Information injection-pump assembly
BOSCH
9 400 618 508
9400618508
ZEXEL
106873-7680
1068737680
MITSUBISHI
ME094869
me094869
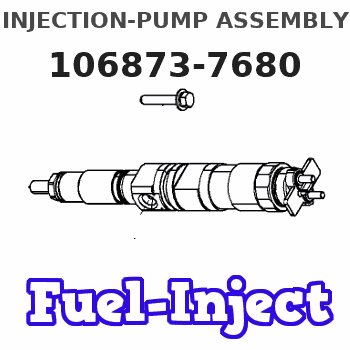
Rating:
Cross reference number
BOSCH
9 400 618 508
9400618508
ZEXEL
106873-7680
1068737680
MITSUBISHI
ME094869
me094869
Zexel num
Bosch num
Firm num
Name
106873-7680
9 400 618 508
ME094869 MITSUBISHI
INJECTION-PUMP ASSEMBLY
8DC11 K
8DC11 K
Calibration Data:
Adjustment conditions
Test oil
1404 Test oil ISO4113 or {SAEJ967d}
1404 Test oil ISO4113 or {SAEJ967d}
Test oil temperature
degC
40
40
45
Nozzle and nozzle holder
105780-8140
Bosch type code
EF8511/9A
Nozzle
105780-0000
Bosch type code
DN12SD12T
Nozzle holder
105780-2080
Bosch type code
EF8511/9
Opening pressure
MPa
17.2
Opening pressure
kgf/cm2
175
Injection pipe
Outer diameter - inner diameter - length (mm) mm 8-3-600
Outer diameter - inner diameter - length (mm) mm 8-3-600
Overflow valve
134424-1320
Overflow valve opening pressure
kPa
157
123
191
Overflow valve opening pressure
kgf/cm2
1.6
1.25
1.95
Tester oil delivery pressure
kPa
157
157
157
Tester oil delivery pressure
kgf/cm2
1.6
1.6
1.6
Direction of rotation (viewed from drive side)
Right R
Right R
Injection timing adjustment
Direction of rotation (viewed from drive side)
Right R
Right R
Injection order
1-2-7-3-
4-5-6-8
Pre-stroke
mm
4.8
4.75
4.85
Beginning of injection position
Governor side NO.1
Governor side NO.1
Difference between angles 1
Cyl.1-2 deg. 45 44.5 45.5
Cyl.1-2 deg. 45 44.5 45.5
Difference between angles 2
Cal 1-7 deg. 90 89.5 90.5
Cal 1-7 deg. 90 89.5 90.5
Difference between angles 3
Cal 1-3 deg. 135 134.5 135.5
Cal 1-3 deg. 135 134.5 135.5
Difference between angles 4
Cal 1-4 deg. 180 179.5 180.5
Cal 1-4 deg. 180 179.5 180.5
Difference between angles 5
Cal 1-5 deg. 225 224.5 225.5
Cal 1-5 deg. 225 224.5 225.5
Difference between angles 6
Cal 1-6 deg. 270 269.5 270.5
Cal 1-6 deg. 270 269.5 270.5
Difference between angles 7
Cal 1-8 deg. 315 314.5 315.5
Cal 1-8 deg. 315 314.5 315.5
Injection quantity adjustment
Adjusting point
-
Rack position
10.3
Pump speed
r/min
650
650
650
Each cylinder's injection qty
mm3/st.
122
118.3
125.7
Basic
*
Fixing the rack
*
Standard for adjustment of the maximum variation between cylinders
*
Injection quantity adjustment_02
Adjusting point
C
Rack position
6.2+-0.5
Pump speed
r/min
225
225
225
Each cylinder's injection qty
mm3/st.
17.5
14.9
20.1
Fixing the rack
*
Standard for adjustment of the maximum variation between cylinders
*
Injection quantity adjustment_03
Adjusting point
A
Rack position
R1(10.3)
Pump speed
r/min
650
650
650
Average injection quantity
mm3/st.
122
121
123
Basic
*
Fixing the lever
*
Injection quantity adjustment_04
Adjusting point
B
Rack position
R1+0.15
Pump speed
r/min
1100
1100
1100
Average injection quantity
mm3/st.
131
127
135
Fixing the lever
*
Injection quantity adjustment_05
Adjusting point
E
Rack position
-
Pump speed
r/min
100
100
100
Average injection quantity
mm3/st.
135
115
155
Fixing the lever
*
Remarks
After startup boost setting
After startup boost setting
Timer adjustment
Pump speed
r/min
500--
Advance angle
deg.
0
0
0
Load
0/4
Remarks
Start
Start
Timer adjustment_02
Pump speed
r/min
450
Advance angle
deg.
0.5
Load
0/4
Timer adjustment_03
Pump speed
r/min
590
Advance angle
deg.
2
1.5
2.5
Load
0/4
Timer adjustment_04
Pump speed
r/min
(950)
Advance angle
deg.
2
1.5
2.5
Load
4/4
Remarks
Measure the actual speed.
Measure the actual speed.
Timer adjustment_05
Pump speed
r/min
(1100)
Advance angle
deg.
5.5
5
6
Load
4/4
Remarks
Measure the actual speed, stop
Measure the actual speed, stop
Test data Ex:
Governor adjustment
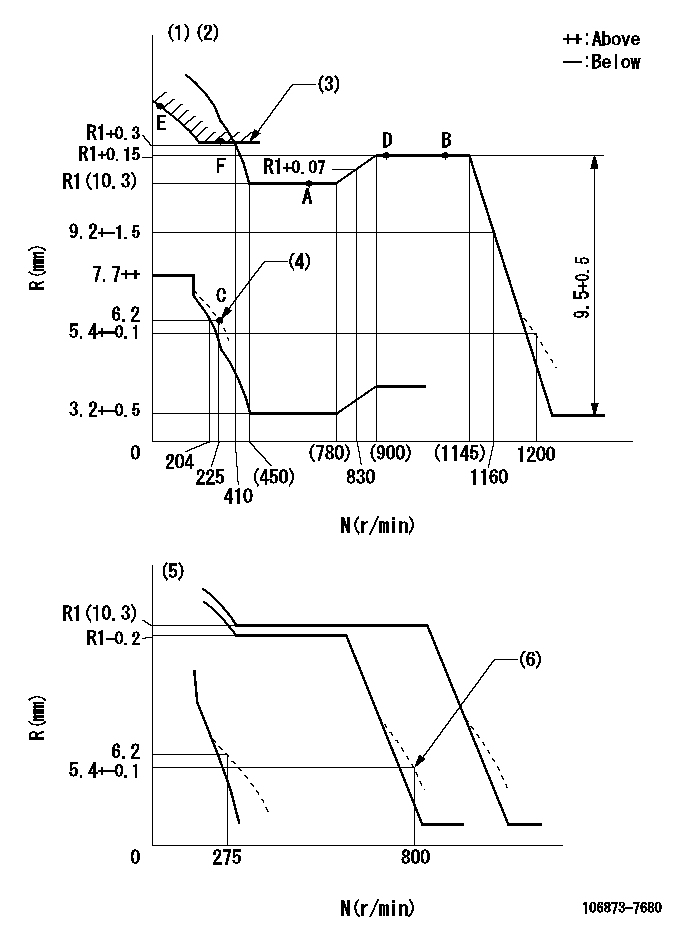
N:Pump speed
R:Rack position (mm)
(1)Adjust with speed control lever at full position (minimum-maximum speed specification)
(2)Tolerance for racks not indicated: +-0.05mm.
(3)Excess fuel setting for starting: SXL
(4)Damper spring setting
(5)Adjust with the load control lever in the full position (variable speed specification).
(6)When air cylinder is operating.
----------
SXL=10.8+-0.1mm
----------
----------
SXL=10.8+-0.1mm
----------
Speed control lever angle
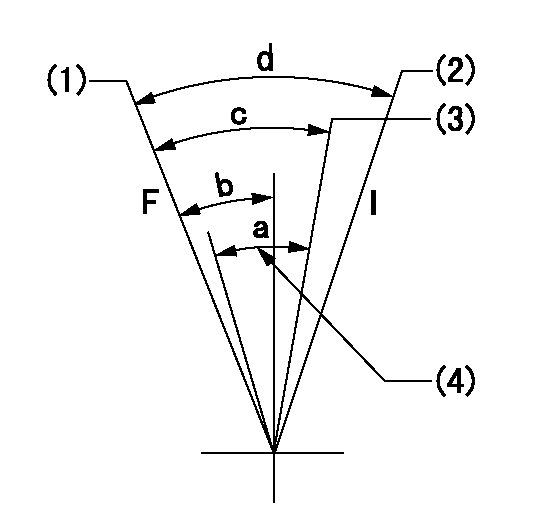
F:Full speed
I:Idle
(1)Pump speed = aa
(2)Pump speed = bb
(3)Pump speed cc
(4)Air cylinder's adjustable range
----------
aa=1200r/min bb=275r/min cc=800r/min
----------
a=(11.5deg) b=(6deg)+-5deg c=(11.5deg)+-5deg d=(22deg)+-5deg
----------
aa=1200r/min bb=275r/min cc=800r/min
----------
a=(11.5deg) b=(6deg)+-5deg c=(11.5deg)+-5deg d=(22deg)+-5deg
0000000901

F:Full load
I:Idle
(1)Stopper bolt setting
----------
----------
a=10deg+-5deg b=26.5deg+-3deg
----------
----------
a=10deg+-5deg b=26.5deg+-3deg
Stop lever angle
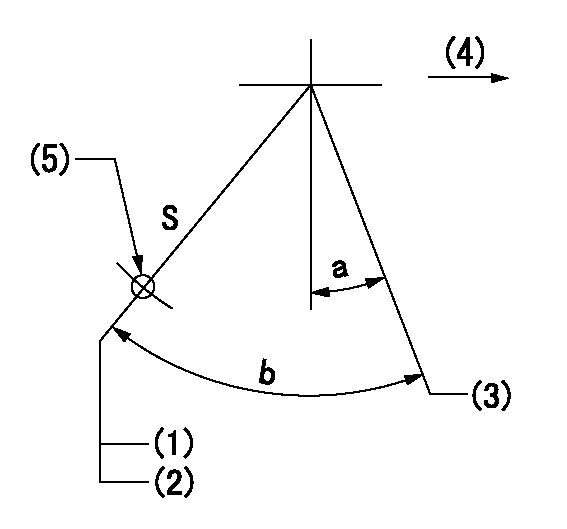
S:Stop the pump.
(1)Rack position = aa
(2)Stopper bolt setting
(3)Free (at delivery)
(4)Drive side
(5)Use the hole at R = bb
----------
aa=4.1-0.5mm bb=36mm
----------
a=10.5deg+-5deg b=55.5deg+7deg-5deg
----------
aa=4.1-0.5mm bb=36mm
----------
a=10.5deg+-5deg b=55.5deg+7deg-5deg
0000001501 MICRO SWITCH
Adjustment of the micro-switch
Adjust the bolt to obtain the following lever position when the micro-switch is ON.
(1)Speed N1
(2)Rack position Ra
----------
N1=325r/min Ra=5.7+-0.1mm
----------
----------
N1=325r/min Ra=5.7+-0.1mm
----------
0000001601 2-STAGE CHANGEOVER DEVICE

RFD governor 2 stage changeover mechanism adjustment outline
(A) Bolt
(B) bolt
(c) Nut
(D) Return spring
(E) Bolt
(F) Bolt
(G) Screw
(H) Bolt
(I) Load lever
(J) Speed lever
(K) Air cylinder
(M Air inlet
Figure 1 is only for reference. Lever shape, etc, may vary.
1. Minimum-maximum speed specification adjustment (when running)
(a) Without applying air to the air cylinder, loosen bolts (A) and (B).
(1)High speed return L setting
(a) In the speed range Nf~Nf - 300r/min, adjust using the speed adjusting bolt to determine the temporary beginning of high speed control speed.
(b) Determine the rack position in the vicinity of Rf using the full load lever.
(c) Increase speed and confirm return distance L.
(d) Adjust using the tension lever bolt to obtain L.
(2)Setting full load rack position Rf
(a) Move the load control lever to the full side.
(b) Adjust the full load adjusting bolt so that Rf can be obtained, then fix.
(3)Setting the beginning of high speed operation Nf
(a) Adjust using bolt (E) so that Nf can be obtained, and then fix.
(4)Idle control setting (Re, Ni, Rc)
(a) Set the speed at Ns + 200r/min and move the load control lever to the idle side.
(b) Fix the lever in the position where Re can be obtained.
(c) Next, decrease speed to Ni and screw in the idle spring.
(d) Adjust to obtain rack position Ri.
(e) Increase the speed and after confirming that the rack position is Re at Ns, set the speed at 0.
(f) Confirm protrusion position Rc at idle.
(5)Damper spring adjustment
(a) Increase speed and set the speed at the rack position Rd - 0.1 mm
(b) Set using the damper spring so that the rack position Rd can be obtained.
(c) When Rd is not specified, Rd = Ri - 0.5 mm.
(6)High speed droop confirmation
(a) Return the load control lever to the full load lever position.
(b) Increase the speed and confirm that Rf can be obtained at Nf r/min.
(c) Confirm that speed is Nh at rack position Rh.
2. Variable speed specification adjustment (at operation)
(a) Remove return spring (D).
(b) Apply air pressure of 245~294 kPa {2.5~3 kg/cm2} to the air cylinder.
(c) Perform the following adjustment in this condition.
(1)Setting full load rack position Rf'
(a) Pull the load lever to the idle side.
(b) Obtain rack position Rf' using the nut (C). (Pump speed is Nf'-50 r/min.)
(2)Setting full speed Nf'
(a) Adjust using bolt (B) so that Nf can be obtained, and then fix.
(3)Low speed side setting
(a) At 350r/min, set bolt (F) at beginning of governor operation position, then fix.
3. Bolt (A) adjustment
(1)Install return spring (D) and perform the adjustments below at air pressure 0.
(a) Set at speed Nf using bolt (E).
(b) Screw in bolt (A).
(c) Screw in 1 more turn from the speed lever contact position
(d) Fix bolt (A).
(e) At this time confirm that the air cylinder's shaft moves approximately 1 mm towards the governor.
4. Lever operation confirmation using the air cylinder
(1)Apply 588 kPa {6 kg/cm2} air pressure to the air cylinder.
(2)Confirm that the cylinder piston is moved 50 mm by the spring (D).
----------
----------
----------
----------
Timing setting

(1)Pump vertical direction
(2)Coupling's key groove position at No 1 cylinder's beginning of injection
(3)B.T.D.C.: aa
(4)-
----------
aa=7deg
----------
a=(40deg)
----------
aa=7deg
----------
a=(40deg)
Information:
The heat baths listed in Chart B meet the specified requirements and can be purchased from:Cole-Parmer Instruments Co.
7425 North Oakpark Ave.
Niles, IL, 60714 U.S.A.
Phone (800) 323-4340
Fax: (708) 647-9660
* Heat Bath Fluid The heat bath fluid must be able to obtain and maintain the required contactor actuation and deactuation temperatures. For the temperatures required for the calibration procedure, silicone fluid must be used. Silicone fluid has a temperature range between 10° C (50° F) and 230° C (446° F). Silicone fluid can be purchased from Cole-Parmer by ordering G-01294-40. The fluid comes in a 3.8 Liter (1 gal) container.
Use extreme caution around heat baths with high temperature fluids. High temperature fluids can cause severe burns.
Calibration Procedure
Use the following procedure to test and calibrate the temperature contactors.1. If connected, disconnect the contactor from the power supply. Mark the terminal location and disconnect the three wires from terminals 1, 2, and 4.
High voltage electrical shock is possible. The contactor must be disconnected from the power supply and the wires disconnected from terminals 1, 2, and 4. Failure to follow this recommendation can result in serious bodily injury.
2. Locate and record the part number of the temperature contactor in Chart A. This will determine the actuation and deactuation temperatures. If the temperature contactor is used in extreme ambient temperatures there will be a scale deviation from the required actuation and deactuation temperatures. Refer to the "Calculating Scale Correction for Severe Temperature Applications" section in this Special Instruction.
Temperature Contactor
(1) Housing cover. (2) Housing cover screws. (3) Temperature probe. (4) Capillary tube.3. Loosen housing cover screws (2) and remove housing cover (1).4. Fill the heat bath unit with silicone fluid and heat it to approximately 5° C (10° F) below the actuation temperature setting. Do not immerse the temperature probe at this time.
Nomenclature Of Internal Parts
(5). Lock screw. (6) Range spindle. (7) Range scale. (8) Differential spindle. (9) Differential scale.5. Loosen lock screw (5).6. Adjust range spindle (6) to a setting above the desired actuation setting determined in Step 2. Determine the setting by using range scale (7).7. Adjust the differential spindle (8) to the approximate mechanical differential temperature using differential scale (9). Mechanical differential temperature is the difference between the actuation and deactuation temperature settings.
Temperature Control Function For Actuation And Deactuation (specifically shown for 7C-3888 Contactor)
Adjusting Temperature and Differential Settings On The Temperature Contactor
This example shows the temperature set at 66° C with an 8° C differential setting. This results in a deactuation temperature of 58° C and actuation temperature of 66° C. (Refer to "Temperature Control Function For Actuation And Deactuation" illustration.)8. Fully immerse temperature probe (3) in the silicone fluid. Increase the heat bath temperature to the specified actuation temperature.9. When the actuation temperature has stabilized, very slowly turn range spindle (6) counterclockwise until the contact actuates. This will be accompanied by an audible "click".
When Contact Actuates, Terminals 1 And 4 Will Have Continuity10. Use a 6V-7070 Multimeter, or equivalent, to verify the actuation of the contactor. Check for continuity between
7425 North Oakpark Ave.
Niles, IL, 60714 U.S.A.
Phone (800) 323-4340
Fax: (708) 647-9660
* Heat Bath Fluid The heat bath fluid must be able to obtain and maintain the required contactor actuation and deactuation temperatures. For the temperatures required for the calibration procedure, silicone fluid must be used. Silicone fluid has a temperature range between 10° C (50° F) and 230° C (446° F). Silicone fluid can be purchased from Cole-Parmer by ordering G-01294-40. The fluid comes in a 3.8 Liter (1 gal) container.
Use extreme caution around heat baths with high temperature fluids. High temperature fluids can cause severe burns.
Calibration Procedure
Use the following procedure to test and calibrate the temperature contactors.1. If connected, disconnect the contactor from the power supply. Mark the terminal location and disconnect the three wires from terminals 1, 2, and 4.
High voltage electrical shock is possible. The contactor must be disconnected from the power supply and the wires disconnected from terminals 1, 2, and 4. Failure to follow this recommendation can result in serious bodily injury.
2. Locate and record the part number of the temperature contactor in Chart A. This will determine the actuation and deactuation temperatures. If the temperature contactor is used in extreme ambient temperatures there will be a scale deviation from the required actuation and deactuation temperatures. Refer to the "Calculating Scale Correction for Severe Temperature Applications" section in this Special Instruction.
Temperature Contactor
(1) Housing cover. (2) Housing cover screws. (3) Temperature probe. (4) Capillary tube.3. Loosen housing cover screws (2) and remove housing cover (1).4. Fill the heat bath unit with silicone fluid and heat it to approximately 5° C (10° F) below the actuation temperature setting. Do not immerse the temperature probe at this time.
Nomenclature Of Internal Parts
(5). Lock screw. (6) Range spindle. (7) Range scale. (8) Differential spindle. (9) Differential scale.5. Loosen lock screw (5).6. Adjust range spindle (6) to a setting above the desired actuation setting determined in Step 2. Determine the setting by using range scale (7).7. Adjust the differential spindle (8) to the approximate mechanical differential temperature using differential scale (9). Mechanical differential temperature is the difference between the actuation and deactuation temperature settings.
Temperature Control Function For Actuation And Deactuation (specifically shown for 7C-3888 Contactor)
Adjusting Temperature and Differential Settings On The Temperature Contactor
This example shows the temperature set at 66° C with an 8° C differential setting. This results in a deactuation temperature of 58° C and actuation temperature of 66° C. (Refer to "Temperature Control Function For Actuation And Deactuation" illustration.)8. Fully immerse temperature probe (3) in the silicone fluid. Increase the heat bath temperature to the specified actuation temperature.9. When the actuation temperature has stabilized, very slowly turn range spindle (6) counterclockwise until the contact actuates. This will be accompanied by an audible "click".
When Contact Actuates, Terminals 1 And 4 Will Have Continuity10. Use a 6V-7070 Multimeter, or equivalent, to verify the actuation of the contactor. Check for continuity between
Have questions with 106873-7680?
Group cross 106873-7680 ZEXEL
Mitsubishi
Mitsubishi
Mitsubishi
Mitsubishi
Mitsubishi
Mitsubishi
106873-7680
9 400 618 508
ME094869
INJECTION-PUMP ASSEMBLY
8DC11
8DC11