Information injection-pump assembly
ZEXEL
106873-3410
1068733410
HINO
220801670A
220801670a
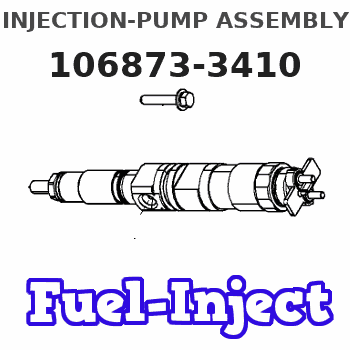
Rating:
Cross reference number
ZEXEL
106873-3410
1068733410
HINO
220801670A
220801670a
Zexel num
Bosch num
Firm num
Name
Calibration Data:
Adjustment conditions
Test oil
1404 Test oil ISO4113 or {SAEJ967d}
1404 Test oil ISO4113 or {SAEJ967d}
Test oil temperature
degC
40
40
45
Nozzle and nozzle holder
105780-8140
Bosch type code
EF8511/9A
Nozzle
105780-0000
Bosch type code
DN12SD12T
Nozzle holder
105780-2080
Bosch type code
EF8511/9
Opening pressure
MPa
17.2
Opening pressure
kgf/cm2
175
Injection pipe
Outer diameter - inner diameter - length (mm) mm 8-3-600
Outer diameter - inner diameter - length (mm) mm 8-3-600
Overflow valve
131425-0020
Overflow valve opening pressure
kPa
127
107
147
Overflow valve opening pressure
kgf/cm2
1.3
1.1
1.5
Tester oil delivery pressure
kPa
157
157
157
Tester oil delivery pressure
kgf/cm2
1.6
1.6
1.6
Direction of rotation (viewed from drive side)
Right R
Right R
Injection timing adjustment
Direction of rotation (viewed from drive side)
Right R
Right R
Injection order
1-8-6-2-
7-5-4-3
Pre-stroke
mm
4.2
4.14
4.2
Beginning of injection position
Drive side NO.1
Drive side NO.1
Difference between angles 1
Cal 1-8 deg. 45 44.75 45.25
Cal 1-8 deg. 45 44.75 45.25
Difference between angles 2
Cal 1-6 deg. 90 89.75 90.25
Cal 1-6 deg. 90 89.75 90.25
Difference between angles 3
Cyl.1-2 deg. 135 134.75 135.25
Cyl.1-2 deg. 135 134.75 135.25
Difference between angles 4
Cal 1-7 deg. 180 179.75 180.25
Cal 1-7 deg. 180 179.75 180.25
Difference between angles 5
Cal 1-5 deg. 225 224.75 225.25
Cal 1-5 deg. 225 224.75 225.25
Difference between angles 6
Cal 1-4 deg. 270 269.75 270.25
Cal 1-4 deg. 270 269.75 270.25
Difference between angles 7
Cal 1-3 deg. 315 314.75 315.25
Cal 1-3 deg. 315 314.75 315.25
Injection quantity adjustment
Adjusting point
A
Rack position
8.4
Pump speed
r/min
700
700
700
Average injection quantity
mm3/st.
149
147
151
Max. variation between cylinders
%
0
-2
2
Basic
*
Fixing the lever
*
Injection quantity adjustment_02
Adjusting point
B
Rack position
8.25
Pump speed
r/min
500
500
500
Average injection quantity
mm3/st.
147.5
144.5
150.5
Fixing the lever
*
Injection quantity adjustment_03
Adjusting point
D
Rack position
8.4+-0.5
Pump speed
r/min
1100
1100
1100
Average injection quantity
mm3/st.
140
132
148
Fixing the lever
*
Injection quantity adjustment_04
Adjusting point
E
Rack position
7.6
Pump speed
r/min
1200
1200
1200
Average injection quantity
mm3/st.
117.5
112.5
122.5
Fixing the lever
*
Injection quantity adjustment_05
Adjusting point
F
Rack position
3.4+-0.5
Pump speed
r/min
225
225
225
Average injection quantity
mm3/st.
12
9
15
Max. variation between cylinders
%
0
-15
15
Fixing the rack
*
Injection quantity adjustment_06
Adjusting point
G
Rack position
8.7+-0.1
Pump speed
r/min
330
330
330
Average injection quantity
mm3/st.
156.5
150.5
162.5
Fixing the lever
*
Remarks
Startup boost setting
Startup boost setting
Injection quantity adjustment_07
Adjusting point
H
Rack position
-
Pump speed
r/min
100
100
100
Average injection quantity
mm3/st.
165
165
185
Fixing the lever
*
Remarks
After startup boost setting
After startup boost setting
Timer adjustment
Pump speed
r/min
710--
Advance angle
deg.
0
0
0
Load
2/5
Remarks
Start
Start
Timer adjustment_02
Pump speed
r/min
660
Advance angle
deg.
0.3
Load
2/5
Timer adjustment_03
Pump speed
r/min
(760)
Advance angle
deg.
2
1.7
2.3
Load
5/5
Remarks
Measure the actual speed.
Measure the actual speed.
Timer adjustment_04
Pump speed
r/min
900+50
Advance angle
deg.
2
1.7
2.3
Load
4/5
Timer adjustment_05
Pump speed
r/min
1100-50
Advance angle
deg.
6.75
6.45
7.05
Load
5/5
Remarks
Finish
Finish
Test data Ex:
Governor adjustment
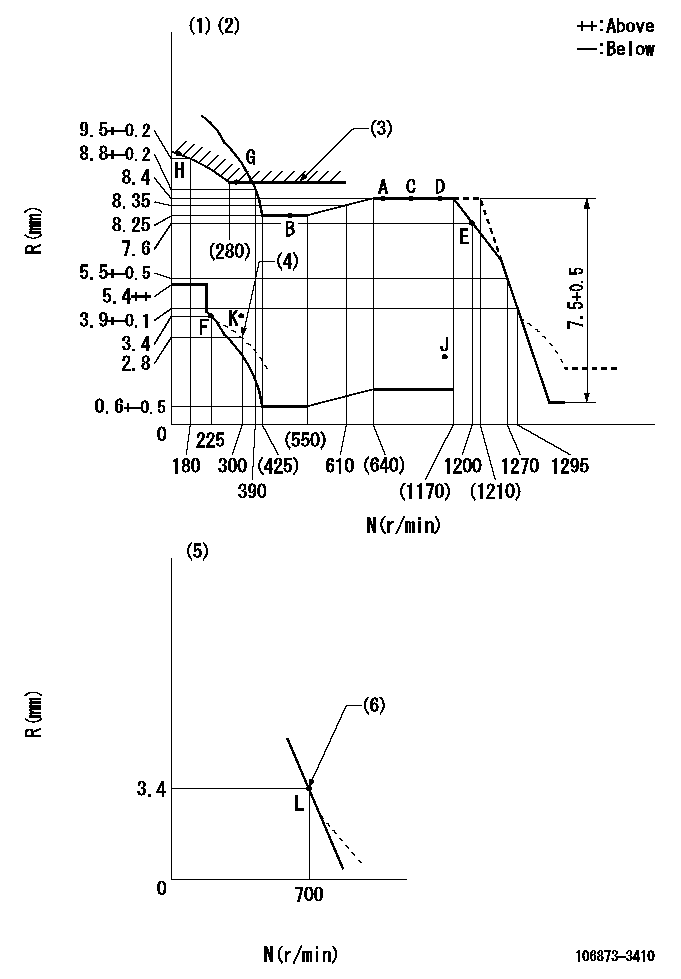
N:Pump speed
R:Rack position (mm)
(1)Tolerance for racks not indicated: +-0.05mm.
(2)Set idle at point K (N = N1, R = R1) and confirm that the injection quantity does not exceed Q1 at point J (N = N2).
(3)Excess fuel setting for starting: SXL
(4)Damper spring setting
(5)Variable speed specification: idling adjustment
(6)Main spring setting
----------
N1=300r/min R1=3.4mm N2=1100r/min Q1=3mm3/st SXL=8.7+-0.1mm
----------
----------
N1=300r/min R1=3.4mm N2=1100r/min Q1=3mm3/st SXL=8.7+-0.1mm
----------
Speed control lever angle
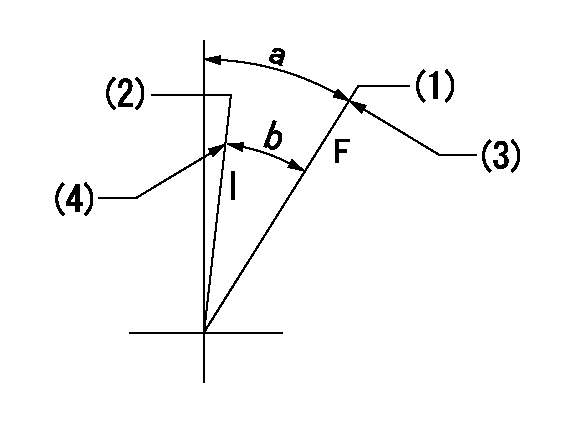
F:Full speed
I:Idle
(1)Set the pump speed at aa
(2)Set the pump speed at bb.
(3)Stopper bolt setting
(4)Stopper bolt setting
----------
aa=1295r/min bb=700r/min
----------
a=17.5deg+-5deg b=(12deg)+-5deg
----------
aa=1295r/min bb=700r/min
----------
a=17.5deg+-5deg b=(12deg)+-5deg
0000000901

F:Full load
I:Idle
(1)Use the hole at R = aa
(2)Stopper bolt setting
----------
aa=39mm
----------
a=39deg+-5deg b=41deg+-3deg
----------
aa=39mm
----------
a=39deg+-5deg b=41deg+-3deg
Stop lever angle
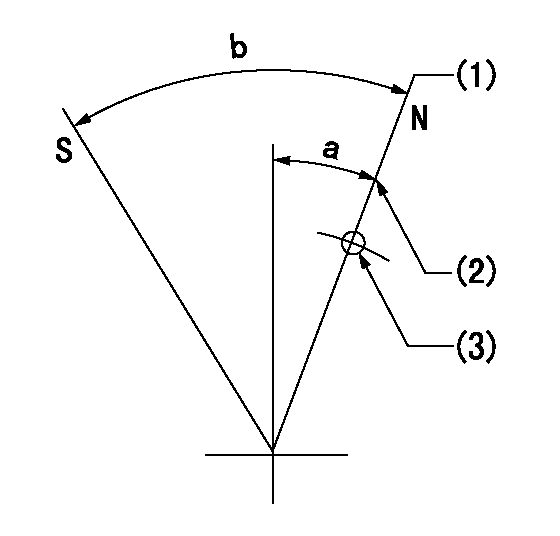
N:Pump normal
S:Stop the pump.
(1)Rack position = aa (set before setting excess fuel for starting)
(2)Set the stopper bolt (apply red paint).
(3)Use the hole at R = bb
----------
aa=12+0.5mm bb=37mm
----------
a=17.5deg+-5deg b=35deg+-5deg
----------
aa=12+0.5mm bb=37mm
----------
a=17.5deg+-5deg b=35deg+-5deg
0000001501 LEVER

2-stage changeover lever adjustment
(A) Speed lever
(B) Load lever
(C) 2-stage changeover lever
(D) Link
(E) Bolt
(G) Variable speed specifications
(H) Minimum maximum speed specifications
F:Full speed
I:Idle
1. Minimum-maximum speed specification adjustment (when running)
(1)After completing governor adjustment, hold the 2-stage changeover lever (C) so that the speed lever (A) contacts the full speed stopper.
(2)In this condition, the load lever is held in the idle position.
(3)Adjust bolt (E) so that the clearance between the pin underneath lever (C) and the end of the long groove in link (D) is L.
(4)Lock using the nut.
2. Variable speed specification adjustment (at operation)
(1)Hold the 2-stage changeover lever (C) so that the load lever (B) contacts the full load stopper. (When the load lever is equipped with a cancel mechanism, move it so that it contacts the stopper without canceling.)
(2)In this condition, confirm that the speed lever (A) moves from idle to full speed.
----------
L=1~2mm
----------
----------
L=1~2mm
----------
Timing setting
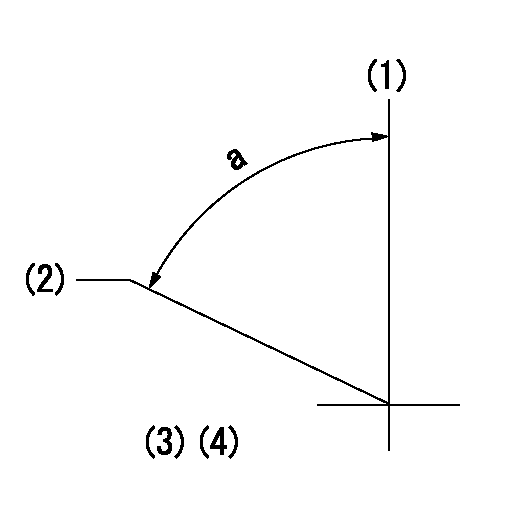
(1)Pump vertical direction
(2)Coupling's key groove position at No 1 cylinder's beginning of injection
(3)-
(4)-
----------
----------
a=(80deg)
----------
----------
a=(80deg)
Information:
Electric Starting
Startability will be improved at temperatures below 16°C (60°F) by the use of a starting aid. A jacket water (coolant) heater or other means can be used to heat the crankcase oil.Start the engine using the following procedure:1. Perform all before-starting inspections.2. If the engine is equipped with a manual control, ensure that is in the RUN position. Place the transmission in NEUTRAL (and disengage the flywheel clutch, if equipped). For Generator Sets, open the main electrical circuit breaker.2. Move throttle to approximately half engine speed to get the fuel rack to move to the FUEL ON position.3. Turn the starter switch to START (or battery disconnect switch to the ON position) or the Engine Control Switch (ECS) to MAN. START. The starting motor will crank and attempt to start the engine. At temperatures below 0°C (32°F), it may be necessary to spray starting fluid into the air cleaner inlet. Additional injections of ether may be required to start and/or achieve low idle speed.
Excessive ether can cause piston and ring damage. When using starting fluid, follow the manufacturer's instructions carefully, use it sparingly and spray it ONLY WHILE CRANKING THE ENGINE. Failure to do so could result in an explosion and/or fire and possible personal injury.Use ether for cold starting purposes only.
Do not crank the engine for more than 30 seconds.
If a warm engine fails to start within 30 seconds: release the starter switch and wait two minutes to allow the starter motor to cool before using it again.4. As soon as the engine starts, allow the engine to idle for 3 to 5 minutes, or until the water temperature gauge indicator has begun to rise. The engine should run at low idle smoothly until speed is gradually increased to high idle.
Do not increase engine speed until the oil pressure gauge indicates normal. Oil pressure should rise within 15 seconds after the engine starts. If oil pressure is not indicated on gauge within 15 seconds, stop the engine, investigate and correct the cause.
5. Allow white smoke to clear up and proceed with normal operation. Do not apply load to the engine or increase engine speed until the oil pressure gauge indicates normal. Oil pressure should raise within 15 seconds after the engine starts. For starting in cold weather, to minimize white smoke: start the engine and allow the engine to idle for 30 seconds. Increase rpm until engine speed reaches 1200 rpm. Then allow the engine to return to low idle.6. Operate the engine at low load until all systems reach operating temperature. Check all gauges during the warm-up period.Engine Starting With Jumper Cables
When boost starting an engine, follow the instructions to properly start the engine. This engine is equipped with a 12 or 24 volt starting system. Use only equal voltage for boost starting. The use of higher voltage will damage the electrical system.
Batteries give off flammable fumes that can explode.Improper jumper cable connections can cause an explosion resulting in personal injury.Prevent sparks near the batteries.
Startability will be improved at temperatures below 16°C (60°F) by the use of a starting aid. A jacket water (coolant) heater or other means can be used to heat the crankcase oil.Start the engine using the following procedure:1. Perform all before-starting inspections.2. If the engine is equipped with a manual control, ensure that is in the RUN position. Place the transmission in NEUTRAL (and disengage the flywheel clutch, if equipped). For Generator Sets, open the main electrical circuit breaker.2. Move throttle to approximately half engine speed to get the fuel rack to move to the FUEL ON position.3. Turn the starter switch to START (or battery disconnect switch to the ON position) or the Engine Control Switch (ECS) to MAN. START. The starting motor will crank and attempt to start the engine. At temperatures below 0°C (32°F), it may be necessary to spray starting fluid into the air cleaner inlet. Additional injections of ether may be required to start and/or achieve low idle speed.
Excessive ether can cause piston and ring damage. When using starting fluid, follow the manufacturer's instructions carefully, use it sparingly and spray it ONLY WHILE CRANKING THE ENGINE. Failure to do so could result in an explosion and/or fire and possible personal injury.Use ether for cold starting purposes only.
Do not crank the engine for more than 30 seconds.
If a warm engine fails to start within 30 seconds: release the starter switch and wait two minutes to allow the starter motor to cool before using it again.4. As soon as the engine starts, allow the engine to idle for 3 to 5 minutes, or until the water temperature gauge indicator has begun to rise. The engine should run at low idle smoothly until speed is gradually increased to high idle.
Do not increase engine speed until the oil pressure gauge indicates normal. Oil pressure should rise within 15 seconds after the engine starts. If oil pressure is not indicated on gauge within 15 seconds, stop the engine, investigate and correct the cause.
5. Allow white smoke to clear up and proceed with normal operation. Do not apply load to the engine or increase engine speed until the oil pressure gauge indicates normal. Oil pressure should raise within 15 seconds after the engine starts. For starting in cold weather, to minimize white smoke: start the engine and allow the engine to idle for 30 seconds. Increase rpm until engine speed reaches 1200 rpm. Then allow the engine to return to low idle.6. Operate the engine at low load until all systems reach operating temperature. Check all gauges during the warm-up period.Engine Starting With Jumper Cables
When boost starting an engine, follow the instructions to properly start the engine. This engine is equipped with a 12 or 24 volt starting system. Use only equal voltage for boost starting. The use of higher voltage will damage the electrical system.
Batteries give off flammable fumes that can explode.Improper jumper cable connections can cause an explosion resulting in personal injury.Prevent sparks near the batteries.