Information injection-pump assembly
ZEXEL
106873-2671
1068732671
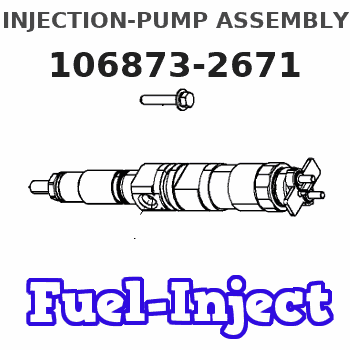
Rating:
Service parts 106873-2671 INJECTION-PUMP ASSEMBLY:
1.
_
7.
COUPLING PLATE
8.
_
9.
_
11.
Nozzle and Holder
ME160666
12.
Open Pre:MPa(Kqf/cm2)
17.7{180}/24.5{250}
15.
NOZZLE SET
Include in #1:
106873-2671
as INJECTION-PUMP ASSEMBLY
Cross reference number
ZEXEL
106873-2671
1068732671
Zexel num
Bosch num
Firm num
Name
106873-2671
INJECTION-PUMP ASSEMBLY
Calibration Data:
Adjustment conditions
Test oil
1404 Test oil ISO4113 or {SAEJ967d}
1404 Test oil ISO4113 or {SAEJ967d}
Test oil temperature
degC
40
40
45
Nozzle and nozzle holder
105780-8140
Bosch type code
EF8511/9A
Nozzle
105780-0000
Bosch type code
DN12SD12T
Nozzle holder
105780-2080
Bosch type code
EF8511/9
Opening pressure
MPa
17.2
Opening pressure
kgf/cm2
175
Injection pipe
Outer diameter - inner diameter - length (mm) mm 8-3-600
Outer diameter - inner diameter - length (mm) mm 8-3-600
Overflow valve
131424-7920
Overflow valve opening pressure
kPa
255
221
289
Overflow valve opening pressure
kgf/cm2
2.6
2.25
2.95
Tester oil delivery pressure
kPa
157
157
157
Tester oil delivery pressure
kgf/cm2
1.6
1.6
1.6
Direction of rotation (viewed from drive side)
Right R
Right R
Injection timing adjustment
Direction of rotation (viewed from drive side)
Right R
Right R
Injection order
1-2-7-3-
4-5-6-8
Pre-stroke
mm
4.4
4.37
4.43
Beginning of injection position
Governor side NO.1
Governor side NO.1
Difference between angles 1
Cyl.1-2 deg. 45 44.75 45.25
Cyl.1-2 deg. 45 44.75 45.25
Difference between angles 2
Cal 1-7 deg. 90 89.75 90.25
Cal 1-7 deg. 90 89.75 90.25
Difference between angles 3
Cal 1-3 deg. 135 134.75 135.25
Cal 1-3 deg. 135 134.75 135.25
Difference between angles 4
Cal 1-4 deg. 180 179.75 180.25
Cal 1-4 deg. 180 179.75 180.25
Difference between angles 5
Cal 1-5 deg. 225 224.75 225.25
Cal 1-5 deg. 225 224.75 225.25
Difference between angles 6
Cal 1-6 deg. 270 269.75 270.25
Cal 1-6 deg. 270 269.75 270.25
Difference between angles 7
Cal 1-8 deg. 315 314.75 315.25
Cal 1-8 deg. 315 314.75 315.25
Injection quantity adjustment
Adjusting point
-
Rack position
10.1
Pump speed
r/min
650
650
650
Each cylinder's injection qty
mm3/st.
146
141.6
150.4
Basic
*
Fixing the rack
*
Standard for adjustment of the maximum variation between cylinders
*
Injection quantity adjustment_02
Adjusting point
C
Rack position
5.9+-0.5
Pump speed
r/min
225
225
225
Each cylinder's injection qty
mm3/st.
18
15.3
20.7
Fixing the rack
*
Standard for adjustment of the maximum variation between cylinders
*
Injection quantity adjustment_03
Adjusting point
A
Rack position
R1(10.1)
Pump speed
r/min
650
650
650
Average injection quantity
mm3/st.
146
145
147
Basic
*
Fixing the lever
*
Injection quantity adjustment_04
Adjusting point
B
Rack position
R1+1
Pump speed
r/min
1100
1100
1100
Average injection quantity
mm3/st.
161.5
157.5
165.5
Fixing the lever
*
Injection quantity adjustment_05
Adjusting point
E
Rack position
-
Pump speed
r/min
100
100
100
Average injection quantity
mm3/st.
175
155
195
Fixing the lever
*
Remarks
After startup boost setting
After startup boost setting
Timer adjustment
Pump speed
r/min
900--
Advance angle
deg.
0
0
0
Remarks
Start
Start
Timer adjustment_02
Pump speed
r/min
850
Advance angle
deg.
0.5
Timer adjustment_03
Pump speed
r/min
1100
Advance angle
deg.
4.5
4
5
Remarks
Finish
Finish
Test data Ex:
Governor adjustment
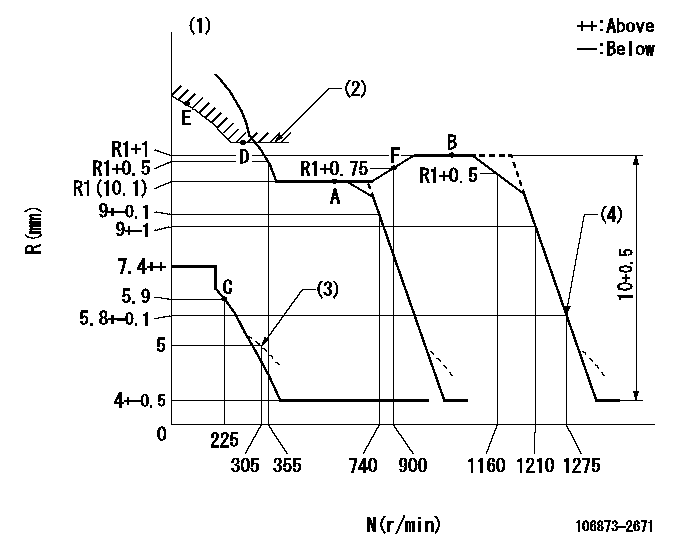
N:Pump speed
R:Rack position (mm)
(1)Tolerance for racks not indicated: +-0.05mm.
(2)Excess fuel setting for starting: SXL
(3)Damper spring setting
(4)When air cylinder is operating.
----------
SXL=11.3+-0.1mm
----------
----------
SXL=11.3+-0.1mm
----------
Speed control lever angle
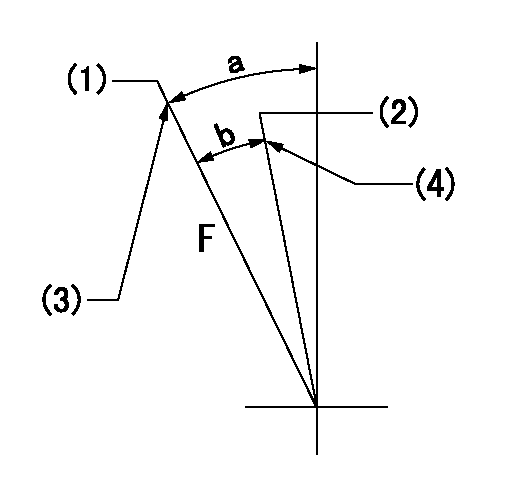
F:Full speed
(1)Set the pump speed at aa
(2)Set the pump speed at bb.
(3)Stopper bolt setting
(4)Stopper bolt setting
----------
aa=1275r/min bb=740r/min
----------
a=19deg+-5deg b=(8deg)+-5deg
----------
aa=1275r/min bb=740r/min
----------
a=19deg+-5deg b=(8deg)+-5deg
0000000901

F:Full load
I:Idle
(1)Stopper bolt setting
----------
----------
a=10deg+-5deg b=22.5deg+-3deg
----------
----------
a=10deg+-5deg b=22.5deg+-3deg
Stop lever angle
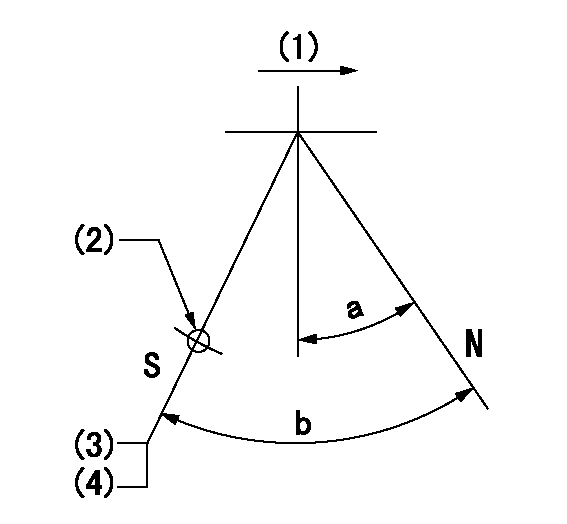
N:Pump normal
S:Stop the pump.
(1)Drive side
(2)Use the hole at R = aa
(3)Rack position bb
(4)Stopper bolt setting
----------
aa=36mm bb=3.7-0.5mm
----------
a=10.5deg+-5deg b=57deg+7deg-5deg
----------
aa=36mm bb=3.7-0.5mm
----------
a=10.5deg+-5deg b=57deg+7deg-5deg
0000001501 MICRO SWITCH
Adjustment of the micro-switch
Adjust the bolt to obtain the following lever position when the micro-switch is ON.
(1)Speed N1
(2)Rack position Ra
----------
N1=325r/min Ra=5.4+-0.1mm
----------
----------
N1=325r/min Ra=5.4+-0.1mm
----------
0000001601 GOVERNOR TORQUE CONTROL

Dr:Torque control stroke
(A): Without torque control spring capsule
1. Adjustment procedures
(1)Procedure is the same as that for the RFD (former type), except that the positive torque control stroke must be determined at the full lever setting.
2. Procedures for adjustment
(1)Remove the torque control spring capsule.
(2)Operate the pump at approximately N1. (End of idling spring operation < N1.)
(3)Tilt the lever to the full side.
(4)Set so that R = RF.
(5)Increase the speed by pushing in the screw (attached to the bracket on the rear of the tension lever) through the adjusting window.
(6)Adjust so that the torque control stroke Dr1 can be obtained.
(7)Align N2 and N3 with the torque control spring capsule.
3. Final confirmation
(1)After final confirmation, temporarily set the load lever to N = N1, R = idling position.
(2)From this condition, increase speed to N = N4.
(3)Confirm that positive torque control stroke is Dr2.
----------
N1=500r/min N2=- N3=- N4=1100r/min RF=10.1mm Dr1=1mm Dr2=0+0.3mm
----------
----------
N1=500r/min N2=- N3=- N4=1100r/min RF=10.1mm Dr1=1mm Dr2=0+0.3mm
----------
Timing setting

(1)Pump vertical direction
(2)Coupling's key groove position at No 1 cylinder's beginning of injection
(3)B.T.D.C.: aa
(4)-
----------
aa=12deg
----------
a=(40deg)
----------
aa=12deg
----------
a=(40deg)
Information:
When the preset temperature, pressure or fluid level occurs, either a light or an audible alarm will be energized. The light or alarm will continue to operate until the condition is corrected. When the condition is corrected the alarm will automatically reset and the light will turn off.
The cause of the shutdown must be investigated and corrected before starting and operating the engine.
Testing Indicator Lights
Most control panels are equipped with a test switch. By turning the switch ON, all of the indicator lights can be checked for proper operation. Test the indicator lights periodically, replace burned out light bulbs immediately.Alarm Shutoff Switch
A switch may be installed in the alarm circuit for silencing the alarm while the engine is stopped for repairs. Be sure the switch is moved to the closed (ON) position and the warning lights are lit before starting.
Place switch in the closed (ON) position when the engine is started, so the engine will be protected.
Output Shaft Governor Operation
When the load can overspeed the torque converter output shaft, an output shaft governor should be installed. The output shaft governor is a speed limiting device which automatically adjusts engine governor setting according to load requirement.Determining Cause Of Shutdown
If the engine has been shutdown by a safety device, do not start the engine and place it into service without having the cause of the shutdown investigated and corrected.
Low Oil Pressure Checks
If the low oil pressure shutoff control has stopped the engine, make the following checks: 1. Check the water temperature gauge. Determine if the engine was overheated. Check for external water leaks.
Beware of steam or scalding water. Do not attempt to loosen the radiator cap until the temperature gauge indicates the coolant has sufficiently cooled. Then, loosen the cap slowly.
2. Check the oil level. Oil level must be between the ADD and FULL marks on the side of the dipstick stamped CHECK WITH ENGINE STOPPED.3. If the oil level is below the ADD mark, check for oil spray and/or oil accumulations. If any are found, have the necessary repairs made. Before starting, add oil to the FULL mark.4. Reset the shutoff control.5. Remove the load and start the engine at its slowest speed. Be prepared to shut the engine down manually.6. Be alert for unusual sounds or noises. If the engine knocks, stop the engine immediately and call your Caterpillar dealer.7. If the engine blows excessive black exhaust or has excessive crankcase blow-by, the engine may need reconditioning. Stop the engine and call your Caterpillar dealer.8. If the engine runs satisfactorily, observe the oil pressure gauge. If satisfactory pressure is not indicated, shut the engine down; call your Caterpillar dealer.9. If proper oil pressure is registered, check to see if the reset knob has moved to the run position. If the knob does not move, stop the engine. Check the shutoff control, the oil line, and the oil pressure gauge. Have necessary repairs made.10. If the oil pressure gauge registers normal oil pressure, if the knob on the shutoff
The cause of the shutdown must be investigated and corrected before starting and operating the engine.
Testing Indicator Lights
Most control panels are equipped with a test switch. By turning the switch ON, all of the indicator lights can be checked for proper operation. Test the indicator lights periodically, replace burned out light bulbs immediately.Alarm Shutoff Switch
A switch may be installed in the alarm circuit for silencing the alarm while the engine is stopped for repairs. Be sure the switch is moved to the closed (ON) position and the warning lights are lit before starting.
Place switch in the closed (ON) position when the engine is started, so the engine will be protected.
Output Shaft Governor Operation
When the load can overspeed the torque converter output shaft, an output shaft governor should be installed. The output shaft governor is a speed limiting device which automatically adjusts engine governor setting according to load requirement.Determining Cause Of Shutdown
If the engine has been shutdown by a safety device, do not start the engine and place it into service without having the cause of the shutdown investigated and corrected.
Low Oil Pressure Checks
If the low oil pressure shutoff control has stopped the engine, make the following checks: 1. Check the water temperature gauge. Determine if the engine was overheated. Check for external water leaks.
Beware of steam or scalding water. Do not attempt to loosen the radiator cap until the temperature gauge indicates the coolant has sufficiently cooled. Then, loosen the cap slowly.
2. Check the oil level. Oil level must be between the ADD and FULL marks on the side of the dipstick stamped CHECK WITH ENGINE STOPPED.3. If the oil level is below the ADD mark, check for oil spray and/or oil accumulations. If any are found, have the necessary repairs made. Before starting, add oil to the FULL mark.4. Reset the shutoff control.5. Remove the load and start the engine at its slowest speed. Be prepared to shut the engine down manually.6. Be alert for unusual sounds or noises. If the engine knocks, stop the engine immediately and call your Caterpillar dealer.7. If the engine blows excessive black exhaust or has excessive crankcase blow-by, the engine may need reconditioning. Stop the engine and call your Caterpillar dealer.8. If the engine runs satisfactorily, observe the oil pressure gauge. If satisfactory pressure is not indicated, shut the engine down; call your Caterpillar dealer.9. If proper oil pressure is registered, check to see if the reset knob has moved to the run position. If the knob does not move, stop the engine. Check the shutoff control, the oil line, and the oil pressure gauge. Have necessary repairs made.10. If the oil pressure gauge registers normal oil pressure, if the knob on the shutoff
Have questions with 106873-2671?
Group cross 106873-2671 ZEXEL
Mitsubishi
Mitsubishi
Mitsubishi
Mitsubishi
106873-2671
INJECTION-PUMP ASSEMBLY