Information injection-pump assembly
ZEXEL
106873-2830
1068732830
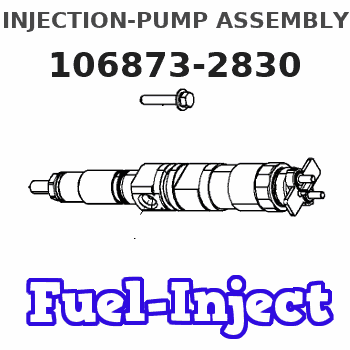
Rating:
Cross reference number
ZEXEL
106873-2830
1068732830
Zexel num
Bosch num
Firm num
Name
106873-2830
INJECTION-PUMP ASSEMBLY
Calibration Data:
Adjustment conditions
Test oil
1404 Test oil ISO4113 or {SAEJ967d}
1404 Test oil ISO4113 or {SAEJ967d}
Test oil temperature
degC
40
40
45
Nozzle and nozzle holder
105780-8140
Bosch type code
EF8511/9A
Nozzle
105780-0000
Bosch type code
DN12SD12T
Nozzle holder
105780-2080
Bosch type code
EF8511/9
Opening pressure
MPa
17.2
Opening pressure
kgf/cm2
175
Injection pipe
Outer diameter - inner diameter - length (mm) mm 8-3-600
Outer diameter - inner diameter - length (mm) mm 8-3-600
Overflow valve
131424-7920
Overflow valve opening pressure
kPa
255
221
289
Overflow valve opening pressure
kgf/cm2
2.6
2.25
2.95
Tester oil delivery pressure
kPa
157
157
157
Tester oil delivery pressure
kgf/cm2
1.6
1.6
1.6
Direction of rotation (viewed from drive side)
Right R
Right R
Injection timing adjustment
Direction of rotation (viewed from drive side)
Right R
Right R
Injection order
1-2-7-3-
4-5-6-8
Pre-stroke
mm
4.4
4.37
4.43
Beginning of injection position
Governor side NO.1
Governor side NO.1
Difference between angles 1
Cyl.1-2 deg. 45 44.75 45.25
Cyl.1-2 deg. 45 44.75 45.25
Difference between angles 2
Cal 1-7 deg. 90 89.75 90.25
Cal 1-7 deg. 90 89.75 90.25
Difference between angles 3
Cal 1-3 deg. 135 134.75 135.25
Cal 1-3 deg. 135 134.75 135.25
Difference between angles 4
Cal 1-4 deg. 180 179.75 180.25
Cal 1-4 deg. 180 179.75 180.25
Difference between angles 5
Cal 1-5 deg. 225 224.75 225.25
Cal 1-5 deg. 225 224.75 225.25
Difference between angles 6
Cal 1-6 deg. 270 269.75 270.25
Cal 1-6 deg. 270 269.75 270.25
Difference between angles 7
Cal 1-8 deg. 315 314.75 315.25
Cal 1-8 deg. 315 314.75 315.25
Injection quantity adjustment
Adjusting point
-
Rack position
10.1
Pump speed
r/min
650
650
650
Each cylinder's injection qty
mm3/st.
146
141.6
150.4
Basic
*
Fixing the rack
*
Standard for adjustment of the maximum variation between cylinders
*
Injection quantity adjustment_02
Adjusting point
C
Rack position
5.9+-0.5
Pump speed
r/min
225
225
225
Each cylinder's injection qty
mm3/st.
18
15.3
20.7
Fixing the rack
*
Standard for adjustment of the maximum variation between cylinders
*
Injection quantity adjustment_03
Adjusting point
A
Rack position
R1(10.1)
Pump speed
r/min
650
650
650
Average injection quantity
mm3/st.
146
145
147
Basic
*
Fixing the lever
*
Injection quantity adjustment_04
Adjusting point
B
Rack position
R1+1
Pump speed
r/min
1100
1100
1100
Average injection quantity
mm3/st.
161.5
157.5
165.5
Fixing the lever
*
Injection quantity adjustment_05
Adjusting point
E
Rack position
-
Pump speed
r/min
100
100
100
Average injection quantity
mm3/st.
185
145
225
Fixing the lever
*
Remarks
After startup boost setting
After startup boost setting
Timer adjustment
Pump speed
r/min
900--
Advance angle
deg.
0
0
0
Remarks
Start
Start
Timer adjustment_02
Pump speed
r/min
850
Advance angle
deg.
0.5
Timer adjustment_03
Pump speed
r/min
1100
Advance angle
deg.
4.5
4
5
Remarks
Finish
Finish
Test data Ex:
Governor adjustment
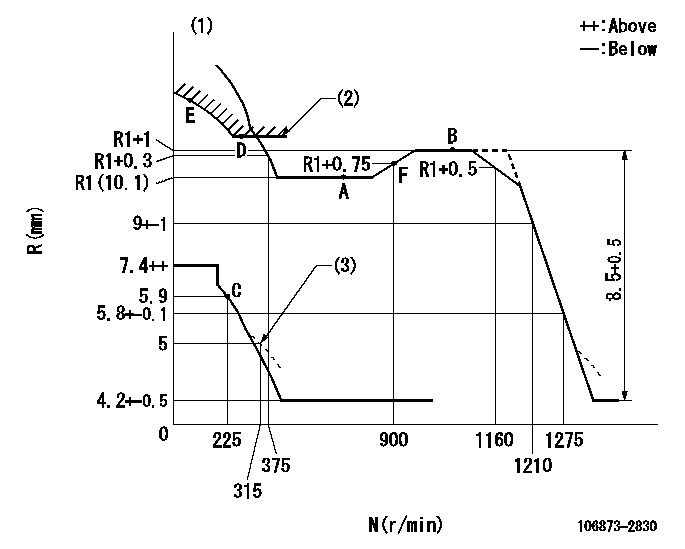
N:Pump speed
R:Rack position (mm)
(1)Tolerance for racks not indicated: +-0.05mm.
(2)Excess fuel setting for starting: SXL
(3)Damper spring setting
----------
SXL=11.5+-0.1mm
----------
----------
SXL=11.5+-0.1mm
----------
Speed control lever angle

F:Full speed
----------
----------
a=(15deg)+-5deg
----------
----------
a=(15deg)+-5deg
0000000901

F:Full load
I:Idle
(1)Stopper bolt setting
----------
----------
a=10deg+-5deg b=32deg+-3deg
----------
----------
a=10deg+-5deg b=32deg+-3deg
Stop lever angle
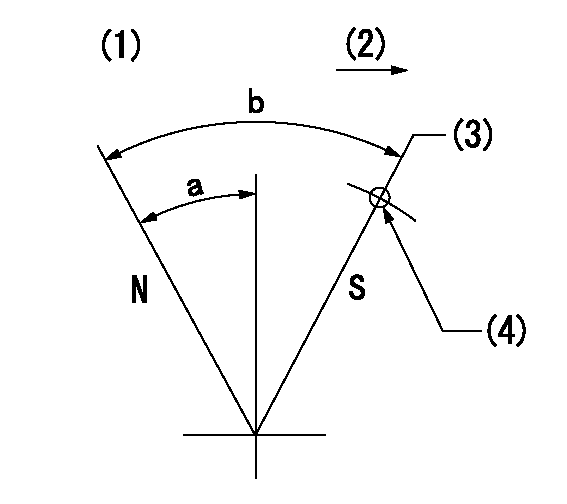
N:Pump normal
S:Stop the pump.
(1)Drive side stop lever
(2)Drive side
(3)Rack position = aa
(4)Use the hole at R = bb
----------
aa=3.7-0.5mm bb=28mm
----------
a=28.5deg+-5deg b=57deg+7deg-5deg
----------
aa=3.7-0.5mm bb=28mm
----------
a=28.5deg+-5deg b=57deg+7deg-5deg
0000001501 MICRO SWITCH
Adjustment of the micro-switch
Adjust the bolt to obtain the following lever position when the micro-switch is ON.
(1)Speed N1
(2)Rack position Ra
----------
N1=325r/min Ra=5.4+-0.1mm
----------
----------
N1=325r/min Ra=5.4+-0.1mm
----------
0000001601 GOVERNOR TORQUE CONTROL

Dr:Torque control stroke
(A): Without torque control spring capsule
1. Adjustment procedures
(1)Procedure is the same as that for the RFD (former type), except that the positive torque control stroke must be determined at the full lever setting.
2. Procedures for adjustment
(1)Remove the torque control spring capsule.
(2)Operate the pump at approximately N1. (End of idling spring operation < N1.)
(3)Tilt the lever to the full side.
(4)Set so that R = RF.
(5)Increase the speed by pushing in the screw (attached to the bracket on the rear of the tension lever) through the adjusting window.
(6)Adjust so that the torque control stroke Dr1 can be obtained.
(7)Align N2 and N3 with the torque control spring capsule.
3. Final confirmation
(1)After final confirmation, temporarily set the load lever to N = N1, R = idling position.
(2)From this condition, increase speed to N = N4.
(3)Confirm that positive torque control stroke is Dr2.
----------
N1=500r/min N2=- N3=- N4=1100r/min RF=R1(10.1)mm Dr1=1mm Dr2=0+0.3mm
----------
----------
N1=500r/min N2=- N3=- N4=1100r/min RF=R1(10.1)mm Dr1=1mm Dr2=0+0.3mm
----------
Timing setting

(1)Pump vertical direction
(2)Coupling's key groove position at No 1 cylinder's beginning of injection
(3)B.T.D.C.: aa
(4)-
----------
aa=12deg
----------
a=(40deg)
----------
aa=12deg
----------
a=(40deg)
Information:
Fuel Recommendations
Use only fuel as recommended in this section. The fuels recommended for use in Caterpillar engines are No.2-D diesel fuel and No.2-D fuel oil. No.2-D is preferred, although No.1 grades are acceptable. The following fuel specifications meet Caterpillar requirements. These fuel characteristics should be considered when procuring fuel for use in Caterpillar diesel engines. Caterpillar Diesel Engines are capable of burning a wide range of distillate fuels. The use of clean, stable blends of distillate fuel which meet the following requirements will provide quality engine service life. Filterability
Clean fuels should have no more than 0.1% of sediment and water. Storage of fuel for extended periods of time can cause fuel oxidation with solids forming, causing filtering problems. Refer to topic, Cold Weather Operation, for additional information.Sulfur
The percentage of sulfur in the fuel will affect the engine oil recommendations. Fuel sulfur is chemically changed during combustion to form both sulfurous and sulfuric acid. These acids chemically attack metal surfaces and cause corrosive wear.Certain additives used in lubricating oils contain alkaline compounds that are formulated to neutralize these acids. The measure of this reserve alkalinity in a lubricating oil is known as its Total Base Number (TBN). TBN values are essential to neutralize the acids from combustion gases and to minimize corrosive wear.Fuels containing 0.5% total weight or LESS sulfur may be used with recommended crankcase oil drain intervals using API CF-4 performance oils. With sulfur ABOVE the 0.5% level, use API CF-4 performance oils with an ASTM D2896 Total Base Number (TBN) of 10 times the fuel sulfur for DI engines and 20 times for PC engines for normal oil drain intervals. ASTM Specs can normally be found at your local technological society, library or college.Caterpillar recommends infrared analysis (in conjunction with wear metal analysis) of used oil in determining the effectiveness of oil TBN and acid neutralization. The Caterpillar dealer S O S program provides this information. Regular oil analysis (S O S) will provide information to monitor oil properties and engine wear metals to maintain successful engine protection and establish oil drain intervals.Periodically request fuel sulfur content information from your fuel supplier. Fuel sulfur content can change with each bulk delivery. American Petroleum Institute (API) classification performance oils should have sufficient TBN for fuels with less than 0.5% sulfur. Fuels containing 0.5% or less sulfur may be used with recommended crankcase oil drain intervals using API CF-4 performance oils.Additives
Fuel additives are generally not recommended nor needed for the specified fuels listed. Cetane improvers can be used as necessary for the direct injection engine requirements. Biocides may be needed to eliminate microorganism growth in storage tanks. In cold conditions, treatment for entrained water may also be necessary.Consult your fuel supplier about the use of additives to prevent incompatibility among additives already in the fuel and the additives to be used. Other fuel types may be used when economics or fuel availability dictate. Consult your Caterpillar dealer for more information and advice on any specific fuel.For more information
Use only fuel as recommended in this section. The fuels recommended for use in Caterpillar engines are No.2-D diesel fuel and No.2-D fuel oil. No.2-D is preferred, although No.1 grades are acceptable. The following fuel specifications meet Caterpillar requirements. These fuel characteristics should be considered when procuring fuel for use in Caterpillar diesel engines. Caterpillar Diesel Engines are capable of burning a wide range of distillate fuels. The use of clean, stable blends of distillate fuel which meet the following requirements will provide quality engine service life. Filterability
Clean fuels should have no more than 0.1% of sediment and water. Storage of fuel for extended periods of time can cause fuel oxidation with solids forming, causing filtering problems. Refer to topic, Cold Weather Operation, for additional information.Sulfur
The percentage of sulfur in the fuel will affect the engine oil recommendations. Fuel sulfur is chemically changed during combustion to form both sulfurous and sulfuric acid. These acids chemically attack metal surfaces and cause corrosive wear.Certain additives used in lubricating oils contain alkaline compounds that are formulated to neutralize these acids. The measure of this reserve alkalinity in a lubricating oil is known as its Total Base Number (TBN). TBN values are essential to neutralize the acids from combustion gases and to minimize corrosive wear.Fuels containing 0.5% total weight or LESS sulfur may be used with recommended crankcase oil drain intervals using API CF-4 performance oils. With sulfur ABOVE the 0.5% level, use API CF-4 performance oils with an ASTM D2896 Total Base Number (TBN) of 10 times the fuel sulfur for DI engines and 20 times for PC engines for normal oil drain intervals. ASTM Specs can normally be found at your local technological society, library or college.Caterpillar recommends infrared analysis (in conjunction with wear metal analysis) of used oil in determining the effectiveness of oil TBN and acid neutralization. The Caterpillar dealer S O S program provides this information. Regular oil analysis (S O S) will provide information to monitor oil properties and engine wear metals to maintain successful engine protection and establish oil drain intervals.Periodically request fuel sulfur content information from your fuel supplier. Fuel sulfur content can change with each bulk delivery. American Petroleum Institute (API) classification performance oils should have sufficient TBN for fuels with less than 0.5% sulfur. Fuels containing 0.5% or less sulfur may be used with recommended crankcase oil drain intervals using API CF-4 performance oils.Additives
Fuel additives are generally not recommended nor needed for the specified fuels listed. Cetane improvers can be used as necessary for the direct injection engine requirements. Biocides may be needed to eliminate microorganism growth in storage tanks. In cold conditions, treatment for entrained water may also be necessary.Consult your fuel supplier about the use of additives to prevent incompatibility among additives already in the fuel and the additives to be used. Other fuel types may be used when economics or fuel availability dictate. Consult your Caterpillar dealer for more information and advice on any specific fuel.For more information
Have questions with 106873-2830?
Group cross 106873-2830 ZEXEL
Mitsubishi
106873-2830
INJECTION-PUMP ASSEMBLY