Information injection-pump assembly
BOSCH
9 400 618 309
9400618309
ZEXEL
106871-8911
1068718911
HINO
220007540B
220007540b
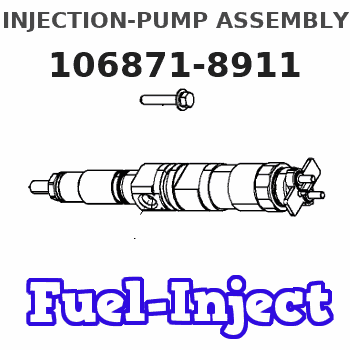
Rating:
Service parts 106871-8911 INJECTION-PUMP ASSEMBLY:
1.
_
7.
COUPLING PLATE
8.
_
9.
_
11.
Nozzle and Holder
236002252A
12.
Open Pre:MPa(Kqf/cm2)
15.7(160)/24.5(250)
15.
NOZZLE SET
Include in #1:
106871-8911
as INJECTION-PUMP ASSEMBLY
Cross reference number
BOSCH
9 400 618 309
9400618309
ZEXEL
106871-8911
1068718911
HINO
220007540B
220007540b
Zexel num
Bosch num
Firm num
Name
106871-8911
9 400 618 309
220007540B HINO
INJECTION-PUMP ASSEMBLY
F20C * K
F20C * K
Calibration Data:
Adjustment conditions
Test oil
1404 Test oil ISO4113 or {SAEJ967d}
1404 Test oil ISO4113 or {SAEJ967d}
Test oil temperature
degC
40
40
45
Nozzle and nozzle holder
105780-8140
Bosch type code
EF8511/9A
Nozzle
105780-0000
Bosch type code
DN12SD12T
Nozzle holder
105780-2080
Bosch type code
EF8511/9
Opening pressure
MPa
17.2
Opening pressure
kgf/cm2
175
Injection pipe
Outer diameter - inner diameter - length (mm) mm 8-3-600
Outer diameter - inner diameter - length (mm) mm 8-3-600
Overflow valve
134424-1020
Overflow valve opening pressure
kPa
127
107
147
Overflow valve opening pressure
kgf/cm2
1.3
1.1
1.5
Tester oil delivery pressure
kPa
157
157
157
Tester oil delivery pressure
kgf/cm2
1.6
1.6
1.6
Direction of rotation (viewed from drive side)
Right R
Right R
Injection timing adjustment
Direction of rotation (viewed from drive side)
Right R
Right R
Injection order
1-8-6-2-
7-5-4-3
Pre-stroke
mm
4.5
4.44
4.5
Beginning of injection position
Drive side NO.1
Drive side NO.1
Difference between angles 1
Cal 1-8 deg. 45 44.75 45.25
Cal 1-8 deg. 45 44.75 45.25
Difference between angles 2
Cal 1-6 deg. 90 89.75 90.25
Cal 1-6 deg. 90 89.75 90.25
Difference between angles 3
Cyl.1-2 deg. 135 134.75 135.25
Cyl.1-2 deg. 135 134.75 135.25
Difference between angles 4
Cal 1-7 deg. 180 179.75 180.25
Cal 1-7 deg. 180 179.75 180.25
Difference between angles 5
Cal 1-5 deg. 225 224.75 225.25
Cal 1-5 deg. 225 224.75 225.25
Difference between angles 6
Cal 1-4 deg. 270 269.75 270.25
Cal 1-4 deg. 270 269.75 270.25
Difference between angles 7
Cal 1-3 deg. 315 314.75 315.25
Cal 1-3 deg. 315 314.75 315.25
Injection quantity adjustment
Adjusting point
A
Rack position
9.2
Pump speed
r/min
700
700
700
Average injection quantity
mm3/st.
154.4
152.4
156.4
Max. variation between cylinders
%
0
-2
2
Basic
*
Fixing the lever
*
Injection quantity adjustment_02
Adjusting point
B
Rack position
9.05
Pump speed
r/min
500
500
500
Average injection quantity
mm3/st.
155.5
152.5
158.5
Fixing the lever
*
Injection quantity adjustment_03
Adjusting point
C
Rack position
9.25
Pump speed
r/min
900
900
900
Average injection quantity
mm3/st.
152.7
149.7
155.7
Fixing the lever
*
Injection quantity adjustment_04
Adjusting point
D
Rack position
9.25+-0.
5
Pump speed
r/min
1100
1100
1100
Average injection quantity
mm3/st.
143.5
139.5
147.5
Fixing the lever
*
Injection quantity adjustment_05
Adjusting point
E
Rack position
8.45
Pump speed
r/min
1200
1200
1200
Average injection quantity
mm3/st.
123.9
120.9
126.9
Fixing the lever
*
Injection quantity adjustment_06
Adjusting point
F
Rack position
3.8+-0.5
Pump speed
r/min
225
225
225
Average injection quantity
mm3/st.
12.1
9.1
15.1
Max. variation between cylinders
%
0
-15
15
Fixing the rack
*
Injection quantity adjustment_07
Adjusting point
H
Rack position
-
Pump speed
r/min
100
100
100
Average injection quantity
mm3/st.
185
185
225
Fixing the lever
*
Remarks
After startup boost setting
After startup boost setting
Timer adjustment
Pump speed
r/min
-
Advance angle
deg.
0
0
0
Remarks
Measure speed (beginning of operation).
Measure speed (beginning of operation).
Timer adjustment_02
Pump speed
r/min
800--
Advance angle
deg.
1
0.7
1.3
Timer adjustment_03
Pump speed
r/min
-
Advance angle
deg.
1
0.7
1.3
Remarks
Measure the actual speed.
Measure the actual speed.
Timer adjustment_04
Pump speed
r/min
1100-50
Advance angle
deg.
4.75
4.45
5.05
Remarks
Finish
Finish
Test data Ex:
Governor adjustment
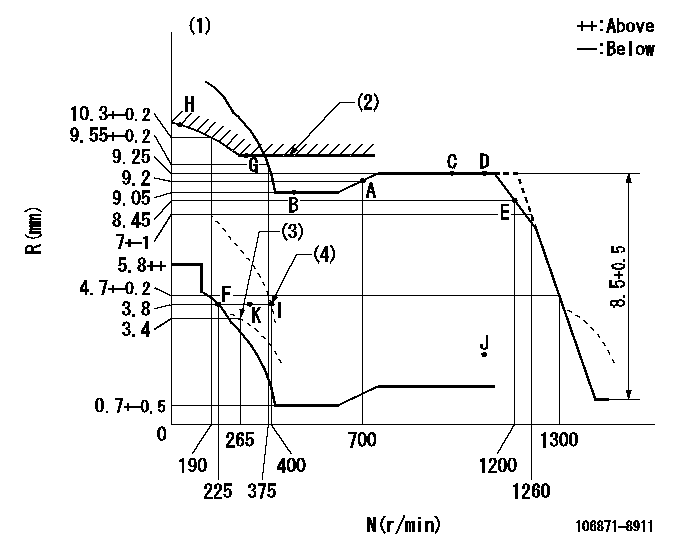
N:Pump speed
R:Rack position (mm)
(1)Tolerance for racks not indicated: +-0.05mm.
(2)Excess fuel setting for starting: SXL
(3)Damper spring setting
(4)When air cylinder is operating.
----------
SXL=9.75+-0.1mm
----------
----------
SXL=9.75+-0.1mm
----------
Speed control lever angle

F:Full speed
----------
----------
a=15.5deg+-5deg
----------
----------
a=15.5deg+-5deg
0000000901

F:Full load
I:Idle
(1)Set point I (at air cylinder operation)
(2)Use the hole at R = aa
(3)Stopper bolt setting
----------
aa=39mm
----------
a=39deg+-5deg b=44.5deg+-3deg c=(14.5deg)
----------
aa=39mm
----------
a=39deg+-5deg b=44.5deg+-3deg c=(14.5deg)
Stop lever angle

N:Pump normal
S:Stop the pump.
----------
----------
a=15deg+-5deg b=64deg+-5deg
----------
----------
a=15deg+-5deg b=64deg+-5deg
0000001501 RACK SENSOR
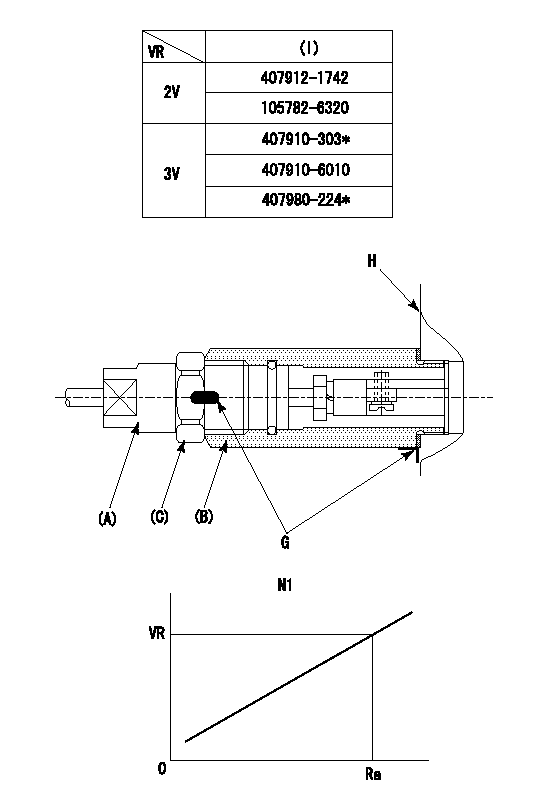
(VR) measurement voltage
(I) Part number of the control unit
(G) Apply red paint.
(H): End surface of the pump
1. Rack sensor adjustment (-0620)
(1)Fix the speed control lever at the full position
(2)Set the speed to N1 r/min.
(If the boost compensator is provided, apply boost pressure.)
(3)Adjust the bobbin (A) so that the rack sensor's output voltage is VR+-0.01.
(4)At that time, rack position must be Ra.
(5)Apply G at two places.
Connecting part between the joint (B) and the nut (F)
Connecting part between the joint (B) and the end surface of the pump (H)
----------
N1=900r/min Ra=9.25mm
----------
----------
N1=900r/min Ra=9.25mm
----------
0000001601 LEVER

1. Air cylinder adjustment
(1)With the load lever in the idle position, temporarily set the distance between the load lever A and the air cylinder D at approximately L.
(2)Set N1 and apply P1 to the air cylinder D.
(3)Adjust set bolt (D) to obtain R1 at the same speed.
(4)Lock using nut C.
(5)Apply positive pressure several times.
(6)Confirm that the load lever A returns to the idling position N2 at pressure P2.
(7)Also at P1 confirm R1 (N1).
----------
L=(5)mm R1=3.8mm N1=400r/min N2=(225)r/min P1=392+98kPa(4+1kgf/cm2) P2=0kPa(0kgf/cm2)
----------
----------
L=(5)mm R1=3.8mm N1=400r/min N2=(225)r/min P1=392+98kPa(4+1kgf/cm2) P2=0kPa(0kgf/cm2)
----------
Timing setting
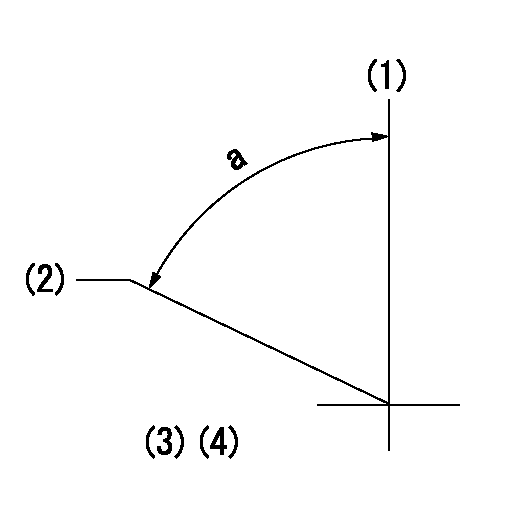
(1)Pump vertical direction
(2)Coupling's key groove position at No 1 cylinder's beginning of injection
(3)-
(4)-
----------
----------
a=(80deg)
----------
----------
a=(80deg)
Information:
(1) Maximum permissible temperature of the gear for installation on the camshaft (do not use a torch) ... 315°C (600°F)(2) Tight fit between the gear and camshaft ... 0.037 to 0.123 mm (.0015 to .0048 in)(3) Diameter of the surfaces (journals) for the camshaft bearings (new) ... 69.850 0.013 mm (2.7500 .0005 in) Bore in front bearing for the camshaft (after assembly) ... 69.969 0.048 mm (2.7547 .0019 in)Bore in the other six bearings for the camshaft (after assembly) ... 69.982 0.061 mm (2.7552 .0024 in)(4) Thickness of thrust plate (new) ... 4.65 0.03 mm (.183 .001 in) End play of the camshaft ... 0.10 to 0.26 mm (.004 to .010 in) (5) Height of camshaft lobes.To find lobe height, use the procedure that follows:A. Measure camshaft lobe height (5).B. Measure base circle (7).C. Subtract base circle (STEP B) from lobe height (STEP A). The difference is actual lobe lift (6).D. Specified camshaft lobe lift (6) is:4W2430 Camshaft Assembly
a. Exhaust lobe ... 10.211 mm (.4020 in)b. Intake lobe ... 10.211 mm (.4020 in)7W3797 Camshaft Assembly
a. Exhaust lobe ... 10.210 mm (.4020 in)b. Intake lobe ... 10.212 mm (.4021 in)Maximum permissible difference between actual lobe lift (STEP C) and specified lobe lift (STEP D) is 0.13 mm (.005 in).Intake Valve Timing
1. Check the No. 1 intake valve clearance with the engine stopped. The valve clearance must be 0.30 to 0.46 mm (.012 to .018 in). If the valve clearance is not in this range, adjust the clearance to 0.38 mm (.015 in).2. Mark Top Center Position of the crankshaft on the vibration damper or pulley.3. Use a dial indicator to measure the intake valve movement.4. Rotate the crankshaft in the direction of normal engine rotation. Stop when the intake valve is 1.91 mm (.075 in) off its seat in the opening sequence.At this point the crankshaft Top Center Position Mark must be in position as follows: Engines with the 4W2430 Camshaft Assembly ... 7 2° After Top CenterEngines with the 7W3797 Camshaft Assembly ... 1 2° After Top CenterChecking Valve-Camshaft Timing (field procedure)
The following factory procedure as described in the December 11, 1989 Service Magazine article will simplify in the field checking of the camshaft timing procedures.1. Set the No. 3 intake bridge adjustment.2. Set the No. 3 intake valve clearance.3. Install the bolt in the flywheel with No. 1 piston at top center.4. Install the dial indicator (magnetic base) to No. 3 intake bridge.5. Remove the bolt from the flywheel.6. Set the gauge at zero and rotate the engine in the normal direction of operation (counterclockwise as seen from the flywheel end) until dial travel stops.The following chart indicates the correct setting.
a. Exhaust lobe ... 10.211 mm (.4020 in)b. Intake lobe ... 10.211 mm (.4020 in)7W3797 Camshaft Assembly
a. Exhaust lobe ... 10.210 mm (.4020 in)b. Intake lobe ... 10.212 mm (.4021 in)Maximum permissible difference between actual lobe lift (STEP C) and specified lobe lift (STEP D) is 0.13 mm (.005 in).Intake Valve Timing
1. Check the No. 1 intake valve clearance with the engine stopped. The valve clearance must be 0.30 to 0.46 mm (.012 to .018 in). If the valve clearance is not in this range, adjust the clearance to 0.38 mm (.015 in).2. Mark Top Center Position of the crankshaft on the vibration damper or pulley.3. Use a dial indicator to measure the intake valve movement.4. Rotate the crankshaft in the direction of normal engine rotation. Stop when the intake valve is 1.91 mm (.075 in) off its seat in the opening sequence.At this point the crankshaft Top Center Position Mark must be in position as follows: Engines with the 4W2430 Camshaft Assembly ... 7 2° After Top CenterEngines with the 7W3797 Camshaft Assembly ... 1 2° After Top CenterChecking Valve-Camshaft Timing (field procedure)
The following factory procedure as described in the December 11, 1989 Service Magazine article will simplify in the field checking of the camshaft timing procedures.1. Set the No. 3 intake bridge adjustment.2. Set the No. 3 intake valve clearance.3. Install the bolt in the flywheel with No. 1 piston at top center.4. Install the dial indicator (magnetic base) to No. 3 intake bridge.5. Remove the bolt from the flywheel.6. Set the gauge at zero and rotate the engine in the normal direction of operation (counterclockwise as seen from the flywheel end) until dial travel stops.The following chart indicates the correct setting.
Have questions with 106871-8911?
Group cross 106871-8911 ZEXEL
Hino
106871-8911
9 400 618 309
220007540B
INJECTION-PUMP ASSEMBLY
F20C
F20C