Information injection-pump assembly
ZEXEL
106873-3342
1068733342
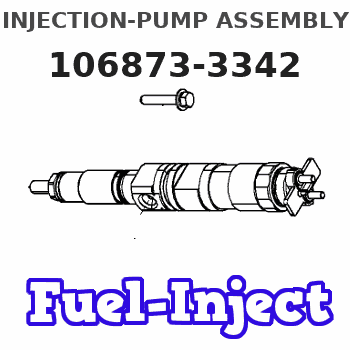
Rating:
Service parts 106873-3342 INJECTION-PUMP ASSEMBLY:
1.
_
7.
COUPLING PLATE
8.
_
9.
_
11.
Nozzle and Holder
23600-2750A
12.
Open Pre:MPa(Kqf/cm2)
14.7{150}/21.6{220}
14.
NOZZLE
Include in #1:
106873-3342
as INJECTION-PUMP ASSEMBLY
Cross reference number
ZEXEL
106873-3342
1068733342
Zexel num
Bosch num
Firm num
Name
106873-3342
INJECTION-PUMP ASSEMBLY
14CD PE8P PE
14CD PE8P PE
Calibration Data:
Adjustment conditions
Test oil
1404 Test oil ISO4113 or {SAEJ967d}
1404 Test oil ISO4113 or {SAEJ967d}
Test oil temperature
degC
40
40
45
Nozzle and nozzle holder
105780-8250
Bosch type code
1 688 901 101
Nozzle
105780-0120
Bosch type code
1 688 901 990
Nozzle holder
105780-2190
Opening pressure
MPa
20.7
Opening pressure
kgf/cm2
211
Injection pipe
Outer diameter - inner diameter - length (mm) mm 8-3-600
Outer diameter - inner diameter - length (mm) mm 8-3-600
Overflow valve
134424-4120
Overflow valve opening pressure
kPa
255
221
289
Overflow valve opening pressure
kgf/cm2
2.6
2.25
2.95
Tester oil delivery pressure
kPa
255
255
255
Tester oil delivery pressure
kgf/cm2
2.6
2.6
2.6
Direction of rotation (viewed from drive side)
Right R
Right R
Injection timing adjustment
Direction of rotation (viewed from drive side)
Right R
Right R
Injection order
1-8-6-2-
7-5-4-3
Pre-stroke
mm
4
3.94
4
Beginning of injection position
Drive side NO.1
Drive side NO.1
Difference between angles 1
Cal 1-8 deg. 45 44.75 45.25
Cal 1-8 deg. 45 44.75 45.25
Difference between angles 2
Cal 1-6 deg. 90 89.75 90.25
Cal 1-6 deg. 90 89.75 90.25
Difference between angles 3
Cyl.1-2 deg. 135 134.75 135.25
Cyl.1-2 deg. 135 134.75 135.25
Difference between angles 4
Cal 1-7 deg. 180 179.75 180.25
Cal 1-7 deg. 180 179.75 180.25
Difference between angles 5
Cal 1-5 deg. 225 224.75 225.25
Cal 1-5 deg. 225 224.75 225.25
Difference between angles 6
Cal 1-4 deg. 270 269.75 270.25
Cal 1-4 deg. 270 269.75 270.25
Difference between angles 7
Cal 1-3 deg. 315 314.75 315.25
Cal 1-3 deg. 315 314.75 315.25
Injection quantity adjustment
Adjusting point
-
Rack position
12.8
Pump speed
r/min
700
700
700
Average injection quantity
mm3/st.
140
137
143
Max. variation between cylinders
%
0
-2
2
Basic
*
Fixing the rack
*
Standard for adjustment of the maximum variation between cylinders
*
Injection quantity adjustment_02
Adjusting point
Z
Rack position
8+-0.5
Pump speed
r/min
420
420
420
Average injection quantity
mm3/st.
15.9
12.9
18.9
Max. variation between cylinders
%
0
-15
15
Fixing the rack
*
Standard for adjustment of the maximum variation between cylinders
*
Injection quantity adjustment_03
Adjusting point
A
Rack position
R1(12.8)
Pump speed
r/min
700
700
700
Average injection quantity
mm3/st.
140
138
142
Basic
*
Fixing the lever
*
Injection quantity adjustment_04
Adjusting point
B
Rack position
R1+0.3
Pump speed
r/min
1100
1100
1100
Average injection quantity
mm3/st.
126
120
132
Fixing the lever
*
Injection quantity adjustment_05
Adjusting point
C
Rack position
R1-1.1
Pump speed
r/min
300
300
300
Average injection quantity
mm3/st.
138
132
144
Fixing the lever
*
Timer adjustment
Pump speed
r/min
710--
Advance angle
deg.
0
0
0
Load
2/5
Remarks
Start
Start
Timer adjustment_02
Pump speed
r/min
660
Advance angle
deg.
0.3
Load
2/5
Timer adjustment_03
Pump speed
r/min
(760)
Advance angle
deg.
2
1.7
2.3
Load
5/5
Remarks
Measure the actual speed.
Measure the actual speed.
Timer adjustment_04
Pump speed
r/min
900+50
Advance angle
deg.
2
1.7
2.3
Load
4/5
Timer adjustment_05
Pump speed
r/min
1100-50
Advance angle
deg.
5.75
5.45
6.05
Load
5/5
Remarks
Finish
Finish
Test data Ex:
Governor adjustment
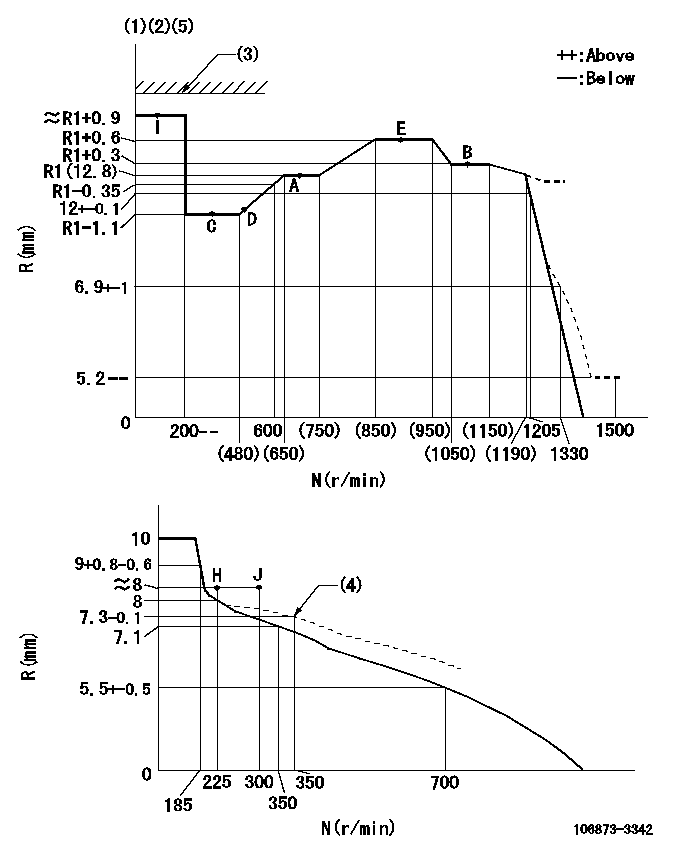
N:Pump speed
R:Rack position (mm)
(1)Torque cam stamping: T1
(2)Tolerance for racks not indicated: +-0.05mm.
(3)Stop lever's normal position setting: equivalent to R1
(4)Damper spring setting
(5)Set stop lever before governor adjustment. [When setting stop lever after governor adjustment, confirm that point I (Ra) can be obtained at full setting.]
----------
T1=AC10 R1=17.5mm Ra=(12.8)+0.9mm
----------
----------
T1=AC10 R1=17.5mm Ra=(12.8)+0.9mm
----------
Speed control lever angle
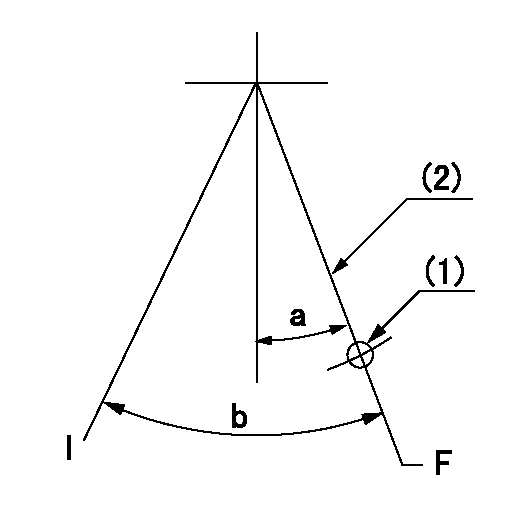
F:Full speed
I:Idle
(1)Use the hole at R = aa
(2)Stopper bolt set position 'H'
----------
aa=94mm
----------
a=17deg+-5deg b=39deg+-3deg
----------
aa=94mm
----------
a=17deg+-5deg b=39deg+-3deg
Stop lever angle
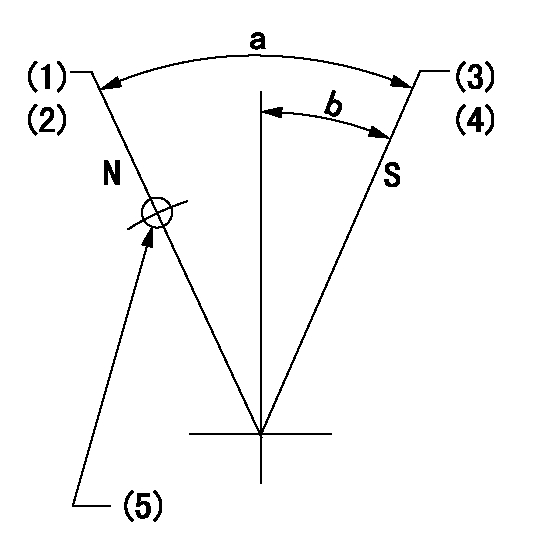
N:Pump normal
S:Stop the pump.
(1)Rack position = aa
(2)Set the stopper screw. (After setting, apply red paint.)
(3)Rack position = bb (speed = cc)
(4)Set the stopper screw. (After setting, apply red paint.)
(5)Use the hole above R = dd
----------
aa=(17.5)mm bb=1.5+-0.3mm cc=0r/min dd=35mm
----------
a=35deg+-5deg b=15deg+-5deg
----------
aa=(17.5)mm bb=1.5+-0.3mm cc=0r/min dd=35mm
----------
a=35deg+-5deg b=15deg+-5deg
Timing setting
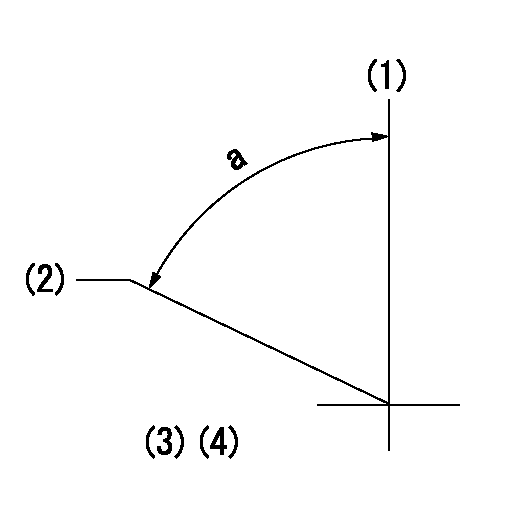
(1)Pump vertical direction
(2)Coupling's key groove position at No 1 cylinder's beginning of injection
(3)-
(4)-
----------
----------
a=(80deg)
----------
----------
a=(80deg)
Information:
The vehicle must be parked on a level surface to perform this maintenance procedure.
1. Check the oil leve with the engine stopped. 2. Maintain the oil leve between the ADD and FULL marks in the FULL RANGE zone on the ENGINE STOPPED side of the dipstick. Do not fill the crankcase above the FULL RANGE zone. Operating your engine when the oil level is above the FULL RANGE zone could cause your crankshaft to dip into the oil. If this happens, the air bubbles created from the crankshaft dipping into the oil will reduce the lubricating characteristics of your oil and would result in the loss of power.If the dipstick does not have a FULL mark in the FULL RANGE zone, refer to calibrating the oil level gauge in the Dipsticks section of this manual or consult your Caterpillar dealer before operating the engine. 3. Add oil if necessary. See Refill Capacities and Lubricant Specifications for the size of your engine crankcase and proper oil to use. Remote mounted or auxiliary filters require additional oil. For all information pertaining to auxiliary filters, refer to the OEM or manufacturer's instructions.Leaks and Loose Connections
Inspect the Engine
For maximum service life of your truck engine, make a thorough under the hood inspection before starting the engine. Look for such items as oil or coolant leaks, loose bolts, worn fan belts, loose connections and trash build-up. Remove trash build-up and have repairs made as needed.Keep a close watch for leaks. If leaking is observed, find the source and correct the leak. If leaking is suspected, check the fluid levels more frequently than the recommended intervals prescribed in this publication. Continue monitoring fluid levels until a leak is found and fixed, or until the suspicion for a leak has been proven to be unwarranted.* Wipe all fittings, caps and plugs before servicing. * Inspect the radiator for leaks and trash build-up. * Inspect the radiator hoses for cracks and loose clamps. * Inspect the fan and accessory drive belts for cracks, breaks or other damage.Belts for multiple groove pulleys must be replaced as matched sets. If only one belt of a 2 or 3 belt set is replaced, it will carry more of a load than the belts not replaced since the older belts are stretched. The additional load on the new belt could cause it to break. * Inspect the water pump for leaks. Check weep hole for water pump breather filter, 4N1400 (1), blockage and replace if necessary. * Inspect the engine for oil leaks, such as front and rear crankshaft seals, oil pan, oil filters and valve covers. * Inspect the fuel system for leaks, loose fuel line clamps and fittings and loose or worn hoses. * Inspect wiring for loose connections and worn or frayed wires. * Inspect air intake system hoses and elbows for cracks and loose clamps. * Inspect engine-to-frame ground strap for good connection and condition.* All guards must be in place. Repair or replace missing or
Have questions with 106873-3342?
Group cross 106873-3342 ZEXEL
Hino
Hino
Hino
106873-3342
INJECTION-PUMP ASSEMBLY