Information injection-pump assembly
BOSCH
9 400 618 218
9400618218
ZEXEL
106871-7581
1068717581
MITSUBISHI
ME090645
me090645
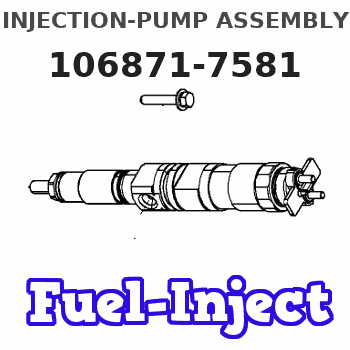
Rating:
Service parts 106871-7581 INJECTION-PUMP ASSEMBLY:
1.
_
7.
COUPLING PLATE
8.
_
9.
_
11.
Nozzle and Holder
ME066499
12.
Open Pre:MPa(Kqf/cm2)
17.7{180}/21.6{220}
15.
NOZZLE SET
Include in #1:
106871-7581
as INJECTION-PUMP ASSEMBLY
Cross reference number
BOSCH
9 400 618 218
9400618218
ZEXEL
106871-7581
1068717581
MITSUBISHI
ME090645
me090645
Zexel num
Bosch num
Firm num
Name
9 400 618 218
ME090645 MITSUBISHI
INJECTION-PUMP ASSEMBLY
8DC9T2 K 14CD INJECTION PUMP ASSY PE8P PE
8DC9T2 K 14CD INJECTION PUMP ASSY PE8P PE
Calibration Data:
Adjustment conditions
Test oil
1404 Test oil ISO4113 or {SAEJ967d}
1404 Test oil ISO4113 or {SAEJ967d}
Test oil temperature
degC
40
40
45
Nozzle and nozzle holder
105780-8140
Bosch type code
EF8511/9A
Nozzle
105780-0000
Bosch type code
DN12SD12T
Nozzle holder
105780-2080
Bosch type code
EF8511/9
Opening pressure
MPa
17.2
Opening pressure
kgf/cm2
175
Injection pipe
Outer diameter - inner diameter - length (mm) mm 8-3-600
Outer diameter - inner diameter - length (mm) mm 8-3-600
Overflow valve
131424-4620
Overflow valve opening pressure
kPa
255
221
289
Overflow valve opening pressure
kgf/cm2
2.6
2.25
2.95
Tester oil delivery pressure
kPa
157
157
157
Tester oil delivery pressure
kgf/cm2
1.6
1.6
1.6
Direction of rotation (viewed from drive side)
Right R
Right R
Injection timing adjustment
Direction of rotation (viewed from drive side)
Right R
Right R
Injection order
1-2-7-3-
4-5-6-8
Pre-stroke
mm
4.8
4.75
4.85
Beginning of injection position
Governor side NO.1
Governor side NO.1
Difference between angles 1
Cyl.1-2 deg. 45 44.5 45.5
Cyl.1-2 deg. 45 44.5 45.5
Difference between angles 2
Cal 1-7 deg. 90 89.5 90.5
Cal 1-7 deg. 90 89.5 90.5
Difference between angles 3
Cal 1-3 deg. 135 134.5 135.5
Cal 1-3 deg. 135 134.5 135.5
Difference between angles 4
Cal 1-4 deg. 180 179.5 180.5
Cal 1-4 deg. 180 179.5 180.5
Difference between angles 5
Cal 1-5 deg. 225 224.5 225.5
Cal 1-5 deg. 225 224.5 225.5
Difference between angles 6
Cal 1-6 deg. 270 269.5 270.5
Cal 1-6 deg. 270 269.5 270.5
Difference between angles 7
Cal 1-8 deg. 315 314.5 315.5
Cal 1-8 deg. 315 314.5 315.5
Injection quantity adjustment
Adjusting point
-
Rack position
11.4
Pump speed
r/min
700
700
700
Each cylinder's injection qty
mm3/st.
156
151.3
160.7
Basic
*
Fixing the rack
*
Standard for adjustment of the maximum variation between cylinders
*
Injection quantity adjustment_02
Adjusting point
C
Rack position
6.1+-0.5
Pump speed
r/min
225
225
225
Each cylinder's injection qty
mm3/st.
20
17
23
Fixing the rack
*
Standard for adjustment of the maximum variation between cylinders
*
Injection quantity adjustment_03
Adjusting point
A
Rack position
R1(11.4)
Pump speed
r/min
700
700
700
Average injection quantity
mm3/st.
156
155
157
Fixing the lever
*
Boost pressure
kPa
28
28
Boost pressure
mmHg
210
210
Injection quantity adjustment_04
Adjusting point
B
Rack position
R1(11.4)
Pump speed
r/min
1100
1100
1100
Average injection quantity
mm3/st.
164
157
171
Difference in delivery
mm3/st.
14
14
14
Fixing the lever
*
Boost pressure
kPa
28
28
Boost pressure
mmHg
210
210
Injection quantity adjustment_05
Adjusting point
D
Rack position
-
Pump speed
r/min
100
100
100
Average injection quantity
mm3/st.
130
90
170
Fixing the lever
*
Boost pressure
kPa
0
0
0
Boost pressure
mmHg
0
0
0
Boost compensator adjustment
Pump speed
r/min
650
650
650
Rack position
9.9
Boost pressure
kPa
5.3
5.3
5.3
Boost pressure
mmHg
40
40
40
Boost compensator adjustment_02
Pump speed
r/min
650
650
650
Rack position
10.8
Boost pressure
kPa
10.7
9.4
12
Boost pressure
mmHg
80
70
90
Boost compensator adjustment_03
Pump speed
r/min
650
650
650
Rack position
R1(11.4)
Boost pressure
kPa
14.7
8
21.4
Boost pressure
mmHg
110
60
160
Timer adjustment
Pump speed
r/min
950--
Advance angle
deg.
0
0
0
Load
3/4
Remarks
Start
Start
Timer adjustment_02
Pump speed
r/min
900
Advance angle
deg.
0.5
Load
3/4
Timer adjustment_03
Pump speed
r/min
1130
Advance angle
deg.
3.5
3
4
Load
4/4
Remarks
Finish
Finish
Test data Ex:
Governor adjustment
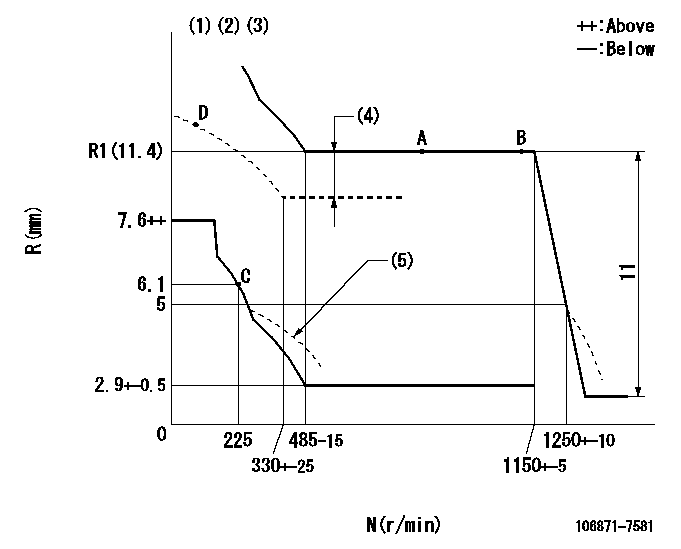
N:Pump speed
R:Rack position (mm)
(1)Lever ratio: RT
(2)Target shim dimension: TH
(3)Boost compensator cancel stroke: BSL
(4)Boost compensator stroke: BCL
(5)Damper spring setting: DL
----------
RT=1 TH=2.1mm BSL=1.6mm BCL=1.5+-0.1mm DL=4.3-0.2mm
----------
----------
RT=1 TH=2.1mm BSL=1.6mm BCL=1.5+-0.1mm DL=4.3-0.2mm
----------
Speed control lever angle

F:Full speed
----------
----------
a=18deg+-5deg
----------
----------
a=18deg+-5deg
0000000901

F:Full load
I:Idle
(1)Stopper bolt setting
----------
----------
a=10deg+-5deg b=31.5deg+-3deg
----------
----------
a=10deg+-5deg b=31.5deg+-3deg
Stop lever angle
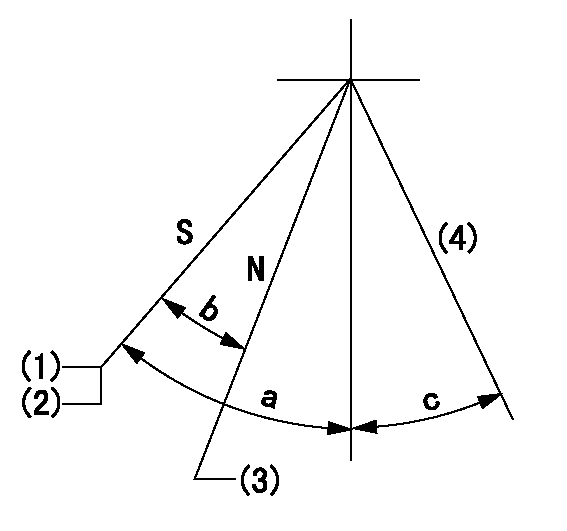
N:Engine manufacturer's normal use
S:Stop the pump.
(1)Rack position = aa
(2)Stopper bolt setting
(3)Rack position bb
(4)Free (at shipping)
----------
aa=4-0.5mm bb=14.6mm
----------
a=43deg+7deg-5deg b=30deg+-5deg c=(10.5deg)
----------
aa=4-0.5mm bb=14.6mm
----------
a=43deg+7deg-5deg b=30deg+-5deg c=(10.5deg)
0000001501 MICRO SWITCH
Adjustment of the micro-switch
Adjust the bolt to obtain the following lever position when the micro-switch is ON.
(1)Speed N1
(2)Rack position Ra
----------
N1=325+-5r/min Ra=5.6mm
----------
----------
N1=325+-5r/min Ra=5.6mm
----------
Timing setting

(1)Pump vertical direction
(2)Coupling's key groove position at No 1 cylinder's beginning of injection
(3)-
(4)-
----------
----------
a=(40deg)
----------
----------
a=(40deg)
Information:
3. Remove connecting rod caps (1) from the two connecting rods and push the pistons up until the rings are free of the cylinder liner.4. Remove the two pistons.5. Do the above steps again for the remainder of the pistons.Install Pistons
1. Turn the crankshaft until the bearing journals for the pistons to be installed are at bottom center.2. Put clean engine oil on the crankshaft journals and on the inside of the cylinder liners. Put clean engine oil on the piston rings and connecting rod bearings.3. Move the piston rings on the piston until the ring openings (gap) are approximately 180° apart.
Never install tool (A) (the ring compressor) without the use of the cylinder liner as a guide. Damage to the piston rings can be the result.
TYPICAL EXAMPLE4. Put tool (A) in position on the cylinder liner as shown. Put the connecting rod and piston in position in the same cylinder liner from which it was removed and into the ring compressor. Make sure the "V" mark on the piston is in alignment with the "V" mark on the cylinder block.5. Push the piston into position while the connecting rod is put into position over the crankshaft. 6. Put clean engine oil on bearings, bolt threads and surfaces of the nuts that make contact with the connecting rod caps. Put caps (1) in position on the connecting rods and install the nuts. Tighten the nuts to a torque of 30 3 lb.ft. (40 4 N m). Put a mark on each nut and the end of each bolt. Tighten the nuts 90° more.
When the connecting rod caps are installed, make sure the number on the side of the cap is next to and respective with the number on the side of the connecting rod.
7. Follow Steps 1 through 6 for the installation of the other pistons.end by:a) install oil pumpb) install cylinder head assemblyDisassemble And Assemble Pistons
start by:a) remove pistons 1. Remove keystone rings from the piston with tool (A). 2. Remove snap ring (3), piston pin (1) and connecting rod (2) from the piston.3. Clean the piston ring grooves on the old piston with an acceptable ring groove tool. For clearances on pistons and rings of earlier models, see PISTON AND RINGS in SPECIFICATIONS.4. See SPECIAL INSTRUCTIONS, Form SMHS7295 for USE OF PISTON PIN REMOVAL AND INSTALLATION TOOLS. Be sure to remove the bearings from the crankshaft end of connecting rod.5. Heat the connecting rod in an oven to a temperature of 350°-500°F (176°-260°C). Never use a direct flame to heat a connecting rod. 6. Put the connecting rod in position on tooling (B) for the regular rod. Use tooling (C) for the tapered rod. Put a new rod pin bearing in position. Make sure the rod pin bearing joint (4) is 90° from a center line through crankshaft and pin bearing bores.7. Remove the old rod pin bearing and install the new rod pin bearing with one operation. 8. Use a pin bearing machine
1. Turn the crankshaft until the bearing journals for the pistons to be installed are at bottom center.2. Put clean engine oil on the crankshaft journals and on the inside of the cylinder liners. Put clean engine oil on the piston rings and connecting rod bearings.3. Move the piston rings on the piston until the ring openings (gap) are approximately 180° apart.
Never install tool (A) (the ring compressor) without the use of the cylinder liner as a guide. Damage to the piston rings can be the result.
TYPICAL EXAMPLE4. Put tool (A) in position on the cylinder liner as shown. Put the connecting rod and piston in position in the same cylinder liner from which it was removed and into the ring compressor. Make sure the "V" mark on the piston is in alignment with the "V" mark on the cylinder block.5. Push the piston into position while the connecting rod is put into position over the crankshaft. 6. Put clean engine oil on bearings, bolt threads and surfaces of the nuts that make contact with the connecting rod caps. Put caps (1) in position on the connecting rods and install the nuts. Tighten the nuts to a torque of 30 3 lb.ft. (40 4 N m). Put a mark on each nut and the end of each bolt. Tighten the nuts 90° more.
When the connecting rod caps are installed, make sure the number on the side of the cap is next to and respective with the number on the side of the connecting rod.
7. Follow Steps 1 through 6 for the installation of the other pistons.end by:a) install oil pumpb) install cylinder head assemblyDisassemble And Assemble Pistons
start by:a) remove pistons 1. Remove keystone rings from the piston with tool (A). 2. Remove snap ring (3), piston pin (1) and connecting rod (2) from the piston.3. Clean the piston ring grooves on the old piston with an acceptable ring groove tool. For clearances on pistons and rings of earlier models, see PISTON AND RINGS in SPECIFICATIONS.4. See SPECIAL INSTRUCTIONS, Form SMHS7295 for USE OF PISTON PIN REMOVAL AND INSTALLATION TOOLS. Be sure to remove the bearings from the crankshaft end of connecting rod.5. Heat the connecting rod in an oven to a temperature of 350°-500°F (176°-260°C). Never use a direct flame to heat a connecting rod. 6. Put the connecting rod in position on tooling (B) for the regular rod. Use tooling (C) for the tapered rod. Put a new rod pin bearing in position. Make sure the rod pin bearing joint (4) is 90° from a center line through crankshaft and pin bearing bores.7. Remove the old rod pin bearing and install the new rod pin bearing with one operation. 8. Use a pin bearing machine