Information injection-pump assembly
BOSCH
9 400 618 395
9400618395
ZEXEL
106873-2870
1068732870
MITSUBISHI
ME160954
me160954
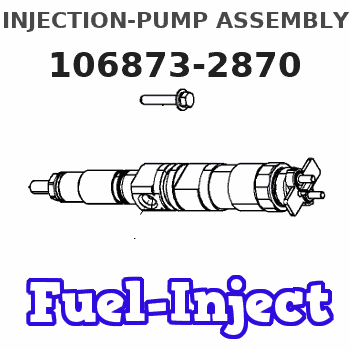
Rating:
Service parts 106873-2870 INJECTION-PUMP ASSEMBLY:
1.
_
7.
COUPLING PLATE
8.
_
9.
_
11.
Nozzle and Holder
12.
Open Pre:MPa(Kqf/cm2)
17.7{180}/24.5{250}
15.
NOZZLE SET
Include in #1:
106873-2870
as INJECTION-PUMP ASSEMBLY
Cross reference number
BOSCH
9 400 618 395
9400618395
ZEXEL
106873-2870
1068732870
MITSUBISHI
ME160954
me160954
Zexel num
Bosch num
Firm num
Name
106873-2870
9 400 618 395
ME160954 MITSUBISHI
INJECTION-PUMP ASSEMBLY
8M20-2 K
8M20-2 K
Calibration Data:
Adjustment conditions
Test oil
1404 Test oil ISO4113 or {SAEJ967d}
1404 Test oil ISO4113 or {SAEJ967d}
Test oil temperature
degC
40
40
45
Nozzle and nozzle holder
105780-8140
Bosch type code
EF8511/9A
Nozzle
105780-0000
Bosch type code
DN12SD12T
Nozzle holder
105780-2080
Bosch type code
EF8511/9
Opening pressure
MPa
17.2
Opening pressure
kgf/cm2
175
Injection pipe
Outer diameter - inner diameter - length (mm) mm 8-3-600
Outer diameter - inner diameter - length (mm) mm 8-3-600
Overflow valve
131424-4620
Overflow valve opening pressure
kPa
255
221
289
Overflow valve opening pressure
kgf/cm2
2.6
2.25
2.95
Tester oil delivery pressure
kPa
157
157
157
Tester oil delivery pressure
kgf/cm2
1.6
1.6
1.6
Direction of rotation (viewed from drive side)
Right R
Right R
Injection timing adjustment
Direction of rotation (viewed from drive side)
Right R
Right R
Injection order
1-2-7-3-
4-5-6-8
Pre-stroke
mm
4.8
4.75
4.85
Beginning of injection position
Governor side NO.1
Governor side NO.1
Difference between angles 1
Cyl.1-2 deg. 45 44.5 45.5
Cyl.1-2 deg. 45 44.5 45.5
Difference between angles 2
Cal 1-7 deg. 90 89.5 90.5
Cal 1-7 deg. 90 89.5 90.5
Difference between angles 3
Cal 1-3 deg. 135 134.5 135.5
Cal 1-3 deg. 135 134.5 135.5
Difference between angles 4
Cal 1-4 deg. 180 179.5 180.5
Cal 1-4 deg. 180 179.5 180.5
Difference between angles 5
Cal 1-5 deg. 225 224.5 225.5
Cal 1-5 deg. 225 224.5 225.5
Difference between angles 6
Cal 1-6 deg. 270 269.5 270.5
Cal 1-6 deg. 270 269.5 270.5
Difference between angles 7
Cal 1-8 deg. 315 314.5 315.5
Cal 1-8 deg. 315 314.5 315.5
Injection quantity adjustment
Adjusting point
-
Rack position
10.4
Pump speed
r/min
650
650
650
Each cylinder's injection qty
mm3/st.
140
135.8
144.2
Basic
*
Fixing the rack
*
Standard for adjustment of the maximum variation between cylinders
*
Injection quantity adjustment_02
Adjusting point
C
Rack position
6.8+-0.5
Pump speed
r/min
225
225
225
Each cylinder's injection qty
mm3/st.
19
16.1
21.9
Fixing the rack
*
Standard for adjustment of the maximum variation between cylinders
*
Injection quantity adjustment_03
Adjusting point
A
Rack position
R1(10.4)
Pump speed
r/min
650
650
650
Average injection quantity
mm3/st.
140
139
141
Basic
*
Fixing the lever
*
Injection quantity adjustment_04
Adjusting point
E
Rack position
-
Pump speed
r/min
100
100
100
Average injection quantity
mm3/st.
165
125
205
Fixing the lever
*
Remarks
After startup boost setting
After startup boost setting
Test data Ex:
Governor adjustment
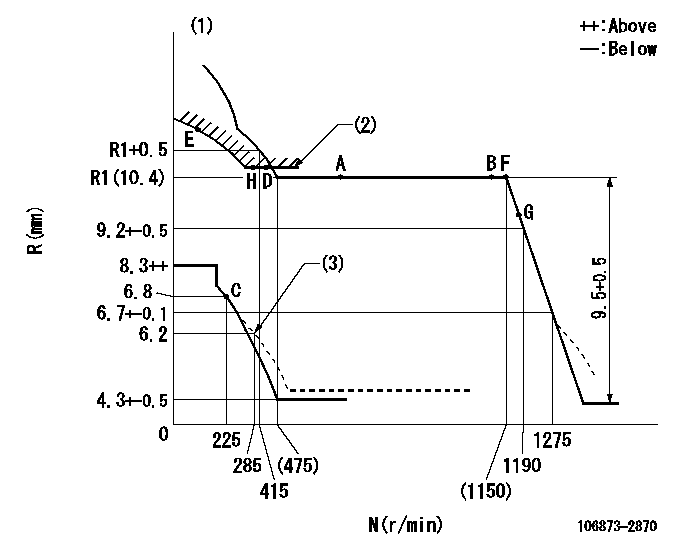
N:Pump speed
R:Rack position (mm)
(1)Tolerance for racks not indicated: +-0.05mm.
(2)Excess fuel setting for starting: SXL
(3)Damper spring setting
----------
SXL=10.6+-0.1mm
----------
----------
SXL=10.6+-0.1mm
----------
Timer adjustment

(1)Adjusting range
(2)Step response time
(N): Speed of the pump
(L): Load
(theta) Advance angle
(Srd1) Step response time 1
(Srd2) Step response time 2
1. Adjusting conditions for the variable timer
(1)Adjust the clearance between the pickup and the protrusion to L.
----------
L=1-0.2mm N2=800r/min C2=(8.8)deg t1=2.5--sec. t2=2.5--sec.
----------
N1=750++r/min P1=0kPa(0kgf/cm2) P2=392kPa(4kgf/cm2) C1=8.8+-0.3deg R01=0/4load R02=4/4load
----------
L=1-0.2mm N2=800r/min C2=(8.8)deg t1=2.5--sec. t2=2.5--sec.
----------
N1=750++r/min P1=0kPa(0kgf/cm2) P2=392kPa(4kgf/cm2) C1=8.8+-0.3deg R01=0/4load R02=4/4load
Speed control lever angle

F:Full speed
----------
----------
a=(22deg)+-5deg
----------
----------
a=(22deg)+-5deg
0000000901

F:Full load
I:Idle
(1)Stopper bolt setting
----------
----------
a=10deg+-5deg b=22.5deg+-3deg
----------
----------
a=10deg+-5deg b=22.5deg+-3deg
Stop lever angle
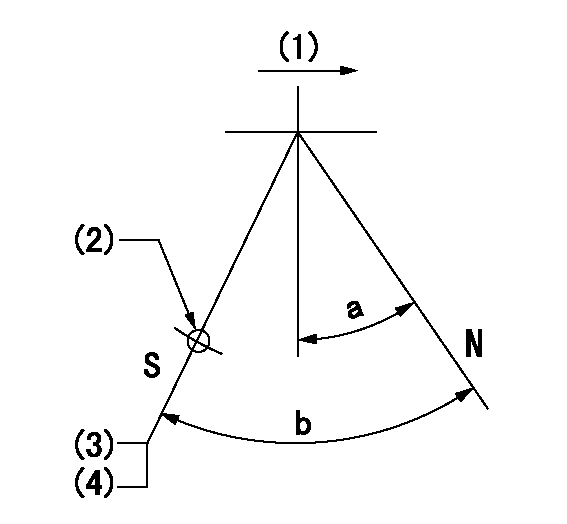
N:Pump normal
S:Stop the pump.
(1)Drive side
(2)Use the hole at R = aa
(3)Rack position bb
(4)Stopper bolt setting
----------
aa=36mm bb=4.3-0.5mm
----------
a=10.5deg+-5deg b=55deg+7deg-5deg
----------
aa=36mm bb=4.3-0.5mm
----------
a=10.5deg+-5deg b=55deg+7deg-5deg
0000001501 MICRO SWITCH
Adjustment of the micro-switch
Adjust the bolt to obtain the following lever position when the micro-switch is ON.
(1)Speed N1
(2)Rack position Ra
----------
N1=325r/min Ra=6.3+-0.1mm
----------
----------
N1=325r/min Ra=6.3+-0.1mm
----------
0000001601 RACK SENSOR

V1:Supply voltage
V2f:Full side output voltage
V2i:Idle side output voltage
(A) Black
(B) Yellow
(C) Red
(D) Trimmer
(E): Shaft
(F) Nut
(G) Load lever
1. Load sensor adjustment
(1)Connect as shown in the above diagram and apply supply voltage V1.
(2)Hold the load lever (G) against the full side.
(3)Turn the shaft so that the voltage between (A) and (B) is V2.
(4)Hold the load lever (G) against the idle side.
(5)Adjust (D) so that the voltage between (A) and (B) is V2i.
(6)Repeat the above adjustments.
(7)Tighten the nut (F) at the point satisfying the standards.
(8)Hold the load lever against the full side stopper and the idle side stopper.
(9)At this time, confirm that the full side output voltage is V2f and the idle side output voltage is V2i.
----------
V1=5+-0.02V V2f=0.15+0.03V V2i=2.35-0.03V
----------
----------
V1=5+-0.02V V2f=0.15+0.03V V2i=2.35-0.03V
----------
Timing setting

(1)Pump vertical direction
(2)Coupling's key groove position at No 1 cylinder's beginning of injection
(3)B.T.D.C.: aa
(4)-
----------
aa=12deg
----------
a=(40deg)
----------
aa=12deg
----------
a=(40deg)
Information:
Operate the controls ONLY with the engine running. Report any needed repairs noted during operation.
Engine and Marine Transmission Operation
Operate a cool engine at low load. After normal oil pressure is reached and the temperature gauges begin to move, the engine may be operated at full load.Transmission Selector Lever
Typical ExampleFull power is transferred from the engine through the marine transmission, in either forward (1) or reverse (3) rotation, to the propeller shaft. The engine transmissions can be operated by mechanical, hydraulic, pneumatic or electrically actuated controls for the forward and reverse drives.A control valve directs the flow of oil to either the forward or reverse clutch (for forward or reverse operation). The valve is operated by a selector lever, which can be remotely operated (from the pilot station) or operated manually from the transmission (in the engine room).Moving and Getting Underway
The marine transmission selector valve is usually operated from the pilot house. It can also be operated at the marine transmission. Pilot house controls must be adjusted so as to permit full travel of the selector lever on the marine transmission, and full engagement of the clutch plates.To get underway after the engine has started and is warm:1. Fully engage the marine transmission control lever in the desired direction of travel. Allow one second before increasing engine speed.2. Wait a sufficient amount of time to allow complete engagement of the clutch.3. Gradually increase engine speed as required.Docking or Traveling (Direction Change)
The engine torque must be able to overcome the propeller and drive line inertia, the marine transmission inertia and the propeller slip stream torque. 1. Reduce engine speed to LOW IDLE.
Do not shift across NEUTRAL position without a few seconds delay. When reversing direction of travel (propeller rotation), stop at least two seconds in the position to allow the clutch plates to completely disengage, and the propeller to stop turning. A direct through-shift will cause severe shock loads to the engine, marine gear and hull. Also, it can cause the engine to reverse its rotation. If the engine reverses rotation, the engine and marine transmission oil pumps will be running opposite normal rotation. Oil will be pulled from the bearings and cause severe damage.
2. Move the marine transmission control lever to the NEUTRAL position.3. Move the marine transmission control lever to the engaged position. Wait a sufficient amount of time to allow complete engagement of the clutch before gradually increasing engine speed. The marine gear rotation should not be changed at full engine speed. To prevent the propeller from stalling or reversing the engine's rotation gradually increase engine speed as the clutch is engaged. A sequenced engine control system may be required. This equipment consists of a throttle boost with an optional shaft brake. The throttle boost system momentarily increases engine speed as the marine transmission selector lever is moved from NEUTRAL to the engaged position. The throttle boost is released upon completion of clutch engagement. The governor setting then regulates the engine speed.With the selector lever in the
Have questions with 106873-2870?
Group cross 106873-2870 ZEXEL
Mitsubishi
Mitsubishi
106873-2870
9 400 618 395
ME160954
INJECTION-PUMP ASSEMBLY
8M20-2
8M20-2