Information injection-pump assembly
BOSCH
9 400 611 036
9400611036
ZEXEL
106873-7280
1068737280
MITSUBISHI
ME094088
me094088
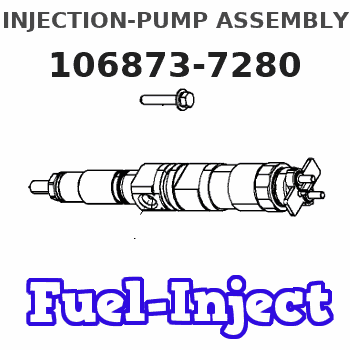
Rating:
Service parts 106873-7280 INJECTION-PUMP ASSEMBLY:
1.
_
7.
COUPLING PLATE
8.
_
9.
_
11.
Nozzle and Holder
ME092348
12.
Open Pre:MPa(Kqf/cm2)
21.6{220}
15.
NOZZLE SET
Include in #1:
106873-7280
as INJECTION-PUMP ASSEMBLY
Cross reference number
BOSCH
9 400 611 036
9400611036
ZEXEL
106873-7280
1068737280
MITSUBISHI
ME094088
me094088
Zexel num
Bosch num
Firm num
Name
106873-7280
9 400 611 036
ME094088 MITSUBISHI
INJECTION-PUMP ASSEMBLY
8DC9 K 14CD INJECTION PUMP ASSY PE8P PE
8DC9 K 14CD INJECTION PUMP ASSY PE8P PE
Calibration Data:
Adjustment conditions
Test oil
1404 Test oil ISO4113 or {SAEJ967d}
1404 Test oil ISO4113 or {SAEJ967d}
Test oil temperature
degC
40
40
45
Nozzle and nozzle holder
105780-8140
Bosch type code
EF8511/9A
Nozzle
105780-0000
Bosch type code
DN12SD12T
Nozzle holder
105780-2080
Bosch type code
EF8511/9
Opening pressure
MPa
17.2
Opening pressure
kgf/cm2
175
Injection pipe
Outer diameter - inner diameter - length (mm) mm 8-3-600
Outer diameter - inner diameter - length (mm) mm 8-3-600
Overflow valve
134424-1320
Overflow valve opening pressure
kPa
157
157
157
Overflow valve opening pressure
kgf/cm2
1.6
1.6
1.6
Tester oil delivery pressure
kPa
157
157
157
Tester oil delivery pressure
kgf/cm2
1.6
1.6
1.6
Direction of rotation (viewed from drive side)
Right R
Right R
Injection timing adjustment
Direction of rotation (viewed from drive side)
Right R
Right R
Injection order
1-2-7-3-
4-5-6-8
Pre-stroke
mm
4.8
4.75
4.85
Beginning of injection position
Governor side NO.1
Governor side NO.1
Difference between angles 1
Cyl.1-2 deg. 45 44.5 45.5
Cyl.1-2 deg. 45 44.5 45.5
Difference between angles 2
Cal 1-7 deg. 90 89.5 90.5
Cal 1-7 deg. 90 89.5 90.5
Difference between angles 3
Cal 1-3 deg. 135 134.5 135.5
Cal 1-3 deg. 135 134.5 135.5
Difference between angles 4
Cal 1-4 deg. 180 179.5 180.5
Cal 1-4 deg. 180 179.5 180.5
Difference between angles 5
Cal 1-5 deg. 225 224.5 225.5
Cal 1-5 deg. 225 224.5 225.5
Difference between angles 6
Cal 1-6 deg. 270 269.5 270.5
Cal 1-6 deg. 270 269.5 270.5
Difference between angles 7
Cal 1-8 deg. 315 314.5 315.5
Cal 1-8 deg. 315 314.5 315.5
Injection quantity adjustment
Adjusting point
-
Rack position
9.3
Pump speed
r/min
700
700
700
Each cylinder's injection qty
mm3/st.
112.5
109.1
115.9
Basic
*
Fixing the rack
*
Standard for adjustment of the maximum variation between cylinders
*
Injection quantity adjustment_02
Adjusting point
C
Rack position
6.1+-0.5
Pump speed
r/min
225
225
225
Each cylinder's injection qty
mm3/st.
20
17
23
Fixing the rack
*
Standard for adjustment of the maximum variation between cylinders
*
Injection quantity adjustment_03
Adjusting point
A
Rack position
R1(9.3)
Pump speed
r/min
700
700
700
Average injection quantity
mm3/st.
112.5
111.5
113.5
Basic
*
Fixing the lever
*
Injection quantity adjustment_04
Adjusting point
B
Rack position
R1(9.3)
Pump speed
r/min
1100
1100
1100
Average injection quantity
mm3/st.
118.5
113.3
123.7
Difference in delivery
mm3/st.
10.4
10.4
10.4
Fixing the lever
*
Injection quantity adjustment_05
Adjusting point
E
Rack position
-
Pump speed
r/min
100
100
100
Average injection quantity
mm3/st.
140
100
180
Fixing the lever
*
Remarks
After startup boost setting
After startup boost setting
Timer adjustment
Pump speed
r/min
550--
Advance angle
deg.
0
0
0
Remarks
Start
Start
Timer adjustment_02
Pump speed
r/min
500
Advance angle
deg.
0.5
Timer adjustment_03
Pump speed
r/min
1100
Advance angle
deg.
5
4.5
5.5
Remarks
Finish
Finish
Test data Ex:
Governor adjustment
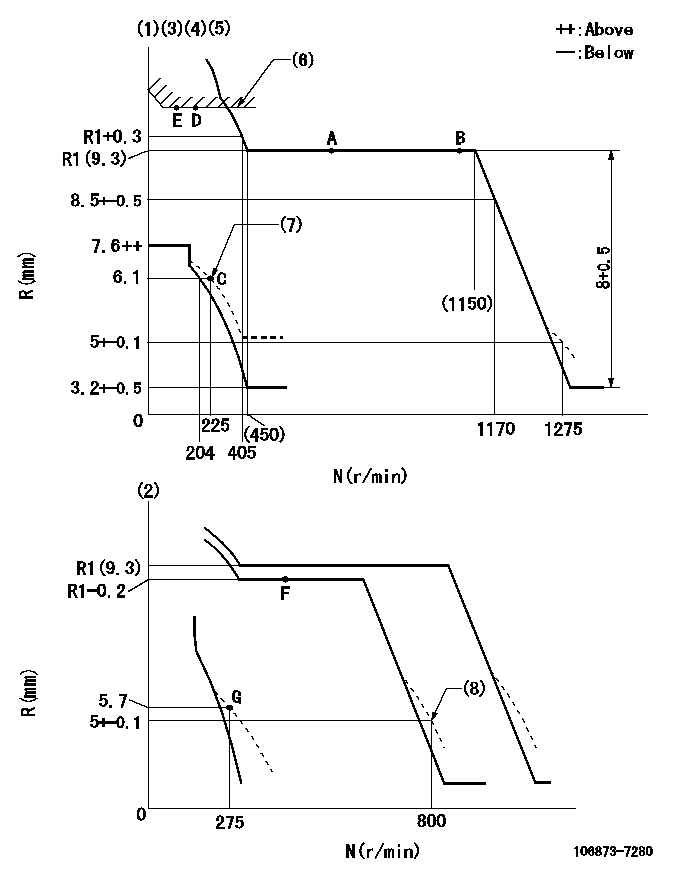
N:Pump speed
R:Rack position (mm)
(1)Adjust with speed control lever at full position (minimum-maximum speed specification)
(2)Adjust with the load control lever in the full position (variable speed specification).
(3)Lever ratio: RT
(4)Target shim dimension: TH
(5)Tolerance for racks not indicated: +-0.05mm.
(6)Excess fuel setting for starting: SXL
(7)Damper spring setting
(8)When air cylinder is operating.
----------
RT=1 TH=2mm SXL=12+-0.1mm
----------
----------
RT=1 TH=2mm SXL=12+-0.1mm
----------
Speed control lever angle
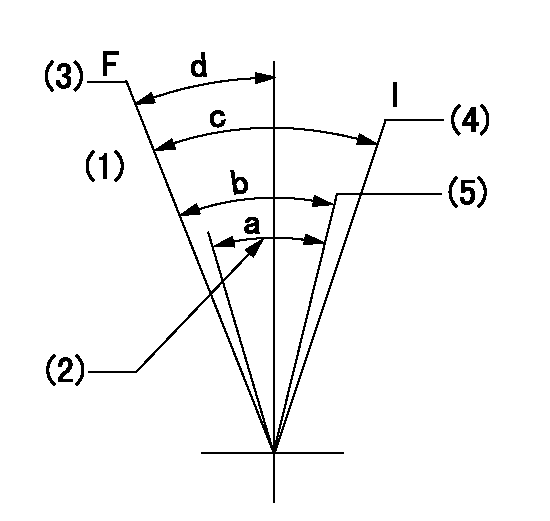
F:Full speed
I:Idle
(1)-
(2)Air cylinder's adjustable range
(3)Pump speed = aa
(4)Pump speed = bb
(5)Pump speed cc
----------
aa=1275r/min bb=275r/min cc=800r/min
----------
a=(7.5deg) b=(7.5deg)+-5deg c=(14.5deg)+-5deg d=(5deg)+-5deg
----------
aa=1275r/min bb=275r/min cc=800r/min
----------
a=(7.5deg) b=(7.5deg)+-5deg c=(14.5deg)+-5deg d=(5deg)+-5deg
0000000901

F:Full load
I:Idle
(1)Stopper bolt setting
----------
----------
a=10deg+-5deg b=23deg+-3deg
----------
----------
a=10deg+-5deg b=23deg+-3deg
Stop lever angle

S:Stop the pump.
(1)Rack position = aa
(2)Stopper bolt setting
(3)Free (at delivery)
----------
aa=4-0.5mm
----------
a=10.5deg+-5deg b=56deg+7deg-5deg
----------
aa=4-0.5mm
----------
a=10.5deg+-5deg b=56deg+7deg-5deg
0000001501 MICRO SWITCH
Adjustment of the micro-switch
Adjust the bolt to obtain the following lever position when the micro-switch is ON.
(1)Speed N1
(2)Rack position Ra
----------
N1=325r/min Ra=5.6+-0.1mm
----------
----------
N1=325r/min Ra=5.6+-0.1mm
----------
0000001601 2-STAGE CHANGEPVER DEVICE

RFD governor 2 stage changeover mechanism adjustment outline
(A) Bolt
(B) bolt
(c) Nut
(D) Return spring
(E) Bolt
(F) Bolt
(G) Screw
(H) Bolt
(I) Load lever
(J) Speed lever
(K) Air cylinder
(M Air inlet
Figure 1 is only for reference. Lever shape, etc, may vary.
1. Minimum-maximum speed specification adjustment (when running)
(a) Without applying air to the air cylinder, loosen bolts (A) and (B).
(1)High speed return L setting
(a) In the speed range Nf~Nf - 300r/min, adjust using the speed adjusting bolt to determine the temporary beginning of high speed control speed.
(b) Determine the rack position in the vicinity of Rf using the full load lever.
(c) Increase speed and confirm return distance L.
(d) Adjust using the tension lever bolt to obtain L.
(2)Setting full load rack position Rf
(a) Move the load control lever to the full side.
(b) Adjust the full load adjusting bolt so that Rf can be obtained, then fix.
(3)Setting the beginning of high speed operation Nf
(a) Adjust using bolt (E) so that Nf can be obtained, and then fix.
(4)Idle control setting (Re, Ni, Rc)
(a) Set the speed at Ns + 200r/min and move the load control lever to the idle side.
(b) Fix the lever in the position where Re can be obtained.
(c) Next, decrease speed to Ni and screw in the idle spring.
(d) Adjust to obtain rack position Ri.
(e) Increase the speed and after confirming that the rack position is Re at Ns, set the speed at 0.
(f) Confirm protrusion position Rc at idle.
(5)Damper spring adjustment
(a) Increase speed and set the speed at the rack position Rd - 0.1 mm
(b) Set using the damper spring so that the rack position Rd can be obtained.
(c) When Rd is not specified, Rd = Ri - 0.5 mm.
(6)High speed droop confirmation
(a) Return the load control lever to the full load lever position.
(b) Increase the speed and confirm that Rf can be obtained at Nf r/min.
(c) Confirm that speed is Nh at rack position Rh.
2. Variable speed specification adjustment (at operation)
(a) Remove return spring (D).
(b) Apply air pressure of 245~294 kPa {2.5~3 kg/cm2} to the air cylinder.
(c) Perform the following adjustment in this condition.
(1)Setting full load rack position Rf'
(a) Pull the load lever to the idle side.
(b) Obtain rack position Rf' using the nut (C). (Pump speed is Nf'-50 r/min.)
(2)Setting full speed Nf'
(a) Adjust using bolt (B) so that Nf can be obtained, and then fix.
(3)Low speed side setting
(a) At 350r/min, set bolt (F) at beginning of governor operation position, then fix.
3. Bolt (A) adjustment
(1)Install return spring (D) and perform the adjustments below at air pressure 0.
(a) Set at speed Nf using bolt (E).
(b) Screw in bolt (A).
(c) Screw in 1 more turn from the speed lever contact position
(d) Fix bolt (A).
(e) At this time confirm that the air cylinder's shaft moves approximately 1 mm towards the governor.
4. Lever operation confirmation using the air cylinder
(1)Apply 588 kPa {6 kg/cm2} air pressure to the air cylinder.
(2)Confirm that the cylinder piston is moved 50 mm by the spring (D).
----------
----------
----------
----------
Timing setting

(1)Pump vertical direction
(2)Coupling's key groove position at No 1 cylinder's beginning of injection
(3)-
(4)-
----------
----------
a=(40deg)
----------
----------
a=(40deg)
Information:
Prior to stopping an engine that is being operated at low loads, run the engine at low speed for 30 seconds before stopping. If the engine has been operating at high load, then it should be run at low speed for three to five minutes to reduce and stabilize internal engine coolant and oil temperatures before stopping. Avoiding hot engine shutdowns will maximize turbocharger shaft and bearing life. Make sure the Engine Stopping procedure is understood. Follow the engine stopping procedure outlined below to allow the engine to cool. Make sure the Engine Stopping procedure is understood. Refer to the Engine Control, Monitoring and Protection topic for information regarding GSC control panel.The engine may be shutdown in several ways. To manually stop the engine, refer to the following information and instructions. The engine is equipped with an Emergency Stop Push Button (ESPB) and an Engine Control Switch (ECS). The ECS has four positions:* OFF/RESET* AUTO* MAN. START* COOLDOWN STOPTo manually stop the engine the Engine Control Switch (ECS) may be turned to the COOLDOWN STOP, AUTOmatic or OFF/RESET positions.Emergency Stop Procedure
Emergency stop controls are for EMERGENCY use ONLY. DO NOT use Emergency Stop Pushbutton (ESPB) for normal stopping procedure. Do NOT start the engine until the problem necessitating the emergency stop has been located and corrected.
The Emergency Stop Pushbutton is located on the front of the control panel. The Emergency Stop Pushbutton will cause immediate shutoff of fuel and/or air. Emergency shutoff controls (including any auxiliary Emergency Stop inputs) should only be used when an emergency exists, and not used to routinely stop the engine. * Emergency stops may be made through the Emergency Stop Pushbutton (ESPB). If the need for emergency engine shutdown occurs, Push the EMERGENCY STOP Pushbutton located on the control panel. This will activate the air and/or fuel shutoffs.* Reset the EMERGENCY STOP Pushbutton (pull out and rotate the button in the direction indicated on the button). Some EMERGENCY STOP Pushbuttons can be pulled out to reset, not requiring any rotation. Manual Fuel Shutoff Lever
A manual shutdown shaft/lever is provided to override the governor control of the engine. This shutdown will only move the fuel control linkage to the fuel OFF position to starve the engine of fuel. The engine will coast to a stop. Be sure to secure any external system components that have been operating to support the engine operation.Manual Stop Procedure
Follow the engine stopping procedure outlined below, to allow the engine to cool. Make sure the Engine Stopping procedure is clearly understood.1. Open the main electrical circuit breaker to remove the load. Lower engine speed with the Manual Speed Potentiometer (MSP) on the control panel. 2. Check the crankcase oil level while the engine is idling. Maintain the oil level between the ADD and FULL marks on the ENGINE AT LOW IDLE WITH WARM OIL side of the dipstick. 3. Adjust all other control systems that must be regulated prior to engine shutoff (voltage regulator, idle/rated switch, etc.). Reduce engine
Emergency stop controls are for EMERGENCY use ONLY. DO NOT use Emergency Stop Pushbutton (ESPB) for normal stopping procedure. Do NOT start the engine until the problem necessitating the emergency stop has been located and corrected.
The Emergency Stop Pushbutton is located on the front of the control panel. The Emergency Stop Pushbutton will cause immediate shutoff of fuel and/or air. Emergency shutoff controls (including any auxiliary Emergency Stop inputs) should only be used when an emergency exists, and not used to routinely stop the engine. * Emergency stops may be made through the Emergency Stop Pushbutton (ESPB). If the need for emergency engine shutdown occurs, Push the EMERGENCY STOP Pushbutton located on the control panel. This will activate the air and/or fuel shutoffs.* Reset the EMERGENCY STOP Pushbutton (pull out and rotate the button in the direction indicated on the button). Some EMERGENCY STOP Pushbuttons can be pulled out to reset, not requiring any rotation. Manual Fuel Shutoff Lever
A manual shutdown shaft/lever is provided to override the governor control of the engine. This shutdown will only move the fuel control linkage to the fuel OFF position to starve the engine of fuel. The engine will coast to a stop. Be sure to secure any external system components that have been operating to support the engine operation.Manual Stop Procedure
Follow the engine stopping procedure outlined below, to allow the engine to cool. Make sure the Engine Stopping procedure is clearly understood.1. Open the main electrical circuit breaker to remove the load. Lower engine speed with the Manual Speed Potentiometer (MSP) on the control panel. 2. Check the crankcase oil level while the engine is idling. Maintain the oil level between the ADD and FULL marks on the ENGINE AT LOW IDLE WITH WARM OIL side of the dipstick. 3. Adjust all other control systems that must be regulated prior to engine shutoff (voltage regulator, idle/rated switch, etc.). Reduce engine
Have questions with 106873-7280?
Group cross 106873-7280 ZEXEL
Mitsubishi
Mitsubishi
Mitsubishi
Mitsubishi
Mitsubishi
106873-7280
9 400 611 036
ME094088
INJECTION-PUMP ASSEMBLY
8DC9
8DC9