Information injection-pump assembly
ZEXEL
106873-7710
1068737710
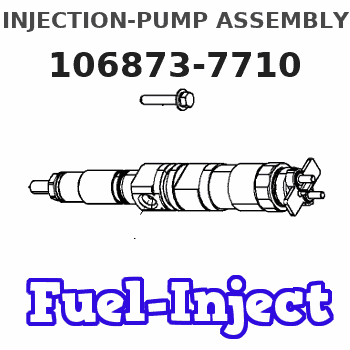
Rating:
Service parts 106873-7710 INJECTION-PUMP ASSEMBLY:
1.
_
7.
COUPLING PLATE
8.
_
9.
_
11.
Nozzle and Holder
ME093528
12.
Open Pre:MPa(Kqf/cm2)
15.7{160}/21.6{220}
14.
NOZZLE
Include in #1:
106873-7710
as INJECTION-PUMP ASSEMBLY
Cross reference number
ZEXEL
106873-7710
1068737710
Zexel num
Bosch num
Firm num
Name
106873-7710
INJECTION-PUMP ASSEMBLY
Calibration Data:
Adjustment conditions
Test oil
1404 Test oil ISO4113 or {SAEJ967d}
1404 Test oil ISO4113 or {SAEJ967d}
Test oil temperature
degC
40
40
45
Nozzle and nozzle holder
105780-8250
Bosch type code
1 688 901 101
Nozzle
105780-0120
Bosch type code
1 688 901 990
Nozzle holder
105780-2190
Opening pressure
MPa
20.7
Opening pressure
kgf/cm2
211
Injection pipe
Outer diameter - inner diameter - length (mm) mm 8-3-600
Outer diameter - inner diameter - length (mm) mm 8-3-600
Overflow valve
131425-0220
Overflow valve opening pressure
kPa
157
123
191
Overflow valve opening pressure
kgf/cm2
1.6
1.25
1.95
Tester oil delivery pressure
kPa
255
255
255
Tester oil delivery pressure
kgf/cm2
2.6
2.6
2.6
Direction of rotation (viewed from drive side)
Right R
Right R
Injection timing adjustment
Direction of rotation (viewed from drive side)
Right R
Right R
Injection order
1-2-7-3-
4-5-6-8
Pre-stroke
mm
3.9
3.85
3.95
Beginning of injection position
Governor side NO.1
Governor side NO.1
Difference between angles 1
Cyl.1-2 deg. 45 44.5 45.5
Cyl.1-2 deg. 45 44.5 45.5
Difference between angles 2
Cal 1-7 deg. 90 89.5 90.5
Cal 1-7 deg. 90 89.5 90.5
Difference between angles 3
Cal 1-3 deg. 135 134.5 135.5
Cal 1-3 deg. 135 134.5 135.5
Difference between angles 4
Cal 1-4 deg. 180 179.5 180.5
Cal 1-4 deg. 180 179.5 180.5
Difference between angles 5
Cal 1-5 deg. 225 224.5 225.5
Cal 1-5 deg. 225 224.5 225.5
Difference between angles 6
Cal 1-6 deg. 270 269.5 270.5
Cal 1-6 deg. 270 269.5 270.5
Difference between angles 7
Cal 1-8 deg. 315 314.5 315.5
Cal 1-8 deg. 315 314.5 315.5
Injection quantity adjustment
Adjusting point
-
Rack position
13.9
Pump speed
r/min
700
700
700
Each cylinder's injection qty
mm3/st.
159
154.2
163.8
Basic
*
Fixing the rack
*
Standard for adjustment of the maximum variation between cylinders
*
Injection quantity adjustment_02
Adjusting point
Z
Rack position
8.6+-0.5
Pump speed
r/min
415
415
415
Each cylinder's injection qty
mm3/st.
19
16.1
21.9
Fixing the rack
*
Standard for adjustment of the maximum variation between cylinders
*
Injection quantity adjustment_03
Adjusting point
A
Rack position
R1(13.9)
Pump speed
r/min
700
700
700
Average injection quantity
mm3/st.
159
158
160
Basic
*
Fixing the lever
*
Boost pressure
kPa
26
26
Boost pressure
mmHg
195
195
Injection quantity adjustment_04
Adjusting point
B
Rack position
R1+1.65
Pump speed
r/min
1100
1100
1100
Average injection quantity
mm3/st.
166.5
162.5
170.5
Fixing the lever
*
Boost pressure
kPa
26
26
Boost pressure
mmHg
195
195
Boost compensator adjustment
Pump speed
r/min
300
300
300
Rack position
R2-1.2
Boost pressure
kPa
6.7
5.4
8
Boost pressure
mmHg
50
40
60
Boost compensator adjustment_02
Pump speed
r/min
300
300
300
Rack position
R2(R1-1.
2)
Boost pressure
kPa
12.7
12.7
12.7
Boost pressure
mmHg
95
95
95
Test data Ex:
Governor adjustment
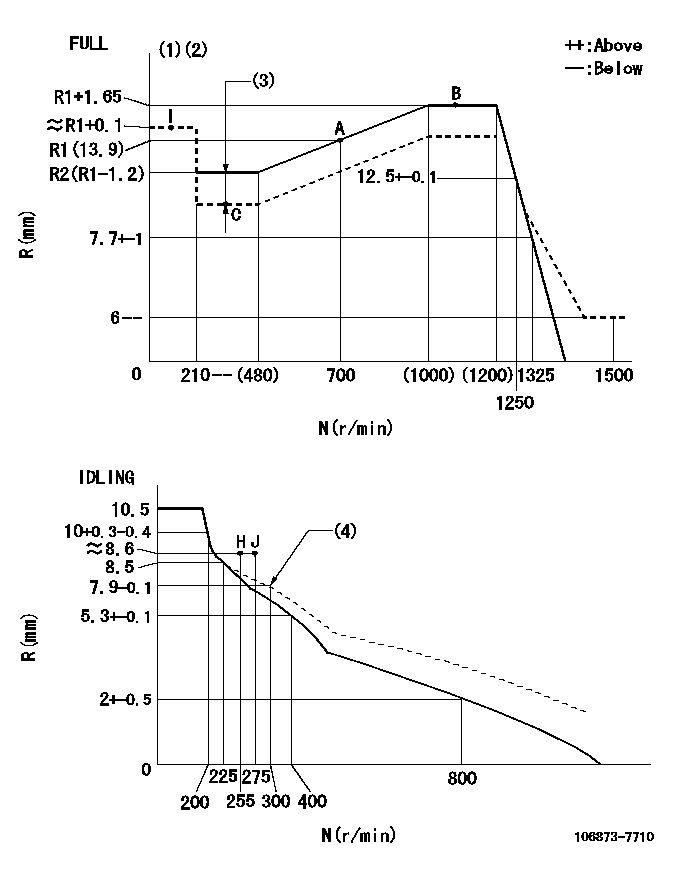
N:Pump speed
R:Rack position (mm)
(1)Torque cam stamping: T1
(2)Tolerance for racks not indicated: +-0.05mm.
(3)Boost compensator stroke: BCL
(4)Damper spring setting
----------
T1=AC77 BCL=1.2+-0.1mm
----------
----------
T1=AC77 BCL=1.2+-0.1mm
----------
Timer adjustment

(1)Adjusting range
(2)Step response time
(N): Speed of the pump
(L): Load
(theta) Advance angle
(Srd1) Step response time 1
(Srd2) Step response time 2
1. Adjusting conditions for the variable timer
(1)Adjust the clearance between the pickup and the protrusion to L.
----------
L=1-0.2mm N2=800r/min C2=(10deg) t1=2.5--sec. t2=2.5--sec.
----------
N1=750++r/min P1=0kPa(0kgf/cm2) P2=392kPa(4kgf/cm2) C1=10+-0.3deg R01=0/4load R02=4/4load
----------
L=1-0.2mm N2=800r/min C2=(10deg) t1=2.5--sec. t2=2.5--sec.
----------
N1=750++r/min P1=0kPa(0kgf/cm2) P2=392kPa(4kgf/cm2) C1=10+-0.3deg R01=0/4load R02=4/4load
Speed control lever angle
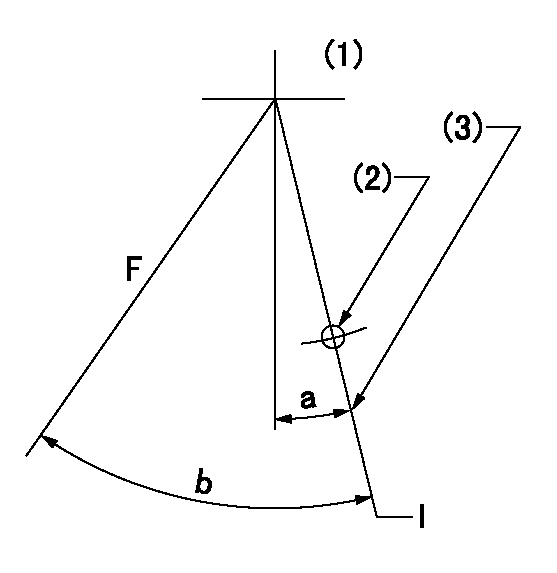
F:Full speed
I:Idle
(1)Viewed from feed pump side.
(2)Use the hole at R = aa
(3)Stopper bolt set position 'H'
----------
aa=37.5mm
----------
a=11.5deg+-5deg b=(42.5deg)+-3deg
----------
aa=37.5mm
----------
a=11.5deg+-5deg b=(42.5deg)+-3deg
Stop lever angle
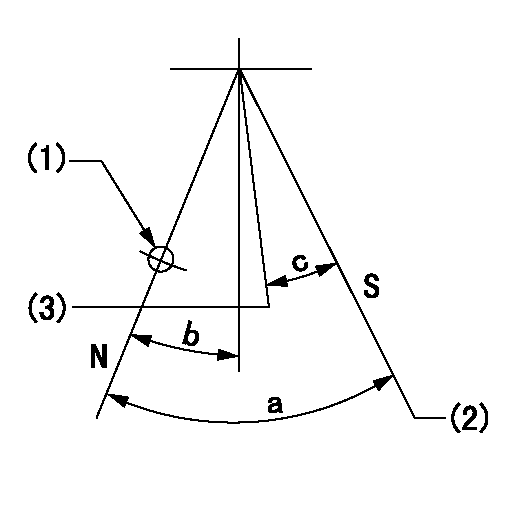
N:Pump normal
S:Stop the pump.
(1)Use the hole at R = aa
(2)Set the stopper bolt so that speed = bb and rack position = cc. (Confirm non-injection.)
(3)Normal engine position (equivalent to R = dd).
----------
aa=54mm bb=1100r/min cc=3.5+-0.3mm dd=18mm
----------
a=41deg+-5deg b=5.5deg+-5deg c=(31deg)
----------
aa=54mm bb=1100r/min cc=3.5+-0.3mm dd=18mm
----------
a=41deg+-5deg b=5.5deg+-5deg c=(31deg)
0000001501 RACK SENSOR
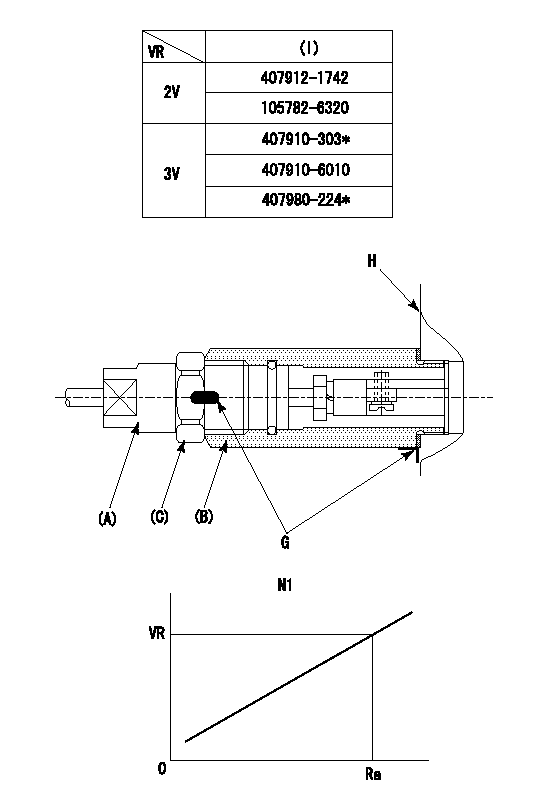
(VR) measurement voltage
(I) Part number of the control unit
(G) Apply red paint.
(H): End surface of the pump
1. Rack sensor adjustment (-0620)
(1)Fix the speed control lever at the full position
(2)Set the speed to N1 r/min.
(If the boost compensator is provided, apply boost pressure.)
(3)Adjust the bobbin (A) so that the rack sensor's output voltage is VR+-0.01.
(4)At that time, rack position must be Ra.
(5)Apply G at two places.
Connecting part between the joint (B) and the nut (F)
Connecting part between the joint (B) and the end surface of the pump (H)
----------
N1=1100r/min Ra=R1(13.9)+1.65mm
----------
----------
N1=1100r/min Ra=R1(13.9)+1.65mm
----------
Timing setting

(1)Pump vertical direction
(2)Coupling's key groove position at No 1 cylinder's beginning of injection
(3)B.T.D.C.: aa
(4)-
----------
aa=4deg
----------
a=(50deg)
----------
aa=4deg
----------
a=(50deg)
Information:
Introduction
The following special instructions must be used to test for a crack in the Diesel Particulate Filter (DPF). Do not perform any procedure that is outlined in this Special Instruction until you have read and understand the information that is contained in this document.Required Tools
Table 1
Required Tools
Part Number Part Name Quantity
380-5200 Tool Kit 1 Testing Procedure
Perform a “Manual Diesel Particulate Filter Regeneration” using Caterpillar Electronic Technician (Cat ® ET).
After the manual DPF regeneration is complete, run the engine at 1800 rpm for a MINIMUM of 20 minutes to stabilize the DPF temperatures.Note: Manually set the engine speed to 1800 rpm, the engine must maintain a steady speed for the entire duration of the test.
Illustration 1 g02597531
(1) DPF Outlet Cap
(2) Filter Paper
(3) Hose Assembly
(4) Air Pump
Illustration 2 g02599276
(5) DPF Outlet Port
Hot parts or hot components can cause burns or personal injury. Do not allow hot parts or components to contact your skin. Use protective clothing or protective equipment to protect your skin.
Shut down the engine and remove the Delta P line from the DPF outlet port. Refer to Illustrations 1 and 2.
Illustration 3 g02599418
(6) Filter Paper
Install the filter in the fitting, Refer to Illustration 3. Install the fitting in the DPF outlet port. The filter must be installed in less than 10 minutes after the engine has shut down.
Turn the vacuum pump ON.
Disable automatic regeneration in Cat ET.
Illustration 4 g02597737
Select "Service" - "Configuration" - "Emissions Parameters" and "ARD Manual Disable Status". Select "Disabled". The check engine light and a 3714-31 active code will be present.
Override the "DPF Differential Pressure Line Override" to "Disconnected", using Cat ET. Refer to Illustration 4.
Start the engine. Run the engine at 1800 rpm for 15 minutes.Note: Manually set the engine speed to 1800 rpm, the engine must maintain a steady speed for the entire duration of the test.
Hot parts or hot components can cause burns or personal injury. Do not allow hot parts or components to contact your skin. Use protective clothing or protective equipment to protect your skin.
Shut the engine down and remove the filter holder within 25 minutes. Use proper personal protective equipment to remove the filter holder.
Allow the filter holder time to cool down before disassembly.
Carefully disassemble the filter holder to prevent contamination. Tip the fitting down on a clean surface to remove the filter paper. Handle the filter paper with clean hands and only by the edges.
Illustration 5 g02597796
Compare the stained area in the center of the filter paper to the color coded sheet provided. Refer to Illustration 5.
If the shade is equal to or darker than the "Color Code Sheet", the DPF has a crack or leak. Replace the DPF. Refer to Special Instruction, "Diesel Particulate Filter (DPF) Maintenance on Tier 4 Products Equipped with a Diesel Particulate Filter".
If the shade is lighter than the "Color Code Sheet", then return the unit to service.
Enable the Automatic regeneration in Cat ET.
Select "Service" - "Configuration" - "Emissions Parameters" and "ARD Manual Disable Status". Select "Not - Disabled". The check engine light will go off unless
The following special instructions must be used to test for a crack in the Diesel Particulate Filter (DPF). Do not perform any procedure that is outlined in this Special Instruction until you have read and understand the information that is contained in this document.Required Tools
Table 1
Required Tools
Part Number Part Name Quantity
380-5200 Tool Kit 1 Testing Procedure
Perform a “Manual Diesel Particulate Filter Regeneration” using Caterpillar Electronic Technician (Cat ® ET).
After the manual DPF regeneration is complete, run the engine at 1800 rpm for a MINIMUM of 20 minutes to stabilize the DPF temperatures.Note: Manually set the engine speed to 1800 rpm, the engine must maintain a steady speed for the entire duration of the test.
Illustration 1 g02597531
(1) DPF Outlet Cap
(2) Filter Paper
(3) Hose Assembly
(4) Air Pump
Illustration 2 g02599276
(5) DPF Outlet Port
Hot parts or hot components can cause burns or personal injury. Do not allow hot parts or components to contact your skin. Use protective clothing or protective equipment to protect your skin.
Shut down the engine and remove the Delta P line from the DPF outlet port. Refer to Illustrations 1 and 2.
Illustration 3 g02599418
(6) Filter Paper
Install the filter in the fitting, Refer to Illustration 3. Install the fitting in the DPF outlet port. The filter must be installed in less than 10 minutes after the engine has shut down.
Turn the vacuum pump ON.
Disable automatic regeneration in Cat ET.
Illustration 4 g02597737
Select "Service" - "Configuration" - "Emissions Parameters" and "ARD Manual Disable Status". Select "Disabled". The check engine light and a 3714-31 active code will be present.
Override the "DPF Differential Pressure Line Override" to "Disconnected", using Cat ET. Refer to Illustration 4.
Start the engine. Run the engine at 1800 rpm for 15 minutes.Note: Manually set the engine speed to 1800 rpm, the engine must maintain a steady speed for the entire duration of the test.
Hot parts or hot components can cause burns or personal injury. Do not allow hot parts or components to contact your skin. Use protective clothing or protective equipment to protect your skin.
Shut the engine down and remove the filter holder within 25 minutes. Use proper personal protective equipment to remove the filter holder.
Allow the filter holder time to cool down before disassembly.
Carefully disassemble the filter holder to prevent contamination. Tip the fitting down on a clean surface to remove the filter paper. Handle the filter paper with clean hands and only by the edges.
Illustration 5 g02597796
Compare the stained area in the center of the filter paper to the color coded sheet provided. Refer to Illustration 5.
If the shade is equal to or darker than the "Color Code Sheet", the DPF has a crack or leak. Replace the DPF. Refer to Special Instruction, "Diesel Particulate Filter (DPF) Maintenance on Tier 4 Products Equipped with a Diesel Particulate Filter".
If the shade is lighter than the "Color Code Sheet", then return the unit to service.
Enable the Automatic regeneration in Cat ET.
Select "Service" - "Configuration" - "Emissions Parameters" and "ARD Manual Disable Status". Select "Not - Disabled". The check engine light will go off unless
Have questions with 106873-7710?
Group cross 106873-7710 ZEXEL
Mitsubishi
106873-7710
INJECTION-PUMP ASSEMBLY