Information injection-pump assembly
BOSCH
F 01G 09U 0A5
f01g09u0a5
ZEXEL
106871-5561
1068715561
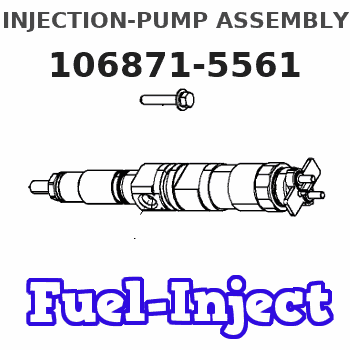
Rating:
Service parts 106871-5561 INJECTION-PUMP ASSEMBLY:
1.
_
7.
COUPLING PLATE
8.
_
9.
_
11.
Nozzle and Holder
16600-97119
12.
Open Pre:MPa(Kqf/cm2)
15.7{160}/22.6{230}
14.
NOZZLE
Include in #1:
106871-5561
as INJECTION-PUMP ASSEMBLY
Cross reference number
BOSCH
F 01G 09U 0A5
f01g09u0a5
ZEXEL
106871-5561
1068715561
Zexel num
Bosch num
Firm num
Name
Calibration Data:
Adjustment conditions
Test oil
1404 Test oil ISO4113 or {SAEJ967d}
1404 Test oil ISO4113 or {SAEJ967d}
Test oil temperature
degC
40
40
45
Nozzle and nozzle holder
105780-8250
Bosch type code
1 688 901 101
Nozzle
105780-0120
Bosch type code
1 688 901 990
Nozzle holder
105780-2190
Opening pressure
MPa
20.7
Opening pressure
kgf/cm2
211
Injection pipe
Outer diameter - inner diameter - length (mm) mm 8-3-600
Outer diameter - inner diameter - length (mm) mm 8-3-600
Overflow valve
131425-0120
Overflow valve opening pressure
kPa
157
123
191
Overflow valve opening pressure
kgf/cm2
1.6
1.25
1.95
Tester oil delivery pressure
kPa
255
255
255
Tester oil delivery pressure
kgf/cm2
2.6
2.6
2.6
RED3 control unit part number
407910-3
960
RED3 rack sensor specifications
mm
19
Direction of rotation (viewed from drive side)
Right R
Right R
Injection timing adjustment
Direction of rotation (viewed from drive side)
Right R
Right R
Injection order
1-8-7-5-
4-3-6-2
Pre-stroke
mm
4.7
4.67
4.73
Beginning of injection position
Governor side NO.1
Governor side NO.1
Difference between angles 1
Cal 1-8 deg. 45 44.75 45.25
Cal 1-8 deg. 45 44.75 45.25
Difference between angles 2
Cal 1-7 deg. 90 89.75 90.25
Cal 1-7 deg. 90 89.75 90.25
Difference between angles 3
Cal 1-5 deg. 135 134.75 135.25
Cal 1-5 deg. 135 134.75 135.25
Difference between angles 4
Cal 1-4 deg. 180 179.75 180.25
Cal 1-4 deg. 180 179.75 180.25
Difference between angles 5
Cal 1-3 deg. 225 224.75 225.25
Cal 1-3 deg. 225 224.75 225.25
Difference between angles 6
Cal 1-6 deg. 270 269.75 270.25
Cal 1-6 deg. 270 269.75 270.25
Difference between angles 7
Cyl.1-2 deg. 315 314.75 315.25
Cyl.1-2 deg. 315 314.75 315.25
Injection quantity adjustment
Rack position
(13.4)
Vist
V
1.85
1.85
1.85
Pump speed
r/min
650
650
650
Average injection quantity
mm3/st.
137
135
139
Max. variation between cylinders
%
0
-4
4
Basic
*
Injection quantity adjustment_02
Rack position
(8.4)
Vist
V
2.6
2.5
2.7
Pump speed
r/min
335
335
335
Average injection quantity
mm3/st.
14
12
16
Max. variation between cylinders
%
0
-10
10
Test data Ex:
Governor adjustment

(1)Adjusting range
(2)Step response time
(N): Speed of the pump
(L): Load
(theta) Advance angle
(Srd1) Step response time 1
(Srd2) Step response time 2
1. Adjusting conditions for the variable timer
(1)Adjust the clearance between the pickup and the protrusion to L.
----------
L=1-0.2mm N4=800r/min C4=(9deg) t1=1.7--sec. t2=1.7--sec.
----------
N1=400r/min N2=1000++r/min N3=- C1=9+-0.3deg C2=3.5++deg C3=- P1=0kPa(0kgf/cm2) P2=294kPa(3kgf/cm2) P3=392kPa(4kgf/cm2) R01=0/4load R02=4/4load R03=4/4load
----------
L=1-0.2mm N4=800r/min C4=(9deg) t1=1.7--sec. t2=1.7--sec.
----------
N1=400r/min N2=1000++r/min N3=- C1=9+-0.3deg C2=3.5++deg C3=- P1=0kPa(0kgf/cm2) P2=294kPa(3kgf/cm2) P3=392kPa(4kgf/cm2) R01=0/4load R02=4/4load R03=4/4load
Speed control lever angle

N:Pump normal
S:Stop the pump.
(1)Rack position = aa
(2)Rack position bb
----------
aa=20mm bb=1mm
----------
a=27deg+-5deg b=37deg+-5deg
----------
aa=20mm bb=1mm
----------
a=27deg+-5deg b=37deg+-5deg
0000000901

(1)Pump vertical direction
(2)Position of the coupling's key groove at the beginning of injection of the No. 8 cylinder.
(3)-
(4)-
----------
----------
a=(90deg)
----------
----------
a=(90deg)
Stop lever angle
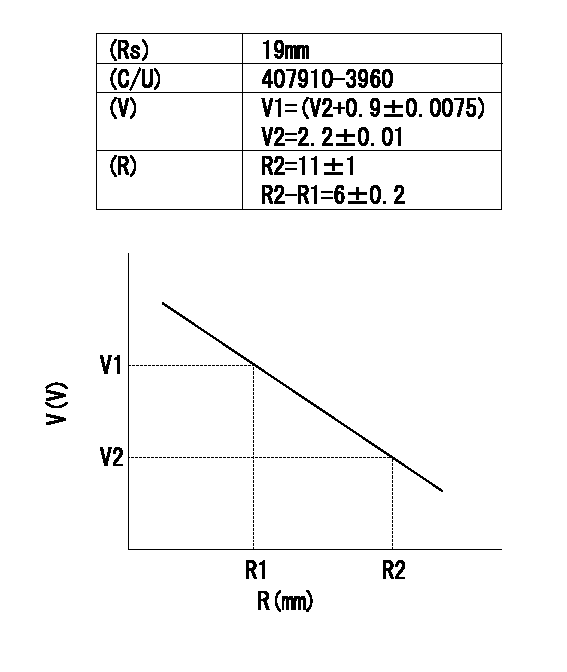
(Rs) rack sensor specifications
(C/U) control unit part number
(V) Rack sensor output voltage
(R) Rack position (mm)
1. Confirming governor output characteristics (rack 19 mm, span 6 mm)
(1)When the output voltages of the rack sensor are V1 and V2, check that the rack positions R1 and R2 in the table above are satisfied.
----------
----------
----------
----------
Information:
Illustration 74 g02026337 Appendix D
Cleaned Filter Specification
Note: Scope: The following steps determine a properly cleaned Caterpillar filter.Note: This specification applies to filters that were cleaned of ash only. This specification is only valid subsequent to the "Recommended Cleaning Procedure". This specification should not be used to determine if soot filled filters are properly cleaned. All filters must be baked appropriately using the "Recommended Cleaning Procedure" prior to application of this specification.HEALTH AND SAFETY
Wear goggles, gloves, protective clothing, and a National Institute for Occupational Safety and Health (NIOSH) approved P95 or N95 half-face respirator when handling a used Diesel Particulate Filter or Catalytic Converter Muffler. Failure to do so could result in personal injury.
Adhere to all local Health and Safety rules and regulations. Use all the personal protective equipment listed below:
Respirator
Safety shoes
Safety glasses
Latex gloves
Lab coatRESOURCESNecessary equipment:
38 cm (15 inch) long by 0.9 mm (0.04 inch) thick stainless steel probe for "200 cpsi" (Cells/Square inch) filters
Tape measureMETHODEvaluation of a cleaned filter:Note: A filter MUST meet all criteria in this section below to be considered clean.
Inspect both inlet and outlet surfaces for oil/fuel contamination, gouges and/or cracks. No cracks may be visible. Gouges may not be exceed 4.0 mm (0.15 inch) deep.
There must be no filter movement within the filters banding. This movement is defined as the substrate moving past the bent-over flange. The filter must be even or below the bent-over flange.
There must not be any signs of the steel fiber ring coming loose or any mat material (cottony gauze) slipping past the filter. See Illustration 75 below.
The flanges are not damaged beyond repair.
There are no dents deeper than 6.4 mm (0.25 inch) in the outer can of the filter and the outer can is not cracked, torn or otherwise breached.
No more than 20 cells are allowed to be damaged (showing soot) on the outlet face of the filter. Refer to Illustrations 76 and 77.
Inspect the ash depth in the cells using the "Check Cell Depth" instructions below.
Illustration 75 g02026392
Proper placement of the filter within the banding
(1) Outside Can
(2) Bent-over flange
(3) Steel fiber ring
(4) Mat material
(5) FilterNote: Filter must be below the bent over-flange (2).
Illustration 76 g02026398
Acceptable filter with less than 20 damaged cells
Illustration 77 g02026399
Unacceptable filter with too many damaged cells
Check Cell Depth
Check cell depth by dropping the stainless steel probe into a cell location noted by a dot in Illustration 78 below.
Lightly tap the probe with a finger until the probe does not travel into the cell any further. Mark the probe to record the depth.
Illustration 78 g02026405
Measure the distance from the tip of the probe which entered the cell to the mark made on the probe. This distance is the cell depth. Repeat this step 17 times per Illustration 78.
If the probe travels a minimum of 28.6 cm (11.25 inch) in all cells, the filter is considered clean.
If the probe encounters heavy resistance in