Information injection-pump assembly
BOSCH
9 400 618 380
9400618380
ZEXEL
106873-2721
1068732721
MITSUBISHI
ME160609
me160609
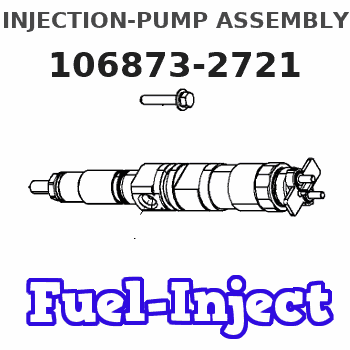
Rating:
Service parts 106873-2721 INJECTION-PUMP ASSEMBLY:
1.
_
7.
COUPLING PLATE
8.
_
9.
_
11.
Nozzle and Holder
12.
Open Pre:MPa(Kqf/cm2)
17.7{180}/24.5{250}
15.
NOZZLE SET
Include in #1:
106873-2721
as INJECTION-PUMP ASSEMBLY
Cross reference number
BOSCH
9 400 618 380
9400618380
ZEXEL
106873-2721
1068732721
MITSUBISHI
ME160609
me160609
Zexel num
Bosch num
Firm num
Name
Calibration Data:
Adjustment conditions
Test oil
1404 Test oil ISO4113 or {SAEJ967d}
1404 Test oil ISO4113 or {SAEJ967d}
Test oil temperature
degC
40
40
45
Nozzle and nozzle holder
105780-8140
Bosch type code
EF8511/9A
Nozzle
105780-0000
Bosch type code
DN12SD12T
Nozzle holder
105780-2080
Bosch type code
EF8511/9
Opening pressure
MPa
17.2
Opening pressure
kgf/cm2
175
Injection pipe
Outer diameter - inner diameter - length (mm) mm 8-3-600
Outer diameter - inner diameter - length (mm) mm 8-3-600
Overflow valve
131424-4620
Overflow valve opening pressure
kPa
255
221
289
Overflow valve opening pressure
kgf/cm2
2.6
2.25
2.95
Tester oil delivery pressure
kPa
157
157
157
Tester oil delivery pressure
kgf/cm2
1.6
1.6
1.6
Direction of rotation (viewed from drive side)
Right R
Right R
Injection timing adjustment
Direction of rotation (viewed from drive side)
Right R
Right R
Injection order
1-2-7-3-
4-5-6-8
Pre-stroke
mm
4.8
4.75
4.85
Beginning of injection position
Governor side NO.1
Governor side NO.1
Difference between angles 1
Cyl.1-2 deg. 45 44.5 45.5
Cyl.1-2 deg. 45 44.5 45.5
Difference between angles 2
Cal 1-7 deg. 90 89.5 90.5
Cal 1-7 deg. 90 89.5 90.5
Difference between angles 3
Cal 1-3 deg. 135 134.5 135.5
Cal 1-3 deg. 135 134.5 135.5
Difference between angles 4
Cal 1-4 deg. 180 179.5 180.5
Cal 1-4 deg. 180 179.5 180.5
Difference between angles 5
Cal 1-5 deg. 225 224.5 225.5
Cal 1-5 deg. 225 224.5 225.5
Difference between angles 6
Cal 1-6 deg. 270 269.5 270.5
Cal 1-6 deg. 270 269.5 270.5
Difference between angles 7
Cal 1-8 deg. 315 314.5 315.5
Cal 1-8 deg. 315 314.5 315.5
Injection quantity adjustment
Adjusting point
-
Rack position
10.4
Pump speed
r/min
650
650
650
Each cylinder's injection qty
mm3/st.
140
135.8
144.2
Basic
*
Fixing the rack
*
Standard for adjustment of the maximum variation between cylinders
*
Injection quantity adjustment_02
Adjusting point
C
Rack position
6.8+-0.5
Pump speed
r/min
225
225
225
Each cylinder's injection qty
mm3/st.
19
16.1
21.9
Fixing the rack
*
Standard for adjustment of the maximum variation between cylinders
*
Injection quantity adjustment_03
Adjusting point
A
Rack position
R1(10.4)
Pump speed
r/min
650
650
650
Average injection quantity
mm3/st.
140
139
141
Basic
*
Fixing the lever
*
Injection quantity adjustment_04
Adjusting point
E
Rack position
-
Pump speed
r/min
100
100
100
Average injection quantity
mm3/st.
155
115
195
Fixing the lever
*
Remarks
After startup boost setting
After startup boost setting
Test data Ex:
Governor adjustment
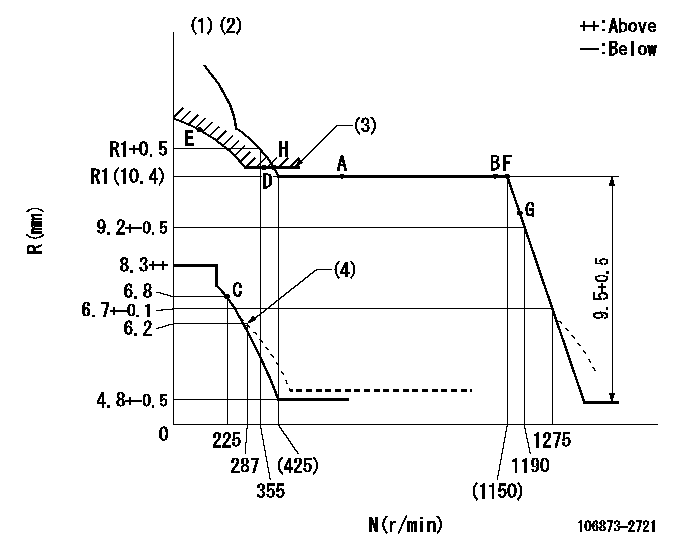
N:Pump speed
R:Rack position (mm)
(1)Tolerance for racks not indicated: +-0.05mm.
(2)Supplied with torque spring not set.
(3)Excess fuel setting for starting: SXL
(4)Damper spring setting
----------
SXL=10.6+-0.1mm
----------
----------
SXL=10.6+-0.1mm
----------
Timer adjustment

(1)Adjusting range
(2)Step response time
(N): Speed of the pump
(L): Load
(theta) Advance angle
(Srd1) Step response time 1
(Srd2) Step response time 2
1. Adjusting conditions for the variable timer
(1)Adjust the clearance between the pickup and the protrusion to L.
----------
L=1-0.2mm N2=800r/min C2=(8.8)deg t1=2.5--sec. t2=2.5--sec.
----------
N1=750++r/min P1=0kPa(0kgf/cm2) P2=392kPa(4kgf/cm2) C1=8.8+-0.3deg R01=0/4load R02=4/4load
----------
L=1-0.2mm N2=800r/min C2=(8.8)deg t1=2.5--sec. t2=2.5--sec.
----------
N1=750++r/min P1=0kPa(0kgf/cm2) P2=392kPa(4kgf/cm2) C1=8.8+-0.3deg R01=0/4load R02=4/4load
Speed control lever angle

F:Full speed
----------
----------
a=(22deg)+-5deg
----------
----------
a=(22deg)+-5deg
0000000901

F:Full load
I:Idle
(1)Stopper bolt setting
----------
----------
a=10deg+-5deg b=21deg+-3deg
----------
----------
a=10deg+-5deg b=21deg+-3deg
Stop lever angle
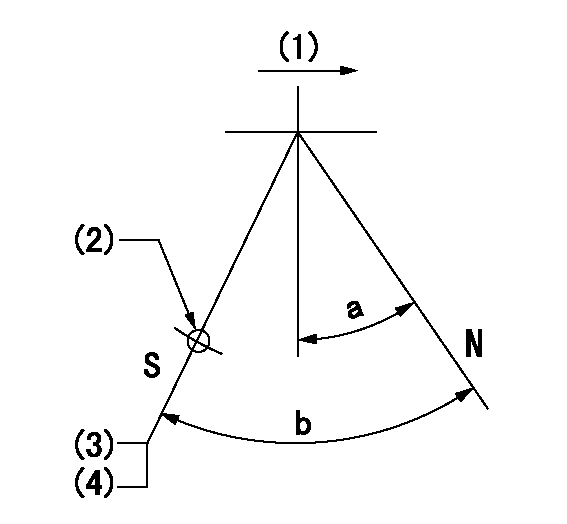
N:Pump normal
S:Stop the pump.
(1)Drive side
(2)Use the hole at R = aa
(3)Rack position bb
(4)Stopper bolt setting
----------
aa=36mm bb=4.3-0.5mm
----------
a=10.5deg+-5deg b=55deg+7deg-5deg
----------
aa=36mm bb=4.3-0.5mm
----------
a=10.5deg+-5deg b=55deg+7deg-5deg
0000001501 MICRO SWITCH
Adjustment of the micro-switch
Adjust the bolt to obtain the following lever position when the micro-switch is ON.
(1)Speed N1
(2)Rack position Ra
----------
N1=325r/min Ra=6.3+-0.1mm
----------
----------
N1=325r/min Ra=6.3+-0.1mm
----------
0000001601 RACK SENSOR

V1:Supply voltage
V2f:Full side output voltage
V2i:Idle side output voltage
(A) Black
(B) Yellow
(C) Red
(D) Trimmer
(E): Shaft
(F) Nut
(G) Load lever
1. Load sensor adjustment
(1)Connect as shown in the above diagram and apply supply voltage V1.
(2)Hold the load lever (G) against the full side.
(3)Turn the shaft so that the voltage between (A) and (B) is V2.
(4)Hold the load lever (G) against the idle side.
(5)Adjust (D) so that the voltage between (A) and (B) is V2i.
(6)Repeat the above adjustments.
(7)Tighten the nut (F) at the point satisfying the standards.
(8)Hold the load lever against the full side stopper and the idle side stopper.
(9)At this time, confirm that the full side output voltage is V2f and the idle side output voltage is V2i.
----------
V1=5+-0.02V V2f=0.15+0.03V V2i=2.35-0.03V
----------
----------
V1=5+-0.02V V2f=0.15+0.03V V2i=2.35-0.03V
----------
Timing setting

(1)Pump vertical direction
(2)Coupling's key groove position at No 1 cylinder's beginning of injection
(3)B.T.D.C.: aa
(4)-
----------
aa=12deg
----------
a=(40deg)
----------
aa=12deg
----------
a=(40deg)
Information:
The combustion process of a diesel engine produces exhaust products such as smoke (visible), hydrocarbons and oxides of nitrogen (invisible). The dark smoke emitted by a diesel engine is soot or carbon particles and even in low concentration make the diesel exhaust highly visible and offensive to most people. Every effort must be made to eliminate smoke even though it can be considered more of a nuisance than a pollutant.Under certain conditions oxides of nitrogen react with certain hydrocarbons to form smog which can become irritating and toxic if large concentrations accumulate. Concentrations of this pollutant combined with pollution of other sources all contribute to the total air quality problem.As an engine manufacturer, our goal is to see that environmental standards are met with a minimum additional complexity or cost to the product. Throughout the years, continuing research and design improvements have been directed at minimizing exhaust emissions. Caterpillar has incorporated items such as -TURBOCHARGING: Reduces exhaust noise and provides more air per cylinder allowing the fuel to burn more efficiently. These engines are integrally designed for turbocharging.AIR-FUEL RATIO CONTROL FOR TURBOCHARGED ENGINES: Limits the amount of fuel during acceleration to minimize smoke levels.RECOMMEND FUELS, LUBRICATING OILS AND MAINTENANCE SCHEDULES: To assure minimum exhaust emissions.Maintenance Recommendations
Caterpillar Truck Engines are certified by the United States Environmental Protection Agency to comply with smoke emission standard limits prescribed by Federal laws at the time of manufacture.Efficiency of emission control and good engine performance depend on adherence to proper operation and maintenance recommendations, use of recommended fuels and lubricating oils. It is recommended that major adjustments and repair be entrusted to your authorized dealer.Various chemical fuel additives are commercially available that claim to reduce visible smoke. Although additives have been used by individuals to solve some isolated smoke problems in the field, they are not recommended for general use. Federal smoke regulations require the certification of engines without a smoke depressant.The corrective steps taken immediately on discovery of worn parts, which may affect emission levels, will help assure proper operation of emission control systems. The use of genuine Caterpillar parts is recommended. Suppliers of non-Caterpillar parts must assure the user that the use of such parts will not adversely affect emission levels.Regular service intervals along with special emphasis on the following items are necessary to keep exhaust emissions within acceptable limits for the useful life of the engine. Refer to the Lubrication and Maintenance Section of this Operation Guide for details and maintenance schedule. If the engine is operating under severe conditions, adjust maintenance schedule accordingly. See your authorized dealer to help analyze your specific maintenance schedule.The following explanation of required emission related component maintenance has been keyed by number to correspond with item number in the maintenance chart.1. COOLANT - LEVEL AND PROTECTION: Check the engine coolant level daily with the engine stopped and cool. Release cooling system pressure before checking. Fill to proper level with permanent-type antifreeze and water as free as possible from scale forming minerals. DO NOT USE
Caterpillar Truck Engines are certified by the United States Environmental Protection Agency to comply with smoke emission standard limits prescribed by Federal laws at the time of manufacture.Efficiency of emission control and good engine performance depend on adherence to proper operation and maintenance recommendations, use of recommended fuels and lubricating oils. It is recommended that major adjustments and repair be entrusted to your authorized dealer.Various chemical fuel additives are commercially available that claim to reduce visible smoke. Although additives have been used by individuals to solve some isolated smoke problems in the field, they are not recommended for general use. Federal smoke regulations require the certification of engines without a smoke depressant.The corrective steps taken immediately on discovery of worn parts, which may affect emission levels, will help assure proper operation of emission control systems. The use of genuine Caterpillar parts is recommended. Suppliers of non-Caterpillar parts must assure the user that the use of such parts will not adversely affect emission levels.Regular service intervals along with special emphasis on the following items are necessary to keep exhaust emissions within acceptable limits for the useful life of the engine. Refer to the Lubrication and Maintenance Section of this Operation Guide for details and maintenance schedule. If the engine is operating under severe conditions, adjust maintenance schedule accordingly. See your authorized dealer to help analyze your specific maintenance schedule.The following explanation of required emission related component maintenance has been keyed by number to correspond with item number in the maintenance chart.1. COOLANT - LEVEL AND PROTECTION: Check the engine coolant level daily with the engine stopped and cool. Release cooling system pressure before checking. Fill to proper level with permanent-type antifreeze and water as free as possible from scale forming minerals. DO NOT USE