455 to .7460 in)Maximum permissible clearance between bearing and bore in housing (worn) ... 0.15 mm (.006 in)Torque for four nuts (put 5P3931 Anti-Seize Compound on threads) and bolts that hold turbocharger to exhaust manifold ... 70 15 N m (50 11 lb ft) Put clean engine oil in the oil inlet of the turbocharger after assembly or before installation to provide start up lubrication and/or storage protection.
Do not overtighten the clamps.
(4) Diameter of shaft (new) ... 11.570 to 11.577 mm (.4555 to .4558 in)Bore in the bearing (new) ... 11.608 to 11.618 mm (.4570 to .4574 in)Maximum permissible clearance between bearing and shaft (worn) ... 0.05 mm (.002 in)(5) Maximum permissible gap of oil seal ring, measured in bore of housing ... 0.25 mm (.010 in)(6) Install the compressor wheel (at room temperature) as follows:a. Put compressor wheel on the shaft.
Do not bend or add stress to the shaft when nut is loosened or tightened.
b. Remove nut from shaft and apply 6V1541 Quick Cure Primer on the threads of the shaft and nut followed by application of 9S3265 Retaining Compound.c. Tighten nut to ... 24.4 1.4 N m (144 4 lb in)(7) Thickness of each thrust ring ... 2.5463 0.0064 mm (.10025 .00025 in)(8) Bore in housing (new) ... 19.050 to 19.075 mm (.7500 to .7510 in)Outside diameter of the bearing (new) ... 18.936 to 18.948 mm (.7455 to .7460 in)Maximum permissible clearance between bearing and bore in housing (worn) ... 0.15 mm (.006 in)Torque for four nuts (put 5P3931 Anti-Seize Compound on threads) and bolts that hold turbocharger to exhaust manifold ... 70 15 N m (50 11 lb ft) Put clean engine oil in the oil inlet of the turbocharger after assembly or before installation to provide start up lubrication and/or storage protection.
Have questions with 106873-7981?
Group cross 106873-7981 ZEXEL
Mitsubishi
Mitsubishi
Mitsubishi
106873-7981
9 400 618 529
ME163602
INJECTION-PUMP ASSEMBLY
8M20
8M20