Information injection-pump assembly
ZEXEL
106873-2010
1068732010
MITSUBISHI
ME091466
me091466
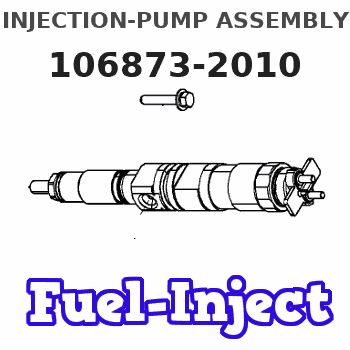
Rating:
Service parts 106873-2010 INJECTION-PUMP ASSEMBLY:
1.
_
7.
COUPLING PLATE
8.
_
9.
_
11.
Nozzle and Holder
12.
Open Pre:MPa(Kqf/cm2)
17.7(180)/21.6(220)
15.
NOZZLE SET
Include in #1:
106873-2010
as INJECTION-PUMP ASSEMBLY
Cross reference number
ZEXEL
106873-2010
1068732010
MITSUBISHI
ME091466
me091466
Zexel num
Bosch num
Firm num
Name
106873-2010
ME091466 MITSUBISHI
INJECTION-PUMP ASSEMBLY
8DC9 * K
8DC9 * K
Calibration Data:
Adjustment conditions
Test oil
1404 Test oil ISO4113 or {SAEJ967d}
1404 Test oil ISO4113 or {SAEJ967d}
Test oil temperature
degC
40
40
45
Nozzle and nozzle holder
105780-8140
Bosch type code
EF8511/9A
Nozzle
105780-0000
Bosch type code
DN12SD12T
Nozzle holder
105780-2080
Bosch type code
EF8511/9
Opening pressure
MPa
17.2
Opening pressure
kgf/cm2
175
Injection pipe
Outer diameter - inner diameter - length (mm) mm 8-3-600
Outer diameter - inner diameter - length (mm) mm 8-3-600
Overflow valve
134424-1320
Overflow valve opening pressure
kPa
157
123
191
Overflow valve opening pressure
kgf/cm2
1.6
1.25
1.95
Tester oil delivery pressure
kPa
157
157
157
Tester oil delivery pressure
kgf/cm2
1.6
1.6
1.6
Direction of rotation (viewed from drive side)
Right R
Right R
Injection timing adjustment
Direction of rotation (viewed from drive side)
Right R
Right R
Injection order
1-2-7-3-
4-5-6-8
Pre-stroke
mm
4.8
4.75
4.85
Beginning of injection position
Governor side NO.1
Governor side NO.1
Difference between angles 1
Cyl.1-2 deg. 45 44.5 45.5
Cyl.1-2 deg. 45 44.5 45.5
Difference between angles 2
Cal 1-7 deg. 90 89.5 90.5
Cal 1-7 deg. 90 89.5 90.5
Difference between angles 3
Cal 1-3 deg. 135 134.5 135.5
Cal 1-3 deg. 135 134.5 135.5
Difference between angles 4
Cal 1-4 deg. 180 179.5 180.5
Cal 1-4 deg. 180 179.5 180.5
Difference between angles 5
Cal 1-5 deg. 225 224.5 225.5
Cal 1-5 deg. 225 224.5 225.5
Difference between angles 6
Cal 1-6 deg. 270 269.5 270.5
Cal 1-6 deg. 270 269.5 270.5
Difference between angles 7
Cal 1-8 deg. 315 314.5 315.5
Cal 1-8 deg. 315 314.5 315.5
Injection quantity adjustment
Adjusting point
-
Rack position
9.5
Pump speed
r/min
700
700
700
Each cylinder's injection qty
mm3/st.
118
114.5
121.5
Basic
*
Fixing the rack
*
Standard for adjustment of the maximum variation between cylinders
*
Injection quantity adjustment_02
Adjusting point
C
Rack position
6.1+-0.5
Pump speed
r/min
225
225
225
Each cylinder's injection qty
mm3/st.
20
17
23
Fixing the rack
*
Standard for adjustment of the maximum variation between cylinders
*
Injection quantity adjustment_03
Adjusting point
A
Rack position
R1(9.5)
Pump speed
r/min
700
700
700
Average injection quantity
mm3/st.
118
117
119
Basic
*
Fixing the lever
*
Injection quantity adjustment_04
Adjusting point
B
Rack position
R1(9.5)
Pump speed
r/min
1100
1100
1100
Average injection quantity
mm3/st.
124
118.8
129.2
Difference in delivery
mm3/st.
10.4
10.4
10.4
Fixing the lever
*
Injection quantity adjustment_05
Adjusting point
E
Rack position
-
Pump speed
r/min
100
100
100
Average injection quantity
mm3/st.
155
135
175
Fixing the lever
*
Remarks
After startup boost setting
After startup boost setting
Timer adjustment
Pump speed
r/min
950--
Advance angle
deg.
0
0
0
Remarks
Start
Start
Timer adjustment_02
Pump speed
r/min
900
Advance angle
deg.
0.5
Timer adjustment_03
Pump speed
r/min
1100
Advance angle
deg.
5
4.5
5.5
Timer adjustment_04
Pump speed
r/min
(1150)
Advance angle
deg.
6.5
6
7
Remarks
Finish
Finish
Test data Ex:
Governor adjustment
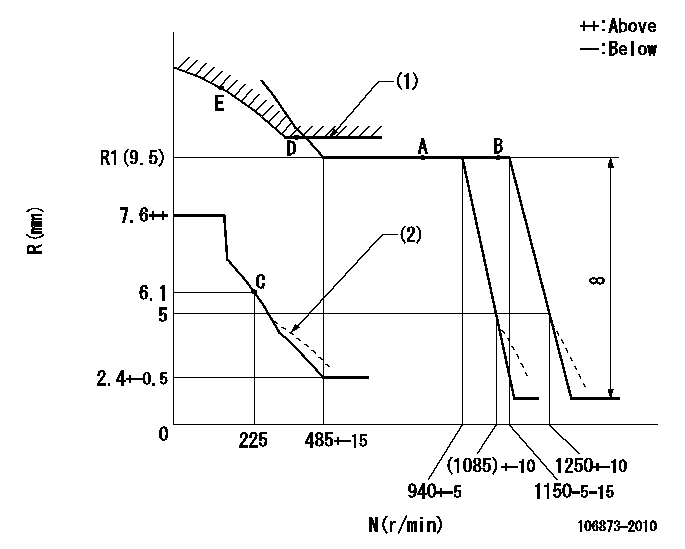
N:Pump speed
R:Rack position (mm)
(1)Excess fuel setting for starting: SXL
(2)Damper spring setting: DL
----------
SXL=10.2+-0.1mm DL=4.3-0.2mm
----------
----------
SXL=10.2+-0.1mm DL=4.3-0.2mm
----------
Speed control lever angle
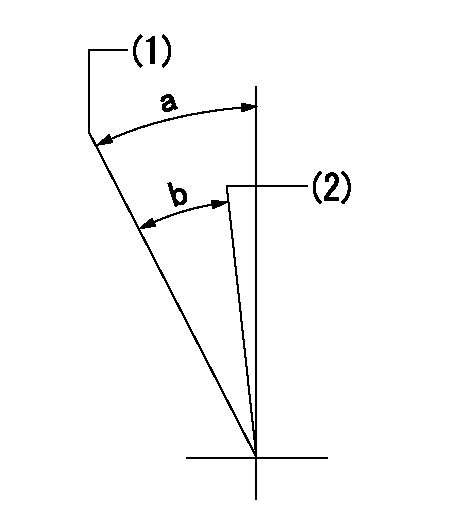
(1)Set the pump speed at aa
(2)Set the pump speed at bb.
----------
aa=1150r/min bb=940r/min
----------
a=24deg+-5deg b=3deg+-5deg
----------
aa=1150r/min bb=940r/min
----------
a=24deg+-5deg b=3deg+-5deg
0000000901

F:Full load
I:Idle
(1)Stopper bolt setting
----------
----------
a=10deg+-5deg b=26deg+-3deg
----------
----------
a=10deg+-5deg b=26deg+-3deg
Stop lever angle
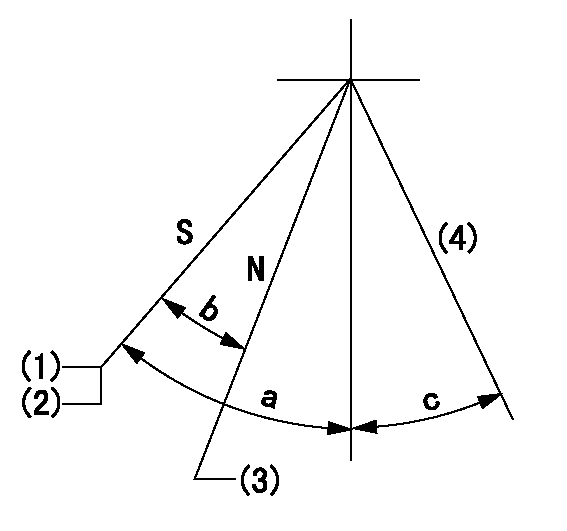
N:Engine manufacturer's normal use
S:Stop the pump.
(1)Rack position = aa
(2)Stopper bolt setting
(3)Rack position bb
(4)Free (at shipping)
----------
aa=4-0.5mm bb=11.7mm
----------
a=43deg+7deg-5deg b=21.5deg+-5deg c=(10.5deg)
----------
aa=4-0.5mm bb=11.7mm
----------
a=43deg+7deg-5deg b=21.5deg+-5deg c=(10.5deg)
0000001501 MICRO SWITCH
Adjustment of the micro-switch
Adjust the bolt to obtain the following lever position when the micro-switch is ON.
(1)Speed N1
(2)Rack position Ra
----------
N1=325+-5r/min Ra=5.6mm
----------
----------
N1=325+-5r/min Ra=5.6mm
----------
Timing setting

(1)Pump vertical direction
(2)Coupling's key groove position at No 1 cylinder's beginning of injection
(3)-
(4)-
----------
----------
a=(40deg)
----------
----------
a=(40deg)
Information:
A measurement of fuel consumption is used to check fuel system performance. If fuel consumption of an engine is within the tolerance of specifications shown in the Fuel Setting And Related Information Fiche, the fuel system is performing correctly and no additional time should be spent checking fuel delivery.Fuel consumption - If the specified amount of fuel is being injected into the engine, the fuel delivery specification is being met. Therefore, the basic fuel system (fuel pump and lines, transfer pump, filters and primary fuel pressure) is within functional limits. Additional time spent troubleshooting these components is probably not justified.Fuel system timing - Fuel cannot be burned efficiently if it is not injected into the cylinder at the correct time. Because engines only develop horsepower when they are running, timing must be measured when they are running. The pin timing of the engine is not adequate. Timing must be measured throughout the speed range (this also checks the timing advance operation).Intake manifold pressure - Manifold pressure is an indication of the overall health of the engine. Boost is affected by any one or all of the following: fuel consumption, compression (valve condition, piston ring condition), turbocharger performance, intake restriction (air filters), exhaust restriction (muffler) or timing.Recommended Procedure With Chassis Dynamometer
Possible Causes/Corrections 1. Check Records Used To Determine Fuel ConsumptionMake sure the records are accurate. The minimum period for accurate fuel records is one month or 10,000 miles. Check the tires (air pressure and size), the gap between the tractor and trailer, air deflectors, trailer width, trailer type, engine cooling fan and driver habits. See "Owner/Operator Input" section for more information on the questions that should be asked. 2. Minor Operating FaultsTo help identify a problem before a more involved troubleshooting procedure is started, follow the procedure given in the "Primary Engine Checks" section. 3. Fuel Ratio Control Out Of Adjustment Or DefectiveFollow the procedure in the Testing and Adjusting section of this Service Manual. 4. Check Engine PerformanceDo a Power Analysis Report (PAR), Level II, to check engine performance. See Special Instruction, Form No. SEHS8025 and SEHS7886 for the tooling and procedures to use. Be sure to make a record of the temperatures for inlet air, fuel (at filter base), lubricating oil and coolant. Also, check for excessive exhaust smoke.At this point, the governor fuel settings should be verified. See the Testing and Adjusting Section of this Service Manual for the correct procedures to use. Also refer back to the information learned earlier (see "Owner Operator Input" section) about truck specifications and application and judge whether or not the engine is performing as expected or customer expectation is realistic. 5. Worn Fuel NozzlesCheck the horsepower on a dynamometer as in Step 4 above. Make a replacement of the fuel injection nozzles and check the horsepower output again. If there is more than 10 hp difference the old nozzles had eroded orifices and were causing high fuel rate.An alternate test is to lower the fuel setting to get the
Possible Causes/Corrections 1. Check Records Used To Determine Fuel ConsumptionMake sure the records are accurate. The minimum period for accurate fuel records is one month or 10,000 miles. Check the tires (air pressure and size), the gap between the tractor and trailer, air deflectors, trailer width, trailer type, engine cooling fan and driver habits. See "Owner/Operator Input" section for more information on the questions that should be asked. 2. Minor Operating FaultsTo help identify a problem before a more involved troubleshooting procedure is started, follow the procedure given in the "Primary Engine Checks" section. 3. Fuel Ratio Control Out Of Adjustment Or DefectiveFollow the procedure in the Testing and Adjusting section of this Service Manual. 4. Check Engine PerformanceDo a Power Analysis Report (PAR), Level II, to check engine performance. See Special Instruction, Form No. SEHS8025 and SEHS7886 for the tooling and procedures to use. Be sure to make a record of the temperatures for inlet air, fuel (at filter base), lubricating oil and coolant. Also, check for excessive exhaust smoke.At this point, the governor fuel settings should be verified. See the Testing and Adjusting Section of this Service Manual for the correct procedures to use. Also refer back to the information learned earlier (see "Owner Operator Input" section) about truck specifications and application and judge whether or not the engine is performing as expected or customer expectation is realistic. 5. Worn Fuel NozzlesCheck the horsepower on a dynamometer as in Step 4 above. Make a replacement of the fuel injection nozzles and check the horsepower output again. If there is more than 10 hp difference the old nozzles had eroded orifices and were causing high fuel rate.An alternate test is to lower the fuel setting to get the
Have questions with 106873-2010?
Group cross 106873-2010 ZEXEL
Mitsubishi
106873-2010
ME091466
INJECTION-PUMP ASSEMBLY
8DC9
8DC9