Information injection-pump assembly
BOSCH
9 400 619 459
9400619459
ZEXEL
106871-7400
1068717400
MITSUBISHI
ME090226
me090226
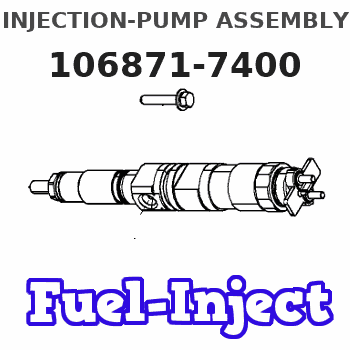
Rating:
Service parts 106871-7400 INJECTION-PUMP ASSEMBLY:
1.
_
7.
COUPLING PLATE
8.
_
9.
_
11.
Nozzle and Holder
ME066499
12.
Open Pre:MPa(Kqf/cm2)
15.
NOZZLE SET
Include in #1:
106871-7400
as INJECTION-PUMP ASSEMBLY
Cross reference number
BOSCH
9 400 619 459
9400619459
ZEXEL
106871-7400
1068717400
MITSUBISHI
ME090226
me090226
Zexel num
Bosch num
Firm num
Name
Calibration Data:
Adjustment conditions
Test oil
1404 Test oil ISO4113 or {SAEJ967d}
1404 Test oil ISO4113 or {SAEJ967d}
Test oil temperature
degC
40
40
45
Nozzle and nozzle holder
105780-8140
Bosch type code
EF8511/9A
Nozzle
105780-0000
Bosch type code
DN12SD12T
Nozzle holder
105780-2080
Bosch type code
EF8511/9
Opening pressure
MPa
17.2
Opening pressure
kgf/cm2
175
Injection pipe
Outer diameter - inner diameter - length (mm) mm 8-3-600
Outer diameter - inner diameter - length (mm) mm 8-3-600
Overflow valve
131424-4620
Overflow valve opening pressure
kPa
255
221
289
Overflow valve opening pressure
kgf/cm2
2.6
2.25
2.95
Tester oil delivery pressure
kPa
157
157
157
Tester oil delivery pressure
kgf/cm2
1.6
1.6
1.6
RED3 control unit part number
407910-2
470
RED3 rack sensor specifications
mm
15
Direction of rotation (viewed from drive side)
Right R
Right R
Injection timing adjustment
Direction of rotation (viewed from drive side)
Right R
Right R
Injection order
1-2-7-3-
4-5-6-8
Pre-stroke
mm
4.8
4.75
4.85
Beginning of injection position
Governor side NO.1
Governor side NO.1
Difference between angles 1
Cyl.1-2 deg. 45 44.5 45.5
Cyl.1-2 deg. 45 44.5 45.5
Difference between angles 2
Cal 1-7 deg. 90 89.5 90.5
Cal 1-7 deg. 90 89.5 90.5
Difference between angles 3
Cal 1-3 deg. 135 134.5 135.5
Cal 1-3 deg. 135 134.5 135.5
Difference between angles 4
Cal 1-4 deg. 180 179.5 180.5
Cal 1-4 deg. 180 179.5 180.5
Difference between angles 5
Cal 1-5 deg. 225 224.5 225.5
Cal 1-5 deg. 225 224.5 225.5
Difference between angles 6
Cal 1-6 deg. 270 269.5 270.5
Cal 1-6 deg. 270 269.5 270.5
Difference between angles 7
Cal 1-8 deg. 315 314.5 315.5
Cal 1-8 deg. 315 314.5 315.5
Injection quantity adjustment
Rack position
(12.9)
Vist
V
1.42
1.42
1.42
Pump speed
r/min
700
700
700
Each cylinder's injection qty
mm3/st.
156
151
161
Basic
*
Injection quantity adjustment_02
Rack position
(7.9)
Vist
V
2.4
2.3
2.5
Pump speed
r/min
225
225
225
Each cylinder's injection qty
mm3/st.
20
17
23
Test data Ex:
Governor adjustment

(1)Adjusting range
(2)Step response time
(N): Speed of the pump
(L): Load
(theta) Advance angle
(Srd1) Step response time 1
(Srd2) Step response time 2
1. Adjusting conditions for the variable timer
(1)Adjust the clearance between the pickup and the protrusion to L.
----------
L=1-0.2mm N2=800r/min C2=(8.8)deg t1=2.5--sec. t2=2.5--sec.
----------
N1=750++r/min P1=0kPa(0kgf/cm2) P2=392kPa(4kgf/cm2) C1=8.8+-0.3deg R01=0/4load R02=4/4load
----------
L=1-0.2mm N2=800r/min C2=(8.8)deg t1=2.5--sec. t2=2.5--sec.
----------
N1=750++r/min P1=0kPa(0kgf/cm2) P2=392kPa(4kgf/cm2) C1=8.8+-0.3deg R01=0/4load R02=4/4load
Speed control lever angle
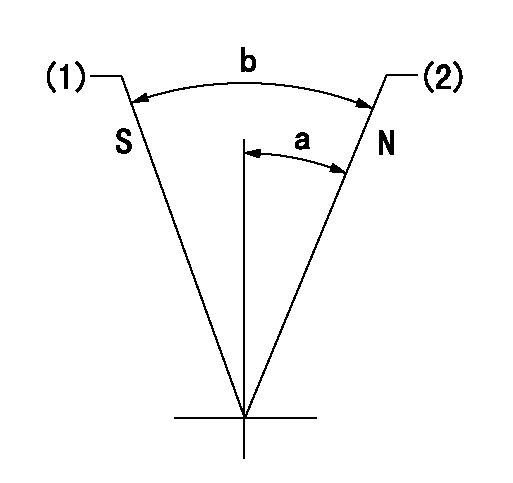
N:Pump normal
S:Stop the pump.
(1)Rack position = aa
(2)Rack position bb
----------
aa=1mm bb=16mm
----------
a=19deg+-5deg b=29deg+-5deg
----------
aa=1mm bb=16mm
----------
a=19deg+-5deg b=29deg+-5deg
0000000901

(1)Pump vertical direction
(2)Coupling's key groove position at No 1 cylinder's beginning of injection
(3)-
(4)-
----------
----------
a=(40deg)
----------
----------
a=(40deg)
Stop lever angle

(Rs) rack sensor specifications
(C/U) control unit part number
(V) Rack sensor output voltage
(R) Rack position (mm)
1. Confirming governor output characteristics (rack 15 mm, span 6 mm)
(1)When the output voltages of the rack sensor are V1 and V2, check that the rack positions R1 and R2 in the table above are satisfied.
----------
----------
----------
----------
Information:
1. Preparation of vehicle for fuel consumption test (consult dynamometer manufacturer's operating instructions for specific details on correct operation). Always perform the Primary Engine Test procedure before vehicle is installed on chassis dynamometer.a. Place vehicle on the chassis dynamometer. Tie the vehicle in a way that will not add any load to the drive wheels. Do not pull wheels down into dynamometer drive rolls. Check the radiator coolant level, crankcase oil level, tire pressure, tire condition, remove rocks from the tire tread and connect exhaust system.
Recapped tires should be run on a chassis dynamometer only at the customer's own risk.
b. The maximum acceptable fuel rate must be calculated for the customer's engine by use of the formula that follows: Find the rated brake specific fuel consumption (lb-bhp/hr) from the RACK SETTING INFORMATION and add .010 in. manufacturing tolerance. Multiply this value by the advertised engine horsepower (plus 3% manf. tol.) and divide by the density of the fuel (lbs/gal).c. Calculate the allowable limits that the customer can expect from his engine and present these figures to him. Caterpillar engines are rated with the conditions that follow: Measure and record these variables. Advertised engine bhp (less 3% manufacturing tolerance) can then be corrected to test conditions by use of procedure and correction tables found in Special Instruction GEG01024.2. Operate vehicle at 60% of rated speed with moderate load until oil and coolant temperatures reach their normal range for operation.
If there is a heavy vibration, drive shaft whip, tire bounce, etc., do not continue with dynamometer test until cause of the problem is corrected. Engines that have had new internal parts installed should be operated on a run-in schedule before operation at full load.
Put transmission in direct gear and the differential in the highest speed ratio. Operate vehicle at maximum engine speed and increase chassis dynamometer load until a speed of 50 rpm less than rated speed is reached (continuity light should be on). Maintain this speed for one minute and record the engine speed, wheel horsepower and fuel rate.3. If the fuel rate and the wheel horsepower are both acceptable, then the engine is not the cause of the complaint, or the complaint is not valid. Refer to section PROBLEM WITH VEHICLE OR VEHICLE OPERATION.4. If the
Recapped tires should be run on a chassis dynamometer only at the customer's own risk.
b. The maximum acceptable fuel rate must be calculated for the customer's engine by use of the formula that follows: Find the rated brake specific fuel consumption (lb-bhp/hr) from the RACK SETTING INFORMATION and add .010 in. manufacturing tolerance. Multiply this value by the advertised engine horsepower (plus 3% manf. tol.) and divide by the density of the fuel (lbs/gal).c. Calculate the allowable limits that the customer can expect from his engine and present these figures to him. Caterpillar engines are rated with the conditions that follow: Measure and record these variables. Advertised engine bhp (less 3% manufacturing tolerance) can then be corrected to test conditions by use of procedure and correction tables found in Special Instruction GEG01024.2. Operate vehicle at 60% of rated speed with moderate load until oil and coolant temperatures reach their normal range for operation.
If there is a heavy vibration, drive shaft whip, tire bounce, etc., do not continue with dynamometer test until cause of the problem is corrected. Engines that have had new internal parts installed should be operated on a run-in schedule before operation at full load.
Put transmission in direct gear and the differential in the highest speed ratio. Operate vehicle at maximum engine speed and increase chassis dynamometer load until a speed of 50 rpm less than rated speed is reached (continuity light should be on). Maintain this speed for one minute and record the engine speed, wheel horsepower and fuel rate.3. If the fuel rate and the wheel horsepower are both acceptable, then the engine is not the cause of the complaint, or the complaint is not valid. Refer to section PROBLEM WITH VEHICLE OR VEHICLE OPERATION.4. If the