Information injection-pump assembly
BOSCH
9 400 618 303
9400618303
ZEXEL
106871-8802
1068718802
HINO
220007282A
220007282a
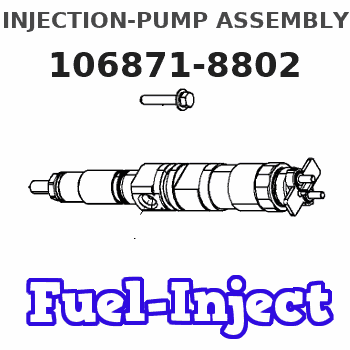
Rating:
Service parts 106871-8802 INJECTION-PUMP ASSEMBLY:
1.
_
7.
COUPLING PLATE
8.
_
9.
_
11.
Nozzle and Holder
23600-2450B
12.
Open Pre:MPa(Kqf/cm2)
17.7{180}/24.5{250}
14.
NOZZLE
Include in #1:
106871-8802
as INJECTION-PUMP ASSEMBLY
Cross reference number
BOSCH
9 400 618 303
9400618303
ZEXEL
106871-8802
1068718802
HINO
220007282A
220007282a
Zexel num
Bosch num
Firm num
Name
Calibration Data:
Adjustment conditions
Test oil
1404 Test oil ISO4113 or {SAEJ967d}
1404 Test oil ISO4113 or {SAEJ967d}
Test oil temperature
degC
40
40
45
Nozzle and nozzle holder
105780-8140
Bosch type code
EF8511/9A
Nozzle
105780-0000
Bosch type code
DN12SD12T
Nozzle holder
105780-2080
Bosch type code
EF8511/9
Opening pressure
MPa
17.2
Opening pressure
kgf/cm2
175
Injection pipe
Outer diameter - inner diameter - length (mm) mm 8-3-600
Outer diameter - inner diameter - length (mm) mm 8-3-600
Overflow valve
134424-0820
Overflow valve opening pressure
kPa
127
107
147
Overflow valve opening pressure
kgf/cm2
1.3
1.1
1.5
Tester oil delivery pressure
kPa
157
157
157
Tester oil delivery pressure
kgf/cm2
1.6
1.6
1.6
Direction of rotation (viewed from drive side)
Right R
Right R
Injection timing adjustment
Direction of rotation (viewed from drive side)
Right R
Right R
Injection order
1-8-6-2-
7-5-4-3
Pre-stroke
mm
4.8
4.74
4.8
Beginning of injection position
Drive side NO.1
Drive side NO.1
Difference between angles 1
Cal 1-8 deg. 45 44.75 45.25
Cal 1-8 deg. 45 44.75 45.25
Difference between angles 2
Cal 1-6 deg. 90 89.75 90.25
Cal 1-6 deg. 90 89.75 90.25
Difference between angles 3
Cyl.1-2 deg. 135 134.75 135.25
Cyl.1-2 deg. 135 134.75 135.25
Difference between angles 4
Cal 1-7 deg. 180 179.75 180.25
Cal 1-7 deg. 180 179.75 180.25
Difference between angles 5
Cal 1-5 deg. 225 224.75 225.25
Cal 1-5 deg. 225 224.75 225.25
Difference between angles 6
Cal 1-4 deg. 270 269.75 270.25
Cal 1-4 deg. 270 269.75 270.25
Difference between angles 7
Cal 1-3 deg. 315 314.75 315.25
Cal 1-3 deg. 315 314.75 315.25
Injection quantity adjustment
Adjusting point
A
Rack position
9.5
Pump speed
r/min
700
700
700
Average injection quantity
mm3/st.
143.6
141.6
145.6
Max. variation between cylinders
%
0
-2
2
Basic
*
Fixing the lever
*
Injection quantity adjustment_02
Adjusting point
B
Rack position
9.8
Pump speed
r/min
1100
1100
1100
Average injection quantity
mm3/st.
141.1
138.1
144.1
Max. variation between cylinders
%
0
-4
4
Fixing the lever
*
Injection quantity adjustment_03
Adjusting point
C
Rack position
9.6
Pump speed
r/min
900
900
900
Average injection quantity
mm3/st.
143.4
140.4
146.4
Fixing the lever
*
Injection quantity adjustment_04
Adjusting point
D
Rack position
9.5
Pump speed
r/min
500
500
500
Average injection quantity
mm3/st.
148.5
142.5
154.5
Fixing the lever
*
Injection quantity adjustment_05
Adjusting point
E
Rack position
9.1
Pump speed
r/min
1200
1200
1200
Average injection quantity
mm3/st.
123.4
117.4
129.4
Fixing the lever
*
Injection quantity adjustment_06
Adjusting point
F
Rack position
4.2+-0.5
Pump speed
r/min
225
225
225
Average injection quantity
mm3/st.
9.6
6.6
12.6
Max. variation between cylinders
%
0
-15
15
Fixing the rack
*
Timer adjustment
Pump speed
r/min
900
Advance angle
deg.
1.7
1.4
2
Load
3/4
Timer adjustment_02
Pump speed
r/min
1060
Advance angle
deg.
4.75
4.45
5.05
Load
4/4
Remarks
Finish
Finish
Test data Ex:
Governor adjustment

N:Pump speed
R:Rack position (mm)
(1)Lever ratio: RT
(2)Target shim dimension: TH
(3)Tolerance for racks not indicated: +-0.05mm.
(4)Excess fuel setting for starting: SXL
(5)Set the damper spring (after setting the idle spring).
----------
RT=0.8 TH=2.7mm SXL=10.1+-0.1mm
----------
----------
RT=0.8 TH=2.7mm SXL=10.1+-0.1mm
----------
Speed control lever angle

F:Full speed
----------
----------
a=14deg+-5deg
----------
----------
a=14deg+-5deg
0000000901

F:Full load
I:Idle
(1)Use the hole at R = aa
(2)Stopper bolt setting
----------
aa=42mm
----------
a=39deg+-5deg b=46deg+-3deg
----------
aa=42mm
----------
a=39deg+-5deg b=46deg+-3deg
Stop lever angle
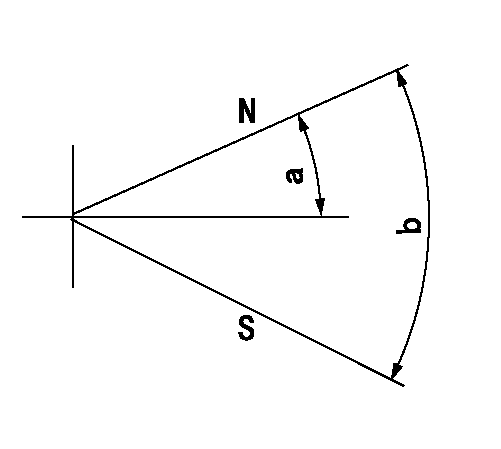
N:Pump normal
S:Stop the pump.
----------
----------
a=46deg+-5deg b=64deg+-5deg
----------
----------
a=46deg+-5deg b=64deg+-5deg
0000001501 RACK SENSOR
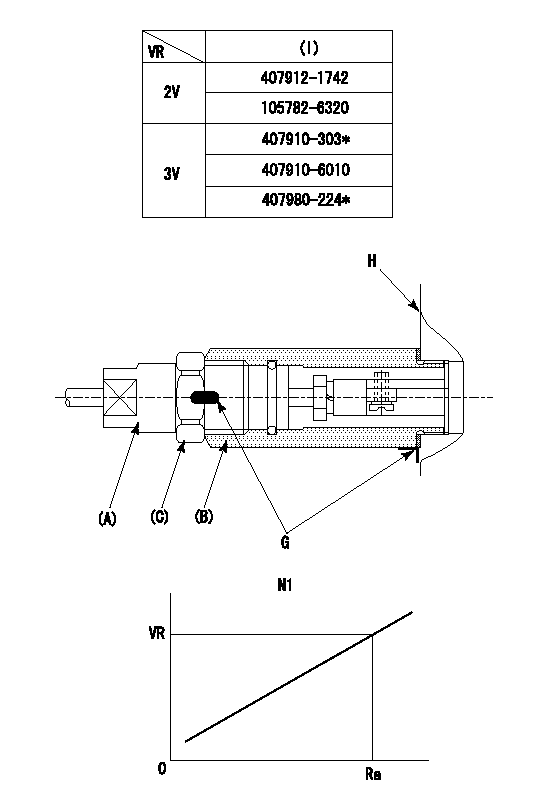
(VR) measurement voltage
(I) Part number of the control unit
(G) Apply red paint.
(H): End surface of the pump
1. Rack sensor adjustment (-0620)
(1)Fix the speed control lever at the full position
(2)Set the speed to N1 r/min.
(If the boost compensator is provided, apply boost pressure.)
(3)Adjust the bobbin (A) so that the rack sensor's output voltage is VR+-0.01.
(4)At that time, rack position must be Ra.
(5)Apply G at two places.
Connecting part between the joint (B) and the nut (F)
Connecting part between the joint (B) and the end surface of the pump (H)
----------
N1=1070r/min Ra=9.8mm
----------
----------
N1=1070r/min Ra=9.8mm
----------
Timing setting
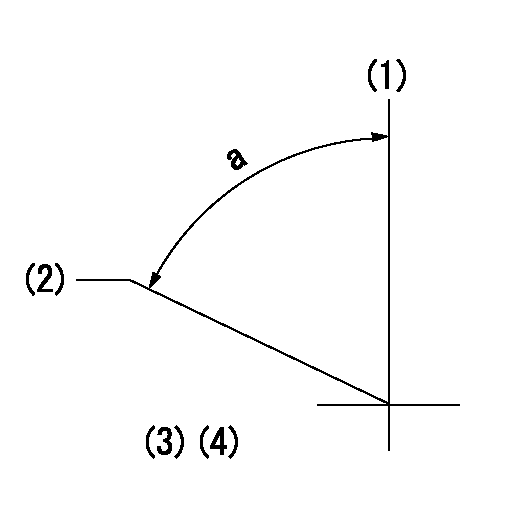
(1)Pump vertical direction
(2)Coupling's key groove position at No 1 cylinder's beginning of injection
(3)-
(4)-
----------
----------
a=(80deg)
----------
----------
a=(80deg)
Information:
Install Crankcase Ventilator Valve
1. Put gasket (2) and ventilator valve (1) in position. 2. Install the bolts and tighten them to a torque of 3.4 0.5 N m (30 4 lb.in.).Disassemble Crankcase Ventilator Valve
The crankcase ventilator valve can be disassembled while installed on the engine. The valve was removed for better photo illustration.1. Remove screws (2) that hold cover (3) on housing (1). 2. Remove cover (3) and spring (4) from the housing. 3. Remove the piston, sleeve (8), retainer (9), and diaphragm (7) from the housing as a unit. 4. Remove inner sleeve (6) and gasket (5) from the housing. 5. Remove nut (12), washer (13), spacer (11), piston (10), diaphragm (7), and the retainer from sleeve (8).Assemble Crankcase Ventilator Valve
1. Put 5H2471 Gasket Cement on both sides of gasket (2). Install the gasket on housing (1). 2. Install inner sleeve (3) in the housing.3. Put piston (6) in position next to the side of diaphragm (4) that has identification "PISTON SIDE".4. Put retainer (5) in the diaphragm. 5. Put the screw through sleeve (7), retainer, diaphragm, and the piston.6. Install spacer (8), washer, and nut (9) on the screw. 7. Put 5H2471 Gasket Cement on the contact surfaces of the diaphragm. Install the sleeve, retainer, diaphragm, and piston in the inner sleeve and housing.8. Put the spring and cover in position on the housing and install the screws that hold the cover in place.
1. Put gasket (2) and ventilator valve (1) in position. 2. Install the bolts and tighten them to a torque of 3.4 0.5 N m (30 4 lb.in.).Disassemble Crankcase Ventilator Valve
The crankcase ventilator valve can be disassembled while installed on the engine. The valve was removed for better photo illustration.1. Remove screws (2) that hold cover (3) on housing (1). 2. Remove cover (3) and spring (4) from the housing. 3. Remove the piston, sleeve (8), retainer (9), and diaphragm (7) from the housing as a unit. 4. Remove inner sleeve (6) and gasket (5) from the housing. 5. Remove nut (12), washer (13), spacer (11), piston (10), diaphragm (7), and the retainer from sleeve (8).Assemble Crankcase Ventilator Valve
1. Put 5H2471 Gasket Cement on both sides of gasket (2). Install the gasket on housing (1). 2. Install inner sleeve (3) in the housing.3. Put piston (6) in position next to the side of diaphragm (4) that has identification "PISTON SIDE".4. Put retainer (5) in the diaphragm. 5. Put the screw through sleeve (7), retainer, diaphragm, and the piston.6. Install spacer (8), washer, and nut (9) on the screw. 7. Put 5H2471 Gasket Cement on the contact surfaces of the diaphragm. Install the sleeve, retainer, diaphragm, and piston in the inner sleeve and housing.8. Put the spring and cover in position on the housing and install the screws that hold the cover in place.