Information injection-pump assembly
ZEXEL
106873-3120
1068733120
HINO
220007960A
220007960a
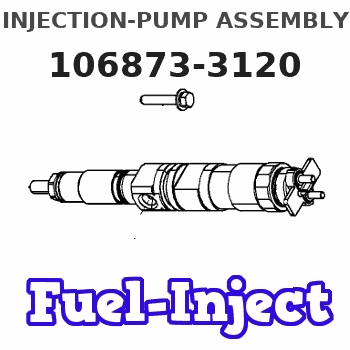
Rating:
Service parts 106873-3120 INJECTION-PUMP ASSEMBLY:
1.
_
7.
COUPLING PLATE
8.
_
9.
_
11.
Nozzle and Holder
23600-2480E
12.
Open Pre:MPa(Kqf/cm2)
14.7{150}/24.5{250}
14.
NOZZLE
Include in #1:
106873-3120
as INJECTION-PUMP ASSEMBLY
Cross reference number
ZEXEL
106873-3120
1068733120
HINO
220007960A
220007960a
Zexel num
Bosch num
Firm num
Name
Calibration Data:
Adjustment conditions
Test oil
1404 Test oil ISO4113 or {SAEJ967d}
1404 Test oil ISO4113 or {SAEJ967d}
Test oil temperature
degC
40
40
45
Nozzle and nozzle holder
105780-8140
Bosch type code
EF8511/9A
Nozzle
105780-0000
Bosch type code
DN12SD12T
Nozzle holder
105780-2080
Bosch type code
EF8511/9
Opening pressure
MPa
17.2
Opening pressure
kgf/cm2
175
Injection pipe
Outer diameter - inner diameter - length (mm) mm 8-3-600
Outer diameter - inner diameter - length (mm) mm 8-3-600
Overflow valve
134424-0820
Overflow valve opening pressure
kPa
127
107
147
Overflow valve opening pressure
kgf/cm2
1.3
1.1
1.5
Tester oil delivery pressure
kPa
157
157
157
Tester oil delivery pressure
kgf/cm2
1.6
1.6
1.6
Direction of rotation (viewed from drive side)
Right R
Right R
Injection timing adjustment
Direction of rotation (viewed from drive side)
Right R
Right R
Injection order
1-8-6-2-
7-5-4-3
Pre-stroke
mm
4.5
4.44
4.5
Beginning of injection position
Drive side NO.1
Drive side NO.1
Difference between angles 1
Cal 1-8 deg. 45 44.75 45.25
Cal 1-8 deg. 45 44.75 45.25
Difference between angles 2
Cal 1-6 deg. 90 89.75 90.25
Cal 1-6 deg. 90 89.75 90.25
Difference between angles 3
Cyl.1-2 deg. 135 134.75 135.25
Cyl.1-2 deg. 135 134.75 135.25
Difference between angles 4
Cal 1-7 deg. 180 179.75 180.25
Cal 1-7 deg. 180 179.75 180.25
Difference between angles 5
Cal 1-5 deg. 225 224.75 225.25
Cal 1-5 deg. 225 224.75 225.25
Difference between angles 6
Cal 1-4 deg. 270 269.75 270.25
Cal 1-4 deg. 270 269.75 270.25
Difference between angles 7
Cal 1-3 deg. 315 314.75 315.25
Cal 1-3 deg. 315 314.75 315.25
Injection quantity adjustment
Adjusting point
A
Rack position
9
Pump speed
r/min
700
700
700
Average injection quantity
mm3/st.
154.9
152.9
156.9
Max. variation between cylinders
%
0
-2
2
Basic
*
Fixing the lever
*
Injection quantity adjustment_02
Adjusting point
B
Rack position
8.9
Pump speed
r/min
500
500
500
Average injection quantity
mm3/st.
160.1
157.1
163.1
Fixing the lever
*
Injection quantity adjustment_03
Adjusting point
D
Rack position
9.05+-0.
5
Pump speed
r/min
1100
1100
1100
Average injection quantity
mm3/st.
142.6
138.6
146.6
Fixing the lever
*
Injection quantity adjustment_04
Adjusting point
E
Rack position
8.3
Pump speed
r/min
1200
1200
1200
Average injection quantity
mm3/st.
125.6
122.6
128.6
Fixing the lever
*
Injection quantity adjustment_05
Adjusting point
F
Rack position
3.9+-0.5
Pump speed
r/min
225
225
225
Average injection quantity
mm3/st.
12
9
15
Max. variation between cylinders
%
0
-15
15
Fixing the rack
*
Injection quantity adjustment_06
Adjusting point
G
Rack position
9.65+-0.
1
Pump speed
r/min
300
300
300
Average injection quantity
mm3/st.
178.2
174.2
182.2
Fixing the lever
*
Remarks
Startup boost setting
Startup boost setting
Injection quantity adjustment_07
Adjusting point
H
Rack position
-
Pump speed
r/min
100
100
100
Average injection quantity
mm3/st.
189
189
209
Fixing the lever
*
Remarks
After startup boost setting
After startup boost setting
Timer adjustment
Pump speed
r/min
600--
Advance angle
deg.
0
0
0
Load
1/4
Remarks
Start
Start
Timer adjustment_02
Pump speed
r/min
550
Advance angle
deg.
0.3
Load
1/4
Timer adjustment_03
Pump speed
r/min
700--
Advance angle
deg.
1
0.7
1.3
Load
4/4
Timer adjustment_04
Pump speed
r/min
900+50
Advance angle
deg.
1
0.7
1.3
Load
3/4
Timer adjustment_05
Pump speed
r/min
1100-50
Advance angle
deg.
4.75
4.45
5.05
Load
4/4
Remarks
Finish
Finish
Test data Ex:
Governor adjustment
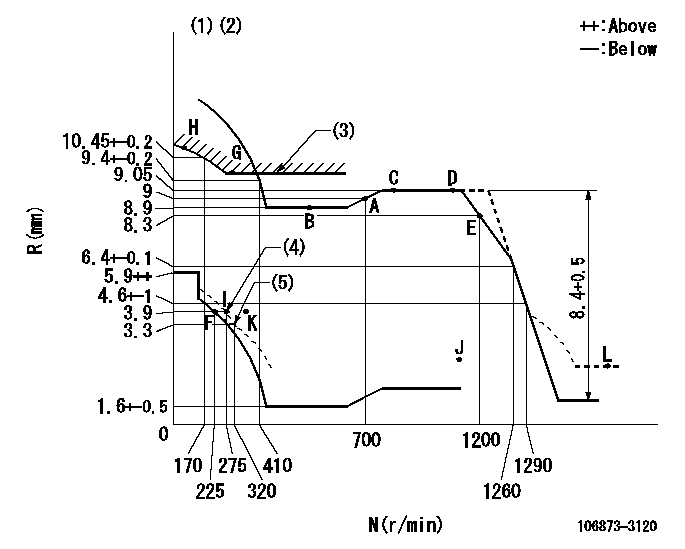
N:Pump speed
R:Rack position (mm)
(1)Tolerance for racks not indicated: +-0.05mm.
(2)Set idle at point K (N = N1, R = R1) and confirm that the injection quantity does not exceed Q1 at point J (N = N2).
(3)Excess fuel setting for starting: SXL
(4)When air cylinder is operating.
(5)Damper spring setting
----------
N1=300r/min R1=3.9mm N2=1150r/min Q1=3mm3/3st SXL=9.65+-0.1mm
----------
----------
N1=300r/min R1=3.9mm N2=1150r/min Q1=3mm3/3st SXL=9.65+-0.1mm
----------
Speed control lever angle

F:Full speed
----------
----------
a=16deg+-5deg
----------
----------
a=16deg+-5deg
0000000901
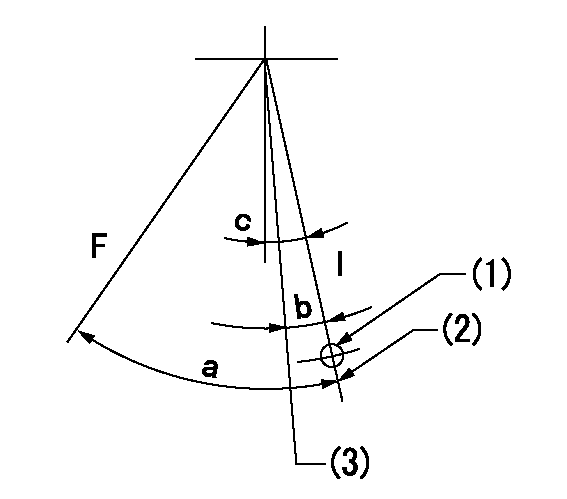
F:Full load
I:Idle
(1)Use the hole at R = aa
(2)Stopper bolt setting
(3)Set point I (at air cylinder operation)
----------
aa=90mm
----------
a=39deg+-3deg b=(8deg) c=14deg+-5deg
----------
aa=90mm
----------
a=39deg+-3deg b=(8deg) c=14deg+-5deg
Stop lever angle
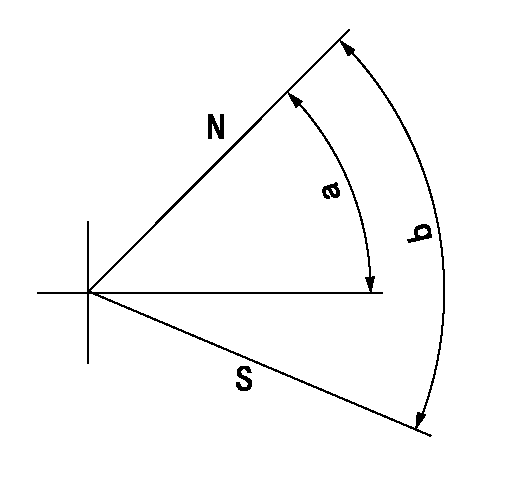
N:Pump normal
S:Stop the pump.
----------
----------
a=46deg+-5deg b=64deg+-5deg
----------
----------
a=46deg+-5deg b=64deg+-5deg
0000001501 RACK SENSOR
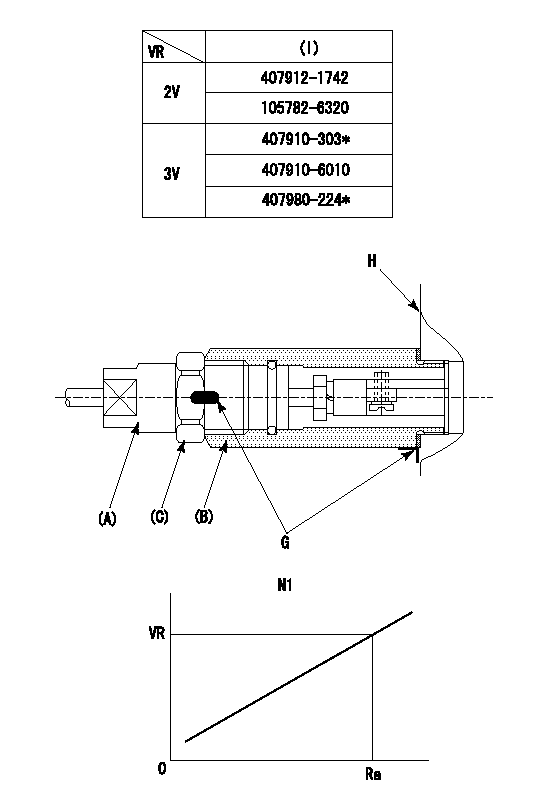
(VR) measurement voltage
(I) Part number of the control unit
(G) Apply red paint.
(H): End surface of the pump
1. Rack sensor adjustment (-0620)
(1)Fix the speed control lever at the full position
(2)Set the speed to N1 r/min.
(If the boost compensator is provided, apply boost pressure.)
(3)Adjust the bobbin (A) so that the rack sensor's output voltage is VR+-0.01.
(4)At that time, rack position must be Ra.
(5)Apply G at two places.
Connecting part between the joint (B) and the nut (F)
Connecting part between the joint (B) and the end surface of the pump (H)
----------
N1=900r/min Ra=(9.05)mm
----------
----------
N1=900r/min Ra=(9.05)mm
----------
0000001601 LEVER

1. Air cylinder adjustment
(1)With the load lever in the idle position, temporarily set the distance between the load lever A and the air cylinder D at approximately L.
(2)Set N1 and apply P1 to the air cylinder D.
(3)Adjust set bolt (D) to obtain R1 at the same speed.
(4)Lock using nut C.
(5)Apply positive pressure several times.
(6)Confirm that the load lever A returns to the idling position N2 at pressure P2.
(7)Also at P1 confirm R1 (N1).
----------
L=(5)mm R1=3.9mm N1=275r/min N2=225r/min P1=392+98kPa(4+1kgf/cm2) P2=0kPa(0kgf/cm2)
----------
----------
L=(5)mm R1=3.9mm N1=275r/min N2=225r/min P1=392+98kPa(4+1kgf/cm2) P2=0kPa(0kgf/cm2)
----------
Timing setting
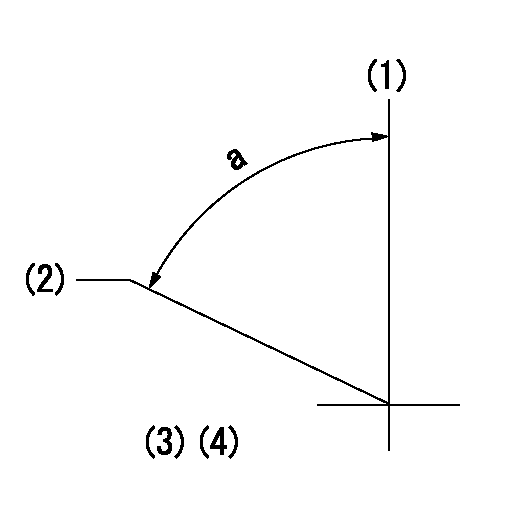
(1)Pump vertical direction
(2)Coupling's key groove position at No 1 cylinder's beginning of injection
(3)-
(4)-
----------
----------
a=(80deg)
----------
----------
a=(80deg)
Information:
Add Coolant Additive (Conditioner)
1. Release the cooling system relief valve slowly to relieve pressure and remove filler cap. Inspect condition of cap gasket. Replace cap if necessary.2. It may be necessary to drain enough coolant from the system to allow for the addition of cooling system additive (conditioner).3. Add Caterpillar Cooling System Conditioner. Add 0.24 liter (1/2 U.S. pint) of Caterpillar Cooling System Additive (Conditioner) for each 38 liter (10 U.S. gallon) of cooling system capacity. This will maintain the required concentration of conditioner. On new, rebuilt or remanufactured engines only, or when draining and changing the coolant, add liquid additive concentration of coolant additive of 1 liter (1 U.S. quart) for every 15 liter (4 U.S. gallon) of cooling system capacity for systems using water as coolant only.Caterpillar Antifreeze contains the necessary coolant additive precharge. Only add the coolant additive precharge if you have decided not to use Caterpillar Antifreeze.Refer to the Refill Capacities chart in this publication for the cooling system capacity for your engine.
Do not use any Methoxypropanol-based antifreeze or coolants such as Dowtherm 209 Full-Fill coolant in the cooling system. Methoxypropanol will cause some seals and gaskets to deteriorate and fail.
4. Maintain coolant level to within 13 mm (1/2 in) below the bottom of the filler tube or to the proper level (upper half) on the sight glass, if equipped. Add premixed coolant if necessary to bring the coolant to the proper level.Refer to the topic Cooling System Specifications in the Specifications section in this manual for additional information about coolant mixture and supplemental coolant additive.5. Start the engine and check for leaks or damaged piping. Allow the coolant level to stabilize. Inspect the cooling system pipes and lines for leaks and/or damaged connections. Make repairs if necessary. Install the filler cap.Coolant Analysis
Obtain Coolant Sample
There are
1. Release the cooling system relief valve slowly to relieve pressure and remove filler cap. Inspect condition of cap gasket. Replace cap if necessary.2. It may be necessary to drain enough coolant from the system to allow for the addition of cooling system additive (conditioner).3. Add Caterpillar Cooling System Conditioner. Add 0.24 liter (1/2 U.S. pint) of Caterpillar Cooling System Additive (Conditioner) for each 38 liter (10 U.S. gallon) of cooling system capacity. This will maintain the required concentration of conditioner. On new, rebuilt or remanufactured engines only, or when draining and changing the coolant, add liquid additive concentration of coolant additive of 1 liter (1 U.S. quart) for every 15 liter (4 U.S. gallon) of cooling system capacity for systems using water as coolant only.Caterpillar Antifreeze contains the necessary coolant additive precharge. Only add the coolant additive precharge if you have decided not to use Caterpillar Antifreeze.Refer to the Refill Capacities chart in this publication for the cooling system capacity for your engine.
Do not use any Methoxypropanol-based antifreeze or coolants such as Dowtherm 209 Full-Fill coolant in the cooling system. Methoxypropanol will cause some seals and gaskets to deteriorate and fail.
4. Maintain coolant level to within 13 mm (1/2 in) below the bottom of the filler tube or to the proper level (upper half) on the sight glass, if equipped. Add premixed coolant if necessary to bring the coolant to the proper level.Refer to the topic Cooling System Specifications in the Specifications section in this manual for additional information about coolant mixture and supplemental coolant additive.5. Start the engine and check for leaks or damaged piping. Allow the coolant level to stabilize. Inspect the cooling system pipes and lines for leaks and/or damaged connections. Make repairs if necessary. Install the filler cap.Coolant Analysis
Obtain Coolant Sample
There are