Information injection-pump assembly
BOSCH
F 01G 09U 09X
f01g09u09x
ZEXEL
106871-5410
1068715410
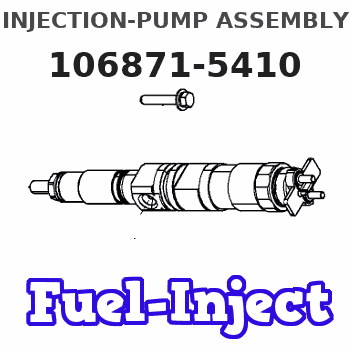
Rating:
Service parts 106871-5410 INJECTION-PUMP ASSEMBLY:
1.
_
7.
COUPLING PLATE
8.
_
9.
_
11.
Nozzle and Holder
16600-97119
12.
Open Pre:MPa(Kqf/cm2)
15.7{160}/22.6{230}
14.
NOZZLE
Include in #1:
106871-5410
as INJECTION-PUMP ASSEMBLY
Cross reference number
BOSCH
F 01G 09U 09X
f01g09u09x
ZEXEL
106871-5410
1068715410
Zexel num
Bosch num
Firm num
Name
Calibration Data:
Adjustment conditions
Test oil
1404 Test oil ISO4113 or {SAEJ967d}
1404 Test oil ISO4113 or {SAEJ967d}
Test oil temperature
degC
40
40
45
Nozzle and nozzle holder
105780-8250
Bosch type code
1 688 901 101
Nozzle
105780-0120
Bosch type code
1 688 901 990
Nozzle holder
105780-2190
Opening pressure
MPa
20.7
Opening pressure
kgf/cm2
211
Injection pipe
Outer diameter - inner diameter - length (mm) mm 8-3-600
Outer diameter - inner diameter - length (mm) mm 8-3-600
Overflow valve
131425-0120
Overflow valve opening pressure
kPa
157
123
191
Overflow valve opening pressure
kgf/cm2
1.6
1.25
1.95
Tester oil delivery pressure
kPa
255
255
255
Tester oil delivery pressure
kgf/cm2
2.6
2.6
2.6
RED3 control unit part number
407910-3
960
RED3 rack sensor specifications
mm
19
Direction of rotation (viewed from drive side)
Right R
Right R
Injection timing adjustment
Direction of rotation (viewed from drive side)
Right R
Right R
Injection order
1-8-7-5-
4-3-6-2
Pre-stroke
mm
4.7
4.67
4.73
Beginning of injection position
Governor side NO.1
Governor side NO.1
Difference between angles 1
Cal 1-8 deg. 45 44.75 45.25
Cal 1-8 deg. 45 44.75 45.25
Difference between angles 2
Cal 1-7 deg. 90 89.75 90.25
Cal 1-7 deg. 90 89.75 90.25
Difference between angles 3
Cal 1-5 deg. 135 134.75 135.25
Cal 1-5 deg. 135 134.75 135.25
Difference between angles 4
Cal 1-4 deg. 180 179.75 180.25
Cal 1-4 deg. 180 179.75 180.25
Difference between angles 5
Cal 1-3 deg. 225 224.75 225.25
Cal 1-3 deg. 225 224.75 225.25
Difference between angles 6
Cal 1-6 deg. 270 269.75 270.25
Cal 1-6 deg. 270 269.75 270.25
Difference between angles 7
Cyl.1-2 deg. 315 314.75 315.25
Cyl.1-2 deg. 315 314.75 315.25
Injection quantity adjustment
Rack position
(13.4)
Vist
V
1.85
1.85
1.85
Pump speed
r/min
650
650
650
Average injection quantity
mm3/st.
137
135
139
Max. variation between cylinders
%
0
-4
4
Basic
*
Injection quantity adjustment_02
Rack position
(8.4)
Vist
V
2.6
2.5
2.7
Pump speed
r/min
335
335
335
Average injection quantity
mm3/st.
14
12
16
Max. variation between cylinders
%
0
-10
10
Governor adjustment
Pump speed
r/min
750--
Advance angle
deg.
0
0
0
Remarks
Q = 155+-2 (mm3/st) / N = 650 (r/min), beginning of effect
Q = 155+-2 (mm3/st) / N = 650 (r/min), beginning of effect
Governor adjustment_02
Pump speed
r/min
700
Advance angle
deg.
0.3
Remarks
Q=155+-2(mm3/st)/N=650 (r/min)
Q=155+-2(mm3/st)/N=650 (r/min)
Governor adjustment_03
Pump speed
r/min
(750)
Advance angle
deg.
2
1.8
2.2
Remarks
Q=155+-2(mm3/st)/N=650 (r/min)
Q=155+-2(mm3/st)/N=650 (r/min)
Governor adjustment_04
Pump speed
r/min
850
Advance angle
deg.
2
1.7
2.3
Remarks
Q=87+-2(mm3/st)/N=850(r/min)
Q=87+-2(mm3/st)/N=850(r/min)
Governor adjustment_05
Pump speed
r/min
1080
Advance angle
deg.
7
6.7
7.3
Remarks
Q = 146+-2 (mm3/st) / N = 1100 (r/min), end of effect
Q = 146+-2 (mm3/st) / N = 1100 (r/min), end of effect
Test data Ex:
Speed control lever angle
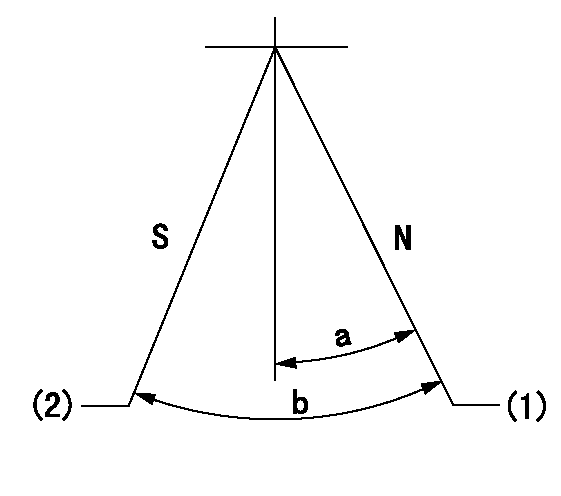
N:Pump normal
S:Stop the pump.
(1)Rack position = aa
(2)Rack position bb
----------
aa=20mm bb=1mm
----------
a=20deg+-5deg b=37deg+-5deg
----------
aa=20mm bb=1mm
----------
a=20deg+-5deg b=37deg+-5deg
0000000901

(1)Pump vertical direction
(2)Position of the coupling's key groove at the beginning of injection of the No. 8 cylinder.
(3)-
(4)-
----------
----------
a=(90deg)
----------
----------
a=(90deg)
Stop lever angle
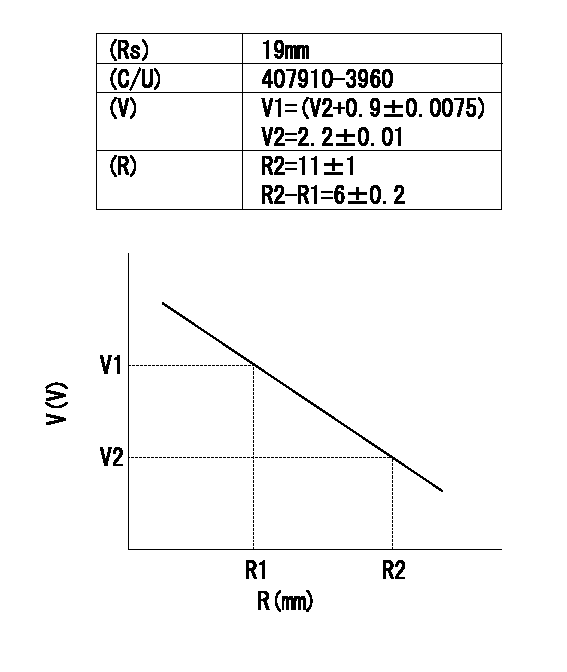
(Rs) rack sensor specifications
(C/U) control unit part number
(V) Rack sensor output voltage
(R) Rack position (mm)
1. Confirming governor output characteristics (rack 19 mm, span 6 mm)
(1)When the output voltages of the rack sensor are V1 and V2, check that the rack positions R1 and R2 in the table above are satisfied.
----------
----------
----------
----------
Information:
Parts Needed
6 - 6I2538 Clip Add injectors and related seals if clip is broken in more than three pieces. Add 336044 O-Ring Seal if thrust pad o-ring is damaged.
Action Required
Parts Stock
Remove all of the following injector groups from parts stock. Rework as described in the attached procedure and return to stock.
4P1410 Injector Group4P1420 Injector Group4P2810 Injector Group4P2820 Injector Group4P9510 Injector Group4P9520 Injector Group4P9610 Injector Group4P9620 Injector Group0R3177 Injector Group0R3178 Injector Group0R3400 Injector GroupAffected Product
Rework the injector groups as described in the attached procedure.
Service Claim Allowances
Parts Stock
Submit one claim for all injector groups removed from parts stock and reworked. List the labor to repair each injector on a separate labor line. A maximum of .2 hours labor per fuel injector will be allowed to remove and install the clip.
Affected Product
Parts Disposition
Handle the parts in accordance with your Warranty Bulletin on warranty parts handling.
Attach.
(1-Rework Procedure)Rework Procedure
Parts Stock or Off Engine
Illustration 1 - 9U5300 Unit Injector Spring Compressor Group
Illustration 2 - Compressor Group In Bench Vice
Illustration 3 - Use caution when handling injectors with missing clips. Loose springs and retainers will allow ball to come loose and fall into the engine.1. Remove injectors from packaging and inspect for a paint stripe across the top face of the spring retainer (either yellow or red). The paint stripe indicates the unit injector has been reworked previously. If a clip has failed and the spring/tappet/plunger are loose, use care during injector removal. The plunger retention ball (see Illustration 3) can drop out and fall into the cylinder/engine.
2. Install service tool in a bench vice as shown in Illustration 2 (position to allow for horizontal installation of injector).3. Use an o-ring pick to remove the o-ring from the injector spring retainer. Remove the rocker arm thrust pad.4. Install the injector in the 9U5300 Unit Injector Spring Compressor Group. Tighten the 5P0541 Nut to compress the spring enough to allow removal of the clip (the clip works like a valve keeper).5. Use a small magnet (pencil size works best) and a suitable clip removal tool to remove the oil clip from the injector. Do not release tension on the spring until a new clip is installed. Releasing tension before a new clip is installed will cause the injector will come apart.
6. Injectors removed from engines only. Inspect the clip that was removed. If the clip is broken in more than three (3) pieces (or if you suspect small pieces have fallen into the injector) the unit injector must be replaced.7. Install a new 6I2538 clip and remove injector from spring compressor group.8. Install thrust pad and thrust pad retaining o-ring. If the thrust pad retaining o-ring is damaged install a new 336044 O-Ring Seal.
9. Mark across the top face of the spring retainer with a yellow paint stripe.10. Repackage new parts and mark "3X" on the box.Affected Product
1. Check for 3X stamped on the block next to the serial number plate. If the block has been stamped do not proceed with the rework unless suspect injectors
6 - 6I2538 Clip Add injectors and related seals if clip is broken in more than three pieces. Add 336044 O-Ring Seal if thrust pad o-ring is damaged.
Action Required
Parts Stock
Remove all of the following injector groups from parts stock. Rework as described in the attached procedure and return to stock.
4P1410 Injector Group4P1420 Injector Group4P2810 Injector Group4P2820 Injector Group4P9510 Injector Group4P9520 Injector Group4P9610 Injector Group4P9620 Injector Group0R3177 Injector Group0R3178 Injector Group0R3400 Injector GroupAffected Product
Rework the injector groups as described in the attached procedure.
Service Claim Allowances
Parts Stock
Submit one claim for all injector groups removed from parts stock and reworked. List the labor to repair each injector on a separate labor line. A maximum of .2 hours labor per fuel injector will be allowed to remove and install the clip.
Affected Product
Parts Disposition
Handle the parts in accordance with your Warranty Bulletin on warranty parts handling.
Attach.
(1-Rework Procedure)Rework Procedure
Parts Stock or Off Engine
Illustration 1 - 9U5300 Unit Injector Spring Compressor Group
Illustration 2 - Compressor Group In Bench Vice
Illustration 3 - Use caution when handling injectors with missing clips. Loose springs and retainers will allow ball to come loose and fall into the engine.1. Remove injectors from packaging and inspect for a paint stripe across the top face of the spring retainer (either yellow or red). The paint stripe indicates the unit injector has been reworked previously. If a clip has failed and the spring/tappet/plunger are loose, use care during injector removal. The plunger retention ball (see Illustration 3) can drop out and fall into the cylinder/engine.
2. Install service tool in a bench vice as shown in Illustration 2 (position to allow for horizontal installation of injector).3. Use an o-ring pick to remove the o-ring from the injector spring retainer. Remove the rocker arm thrust pad.4. Install the injector in the 9U5300 Unit Injector Spring Compressor Group. Tighten the 5P0541 Nut to compress the spring enough to allow removal of the clip (the clip works like a valve keeper).5. Use a small magnet (pencil size works best) and a suitable clip removal tool to remove the oil clip from the injector. Do not release tension on the spring until a new clip is installed. Releasing tension before a new clip is installed will cause the injector will come apart.
6. Injectors removed from engines only. Inspect the clip that was removed. If the clip is broken in more than three (3) pieces (or if you suspect small pieces have fallen into the injector) the unit injector must be replaced.7. Install a new 6I2538 clip and remove injector from spring compressor group.8. Install thrust pad and thrust pad retaining o-ring. If the thrust pad retaining o-ring is damaged install a new 336044 O-Ring Seal.
9. Mark across the top face of the spring retainer with a yellow paint stripe.10. Repackage new parts and mark "3X" on the box.Affected Product
1. Check for 3X stamped on the block next to the serial number plate. If the block has been stamped do not proceed with the rework unless suspect injectors