Information injection-pump assembly
BOSCH
9 400 618 387
9400618387
ZEXEL
106873-2792
1068732792
MITSUBISHI
ME160730
me160730
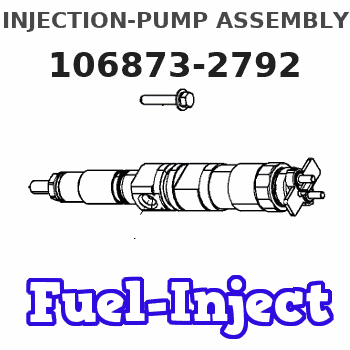
Rating:
Service parts 106873-2792 INJECTION-PUMP ASSEMBLY:
1.
_
7.
COUPLING PLATE
8.
_
9.
_
11.
Nozzle and Holder
12.
Open Pre:MPa(Kqf/cm2)
17.7{180}/24.5{250}
15.
NOZZLE SET
Include in #1:
106873-2792
as INJECTION-PUMP ASSEMBLY
Cross reference number
BOSCH
9 400 618 387
9400618387
ZEXEL
106873-2792
1068732792
MITSUBISHI
ME160730
me160730
Zexel num
Bosch num
Firm num
Name
106873-2792
9 400 618 387
ME160730 MITSUBISHI
INJECTION-PUMP ASSEMBLY
8M20-I K
8M20-I K
Calibration Data:
Adjustment conditions
Test oil
1404 Test oil ISO4113 or {SAEJ967d}
1404 Test oil ISO4113 or {SAEJ967d}
Test oil temperature
degC
40
40
45
Nozzle and nozzle holder
105780-8140
Bosch type code
EF8511/9A
Nozzle
105780-0000
Bosch type code
DN12SD12T
Nozzle holder
105780-2080
Bosch type code
EF8511/9
Opening pressure
MPa
17.2
Opening pressure
kgf/cm2
175
Injection pipe
Outer diameter - inner diameter - length (mm) mm 8-3-600
Outer diameter - inner diameter - length (mm) mm 8-3-600
Overflow valve
131424-7920
Overflow valve opening pressure
kPa
255
221
289
Overflow valve opening pressure
kgf/cm2
2.6
2.25
2.95
Tester oil delivery pressure
kPa
157
157
157
Tester oil delivery pressure
kgf/cm2
1.6
1.6
1.6
Direction of rotation (viewed from drive side)
Right R
Right R
Injection timing adjustment
Direction of rotation (viewed from drive side)
Right R
Right R
Injection order
1-2-7-3-
4-5-6-8
Pre-stroke
mm
4.4
4.37
4.43
Beginning of injection position
Governor side NO.1
Governor side NO.1
Difference between angles 1
Cyl.1-2 deg. 45 44.75 45.25
Cyl.1-2 deg. 45 44.75 45.25
Difference between angles 2
Cal 1-7 deg. 90 89.75 90.25
Cal 1-7 deg. 90 89.75 90.25
Difference between angles 3
Cal 1-3 deg. 135 134.75 135.25
Cal 1-3 deg. 135 134.75 135.25
Difference between angles 4
Cal 1-4 deg. 180 179.75 180.25
Cal 1-4 deg. 180 179.75 180.25
Difference between angles 5
Cal 1-5 deg. 225 224.75 225.25
Cal 1-5 deg. 225 224.75 225.25
Difference between angles 6
Cal 1-6 deg. 270 269.75 270.25
Cal 1-6 deg. 270 269.75 270.25
Difference between angles 7
Cal 1-8 deg. 315 314.75 315.25
Cal 1-8 deg. 315 314.75 315.25
Injection quantity adjustment
Adjusting point
-
Rack position
10.2
Pump speed
r/min
650
650
650
Each cylinder's injection qty
mm3/st.
147.5
143.1
151.9
Basic
*
Fixing the rack
*
Standard for adjustment of the maximum variation between cylinders
*
Injection quantity adjustment_02
Adjusting point
C
Rack position
6.4+-0.5
Pump speed
r/min
225
225
225
Each cylinder's injection qty
mm3/st.
18
15.3
20.7
Fixing the rack
*
Standard for adjustment of the maximum variation between cylinders
*
Injection quantity adjustment_03
Adjusting point
A
Rack position
R1(10.2)
Pump speed
r/min
650
650
650
Average injection quantity
mm3/st.
147.5
146.5
148.5
Basic
*
Fixing the lever
*
Injection quantity adjustment_04
Adjusting point
B
Rack position
R1+0.9
Pump speed
r/min
1100
1100
1100
Average injection quantity
mm3/st.
164.5
160.5
168.5
Fixing the lever
*
Injection quantity adjustment_05
Adjusting point
E
Rack position
-
Pump speed
r/min
100
100
100
Average injection quantity
mm3/st.
180
160
200
Fixing the lever
*
Remarks
After startup boost setting
After startup boost setting
Test data Ex:
Governor adjustment
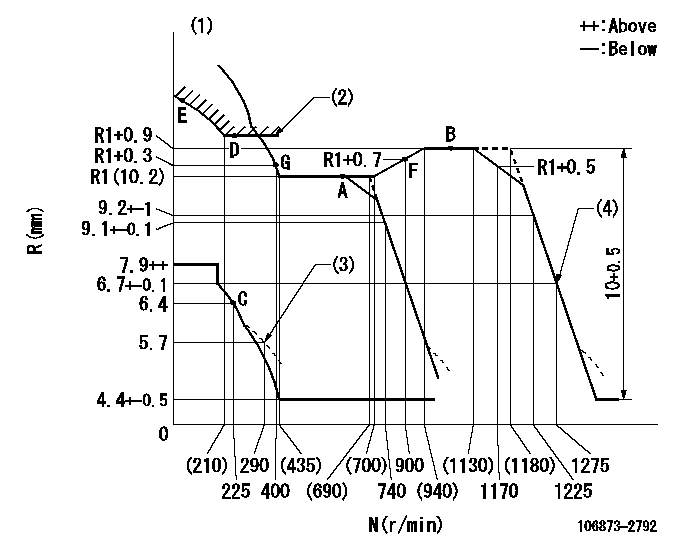
N:Pump speed
R:Rack position (mm)
(1)Tolerance for racks not indicated: +-0.05mm.
(2)Excess fuel setting for starting: SXL
(3)Damper spring setting
(4)When air cylinder is operating.
----------
SXL=11.3+-0.1mm
----------
----------
SXL=11.3+-0.1mm
----------
Timer adjustment

(1)Adjusting range
(2)Step response time
(N): Speed of the pump
(L): Load
(theta) Advance angle
(Srd1) Step response time 1
(Srd2) Step response time 2
1. Adjusting conditions for the variable timer
(1)Adjust the clearance between the pickup and the protrusion to L.
----------
L=1-0.2mm N2=800r/min C2=(8.8)deg t1=2.5--sec. t2=2.5--sec.
----------
N1=750++r/min P1=0kPa(0kgf/cm2) P2=392kPa(4kgf/cm2) C1=8.8+-0.3deg R01=0/4load R02=4/4load
----------
L=1-0.2mm N2=800r/min C2=(8.8)deg t1=2.5--sec. t2=2.5--sec.
----------
N1=750++r/min P1=0kPa(0kgf/cm2) P2=392kPa(4kgf/cm2) C1=8.8+-0.3deg R01=0/4load R02=4/4load
Speed control lever angle
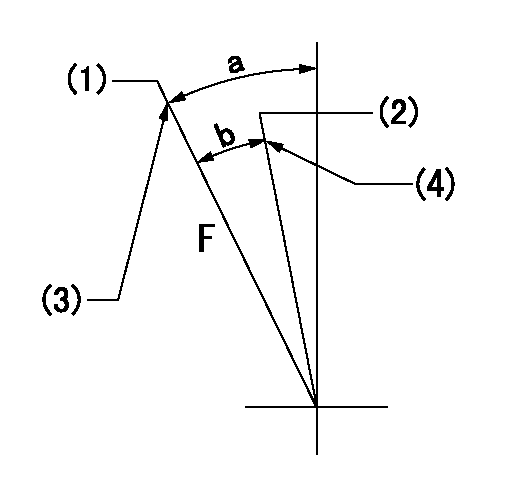
F:Full speed
(1)Set the pump speed at aa
(2)Set the pump speed at bb.
(3)Stopper bolt setting
(4)Stopper bolt setting
----------
aa=1275r/min bb=740r/min
----------
a=19.5deg+-5deg b=(8deg)+-5deg
----------
aa=1275r/min bb=740r/min
----------
a=19.5deg+-5deg b=(8deg)+-5deg
0000000901

F:Full load
I:Idle
(1)Stopper bolt setting
----------
----------
a=10deg+-5deg b=21.5deg+-3deg
----------
----------
a=10deg+-5deg b=21.5deg+-3deg
Stop lever angle
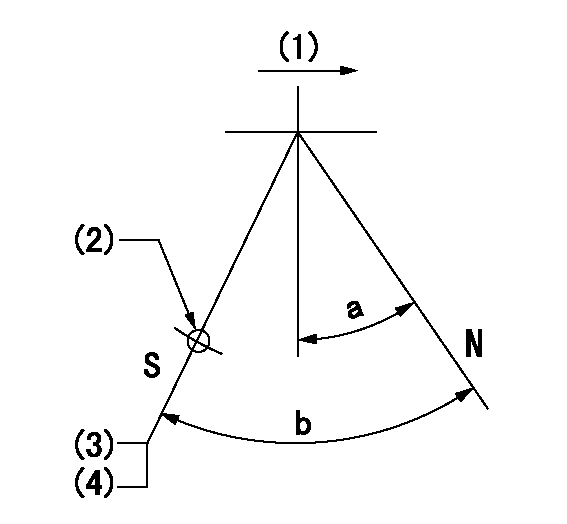
N:Pump normal
S:Stop the pump.
(1)Drive side
(2)Use the hole at R = aa
(3)Rack position bb
(4)Stopper bolt setting
----------
aa=36mm bb=3.7-0.5mm
----------
a=10.5deg+-5deg b=57deg+7deg-5deg
----------
aa=36mm bb=3.7-0.5mm
----------
a=10.5deg+-5deg b=57deg+7deg-5deg
0000001501 GOVERNOR TORQUE CONTROL

Dr:Torque control stroke
(A): Without torque control spring capsule
1. Adjustment procedures
(1)Procedure is the same as that for the RFD (former type), except that the positive torque control stroke must be determined at the full lever setting.
2. Procedures for adjustment
(1)Remove the torque control spring capsule.
(2)Operate the pump at approximately N1. (End of idling spring operation < N1.)
(3)Tilt the lever to the full side.
(4)Set so that R = RF.
(5)Increase the speed by pushing in the screw (attached to the bracket on the rear of the tension lever) through the adjusting window.
(6)Adjust so that the torque control stroke Dr1 can be obtained.
(7)Align N2 and N3 with the torque control spring capsule.
3. Final confirmation
(1)After final confirmation, temporarily set the load lever to N = N1, R = idling position.
(2)From this condition, increase speed to N = N4.
(3)Confirm that positive torque control stroke is Dr2.
----------
N1=500r/min N2=(700)r/min N3=(940)r/min N4=1100r/min RF=R1(10.2)mm Dr1=0.9mm Dr2=0+0.3mm
----------
----------
N1=500r/min N2=(700)r/min N3=(940)r/min N4=1100r/min RF=R1(10.2)mm Dr1=0.9mm Dr2=0+0.3mm
----------
0000001601 MICRO SWITCH
Adjustment of the micro-switch
Adjust the bolt to obtain the following lever position when the micro-switch is ON.
(1)Speed N1
(2)Rack position Ra
----------
N1=325r/min Ra=5.9+-0.1mm
----------
----------
N1=325r/min Ra=5.9+-0.1mm
----------
0000001701 RACK SENSOR

V1:Supply voltage
V2f:Full side output voltage
V2i:Idle side output voltage
(A) Black
(B) Yellow
(C) Red
(D) Trimmer
(E): Shaft
(F) Nut
(G) Load lever
1. Load sensor adjustment
(1)Connect as shown in the above diagram and apply supply voltage V1.
(2)Hold the load lever (G) against the full side.
(3)Turn the shaft so that the voltage between (A) and (B) is V2.
(4)Hold the load lever (G) against the idle side.
(5)Adjust (D) so that the voltage between (A) and (B) is V2i.
(6)Repeat the above adjustments.
(7)Tighten the nut (F) at the point satisfying the standards.
(8)Hold the load lever against the full side stopper and the idle side stopper.
(9)At this time, confirm that the full side output voltage is V2f and the idle side output voltage is V2i.
----------
V1=5+-0.02V V2f=0.15+0.03V V2i=2.35-0.03V
----------
----------
V1=5+-0.02V V2f=0.15+0.03V V2i=2.35-0.03V
----------
0000001801 LEVER
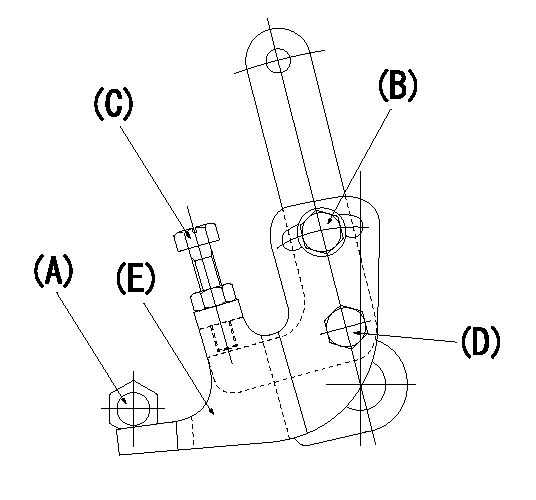
(A) Stopper
(B) bolt
Bolt c
(D) Bolt
(E) Lever
Speed lever angle and speed lever setting procedure
(1)Set the speed lever so that speed N = N1.
(2)With the lever (E) contacting the stopper (A), fully tighten bolts (B) and (D).
(3)Screw in bolt (C) and lock.
(4)Set the speed lever at the full position so that N = N2.
----------
N1=740r/min N2=1275r/min
----------
----------
N1=740r/min N2=1275r/min
----------
Timing setting

(1)Pump vertical direction
(2)Coupling's key groove position at No 1 cylinder's beginning of injection
(3)B.T.D.C.: aa
(4)-
----------
aa=10deg
----------
a=(40deg)
----------
aa=10deg
----------
a=(40deg)
Information:
Rating Definitions
The Caterpillar marine propulsion engine rating definitions are:* A - Continuous Duty-For heavy duty use with little load cycling (throttle operation up to 100 percent of total time) in oceangoing displacement hulls such as freighters, tugboats and bottom-drag trawlers, and deep river towboats. Expected usage is 4000 hours per year or more.* B - Medium Duty-For use with full throttle operation up to 80 percent of total operation time with the balance of time below rated rpm in midwater trawlers, purse seiners, crew and supply boats, ferry boats with trips longer than one hour, and towboats in rivers where locks, sandbars, curves or traffic dictate frequent slowing. Expected usage is 4000 hours per year, average, is typical, but could be higher.* C - Intermittent Duty-For use with full throttle operation up to 50 percent of total operation time with the balance of time below rated rpm in yachts with displacement hulls, as well as ferries with trips less than one hour, fish boats moving at higher speeds out and back (e.g., lobster, crayfish and tuna), and short trip coastal freighters where engine load and speed are cyclical. Expected usage of up to 3000 hours per year, average, is typical.* D - Patrol Craft-For use in patrol, customs, police and some fire boats. Also for bow/stern thrusters. Full throttle operation up to ten percent of total operation time with balance of time below rated rpm. Expected usage is less than 2000 hours per year.* E - High Performance-For use in pleasure craft with planing hulls, as well as for pilot, harbor patrol and harbor master boats with full throttle operation up to five percent of total operation time with balance of time below rated rpm. Expected usage is 200 to 300 hours per year. Some fish boats operate on duty cycles where D or E engine ratings apply.Time at full throttle is the cumulative time the engine is operated at full throttle load and speed during a work cycle, duty cycle, or voyage.These rating definitions dictate the selection of a rating for an application based on a load profile determined by time at various throttle settings or engine speeds. In general, an application requiring less time at full throttle, or lower engine rpm at reduced throttle operation, can utilize a higher rating.Application Guidelines
In selecting a rating for a specific application, the most important consideration is time spent at full throttle. Additionally, these rating definitions identify percent of time at full throttle and corresponding times below rated rpm. This rpm reduction lowers kW (horsepower) requirements as propeller demand follows a cubic speed/power curve.For example, an engine operating at 90 percent of rated speed would be loaded by a typical propeller to about 73 percent of rated power. Operating at recommended reduced speed controls the engine load at or below the continuous power level.As a general guideline, typical operating parameters for each rating level are summarized in the following chart. For more information, refer to your Caterpillar dealer and EDS
The Caterpillar marine propulsion engine rating definitions are:* A - Continuous Duty-For heavy duty use with little load cycling (throttle operation up to 100 percent of total time) in oceangoing displacement hulls such as freighters, tugboats and bottom-drag trawlers, and deep river towboats. Expected usage is 4000 hours per year or more.* B - Medium Duty-For use with full throttle operation up to 80 percent of total operation time with the balance of time below rated rpm in midwater trawlers, purse seiners, crew and supply boats, ferry boats with trips longer than one hour, and towboats in rivers where locks, sandbars, curves or traffic dictate frequent slowing. Expected usage is 4000 hours per year, average, is typical, but could be higher.* C - Intermittent Duty-For use with full throttle operation up to 50 percent of total operation time with the balance of time below rated rpm in yachts with displacement hulls, as well as ferries with trips less than one hour, fish boats moving at higher speeds out and back (e.g., lobster, crayfish and tuna), and short trip coastal freighters where engine load and speed are cyclical. Expected usage of up to 3000 hours per year, average, is typical.* D - Patrol Craft-For use in patrol, customs, police and some fire boats. Also for bow/stern thrusters. Full throttle operation up to ten percent of total operation time with balance of time below rated rpm. Expected usage is less than 2000 hours per year.* E - High Performance-For use in pleasure craft with planing hulls, as well as for pilot, harbor patrol and harbor master boats with full throttle operation up to five percent of total operation time with balance of time below rated rpm. Expected usage is 200 to 300 hours per year. Some fish boats operate on duty cycles where D or E engine ratings apply.Time at full throttle is the cumulative time the engine is operated at full throttle load and speed during a work cycle, duty cycle, or voyage.These rating definitions dictate the selection of a rating for an application based on a load profile determined by time at various throttle settings or engine speeds. In general, an application requiring less time at full throttle, or lower engine rpm at reduced throttle operation, can utilize a higher rating.Application Guidelines
In selecting a rating for a specific application, the most important consideration is time spent at full throttle. Additionally, these rating definitions identify percent of time at full throttle and corresponding times below rated rpm. This rpm reduction lowers kW (horsepower) requirements as propeller demand follows a cubic speed/power curve.For example, an engine operating at 90 percent of rated speed would be loaded by a typical propeller to about 73 percent of rated power. Operating at recommended reduced speed controls the engine load at or below the continuous power level.As a general guideline, typical operating parameters for each rating level are summarized in the following chart. For more information, refer to your Caterpillar dealer and EDS
Have questions with 106873-2792?
Group cross 106873-2792 ZEXEL
Mitsubishi
Mitsubishi
Mitsubishi
Mitsubishi
Mitsubishi
Mitsubishi
106873-2792
9 400 618 387
ME160730
INJECTION-PUMP ASSEMBLY
8M20-I
8M20-I