Information injection-pump assembly
ZEXEL
106871-8180
1068718180
HINO
220005862A
220005862a
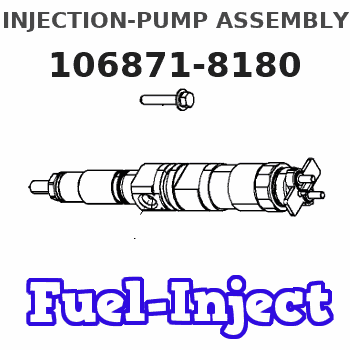
Rating:
Cross reference number
ZEXEL
106871-8180
1068718180
HINO
220005862A
220005862a
Zexel num
Bosch num
Firm num
Name
Calibration Data:
Adjustment conditions
Test oil
1404 Test oil ISO4113 or {SAEJ967d}
1404 Test oil ISO4113 or {SAEJ967d}
Test oil temperature
degC
40
40
45
Nozzle and nozzle holder
105780-8140
Bosch type code
EF8511/9A
Nozzle
105780-0000
Bosch type code
DN12SD12T
Nozzle holder
105780-2080
Bosch type code
EF8511/9
Opening pressure
MPa
17.2
Opening pressure
kgf/cm2
175
Injection pipe
Outer diameter - inner diameter - length (mm) mm 8-3-600
Outer diameter - inner diameter - length (mm) mm 8-3-600
Overflow valve
134424-0820
Overflow valve opening pressure
kPa
127
107
147
Overflow valve opening pressure
kgf/cm2
1.3
1.1
1.5
Tester oil delivery pressure
kPa
157
157
157
Tester oil delivery pressure
kgf/cm2
1.6
1.6
1.6
Direction of rotation (viewed from drive side)
Right R
Right R
Injection timing adjustment
Direction of rotation (viewed from drive side)
Right R
Right R
Injection order
1-8-6-2-
7-5-4-3
Pre-stroke
mm
4.8
4.74
4.8
Beginning of injection position
Drive side NO.1
Drive side NO.1
Difference between angles 1
Cal 1-8 deg. 45 44.75 45.25
Cal 1-8 deg. 45 44.75 45.25
Difference between angles 2
Cal 1-6 deg. 90 89.75 90.25
Cal 1-6 deg. 90 89.75 90.25
Difference between angles 3
Cyl.1-2 deg. 135 134.75 135.25
Cyl.1-2 deg. 135 134.75 135.25
Difference between angles 4
Cal 1-7 deg. 180 179.75 180.25
Cal 1-7 deg. 180 179.75 180.25
Difference between angles 5
Cal 1-5 deg. 225 224.75 225.25
Cal 1-5 deg. 225 224.75 225.25
Difference between angles 6
Cal 1-4 deg. 270 269.75 270.25
Cal 1-4 deg. 270 269.75 270.25
Difference between angles 7
Cal 1-3 deg. 315 314.75 315.25
Cal 1-3 deg. 315 314.75 315.25
Injection quantity adjustment
Adjusting point
A
Rack position
9.8
Pump speed
r/min
700
700
700
Average injection quantity
mm3/st.
140.2
138.2
142.2
Max. variation between cylinders
%
0
-2
2
Basic
*
Fixing the lever
*
Injection quantity adjustment_02
Adjusting point
B
Rack position
10.1
Pump speed
r/min
1100
1100
1100
Average injection quantity
mm3/st.
136.8
130.8
142.8
Max. variation between cylinders
%
0
-4
4
Fixing the lever
*
Injection quantity adjustment_03
Adjusting point
C
Rack position
9.9
Pump speed
r/min
900
900
900
Average injection quantity
mm3/st.
138.4
135.4
141.4
Fixing the lever
*
Injection quantity adjustment_04
Adjusting point
D
Rack position
9.8
Pump speed
r/min
500
500
500
Average injection quantity
mm3/st.
143.8
140.8
146.8
Fixing the lever
*
Injection quantity adjustment_05
Adjusting point
F
Rack position
4.2+-0.5
Pump speed
r/min
225
225
225
Average injection quantity
mm3/st.
9.1
6.1
12.1
Max. variation between cylinders
%
0
-15
15
Fixing the rack
*
Timer adjustment
Pump speed
r/min
900
Advance angle
deg.
1.7
1.4
2
Load
3/4
Timer adjustment_02
Pump speed
r/min
1060
Advance angle
deg.
4.75
4.45
5.05
Load
4/4
Remarks
Finish
Finish
Test data Ex:
Governor adjustment
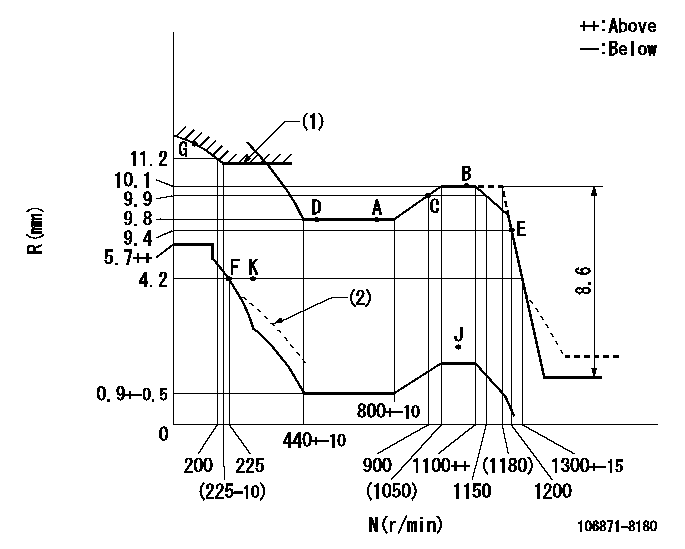
N:Pump speed
R:Rack position (mm)
(1)Excess fuel setting for starting: SXL
(2)Damper spring setting: DL
----------
SXL=11+-0.1mm DL=3.7-0.2mm
----------
----------
SXL=11+-0.1mm DL=3.7-0.2mm
----------
Speed control lever angle

F:Full speed
----------
----------
a=14deg+-5deg
----------
----------
a=14deg+-5deg
0000000901

F:Full load
I:Idle
(1)Use the hole at R = aa
(2)Stopper bolt setting
----------
aa=42mm
----------
a=39deg+-5deg b=46deg+-3deg
----------
aa=42mm
----------
a=39deg+-5deg b=46deg+-3deg
Stop lever angle

N:Engine manufacturer's normal use
S:Stop the pump.
(1)Rack position = aa
(2)Rack position bb
(3)Set the stopper bolt (apply red paint).
(4)Free (at shipping)
----------
aa=12mm bb=3mm
----------
a=(15deg) b=48deg+-5deg c=26deg+-5deg
----------
aa=12mm bb=3mm
----------
a=(15deg) b=48deg+-5deg c=26deg+-5deg
0000001501 RACK SENSOR
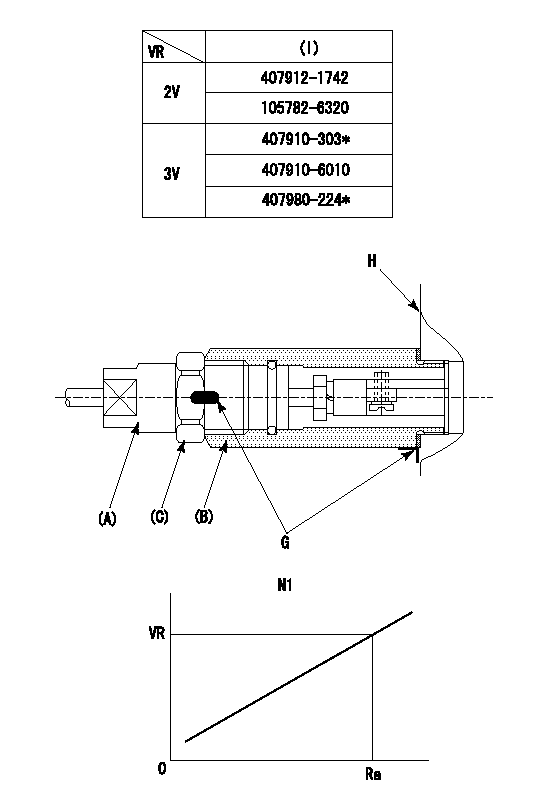
(VR) measurement voltage
(I) Part number of the control unit
(G) Apply red paint.
(H): End surface of the pump
1. Rack sensor adjustment (-0620)
(1)Fix the speed control lever at the full position
(2)Set the speed to N1 r/min.
(If the boost compensator is provided, apply boost pressure.)
(3)Adjust the bobbin (A) so that the rack sensor's output voltage is VR+-0.01.
(4)At that time, rack position must be Ra.
(5)Apply G at two places.
Connecting part between the joint (B) and the nut (F)
Connecting part between the joint (B) and the end surface of the pump (H)
----------
N1=1070r/min Ra=10.1mm
----------
----------
N1=1070r/min Ra=10.1mm
----------
Timing setting
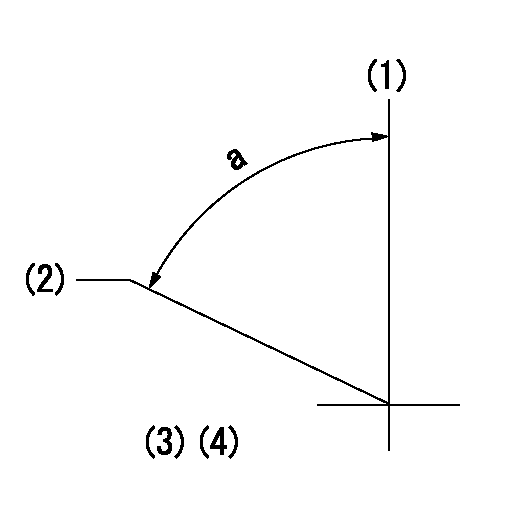
(1)Pump vertical direction
(2)Coupling's key groove position at No 1 cylinder's beginning of injection
(3)-
(4)-
----------
----------
a=(80deg)
----------
----------
a=(80deg)
Information:
Do not operate the machine if any guards or covers are missing or inadequately secured. Personnel could be seriously injured or machine damage may occur.
Observe the safe working load limits of all lifting and blocking devices and keep a safe distance from suspended/blocked loads. Personnel may be seriously injured or killed by falling loads.
Reference Section
Refer to Service Magazine, M0082326, "Diesel Exhaust Fluid (DEF) Contamination on C4.4 Machine Engines".Refer to Service Magazine, M0096547, "Diesel Exhaust Fluid (DEF) Pump Filter Maintenance on Certain C4.4 Machine Engines".Refer to Special Instruction, M0096185, "Diesel Exhaust Fluid (DEF) Pump Diesel Contamination Test on Certain C4.4 Engines".Problem
There have been instances of returned DEF pumps that have no fault found or indicating contamination.Resolution
Complete the form below and attach to any SIMSi claim in addition to a Product Status Report (PSR) from before any troubleshooting was performed or any diagnostic codes were cleared.
Use the electronic service tool to download a PSR with Histograms.
Enter the diagnostic codes that require troubleshooting: ___
Perform the correct troubleshooting procedure for any active diagnostic codes. Refer to Troubleshooting, Diagnostic Trouble Codes.
If the troubleshooting procedure requests that the DEF is tested for contamination or concentration , record the results in Table 1 and Table 2.
For other DEF-related troubleshooting procedures, follow the applicable troubleshooting steps and record the results in Table 3.
Table 1
DEF Contamination
Step Instruction Completed Result Units
1 Perform the test procedure for DEF contamination. Refer to Systems Operation, Testing and Adjusting, Diesel Exhaust Fluid Quality - Test.
2 Compensator measurements. Refer to Special Instruction, M0096185, "Diesel Exhaust Fluid (DEF) Pump Diesel Contamination Test on Certain C4.4 Engines".
Diameter (A) mm
Length (B) mm
3 If contamination is present, confirm that DEF system has been flushed. Refer to Systems Operation, Testing and Adjusting, Diesel Exhaust Fluid Tank - Flush
Table 2
DEF Concentration
Step Instruction Completed Result Units
1 Perform the test procedure for DEF concentration. Refer to Systems Operation, Testing and Adjusting, Diesel Exhaust Fluid Quality - Test. %
2 If the DEF concentration is out of specification, confirm that the DEF tank has been drained and filled with the correct specification of DEF. Refer to Operation and Maintenance Manual, Diesel Exhaust Fluid - Fill.
Table 3
DEF Troubleshooting
Step Instruction Completed Result Units
1 Latest engine and Dosing Control Unit (DCU) software has been installed. Refer to Troubleshooting, ECM Software - Install.
2 DEF lines have been checked for restrictions.
3 DEF pump has been checked for restrictions.
4 DEF injector has been checked for restrictions.
5 DEF lines have been inspected for leaks.
6 Confirm the DEF pressure. Refer to Troubleshooting, DEF Pressure Does Not Respond. kPa
7 DEF dosing system accuracy test has been performed. Refer to Troubleshooting, Aftertreatment SCR System Dosing - Test.
8 DEF pump filter replaced.
9 "Aftertreatment System Functional Test" performed. Refer to Troubleshooting, Service Tool Features.