Information injection-pump assembly
BOSCH
9 400 611 023
9400611023
ZEXEL
106873-3333
1068733333
HINO
220008612A
220008612a
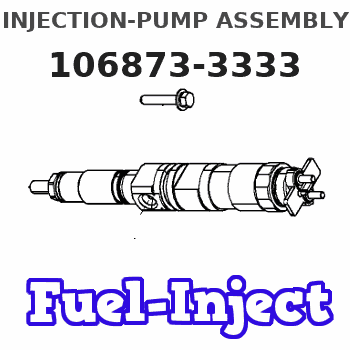
Rating:
Service parts 106873-3333 INJECTION-PUMP ASSEMBLY:
1.
_
7.
COUPLING PLATE
8.
_
9.
_
11.
Nozzle and Holder
23600-2741B
12.
Open Pre:MPa(Kqf/cm2)
14.7{150}/24.5{250}
14.
NOZZLE
Include in #1:
106873-3333
as INJECTION-PUMP ASSEMBLY
Cross reference number
BOSCH
9 400 611 023
9400611023
ZEXEL
106873-3333
1068733333
HINO
220008612A
220008612a
Zexel num
Bosch num
Firm num
Name
9 400 611 023
220008612A HINO
INJECTION-PUMP ASSEMBLY
F-2 K 14CD INJECTION PUMP ASSY PE8P PE
F-2 K 14CD INJECTION PUMP ASSY PE8P PE
Calibration Data:
Adjustment conditions
Test oil
1404 Test oil ISO4113 or {SAEJ967d}
1404 Test oil ISO4113 or {SAEJ967d}
Test oil temperature
degC
40
40
45
Nozzle and nozzle holder
105780-8140
Bosch type code
EF8511/9A
Nozzle
105780-0000
Bosch type code
DN12SD12T
Nozzle holder
105780-2080
Bosch type code
EF8511/9
Opening pressure
MPa
17.2
Opening pressure
kgf/cm2
175
Injection pipe
Outer diameter - inner diameter - length (mm) mm 8-3-600
Outer diameter - inner diameter - length (mm) mm 8-3-600
Overflow valve
131425-0020
Overflow valve opening pressure
kPa
127
107
147
Overflow valve opening pressure
kgf/cm2
1.3
1.1
1.5
Tester oil delivery pressure
kPa
157
157
157
Tester oil delivery pressure
kgf/cm2
1.6
1.6
1.6
Direction of rotation (viewed from drive side)
Right R
Right R
Injection timing adjustment
Direction of rotation (viewed from drive side)
Right R
Right R
Injection order
1-8-6-2-
7-5-4-3
Pre-stroke
mm
4.2
4.14
4.2
Beginning of injection position
Drive side NO.1
Drive side NO.1
Difference between angles 1
Cal 1-8 deg. 45 44.75 45.25
Cal 1-8 deg. 45 44.75 45.25
Difference between angles 2
Cal 1-6 deg. 90 89.75 90.25
Cal 1-6 deg. 90 89.75 90.25
Difference between angles 3
Cyl.1-2 deg. 135 134.75 135.25
Cyl.1-2 deg. 135 134.75 135.25
Difference between angles 4
Cal 1-7 deg. 180 179.75 180.25
Cal 1-7 deg. 180 179.75 180.25
Difference between angles 5
Cal 1-5 deg. 225 224.75 225.25
Cal 1-5 deg. 225 224.75 225.25
Difference between angles 6
Cal 1-4 deg. 270 269.75 270.25
Cal 1-4 deg. 270 269.75 270.25
Difference between angles 7
Cal 1-3 deg. 315 314.75 315.25
Cal 1-3 deg. 315 314.75 315.25
Injection quantity adjustment
Adjusting point
A
Rack position
8
Pump speed
r/min
700
700
700
Average injection quantity
mm3/st.
143.5
141.5
145.5
Max. variation between cylinders
%
0
-2
2
Basic
*
Fixing the lever
*
Injection quantity adjustment_02
Adjusting point
B
Rack position
7.9
Pump speed
r/min
500
500
500
Average injection quantity
mm3/st.
140
137
143
Fixing the lever
*
Injection quantity adjustment_03
Adjusting point
D
Rack position
8.05
Pump speed
r/min
1100
1100
1100
Average injection quantity
mm3/st.
136.5
132.5
140.5
Fixing the lever
*
Injection quantity adjustment_04
Adjusting point
E
Rack position
7.6
Pump speed
r/min
1200
1200
1200
Average injection quantity
mm3/st.
122.5
117.5
127.5
Fixing the lever
*
Injection quantity adjustment_05
Adjusting point
F
Rack position
3.4+-0.5
Pump speed
r/min
225
225
225
Average injection quantity
mm3/st.
12
9
15
Max. variation between cylinders
%
0
-15
15
Fixing the rack
*
Injection quantity adjustment_06
Adjusting point
G
Rack position
8.35+-0.
1
Pump speed
r/min
330
330
330
Average injection quantity
mm3/st.
149.5
143.5
155.5
Fixing the lever
*
Remarks
Startup boost setting
Startup boost setting
Injection quantity adjustment_07
Adjusting point
H
Rack position
-
Pump speed
r/min
100
100
100
Average injection quantity
mm3/st.
170
170
190
Fixing the lever
*
Remarks
After startup boost setting
After startup boost setting
Timer adjustment
Pump speed
r/min
570--
Advance angle
deg.
0
0
0
Remarks
Start
Start
Timer adjustment_02
Pump speed
r/min
520
Advance angle
deg.
0.3
Timer adjustment_03
Pump speed
r/min
(550)
Advance angle
deg.
2
1.7
2.3
Remarks
Measure the actual speed.
Measure the actual speed.
Timer adjustment_04
Pump speed
r/min
900+50
Advance angle
deg.
2
1.7
2.3
Timer adjustment_05
Pump speed
r/min
1100-50
Advance angle
deg.
6.75
6.45
7.05
Remarks
Finish
Finish
Test data Ex:
Governor adjustment
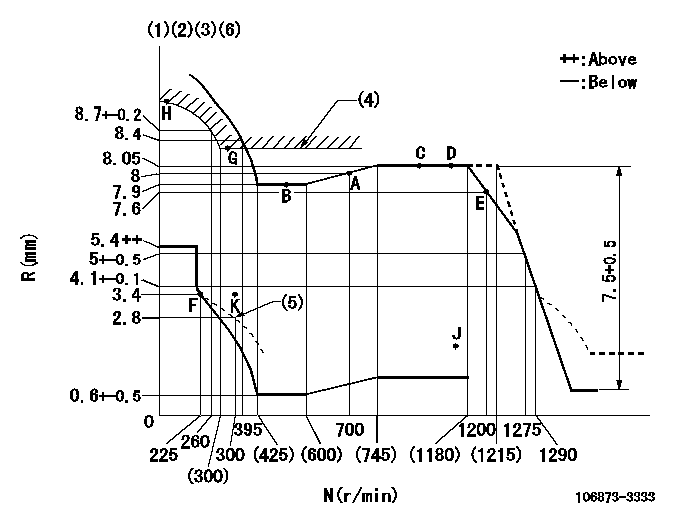
N:Pump speed
R:Rack position (mm)
(1)Lever ratio: RT
(2)Target shim dimension: TH
(3)Tolerance for racks not indicated: +-0.05mm.
(4)Excess fuel setting for starting: SXL
(5)Damper spring setting
(6)Set idle at point K (N = N1, R = R1) and confirm that the injection quantity does not exceed Q1 at point J (N = N2).
----------
RT=0.8 TH=2.8mm SXL=8.35+-0.1mm N1=300r/min R1=3.4mm N2=1100r/min Q1=3mm3/st
----------
----------
RT=0.8 TH=2.8mm SXL=8.35+-0.1mm N1=300r/min R1=3.4mm N2=1100r/min Q1=3mm3/st
----------
Speed control lever angle

F:Full speed
----------
----------
a=14.5deg+-5deg
----------
----------
a=14.5deg+-5deg
0000000901

F:Full load
I:Idle
(1)Use the hole at R = aa
(2)Stopper bolt setting
----------
aa=39mm
----------
a=39deg+-5deg b=39.5deg+-3deg
----------
aa=39mm
----------
a=39deg+-5deg b=39.5deg+-3deg
Stop lever angle
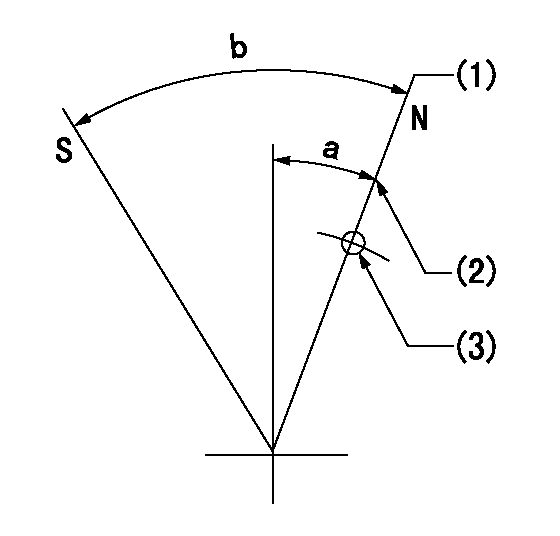
N:Pump normal
S:Stop the pump.
(1)Rack position = aa (set before setting excess fuel for starting)
(2)Set the stopper bolt (apply red paint).
(3)Use the hole at R = bb
----------
aa=12+0.5mm bb=37mm
----------
a=17.5deg+-5deg b=35deg+-5deg
----------
aa=12+0.5mm bb=37mm
----------
a=17.5deg+-5deg b=35deg+-5deg
Timing setting
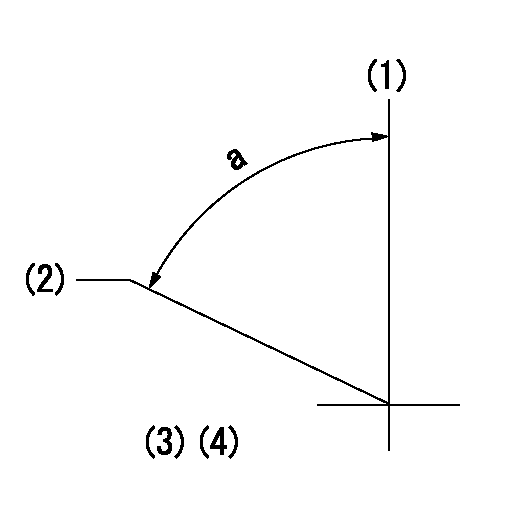
(1)Pump vertical direction
(2)Coupling's key groove position at No 1 cylinder's beginning of injection
(3)-
(4)-
----------
----------
a=(80deg)
----------
----------
a=(80deg)
Information:
Table 1
Revision Summary of Changes
01 Title updated. Effectivity and reference added. Changes were made in problem and solution section. Introduction
The problem that is identified below does not have a known permanent solution. Until a permanent solution is known, use the solution that is identified below.Problem
Illustration 1 g06583948
Clogged diesel particulate filter
Reports have been received that the Diesel Particulate Filter (DPF) may clog at less than 300 hours on the machines listed above. The insulation from the Diesel Oxidation Catalyst (DOC) causes clogging of the DPF.These additional related problems may occur:
Diagnostic code 523602-0"Aftertreatment Regeneration Frequency" may occur
Erratic soot levels
Fuel dilution of the oil or poor oil quality at low machine hoursSolution
Do not operate or work on this product unless you have read and understood the instruction and warnings in the relevant Operation and Maintenance Manuals and relevant service literature. Failure to follow the instructions or heed the warnings could result in injury or death. Proper care is your responsibility.
In the event of failure, follow the troubleshooting procedure below:Troubleshooting Procedure
Check the fuel/water separator for water.Note: Water in fuel can cause excessive ash buildup in the DPF.
Check the air filter and replace the air filter if necessary.
Check the engine oil level and look for fuel dilution of engine oil. Replace the engine oil and filter if fuel dilution has occurred.Note: Frequent regeneration may cause fuel dilution of engine oil due to the fuel dosing required for regeneration. A failed injector could also cause fuel dilution of engine oil.
Check the coolant level.
Troubleshoot active diagnostic codes. Refer to Troubleshooting, UENR3390 on how to troubleshoot excessive DPF regeneration.
Complete a parked DPF regeneration to remove soot.
Inspect the differential pressure sensor tubes for damage.
Inspect the differential pressure sensor tubes and sensors for debris.
Bring the engine up to operating temperature and complete a fuel injector cut-out test to test for failed injectors.If the problem exists even after performing the troubleshooting procedure, create a Global Dealer Solution Network (GDSN) Product Health Service Request (SR) with Workgroup / Subsystem of “Base Machine”. Attach any pertinent photos and detailed failure information for the product group. Mention the CPI number 471218 in the CPI field (and /or) the Technical Information Bulletin (TIB) media number (M0121625) in the description prior to submitting to Caterpillar.Additional troubleshooting/documentation may include:
A photo of the DPF and DOC for identification information
An inspection of the face of the DPF for fibrous material
An inspection of engine oil sample
An inspection of the fuel sample if needed based on diagnostic codes