Information injection-pump assembly
BOSCH
9 400 618 460
9400618460
ZEXEL
106873-7010
1068737010
MITSUBISHI
ME093327
me093327
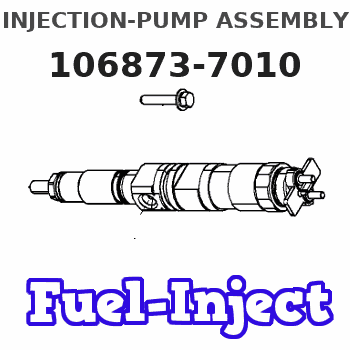
Rating:
Service parts 106873-7010 INJECTION-PUMP ASSEMBLY:
1.
_
7.
COUPLING PLATE
8.
_
9.
_
11.
Nozzle and Holder
ME091246
12.
Open Pre:MPa(Kqf/cm2)
17.7{180}/21.6{220}
15.
NOZZLE SET
Include in #1:
106873-7010
as INJECTION-PUMP ASSEMBLY
Cross reference number
BOSCH
9 400 618 460
9400618460
ZEXEL
106873-7010
1068737010
MITSUBISHI
ME093327
me093327
Zexel num
Bosch num
Firm num
Name
106873-7010
9 400 618 460
ME093327 MITSUBISHI
INJECTION-PUMP ASSEMBLY
8DC9 K 14CD INJECTION PUMP ASSY PE8P PE
8DC9 K 14CD INJECTION PUMP ASSY PE8P PE
Calibration Data:
Adjustment conditions
Test oil
1404 Test oil ISO4113 or {SAEJ967d}
1404 Test oil ISO4113 or {SAEJ967d}
Test oil temperature
degC
40
40
45
Nozzle and nozzle holder
105780-8140
Bosch type code
EF8511/9A
Nozzle
105780-0000
Bosch type code
DN12SD12T
Nozzle holder
105780-2080
Bosch type code
EF8511/9
Opening pressure
MPa
17.2
Opening pressure
kgf/cm2
175
Injection pipe
Outer diameter - inner diameter - length (mm) mm 8-3-600
Outer diameter - inner diameter - length (mm) mm 8-3-600
Overflow valve
134424-1320
Overflow valve opening pressure
kPa
157
123
191
Overflow valve opening pressure
kgf/cm2
1.6
1.25
1.95
Tester oil delivery pressure
kPa
157
157
157
Tester oil delivery pressure
kgf/cm2
1.6
1.6
1.6
Direction of rotation (viewed from drive side)
Right R
Right R
Injection timing adjustment
Direction of rotation (viewed from drive side)
Right R
Right R
Injection order
1-2-7-3-
4-5-6-8
Pre-stroke
mm
4.8
4.75
4.85
Beginning of injection position
Governor side NO.1
Governor side NO.1
Difference between angles 1
Cyl.1-2 deg. 45 44.5 45.5
Cyl.1-2 deg. 45 44.5 45.5
Difference between angles 2
Cal 1-7 deg. 90 89.5 90.5
Cal 1-7 deg. 90 89.5 90.5
Difference between angles 3
Cal 1-3 deg. 135 134.5 135.5
Cal 1-3 deg. 135 134.5 135.5
Difference between angles 4
Cal 1-4 deg. 180 179.5 180.5
Cal 1-4 deg. 180 179.5 180.5
Difference between angles 5
Cal 1-5 deg. 225 224.5 225.5
Cal 1-5 deg. 225 224.5 225.5
Difference between angles 6
Cal 1-6 deg. 270 269.5 270.5
Cal 1-6 deg. 270 269.5 270.5
Difference between angles 7
Cal 1-8 deg. 315 314.5 315.5
Cal 1-8 deg. 315 314.5 315.5
Injection quantity adjustment
Adjusting point
-
Rack position
8.3
Pump speed
r/min
700
700
700
Each cylinder's injection qty
mm3/st.
85
82.4
87.6
Basic
*
Fixing the rack
*
Standard for adjustment of the maximum variation between cylinders
*
Injection quantity adjustment_02
Adjusting point
C
Rack position
5.9+-0.5
Pump speed
r/min
275
275
275
Each cylinder's injection qty
mm3/st.
20
17
23
Fixing the rack
*
Standard for adjustment of the maximum variation between cylinders
*
Injection quantity adjustment_03
Adjusting point
A
Rack position
R1(8.3)
Pump speed
r/min
700
700
700
Average injection quantity
mm3/st.
85
84
86
Basic
*
Fixing the lever
*
Injection quantity adjustment_04
Adjusting point
B
Rack position
R1(8.3)
Pump speed
r/min
1150
1150
1150
Average injection quantity
mm3/st.
101.4
97.2
105.6
Difference in delivery
mm3/st.
8.4
8.4
8.4
Fixing the lever
*
Injection quantity adjustment_05
Adjusting point
E
Rack position
-
Pump speed
r/min
100
100
100
Average injection quantity
mm3/st.
130
90
170
Fixing the lever
*
Remarks
After startup boost setting
After startup boost setting
Timer adjustment
Pump speed
r/min
930--
Advance angle
deg.
0
0
0
Load
3/4
Remarks
Start
Start
Timer adjustment_02
Pump speed
r/min
880
Advance angle
deg.
0.5
Load
3/4
Timer adjustment_03
Pump speed
r/min
1100
Advance angle
deg.
5
4.5
5.5
Load
4/4
Remarks
Finish
Finish
Test data Ex:
Governor adjustment
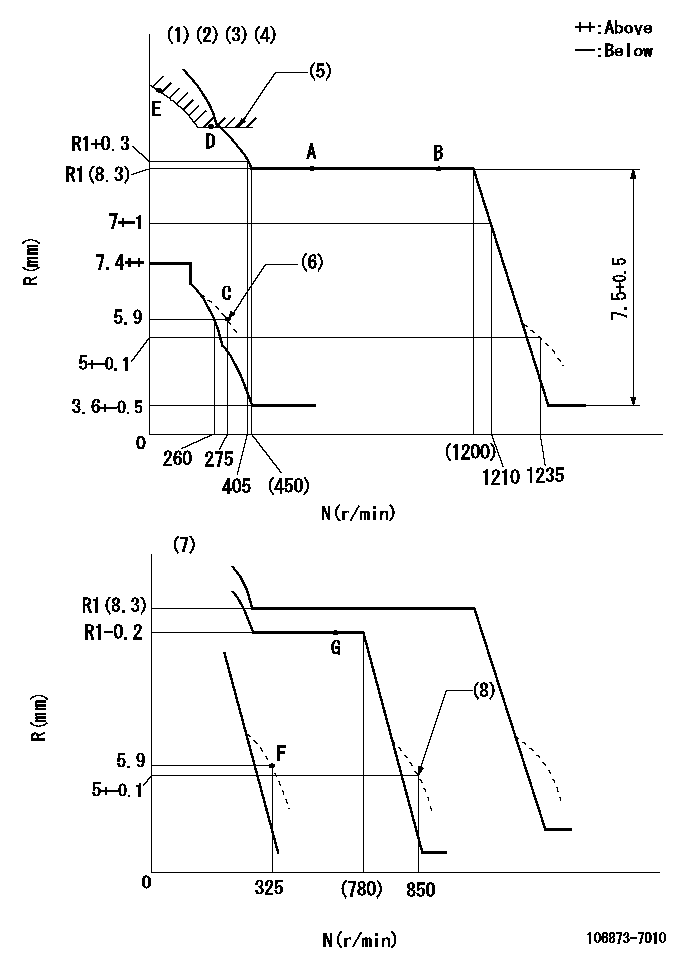
N:Pump speed
R:Rack position (mm)
(1)Adjust with speed control lever at full position (minimum-maximum speed specification)
(2)Lever ratio: RT
(3)Target shim dimension: TH
(4)Tolerance for racks not indicated: +-0.05mm.
(5)Excess fuel setting for starting: SXL
(6)Damper spring setting
(7)Adjust with the load control lever in the full position (variable speed specification).
(8)When air cylinder is operating.
----------
RT=1 TH=1.5mm SXL=11.3+-0.1mm
----------
----------
RT=1 TH=1.5mm SXL=11.3+-0.1mm
----------
Speed control lever angle
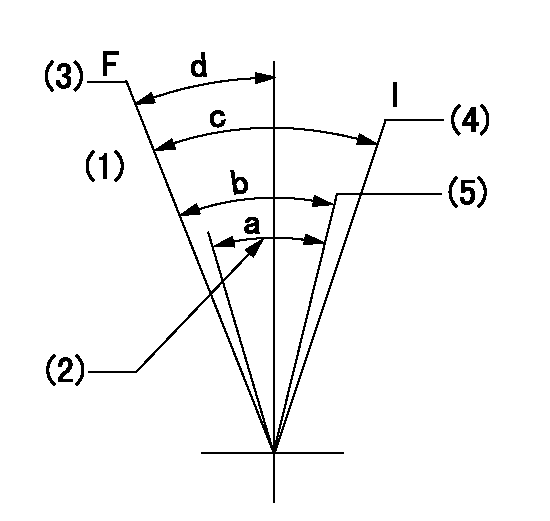
F:Full speed
I:Idle
(1)-
(2)Air cylinder's adjustable range
(3)Pump speed = aa
(4)Pump speed = bb
(5)Pump speed cc
----------
aa=1235r/min bb=325r/min cc=850r/min
----------
a=(12deg) b=(12deg)+-5deg c=(21.5deg)+-5deg d=7deg+-5deg
----------
aa=1235r/min bb=325r/min cc=850r/min
----------
a=(12deg) b=(12deg)+-5deg c=(21.5deg)+-5deg d=7deg+-5deg
0000000901

F:Full load
I:Idle
(1)Stopper bolt setting
----------
----------
a=10deg+-5deg b=17.5deg+-3deg
----------
----------
a=10deg+-5deg b=17.5deg+-3deg
Stop lever angle
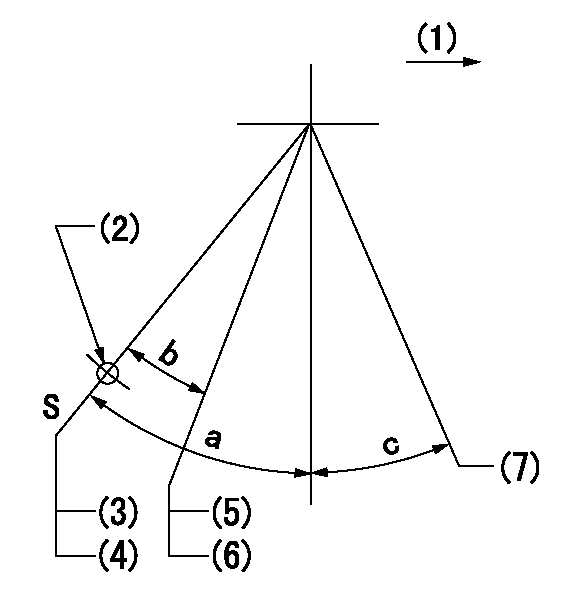
S:Stop the pump.
(1)Drive side
(2)Use the hole at R = aa
(3)Rack position bb
(4)Stopper bolt setting
(5)Engine manufacturer's normal use
(6)Rack position = cc
(7)Free (at delivery)
----------
aa=36mm bb=4-0.5mm cc=11.7mm
----------
a=45.5deg+7deg-5deg b=22deg+-5deg c=10.5deg
----------
aa=36mm bb=4-0.5mm cc=11.7mm
----------
a=45.5deg+7deg-5deg b=22deg+-5deg c=10.5deg
0000001501 MICRO SWITCH
Adjustment of the micro-switch
Adjust the bolt to obtain the following lever position when the micro-switch is ON.
(1)Speed N1
(2)Rack position Ra
----------
N1=325r/min Ra=5.9+-0.1mm
----------
----------
N1=325r/min Ra=5.9+-0.1mm
----------
0000001601 2-STAGE CHANGEOVER DEVICE

RFD governor 2 stage changeover mechanism adjustment outline
(A) Bolt
(B) bolt
(c) Nut
(D) Return spring
(E) Bolt
(F) Bolt
(G) Screw
(H) Bolt
(I) Load lever
(J) Speed lever
(K) Air cylinder
(M Air inlet
Figure 1 is only for reference. Lever shape, etc, may vary.
1. Minimum-maximum speed specification adjustment (when running)
(a) Without applying air to the air cylinder, loosen bolts (A) and (B).
(1)High speed return L setting
(a) In the speed range Nf~Nf - 300r/min, adjust using the speed adjusting bolt to determine the temporary beginning of high speed control speed.
(b) Determine the rack position in the vicinity of Rf using the full load lever.
(c) Increase speed and confirm return distance L.
(d) Adjust using the tension lever bolt to obtain L.
(2)Setting full load rack position Rf
(a) Move the load control lever to the full side.
(b) Adjust the full load adjusting bolt so that Rf can be obtained, then fix.
(3)Setting the beginning of high speed operation Nf
(a) Adjust using bolt (E) so that Nf can be obtained, and then fix.
(4)Idle control setting (Re, Ni, Rc)
(a) Set the speed at Ns + 200r/min and move the load control lever to the idle side.
(b) Fix the lever in the position where Re can be obtained.
(c) Next, decrease speed to Ni and screw in the idle spring.
(d) Adjust to obtain rack position Ri.
(e) Increase the speed and after confirming that the rack position is Re at Ns, set the speed at 0.
(f) Confirm protrusion position Rc at idle.
(5)Damper spring adjustment
(a) Increase speed and set the speed at the rack position Rd - 0.1 mm
(b) Set using the damper spring so that the rack position Rd can be obtained.
(c) When Rd is not specified, Rd = Ri - 0.5 mm.
(6)High speed droop confirmation
(a) Return the load control lever to the full load lever position.
(b) Increase the speed and confirm that Rf can be obtained at Nf r/min.
(c) Confirm that speed is Nh at rack position Rh.
2. Variable speed specification adjustment (at operation)
(a) Remove return spring (D).
(b) Apply air pressure of 245~294 kPa {2.5~3 kg/cm2} to the air cylinder.
(c) Perform the following adjustment in this condition.
(1)Setting full load rack position Rf'
(a) Pull the load lever to the idle side.
(b) Obtain rack position Rf' using the nut (C). (Pump speed is Nf'-50 r/min.)
(2)Setting full speed Nf'
(a) Adjust using bolt (B) so that Nf can be obtained, and then fix.
(3)Low speed side setting
(a) At 350r/min, set bolt (F) at beginning of governor operation position, then fix.
3. Bolt (A) adjustment
(1)Install return spring (D) and perform the adjustments below at air pressure 0.
(a) Set at speed Nf using bolt (E).
(b) Screw in bolt (A).
(c) Screw in 1 more turn from the speed lever contact position
(d) Fix bolt (A).
(e) At this time confirm that the air cylinder's shaft moves approximately 1 mm towards the governor.
4. Lever operation confirmation using the air cylinder
(1)Apply 588 kPa {6 kg/cm2} air pressure to the air cylinder.
(2)Confirm that the cylinder piston is moved 50 mm by the spring (D).
----------
----------
----------
----------
Timing setting

(1)Pump vertical direction
(2)Coupling's key groove position at No 1 cylinder's beginning of injection
(3)-
(4)-
----------
----------
a=(40deg)
----------
----------
a=(40deg)
Information:
Owner Warranty Rights and Obligations
The California Air Resources Board (CARB) and Caterpillar Inc. are pleased to explain the emission control system warranty on your 1993 truck engine.In California, new motor vehicle engines must be designed, built and equipped to meet the state's stringent anti-smog standards. Caterpillar Inc. must warrant the emission control system on your truck engine for the duration of time listed below provided there has not been any abuse, neglect or improper maintenance of your truck engine.Your emission control system may include parts such as the fuel injection system and engine computer, if equipped. Also included may be hoses, connectors, clamps and other emission-related components.Where a warrantable condition exists, Caterpillar Inc. will repair the truck engine at no cost to the owner including diagnosis, parts and labor.Manufacturer's Warranty Coverage
* The emissions warranty period for new truck engines is a duration of 60 months, 100,000 miles (161 000 km), or 3,000 hours of operation, whichever occurs first.* If an emission related part or component on your truck engine is defective, the part or component will be repaired or replaced by Caterpillar Inc. This is your emission control system WARRANTY.Owner's Warranty Responsibilities
* As the truck engine owner, you are responsible for the performance of the required maintenance listed in the truck engine owner's manual (Operation and Maintenance Manual). Caterpillar Inc. recommends that you retain all receipts and records covering the maintenance on your truck engine, but cannot deny warranty solely for the lack of receipts and records or for your failure to ensure the performance of all scheduled maintenance.* You are responsible for presenting your truck engine to a Caterpillar Inc. dealer as soon as a truck engine problem exists. The warranty repairs should be completed in a reasonable amount of time, not to exceed 30 days.* As the truck engine owner, you should also be aware that Caterpillar Inc. may deny you warranty coverage if your truck engine or an emission component or part has failed due to abuse, neglect, improper maintenance or unapproved modifications.If you have questions regarding your warranty rights and responsibilities, contact:Caterpillar Inc.
Manager, Truck Engine Business
Peoria, IL 61629
Phone (309) 578-6288
ORCalifornia Air Resources Board (CARB)
9528 Telstar Ave.
El Monte, CA 91731
Emissions Warranty
Caterpillar Inc. warrants to the initial owner and subsequent owner of a diesel truck engine (powering an on-highway truck), that such engine is:1. Designed, built and equipped so as to conform, at the time of sale, with all applicable regulations adopted by the California Air Resources Board (CARB).2. Free from defects in materials and workmanship in specific emission related parts for a period of 60 months, 100,000 miles (161 000 km) or 3,000 hours of operation, whichever occurs first, after date of delivery to the initial owner.If an emission related part fails during the warranty period, it will be repaired or replaced. Any such part repaired or replaced under warranty is warranted for the remainder of the warranty period.During the term of this warranty, Caterpillar Inc. will provide through a Caterpillar dealer or other establishment
The California Air Resources Board (CARB) and Caterpillar Inc. are pleased to explain the emission control system warranty on your 1993 truck engine.In California, new motor vehicle engines must be designed, built and equipped to meet the state's stringent anti-smog standards. Caterpillar Inc. must warrant the emission control system on your truck engine for the duration of time listed below provided there has not been any abuse, neglect or improper maintenance of your truck engine.Your emission control system may include parts such as the fuel injection system and engine computer, if equipped. Also included may be hoses, connectors, clamps and other emission-related components.Where a warrantable condition exists, Caterpillar Inc. will repair the truck engine at no cost to the owner including diagnosis, parts and labor.Manufacturer's Warranty Coverage
* The emissions warranty period for new truck engines is a duration of 60 months, 100,000 miles (161 000 km), or 3,000 hours of operation, whichever occurs first.* If an emission related part or component on your truck engine is defective, the part or component will be repaired or replaced by Caterpillar Inc. This is your emission control system WARRANTY.Owner's Warranty Responsibilities
* As the truck engine owner, you are responsible for the performance of the required maintenance listed in the truck engine owner's manual (Operation and Maintenance Manual). Caterpillar Inc. recommends that you retain all receipts and records covering the maintenance on your truck engine, but cannot deny warranty solely for the lack of receipts and records or for your failure to ensure the performance of all scheduled maintenance.* You are responsible for presenting your truck engine to a Caterpillar Inc. dealer as soon as a truck engine problem exists. The warranty repairs should be completed in a reasonable amount of time, not to exceed 30 days.* As the truck engine owner, you should also be aware that Caterpillar Inc. may deny you warranty coverage if your truck engine or an emission component or part has failed due to abuse, neglect, improper maintenance or unapproved modifications.If you have questions regarding your warranty rights and responsibilities, contact:Caterpillar Inc.
Manager, Truck Engine Business
Peoria, IL 61629
Phone (309) 578-6288
ORCalifornia Air Resources Board (CARB)
9528 Telstar Ave.
El Monte, CA 91731
Emissions Warranty
Caterpillar Inc. warrants to the initial owner and subsequent owner of a diesel truck engine (powering an on-highway truck), that such engine is:1. Designed, built and equipped so as to conform, at the time of sale, with all applicable regulations adopted by the California Air Resources Board (CARB).2. Free from defects in materials and workmanship in specific emission related parts for a period of 60 months, 100,000 miles (161 000 km) or 3,000 hours of operation, whichever occurs first, after date of delivery to the initial owner.If an emission related part fails during the warranty period, it will be repaired or replaced. Any such part repaired or replaced under warranty is warranted for the remainder of the warranty period.During the term of this warranty, Caterpillar Inc. will provide through a Caterpillar dealer or other establishment
Have questions with 106873-7010?
Group cross 106873-7010 ZEXEL
Mitsubishi
106873-7010
9 400 618 460
ME093327
INJECTION-PUMP ASSEMBLY
8DC9
8DC9