Information injection-pump assembly
ZEXEL
106873-3143
1068733143
HINO
220007992A
220007992a
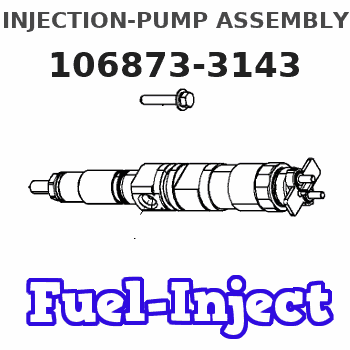
Rating:
Cross reference number
ZEXEL
106873-3143
1068733143
HINO
220007992A
220007992a
Zexel num
Bosch num
Firm num
Name
Calibration Data:
Adjustment conditions
Test oil
1404 Test oil ISO4113 or {SAEJ967d}
1404 Test oil ISO4113 or {SAEJ967d}
Test oil temperature
degC
40
40
45
Nozzle and nozzle holder
105780-8140
Bosch type code
EF8511/9A
Nozzle
105780-0000
Bosch type code
DN12SD12T
Nozzle holder
105780-2080
Bosch type code
EF8511/9
Opening pressure
MPa
17.2
Opening pressure
kgf/cm2
175
Injection pipe
Outer diameter - inner diameter - length (mm) mm 8-3-600
Outer diameter - inner diameter - length (mm) mm 8-3-600
Overflow valve
134424-0820
Overflow valve opening pressure
kPa
127
107
147
Overflow valve opening pressure
kgf/cm2
1.3
1.1
1.5
Tester oil delivery pressure
kPa
157
157
157
Tester oil delivery pressure
kgf/cm2
1.6
1.6
1.6
Direction of rotation (viewed from drive side)
Right R
Right R
Injection timing adjustment
Direction of rotation (viewed from drive side)
Right R
Right R
Injection order
1-8-6-2-
7-5-4-3
Pre-stroke
mm
4.8
4.74
4.8
Beginning of injection position
Drive side NO.1
Drive side NO.1
Difference between angles 1
Cal 1-8 deg. 45 44.75 45.25
Cal 1-8 deg. 45 44.75 45.25
Difference between angles 2
Cal 1-6 deg. 90 89.75 90.25
Cal 1-6 deg. 90 89.75 90.25
Difference between angles 3
Cyl.1-2 deg. 135 134.75 135.25
Cyl.1-2 deg. 135 134.75 135.25
Difference between angles 4
Cal 1-7 deg. 180 179.75 180.25
Cal 1-7 deg. 180 179.75 180.25
Difference between angles 5
Cal 1-5 deg. 225 224.75 225.25
Cal 1-5 deg. 225 224.75 225.25
Difference between angles 6
Cal 1-4 deg. 270 269.75 270.25
Cal 1-4 deg. 270 269.75 270.25
Difference between angles 7
Cal 1-3 deg. 315 314.75 315.25
Cal 1-3 deg. 315 314.75 315.25
Injection quantity adjustment
Adjusting point
A
Rack position
8.9
Pump speed
r/min
700
700
700
Average injection quantity
mm3/st.
139.3
137.3
141.3
Max. variation between cylinders
%
0
-2
2
Basic
*
Fixing the lever
*
Injection quantity adjustment_02
Adjusting point
B
Rack position
8.95+-0.
5
Pump speed
r/min
1100
1100
1100
Average injection quantity
mm3/st.
133.1
129.1
137.1
Fixing the lever
*
Injection quantity adjustment_03
Adjusting point
F
Rack position
3.8+-0.5
Pump speed
r/min
225
225
225
Average injection quantity
mm3/st.
10.4
7.4
13.4
Max. variation between cylinders
%
0
-15
15
Fixing the rack
*
Injection quantity adjustment_04
Adjusting point
G
Rack position
-
Pump speed
r/min
100
100
100
Average injection quantity
mm3/st.
139
139
Fixing the lever
*
Remarks
After startup boost setting
After startup boost setting
Timer adjustment
Pump speed
r/min
750--
Advance angle
deg.
0
0
0
Load
1/4
Remarks
Start
Start
Timer adjustment_02
Pump speed
r/min
700
Advance angle
deg.
0.3
Load
1/4
Timer adjustment_03
Pump speed
r/min
820--
Advance angle
deg.
0.7
0.4
1
Load
4/4
Timer adjustment_04
Pump speed
r/min
900+50
Advance angle
deg.
0.7
0.4
1
Load
3/4
Timer adjustment_05
Pump speed
r/min
1100-50
Advance angle
deg.
5.25
4.95
5.55
Load
4/4
Remarks
Finish
Finish
Test data Ex:
Governor adjustment
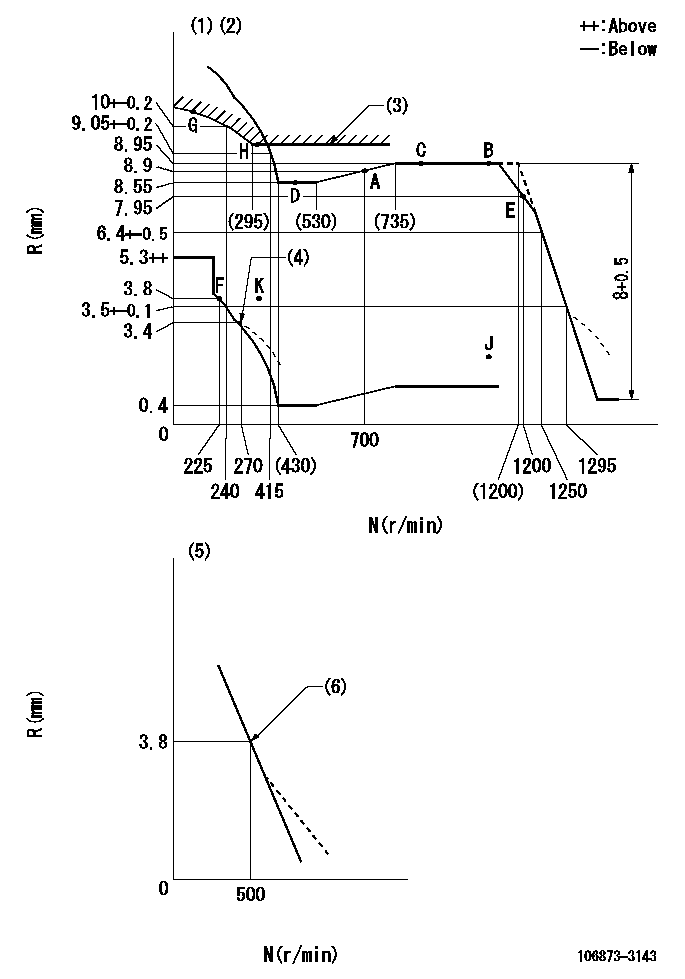
N:Pump speed
R:Rack position (mm)
(1)Tolerance for racks not indicated: +-0.05mm.
(2)Set idle at point K (N = N1, R = R1) and confirm that the injection quantity does not exceed Q1 at point J (N = N2).
(3)Excess fuel setting for starting: SXL
(4)Damper spring setting
(5)Variable speed specification: idling adjustment
(6)Main spring setting
----------
N1=325r/min R1=3.8mm N2=1100r/min Q1=3mm3/st SXL=9.45+-0.1mm
----------
----------
N1=325r/min R1=3.8mm N2=1100r/min Q1=3mm3/st SXL=9.45+-0.1mm
----------
Speed control lever angle

F:Full speed
I:Idle
(1)Stopper bolt setting
----------
----------
a=15.5deg+-5deg b=(14deg)+-5deg
----------
----------
a=15.5deg+-5deg b=(14deg)+-5deg
0000000901

F:Full load
I:Idle
(1)Use the hole at R = aa
(2)Stopper bolt setting
----------
aa=39mm
----------
a=39deg+-5deg b=43.5deg+-3deg
----------
aa=39mm
----------
a=39deg+-5deg b=43.5deg+-3deg
Stop lever angle
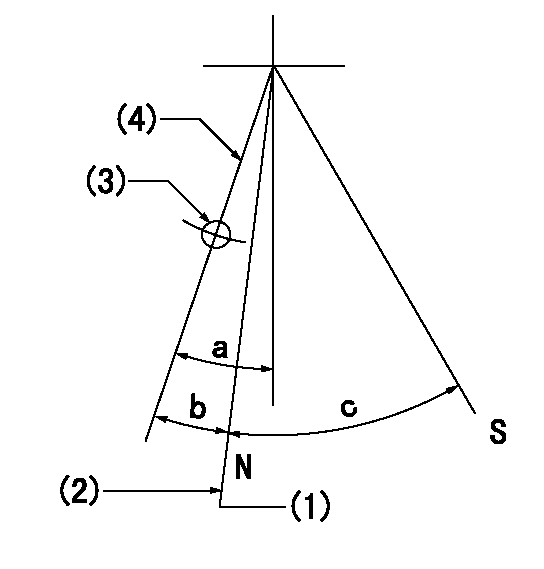
N:Pump normal
S:Stop the pump.
(1)Rack position = aa (at delivery), set before governor adjustment
(2)Set the stopper bolt (apply red paint).
(3)Use the pin at R = bb
(4)Lever free
----------
aa=12+-0.1mm bb=37mm
----------
a=(9deg)+-5deg b=9deg+-5deg c=35deg+-5deg
----------
aa=12+-0.1mm bb=37mm
----------
a=(9deg)+-5deg b=9deg+-5deg c=35deg+-5deg
Timing setting
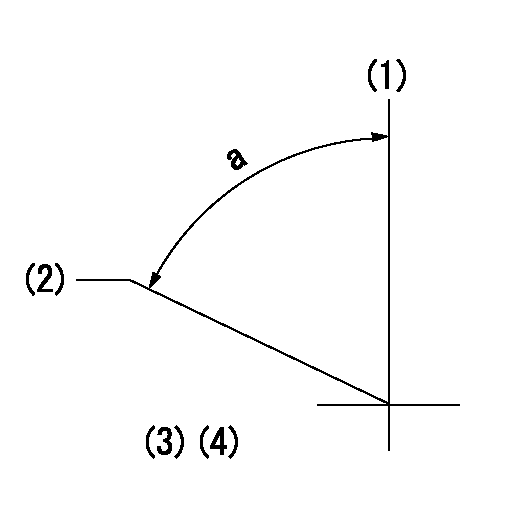
(1)Pump vertical direction
(2)Coupling's key groove position at No 1 cylinder's beginning of injection
(3)-
(4)-
----------
----------
a=(80deg)
----------
----------
a=(80deg)
Information:
New Dipsticks With Full Range Readings
The new rear sump and front sump dipsticks are used with their respective oil pans. These oil pans are used in truck applications with set-back axles.The new dipsticks are different because they have a FULL RANGE zone versus other dipsticks that have the traditional FULL mark. These dipsticks are used for truck applications with various angles and slants of engine installation (angle = front to back tilt, slant = sideways tilt).Calibration
Use the following procedure to calibrate FULL RANGE dipsticks. A convenient time to calibrate the dipstick is at the first oil change.Refer to the PM Level 1 of the Maintenance Management Schedule of this publication for the proper oil change interval.To verify the "ADD" mark and establish the actual "FULL" mark, use the following procedure: Truck must be parked on a level surface.1. Operate the engine until it reaches normal operating temperature.2. Stop the engine. Drain the oil and change the oil filter.3. Fill the crankcase with 32 U.S. quarts (30.3 liters) of oil. Brakesaver models require 36 quarts (34 L). Remote mounted or auxiliary filters require additional oil. For all information pertaining to auxiliary oil filters, refer to the OEM or manufacturer's instructions.4. Allow the oil to drain back to the sump for a minimum of five minutes.5. Remove the dipstick. The oil level should be at the ADD mark. If it is not, mark the actual level on the dipstick. This is now the correct ADD mark.6. Add an additional 4 U.S. quarts (3.8 liters) of oil to the sump. Allow enough time for the oil to drain into the sump. Again, check the level on the dipstick.7. This is the correct FULL mark in the FULL RANGE zone on the dipstick. If it is not, mark the new FULL level on the dipstick. Remote mounted or auxiliary filters require additional oil also. For all information pertaining to auxiliary oil filters, refer to the OEM or manufacturer's instructions.8. Start the engine and operate until it reaches normal operating temperature. Stop the engine.9. Allow the oil to drain back to the sump for a minimum of 10 minutes.10. Remove the dipstick. The oil level should be near the FULL mark. If it is not, add oil until the level reaches the FULL mark on the dipstick.This procedure is correct for use with either the non-spacer plate oil pan or the spacer plate oil pan. Sump capacities and oil levels are the same for each oil pan.Any FULL RANGE dipstick for the 3406B Truck engine can be calibrated using this procedure.
The new rear sump and front sump dipsticks are used with their respective oil pans. These oil pans are used in truck applications with set-back axles.The new dipsticks are different because they have a FULL RANGE zone versus other dipsticks that have the traditional FULL mark. These dipsticks are used for truck applications with various angles and slants of engine installation (angle = front to back tilt, slant = sideways tilt).Calibration
Use the following procedure to calibrate FULL RANGE dipsticks. A convenient time to calibrate the dipstick is at the first oil change.Refer to the PM Level 1 of the Maintenance Management Schedule of this publication for the proper oil change interval.To verify the "ADD" mark and establish the actual "FULL" mark, use the following procedure: Truck must be parked on a level surface.1. Operate the engine until it reaches normal operating temperature.2. Stop the engine. Drain the oil and change the oil filter.3. Fill the crankcase with 32 U.S. quarts (30.3 liters) of oil. Brakesaver models require 36 quarts (34 L). Remote mounted or auxiliary filters require additional oil. For all information pertaining to auxiliary oil filters, refer to the OEM or manufacturer's instructions.4. Allow the oil to drain back to the sump for a minimum of five minutes.5. Remove the dipstick. The oil level should be at the ADD mark. If it is not, mark the actual level on the dipstick. This is now the correct ADD mark.6. Add an additional 4 U.S. quarts (3.8 liters) of oil to the sump. Allow enough time for the oil to drain into the sump. Again, check the level on the dipstick.7. This is the correct FULL mark in the FULL RANGE zone on the dipstick. If it is not, mark the new FULL level on the dipstick. Remote mounted or auxiliary filters require additional oil also. For all information pertaining to auxiliary oil filters, refer to the OEM or manufacturer's instructions.8. Start the engine and operate until it reaches normal operating temperature. Stop the engine.9. Allow the oil to drain back to the sump for a minimum of 10 minutes.10. Remove the dipstick. The oil level should be near the FULL mark. If it is not, add oil until the level reaches the FULL mark on the dipstick.This procedure is correct for use with either the non-spacer plate oil pan or the spacer plate oil pan. Sump capacities and oil levels are the same for each oil pan.Any FULL RANGE dipstick for the 3406B Truck engine can be calibrated using this procedure.