Information injection-pump assembly
ZEXEL
106873-7131
1068737131
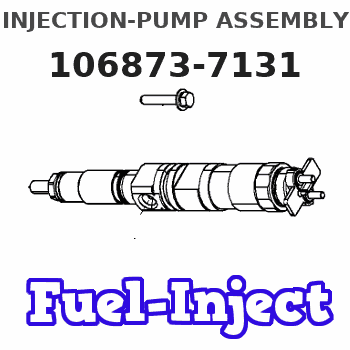
Rating:
Cross reference number
ZEXEL
106873-7131
1068737131
Zexel num
Bosch num
Firm num
Name
106873-7131
INJECTION-PUMP ASSEMBLY
Calibration Data:
Adjustment conditions
Test oil
1404 Test oil ISO4113 or {SAEJ967d}
1404 Test oil ISO4113 or {SAEJ967d}
Test oil temperature
degC
40
40
45
Nozzle and nozzle holder
105780-8250
Bosch type code
1 688 901 101
Nozzle
105780-0120
Bosch type code
1 688 901 990
Nozzle holder
105780-2190
Opening pressure
MPa
20.7
Opening pressure
kgf/cm2
211
Injection pipe
Outer diameter - inner diameter - length (mm) mm 8-3-600
Outer diameter - inner diameter - length (mm) mm 8-3-600
Overflow valve
131425-0220
Overflow valve opening pressure
kPa
157
123
191
Overflow valve opening pressure
kgf/cm2
1.6
1.25
1.95
Tester oil delivery pressure
kPa
255
255
255
Tester oil delivery pressure
kgf/cm2
2.6
2.6
2.6
Direction of rotation (viewed from drive side)
Right R
Right R
Injection timing adjustment
Direction of rotation (viewed from drive side)
Right R
Right R
Injection order
1-2-7-3-
4-5-6-8
Pre-stroke
mm
3.9
3.85
3.95
Beginning of injection position
Governor side NO.1
Governor side NO.1
Difference between angles 1
Cyl.1-2 deg. 45 44.5 45.5
Cyl.1-2 deg. 45 44.5 45.5
Difference between angles 2
Cal 1-7 deg. 90 89.5 90.5
Cal 1-7 deg. 90 89.5 90.5
Difference between angles 3
Cal 1-3 deg. 135 134.5 135.5
Cal 1-3 deg. 135 134.5 135.5
Difference between angles 4
Cal 1-4 deg. 180 179.5 180.5
Cal 1-4 deg. 180 179.5 180.5
Difference between angles 5
Cal 1-5 deg. 225 224.5 225.5
Cal 1-5 deg. 225 224.5 225.5
Difference between angles 6
Cal 1-6 deg. 270 269.5 270.5
Cal 1-6 deg. 270 269.5 270.5
Difference between angles 7
Cal 1-8 deg. 315 314.5 315.5
Cal 1-8 deg. 315 314.5 315.5
Injection quantity adjustment
Adjusting point
-
Rack position
12.8
Pump speed
r/min
650
650
650
Each cylinder's injection qty
mm3/st.
148
143.6
152.4
Basic
*
Fixing the rack
*
Standard for adjustment of the maximum variation between cylinders
*
Injection quantity adjustment_02
Adjusting point
Z
Rack position
8.5+-0.5
Pump speed
r/min
400
400
400
Each cylinder's injection qty
mm3/st.
23
19.5
26.5
Fixing the rack
*
Standard for adjustment of the maximum variation between cylinders
*
Injection quantity adjustment_03
Adjusting point
A
Rack position
R1(12.8)
Pump speed
r/min
650
650
650
Average injection quantity
mm3/st.
148
147
149
Basic
*
Fixing the lever
*
Injection quantity adjustment_04
Adjusting point
B
Rack position
R1+1.15
Pump speed
r/min
1100
1100
1100
Average injection quantity
mm3/st.
145
141
149
Fixing the lever
*
Test data Ex:
Governor adjustment
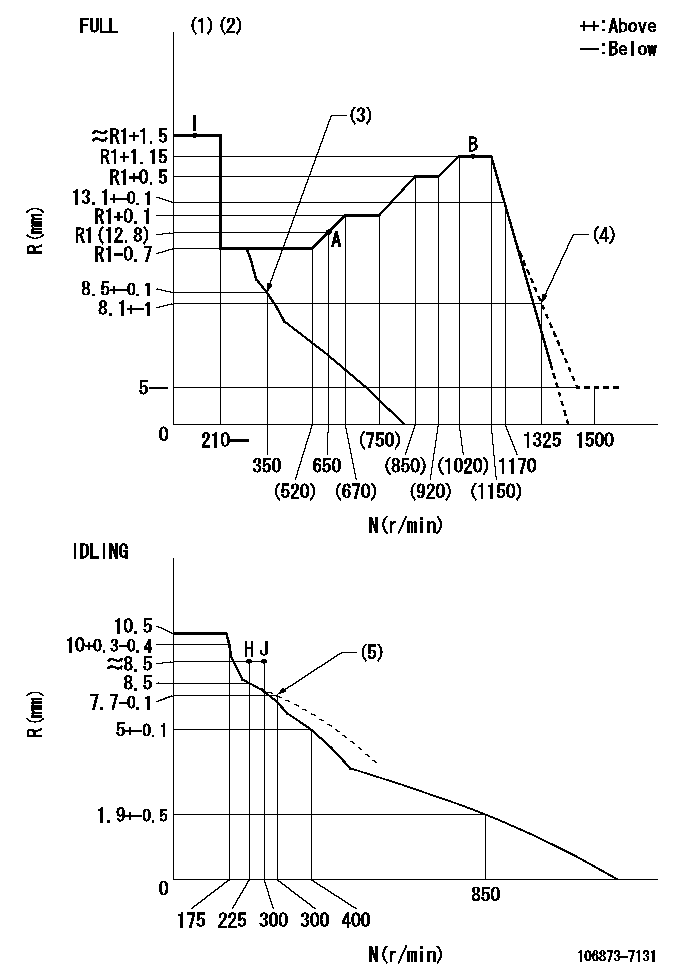
N:Pump speed
R:Rack position (mm)
(1)Torque cam stamping: T1
(2)Tolerance for racks not indicated: +-0.05mm.
(3)Air cylinder OFF
(4)Air cylinder ON
(5)Damper spring setting
----------
T1=AC39
----------
----------
T1=AC39
----------
Timer adjustment

(1)Adjusting range
(2)Step response time
(N): Speed of the pump
(L): Load
(theta) Advance angle
(Srd1) Step response time 1
(Srd2) Step response time 2
1. Adjusting conditions for the variable timer
(1)Adjust the clearance between the pickup and the protrusion to L.
----------
L=1-0.2mm N2=800r/min C2=(10)deg t1=2.5--sec. t2=2.5--sec.
----------
N1=750++r/min P1=0kPa(0kgf/cm2) P2=392kPa(4kgf/cm2) C1=10+-0.3deg R01=0/4load R02=4/4load
----------
L=1-0.2mm N2=800r/min C2=(10)deg t1=2.5--sec. t2=2.5--sec.
----------
N1=750++r/min P1=0kPa(0kgf/cm2) P2=392kPa(4kgf/cm2) C1=10+-0.3deg R01=0/4load R02=4/4load
Speed control lever angle
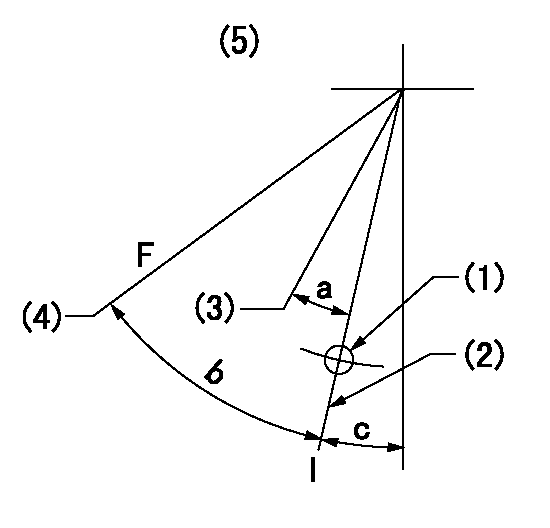
F:Full speed
I:Idle
(1)Use the hole at R = aa
(2)Stopper bolt set position 'H'
(3)When air cylinder OFF.
(4)When air cylinder ON.
(5)Viewed from feed pump side.
----------
aa=37.5mm
----------
a=(10deg) b=35deg+-3deg c=30deg+-5deg
----------
aa=37.5mm
----------
a=(10deg) b=35deg+-3deg c=30deg+-5deg
Stop lever angle
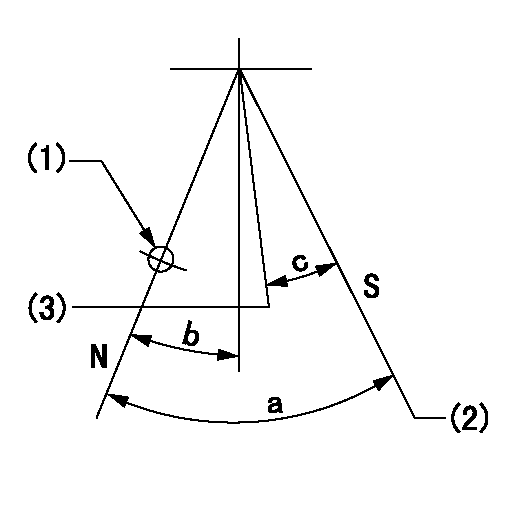
N:Pump normal
S:Stop the pump.
(1)Use the hole at R = aa
(2)Set the stopper bolt so that speed = bb and rack position = cc. (Confirm non-injection.)
(3)Normal engine position (Rack position corresponding to dd)
----------
aa=54mm bb=1100r/min cc=3.5+-0.3mm dd=18mm
----------
a=41deg+-5deg b=5.5deg+-5deg c=(31deg)
----------
aa=54mm bb=1100r/min cc=3.5+-0.3mm dd=18mm
----------
a=41deg+-5deg b=5.5deg+-5deg c=(31deg)
0000001501 MICRO SWITCH
Adjustment of the micro-switch
Adjust the bolt to obtain the following lever position when the micro-switch is ON.
(1)Speed N1
(2)Rack position Ra
----------
N1=325r/min Ra=8.5+-0.1mm
----------
----------
N1=325r/min Ra=8.5+-0.1mm
----------
0000001601 RACK SENSOR
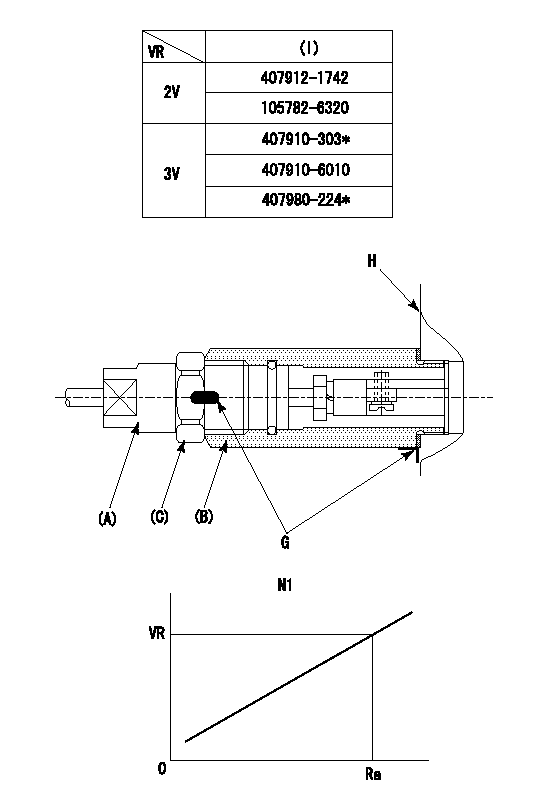
(VR) measurement voltage
(I) Part number of the control unit
(G) Apply red paint.
(H): End surface of the pump
1. Rack sensor adjustment (-0620)
(1)Fix the speed control lever at the full position
(2)Set the speed to N1 r/min.
(If the boost compensator is provided, apply boost pressure.)
(3)Adjust the bobbin (A) so that the rack sensor's output voltage is VR+-0.01.
(4)At that time, rack position must be Ra.
(5)Apply G at two places.
Connecting part between the joint (B) and the nut (F)
Connecting part between the joint (B) and the end surface of the pump (H)
----------
N1=1100r/min Ra=R1(12.8)+1.15mm
----------
----------
N1=1100r/min Ra=R1(12.8)+1.15mm
----------
0000001701 AIR CYLINDER
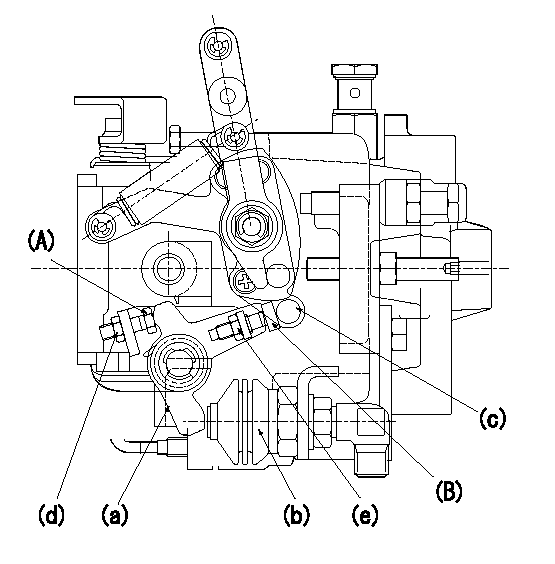
(A) stopper bolt
(B) stopper bolt
(a) lever
(b) air cylinder
(c) speed lever
(d) Nut
(e) nut
1. Stopper bolt A adjusting method
(1)When the air cylinder pressure is P1, confirm that there is a clearance between the stopper bolt (A) and the lever (a).
(2)Then, screw in the stopper bolt A and temporarily set where it contacts the stop lever a.
(3)Apply P2 to the air cylinder.
(4)Confirm that the speed lever (c) operates between idling and full speed positions.
(5)Fix the stopper bolt A using nut d.
2. Stopper bolt <B> adjustment method.
(1)At air cylinder pressure P1, pump speed N1 and rack position is Ra, adjust stopper bolt (B) so that the speed lever (c) is in the stop position.
(2)Move the lever a several times and then fix the stopper bolt B using the nut e.
(3)Nut d tightening torque: T1
(4)Nut e tightening torque: T2
----------
P1=0kPa(0kgf/cm2) P2=392+98kPa(4+1kgf/cm2) N1=350r/min Ra=8.5+-0.1mm T1=4.9~7N-m(0.5~0.7kgf-m) T2=4.9~7N-m(0.5~0.7kgf-m)
----------
----------
P1=0kPa(0kgf/cm2) P2=392+98kPa(4+1kgf/cm2) N1=350r/min Ra=8.5+-0.1mm T1=4.9~7N-m(0.5~0.7kgf-m) T2=4.9~7N-m(0.5~0.7kgf-m)
----------
Timing setting

(1)Pump vertical direction
(2)Coupling's key groove position at No 1 cylinder's beginning of injection
(3)B.T.D.C.: aa
(4)-
----------
aa=6deg
----------
a=(50deg)
----------
aa=6deg
----------
a=(50deg)
Information:
Engine Description
Older 3408 and 3412 models may by precombustion chamber (PC) type engines. Newer 3408 and 3412 models are direct injection (DI) engines.A mechanical governor controls the fuel injection pump output to maintain the engine rpm selected by the operator. The fuel injection pump meters and pumps fuel under high pressure to a fuel injection nozzle for each cylinder. An automatic timing device advances or retards fuel injection to provide the best fuel injection timing over the full range of engine speed.The air/fuel ratio control, located on the governor, restricts the movement of the fuel rack, allowing only the proper amount of fuel to be injected into the cylinders during acceleration, to minimize exhaust smoke.These engines are available as turbocharged (T) or turbocharged and aftercooled (TA). Inlet air is filtered by an air cleaner before entering the engine cylinders. In turbocharged engines, the filtered inlet air is compressed by a turbocharger before entering the engine cylinders. The turbocharger is driven by the engine exhaust.There are four in-head valves (two inlet valves and two exhaust valves) for each cylinder. The camshaft actuates the rocker arms and the valves through mechanical lifters and push rods.The jacket water cooling system uses an expansion tank and a gear driven centrifugal water pump. The engine coolant is circulated by passing through the oil cooler first, then to the engine block and cylinder head. One water temperature regulator for each cylinder bank regulates engine coolant temperature by restricting coolant flow for quick engine warm-up. The regulator opens to allow free circulation of coolant after operating temperature has been reached.The watercooled exhaust manifolds, risers and turbochargers are designed to minimize radiated heat in the engine room.Lubrication of the engine is accomplished by a gear-type pump and bypass valves. The pump provides full pressure lubrication to the engine internal and external parts. The engine lubricating oil (both cooled and filtered) provides unrestricted flow to engine parts when oil viscosity is high or if the oil cooler is restricted or if the oil filter elements become plugged.The engines are available with SAE standard counterclockwise rotation (CCW when viewed from rear of engine). The engines can be equipped with either the SAE No.1 flywheel or the SAE No.0 flywheel to mate with various marine gears. Several marine gear manufacturers offer marine transmissions for the engines through local distributors.Engine Specifications
3408 Engine
3412 Engine
Older 3408 and 3412 models may by precombustion chamber (PC) type engines. Newer 3408 and 3412 models are direct injection (DI) engines.A mechanical governor controls the fuel injection pump output to maintain the engine rpm selected by the operator. The fuel injection pump meters and pumps fuel under high pressure to a fuel injection nozzle for each cylinder. An automatic timing device advances or retards fuel injection to provide the best fuel injection timing over the full range of engine speed.The air/fuel ratio control, located on the governor, restricts the movement of the fuel rack, allowing only the proper amount of fuel to be injected into the cylinders during acceleration, to minimize exhaust smoke.These engines are available as turbocharged (T) or turbocharged and aftercooled (TA). Inlet air is filtered by an air cleaner before entering the engine cylinders. In turbocharged engines, the filtered inlet air is compressed by a turbocharger before entering the engine cylinders. The turbocharger is driven by the engine exhaust.There are four in-head valves (two inlet valves and two exhaust valves) for each cylinder. The camshaft actuates the rocker arms and the valves through mechanical lifters and push rods.The jacket water cooling system uses an expansion tank and a gear driven centrifugal water pump. The engine coolant is circulated by passing through the oil cooler first, then to the engine block and cylinder head. One water temperature regulator for each cylinder bank regulates engine coolant temperature by restricting coolant flow for quick engine warm-up. The regulator opens to allow free circulation of coolant after operating temperature has been reached.The watercooled exhaust manifolds, risers and turbochargers are designed to minimize radiated heat in the engine room.Lubrication of the engine is accomplished by a gear-type pump and bypass valves. The pump provides full pressure lubrication to the engine internal and external parts. The engine lubricating oil (both cooled and filtered) provides unrestricted flow to engine parts when oil viscosity is high or if the oil cooler is restricted or if the oil filter elements become plugged.The engines are available with SAE standard counterclockwise rotation (CCW when viewed from rear of engine). The engines can be equipped with either the SAE No.1 flywheel or the SAE No.0 flywheel to mate with various marine gears. Several marine gear manufacturers offer marine transmissions for the engines through local distributors.Engine Specifications
3408 Engine
3412 Engine
Have questions with 106873-7131?
Group cross 106873-7131 ZEXEL
106873-7131
INJECTION-PUMP ASSEMBLY