Information injection-pump assembly
BOSCH
9 400 611 022
9400611022
ZEXEL
106873-2934
1068732934
MITSUBISHI
ME093216
me093216
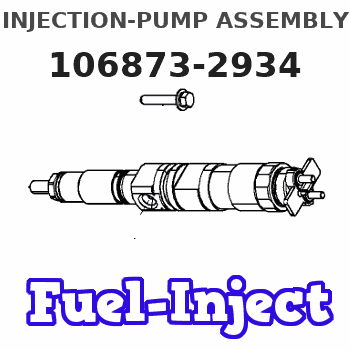
Rating:
Service parts 106873-2934 INJECTION-PUMP ASSEMBLY:
1.
_
7.
COUPLING PLATE
8.
_
9.
_
11.
Nozzle and Holder
ME091276
12.
Open Pre:MPa(Kqf/cm2)
17.7{180}/21.6{220}
15.
NOZZLE SET
Include in #1:
106873-2934
as INJECTION-PUMP ASSEMBLY
Cross reference number
BOSCH
9 400 611 022
9400611022
ZEXEL
106873-2934
1068732934
MITSUBISHI
ME093216
me093216
Zexel num
Bosch num
Firm num
Name
106873-2934
9 400 611 022
ME093216 MITSUBISHI
INJECTION-PUMP ASSEMBLY
8DC11 K 14CD INJECTION PUMP ASSY PE8P PE
8DC11 K 14CD INJECTION PUMP ASSY PE8P PE
Calibration Data:
Adjustment conditions
Test oil
1404 Test oil ISO4113 or {SAEJ967d}
1404 Test oil ISO4113 or {SAEJ967d}
Test oil temperature
degC
40
40
45
Nozzle and nozzle holder
105780-8140
Bosch type code
EF8511/9A
Nozzle
105780-0000
Bosch type code
DN12SD12T
Nozzle holder
105780-2080
Bosch type code
EF8511/9
Opening pressure
MPa
17.2
Opening pressure
kgf/cm2
175
Injection pipe
Outer diameter - inner diameter - length (mm) mm 8-3-600
Outer diameter - inner diameter - length (mm) mm 8-3-600
Overflow valve
134424-1320
Overflow valve opening pressure
kPa
157
123
191
Overflow valve opening pressure
kgf/cm2
1.6
1.25
1.95
Tester oil delivery pressure
kPa
157
157
157
Tester oil delivery pressure
kgf/cm2
1.6
1.6
1.6
Direction of rotation (viewed from drive side)
Right R
Right R
Injection timing adjustment
Direction of rotation (viewed from drive side)
Right R
Right R
Injection order
1-2-7-3-
4-5-6-8
Pre-stroke
mm
4.8
4.75
4.85
Beginning of injection position
Governor side NO.1
Governor side NO.1
Difference between angles 1
Cyl.1-2 deg. 45 44.5 45.5
Cyl.1-2 deg. 45 44.5 45.5
Difference between angles 2
Cal 1-7 deg. 90 89.5 90.5
Cal 1-7 deg. 90 89.5 90.5
Difference between angles 3
Cal 1-3 deg. 135 134.5 135.5
Cal 1-3 deg. 135 134.5 135.5
Difference between angles 4
Cal 1-4 deg. 180 179.5 180.5
Cal 1-4 deg. 180 179.5 180.5
Difference between angles 5
Cal 1-5 deg. 225 224.5 225.5
Cal 1-5 deg. 225 224.5 225.5
Difference between angles 6
Cal 1-6 deg. 270 269.5 270.5
Cal 1-6 deg. 270 269.5 270.5
Difference between angles 7
Cal 1-8 deg. 315 314.5 315.5
Cal 1-8 deg. 315 314.5 315.5
Injection quantity adjustment
Adjusting point
-
Rack position
10.3
Pump speed
r/min
650
650
650
Each cylinder's injection qty
mm3/st.
122
118.3
125.7
Basic
*
Fixing the rack
*
Standard for adjustment of the maximum variation between cylinders
*
Injection quantity adjustment_02
Adjusting point
C
Rack position
6.2+-0.5
Pump speed
r/min
225
225
225
Each cylinder's injection qty
mm3/st.
17.5
14.9
20.1
Fixing the rack
*
Standard for adjustment of the maximum variation between cylinders
*
Injection quantity adjustment_03
Adjusting point
A
Rack position
R1(10.3)
Pump speed
r/min
650
650
650
Average injection quantity
mm3/st.
122
121
123
Basic
*
Fixing the lever
*
Injection quantity adjustment_04
Adjusting point
B
Rack position
R1+0.05
Pump speed
r/min
1100
1100
1100
Average injection quantity
mm3/st.
128.5
124.5
132.5
Fixing the lever
*
Injection quantity adjustment_05
Adjusting point
E
Rack position
-
Pump speed
r/min
100
100
100
Average injection quantity
mm3/st.
135
115
155
Fixing the lever
*
Remarks
After startup boost setting
After startup boost setting
Timer adjustment
Pump speed
r/min
500--
Advance angle
deg.
0
0
0
Load
0/4
Remarks
Start
Start
Timer adjustment_02
Pump speed
r/min
450
Advance angle
deg.
0.5
Load
0/4
Timer adjustment_03
Pump speed
r/min
590
Advance angle
deg.
2
1.5
2.5
Load
0/4
Timer adjustment_04
Pump speed
r/min
(950)
Advance angle
deg.
2
1.5
2.5
Load
4/4
Timer adjustment_05
Pump speed
r/min
(1100)
Advance angle
deg.
5.5
5
6
Load
4/4
Remarks
Finish
Finish
Test data Ex:
Governor adjustment
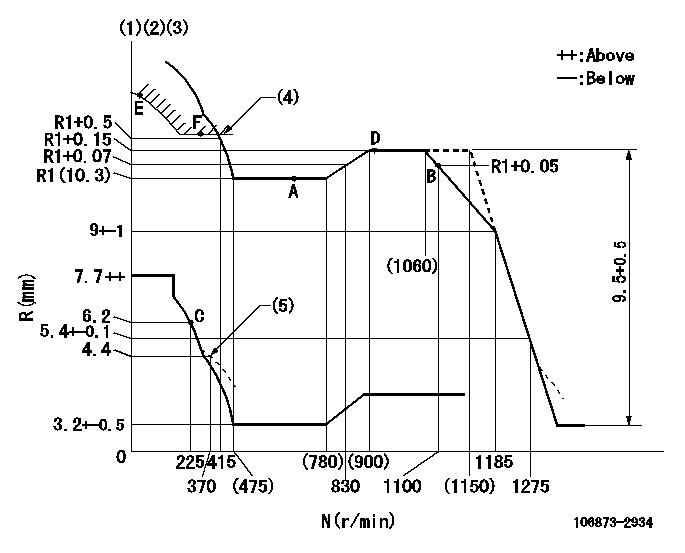
N:Pump speed
R:Rack position (mm)
(1)Lever ratio: RT
(2)Target shim dimension: TH
(3)Tolerance for racks not indicated: +-0.05mm.
(4)Excess fuel setting for starting: SXL
(5)Damper spring setting
----------
RT=1 TH=2.9mm SXL=10.8+-0.1mm
----------
----------
RT=1 TH=2.9mm SXL=10.8+-0.1mm
----------
Speed control lever angle

F:Full speed
----------
----------
a=19.5deg+-5deg
----------
----------
a=19.5deg+-5deg
0000000901

F:Full load
I:Idle
(1)Stopper bolt setting
----------
----------
a=10deg+-5deg b=26.5deg+-3deg
----------
----------
a=10deg+-5deg b=26.5deg+-3deg
Stop lever angle
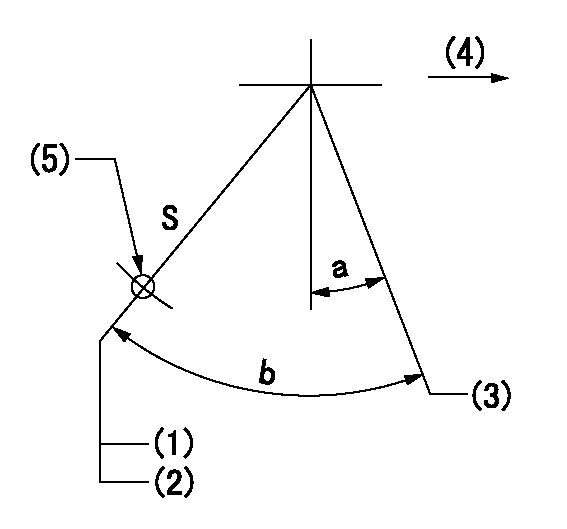
S:Stop the pump.
(1)Rack position = aa
(2)Stopper bolt setting
(3)Free (at delivery)
(4)Drive side
(5)Use the hole at R = bb
----------
aa=4.1-0.5mm bb=36mm
----------
a=10.5deg+-5deg b=55.5deg+7deg-5deg
----------
aa=4.1-0.5mm bb=36mm
----------
a=10.5deg+-5deg b=55.5deg+7deg-5deg
0000001501 MICRO SWITCH
Adjustment of the micro-switch
Adjust the bolt to obtain the following lever position when the micro-switch is ON.
(1)Speed N1
(2)Rack position Ra
----------
N1=325r/min Ra=5.7+-0.1mm
----------
----------
N1=325r/min Ra=5.7+-0.1mm
----------
Timing setting

(1)Pump vertical direction
(2)Coupling's key groove position at No 1 cylinder's beginning of injection
(3)B.T.D.C.: aa
(4)-
----------
aa=7deg
----------
a=(40deg)
----------
aa=7deg
----------
a=(40deg)
Information:
You must read and understand the warnings and instructions contained in the Safety section of this manual before performing any operation or maintenance procedures.Before proceeding with this maintenance interval, perform previous maintenance intervals and Daily maintenance requirements. Perform the maintenance at the interval listed in the Maintenance Schedule for your engine.
For maintenance of the following components in this interval, refer to the OEM manual for maintenance instructions. The following are basic suggestions and instructions.
Marine Gear
Drain Oil
With the oil warm and the engine stopped, drain the transmission.1. Remove the transmission drain plug and allow the oil to drain. Obtain an oil sample for analysis.2. Clean and install the drain plug.If a Sump Pump is Used to Drain Oil
a. Connect a drain line and container to top outlet (A) of pump.b. Be sure valve (B) on the engine oil pan line is closed. Marks on the valve must be turned at right angles to the direction of the engine oil line. c. Open valve (C) on the transmission oil line. The marks on this valve must be turned so that one mark points to the pump and the second mark points to the transmission.d. Operate the sump pump (D) handle until the transmission is empty.e. Close the sump pump valve on the oil line to the transmission.Change Filters
1. Remove transmission oil filter housing drain plug (if equipped). Allow the oil to drain into the marine gear transmission sump.2. Remove filter assembly. Disassemble and discard the element.3. Clean the filter housing and assembly parts with clean, nonflammable solvent. Clean and install the filter housing drain plug.4. Inspect any retainer plates and/or seals. Install new seals if necessary.5. Assemble and install a new filter element assembly. Tighten all bolts.6. Operate the sump pump handle until the transmission is empty. Close the sump pump valve on the oil line to the transmission.Clean the Oil Strainer
1. Remove the strainer cover and plug. Remove the spring washer, strainer screen and magnetic screen tube (if equipped).2. Wash the strainer and magnetic screen tube with clean, nonflammable solvent. If a magnet is broken, install the new magnet properly. The North (N) poles and South (S) poles of the magnets are adjacent to each other so that they repel instead of attract: S-N, N-S, S-N.3. Inspect the strainer, plug and the cover seal for damage. Use new parts if used ones are damaged.4. Install the magnetic screen tube, strainer, spring washer, seal, cover and plug.Clean the Breather (All Marine Transmissions)
1. Remove the breather.2. Clean the breather with clean, nonflammable solvent.3. Install the breather.Fill the Transmission
Be sure both sump pump valves (one to the transmission and one to the engine oil pan) are closed. Otherwise a transfer of oil may occur during sump pump operation and damage could result.
1. Be sure the marine gear drain plug has been installed, or the sump pump valve (C) on the oil line to the marine gear drain line has been closed.2. Fill the marine gear to the FULL mark on the
For maintenance of the following components in this interval, refer to the OEM manual for maintenance instructions. The following are basic suggestions and instructions.
Marine Gear
Drain Oil
With the oil warm and the engine stopped, drain the transmission.1. Remove the transmission drain plug and allow the oil to drain. Obtain an oil sample for analysis.2. Clean and install the drain plug.If a Sump Pump is Used to Drain Oil
a. Connect a drain line and container to top outlet (A) of pump.b. Be sure valve (B) on the engine oil pan line is closed. Marks on the valve must be turned at right angles to the direction of the engine oil line. c. Open valve (C) on the transmission oil line. The marks on this valve must be turned so that one mark points to the pump and the second mark points to the transmission.d. Operate the sump pump (D) handle until the transmission is empty.e. Close the sump pump valve on the oil line to the transmission.Change Filters
1. Remove transmission oil filter housing drain plug (if equipped). Allow the oil to drain into the marine gear transmission sump.2. Remove filter assembly. Disassemble and discard the element.3. Clean the filter housing and assembly parts with clean, nonflammable solvent. Clean and install the filter housing drain plug.4. Inspect any retainer plates and/or seals. Install new seals if necessary.5. Assemble and install a new filter element assembly. Tighten all bolts.6. Operate the sump pump handle until the transmission is empty. Close the sump pump valve on the oil line to the transmission.Clean the Oil Strainer
1. Remove the strainer cover and plug. Remove the spring washer, strainer screen and magnetic screen tube (if equipped).2. Wash the strainer and magnetic screen tube with clean, nonflammable solvent. If a magnet is broken, install the new magnet properly. The North (N) poles and South (S) poles of the magnets are adjacent to each other so that they repel instead of attract: S-N, N-S, S-N.3. Inspect the strainer, plug and the cover seal for damage. Use new parts if used ones are damaged.4. Install the magnetic screen tube, strainer, spring washer, seal, cover and plug.Clean the Breather (All Marine Transmissions)
1. Remove the breather.2. Clean the breather with clean, nonflammable solvent.3. Install the breather.Fill the Transmission
Be sure both sump pump valves (one to the transmission and one to the engine oil pan) are closed. Otherwise a transfer of oil may occur during sump pump operation and damage could result.
1. Be sure the marine gear drain plug has been installed, or the sump pump valve (C) on the oil line to the marine gear drain line has been closed.2. Fill the marine gear to the FULL mark on the
Have questions with 106873-2934?
Group cross 106873-2934 ZEXEL
Mitsubishi
106873-2934
9 400 611 022
ME093216
INJECTION-PUMP ASSEMBLY
8DC11
8DC11