Information injection-pump assembly
ZEXEL
106871-3220
1068713220
HINO
220002143B
220002143b
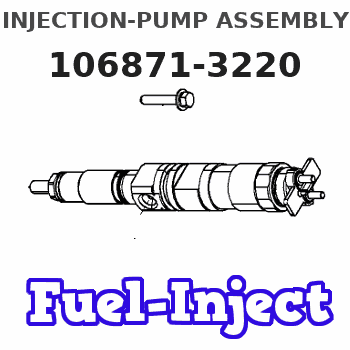
Rating:
Service parts 106871-3220 INJECTION-PUMP ASSEMBLY:
1.
_
7.
COUPLING PLATE
8.
_
9.
_
11.
Nozzle and Holder
23600-1212
12.
Open Pre:MPa(Kqf/cm2)
21.6{220}
15.
NOZZLE SET
Include in #1:
106871-3220
as INJECTION-PUMP ASSEMBLY
Cross reference number
ZEXEL
106871-3220
1068713220
HINO
220002143B
220002143b
Zexel num
Bosch num
Firm num
Name
Calibration Data:
Adjustment conditions
Test oil
1404 Test oil ISO4113 or {SAEJ967d}
1404 Test oil ISO4113 or {SAEJ967d}
Test oil temperature
degC
40
40
45
Nozzle and nozzle holder
105780-8140
Bosch type code
EF8511/9A
Nozzle
105780-0000
Bosch type code
DN12SD12T
Nozzle holder
105780-2080
Bosch type code
EF8511/9
Opening pressure
MPa
17.2
Opening pressure
kgf/cm2
175
Injection pipe
Outer diameter - inner diameter - length (mm) mm 8-3-600
Outer diameter - inner diameter - length (mm) mm 8-3-600
Overflow valve
134424-1020
Overflow valve opening pressure
kPa
127
107
147
Overflow valve opening pressure
kgf/cm2
1.3
1.1
1.5
Tester oil delivery pressure
kPa
157
157
157
Tester oil delivery pressure
kgf/cm2
1.6
1.6
1.6
Direction of rotation (viewed from drive side)
Right R
Right R
Injection timing adjustment
Direction of rotation (viewed from drive side)
Right R
Right R
Injection order
1-8-6-2-
7-5-4-3
Pre-stroke
mm
4
3.94
4
Beginning of injection position
Drive side NO.1
Drive side NO.1
Difference between angles 1
Cal 1-8 deg. 45 44.75 45.25
Cal 1-8 deg. 45 44.75 45.25
Difference between angles 2
Cal 1-6 deg. 90 89.75 90.25
Cal 1-6 deg. 90 89.75 90.25
Difference between angles 3
Cyl.1-2 deg. 135 134.75 135.25
Cyl.1-2 deg. 135 134.75 135.25
Difference between angles 4
Cal 1-7 deg. 180 179.75 180.25
Cal 1-7 deg. 180 179.75 180.25
Difference between angles 5
Cal 1-5 deg. 225 224.75 225.25
Cal 1-5 deg. 225 224.75 225.25
Difference between angles 6
Cal 1-4 deg. 270 269.75 270.25
Cal 1-4 deg. 270 269.75 270.25
Difference between angles 7
Cal 1-3 deg. 315 314.75 315.25
Cal 1-3 deg. 315 314.75 315.25
Injection quantity adjustment
Adjusting point
A
Rack position
9.1
Pump speed
r/min
500
500
500
Average injection quantity
mm3/st.
109
106
112
Max. variation between cylinders
%
0
-4
4
Fixing the lever
*
Injection quantity adjustment_02
Adjusting point
B
Rack position
9.1
Pump speed
r/min
700
700
700
Average injection quantity
mm3/st.
110.5
108.5
112.5
Max. variation between cylinders
%
0
-2
2
Basic
*
Fixing the lever
*
Injection quantity adjustment_03
Adjusting point
C
Rack position
9.6
Pump speed
r/min
1200
1200
1200
Average injection quantity
mm3/st.
125.5
122.5
128.5
Max. variation between cylinders
%
0
-4
4
Fixing the lever
*
Injection quantity adjustment_04
Adjusting point
D
Rack position
6.4+-0.5
Pump speed
r/min
225
225
225
Average injection quantity
mm3/st.
13.7
10.7
16.7
Max. variation between cylinders
%
0
-15
15
Fixing the rack
*
Injection quantity adjustment_05
Adjusting point
E
Rack position
-
Pump speed
r/min
50
50
50
Average injection quantity
mm3/st.
115
115
135
Fixing the lever
*
Remarks
After startup boost setting
After startup boost setting
Injection quantity adjustment_06
Adjusting point
F
Rack position
-
Pump speed
r/min
1000
1000
1000
Average injection quantity
mm3/st.
0
0
0
Fixing the lever
*
Timer adjustment
Pump speed
r/min
950
Advance angle
deg.
0.4
Timer adjustment_02
Pump speed
r/min
1000
Advance angle
deg.
0.7
0.2
1.2
Timer adjustment_03
Pump speed
r/min
1050
Advance angle
deg.
1.6
1.1
2.1
Timer adjustment_04
Pump speed
r/min
1125
Advance angle
deg.
3
2.7
3.3
Remarks
Finish
Finish
Test data Ex:
Governor adjustment
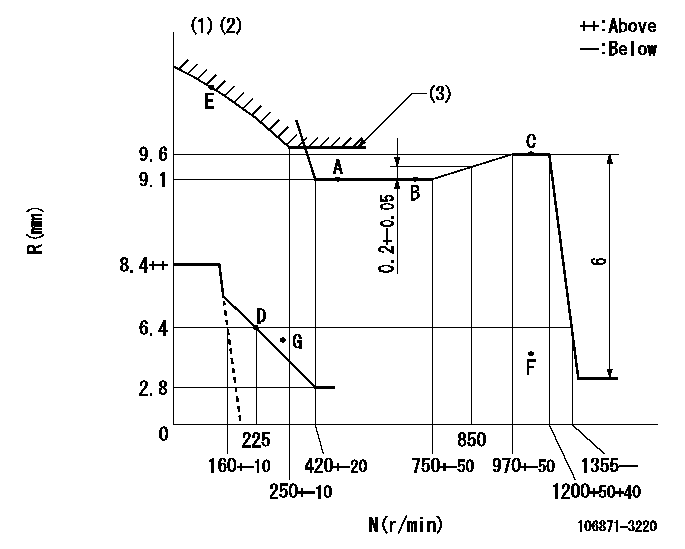
N:Pump speed
R:Rack position (mm)
(1)Beginning of damper spring operation: DL
(2)Set idle at point G (N = N1, R = R1) and confirm that the fuel injection quantity at point F (N = N2) does not exceed Q1.
(3)Excess fuel setting for starting: SXL
----------
DL=5.4-0.2mm N1=300r/min R1=5.4mm N2=1000r/min Q1=0mm3/st SXL=10.2+0.2mm
----------
----------
DL=5.4-0.2mm N1=300r/min R1=5.4mm N2=1000r/min Q1=0mm3/st SXL=10.2+0.2mm
----------
Speed control lever angle

F:Full speed
----------
----------
a=4deg+-5deg
----------
----------
a=4deg+-5deg
0000000901

F:Full load
I:Idle
(1)Stopper bolt setting
----------
----------
a=34deg+-5deg b=34deg+-3deg
----------
----------
a=34deg+-5deg b=34deg+-3deg
Stop lever angle

N:Pump normal
S:Stop the pump.
----------
----------
a=15deg+-5deg b=64deg+-5deg
----------
----------
a=15deg+-5deg b=64deg+-5deg
0000001501 MICRO SWITCH
Switch adjustment
Adjust the bolt so that the lower lever position is obtained when the switch is turned ON.
(1)Speed N1
(2)Rack position Ra
----------
N1=325-25r/min Ra=6.4mm
----------
----------
N1=325-25r/min Ra=6.4mm
----------
Information:
Use Again - if wear on contact surfaces cannot be felt with a seal pick.
Illustration 46 g06346577
Rack control and limiting sleeve.
Use Again - if wear on contact surfaces cannot be felt with a seal pick.Riser Shaft and Pin
Illustration 47 g06346580
Riser shaft.
Use Again - if there is no wear step on the shaft, which can be felt with a seal pick. If a step is present, it will generally occur near the center of the shaft.
Illustration 48 g06346583
Normal wear on pin at end of riser shaft.
Use Again
Illustration 49 g06346588
Pin with material eroded away near the center relief.
Do Not Use AgainFlyweight and Dowel
Illustration 50 g06346593
Flyweight toe with gouges near dowel hole.
Do Not Use Again - if wear marks can be felt with a seal pick.
Illustration 51 g06346599
Flyweight toe wear.
Do Not Use Again
Illustration 52 g06346602
Flyweight toe wear.
Do Not Use Again - if there are any signs of "flat spots". Worn flyweight toes may be highly polished so that flat spots are difficult to feel. Hold the flyweight toe surface in bright light and watch for changes in reflection in worn areas. Use a new flyweight toe for comparison.
Illustration 53 g06346609
Acceptable wear on flyweight dowel.
Use Again - if wear cannot be felt with a seal pick.
Illustration 54 g06346611
Heavy wear on flyweight dowel.
Do Not Use AgainNote: Examine the dowel seating area on the flyweight carrier. If there is any apparent wear, reinstall dowels in the unused positions, 90 degrees from original position.Bearing Assembly
Illustration 55 g06346614
The bearing (white collar) shown in position on the FARC diaphragm retainer (Type V, VI, and VII Governors) shows wear.
Do Not Use AgainGovernor Spring Seat
Illustration 56 g06346615
Governor spring seat with typical wear.
Use Again - if there are no gouges to surfaces (1) on the spring seating area.Spring Pack
Illustration 57 g06346618
End view of governor spring pack.
Use Again - after realignment.Note the off-center position of the internal springs with respect to the outside spring. This can cause governor instability, which results in surging. Rotate the springs on their seat so that the inner springs are aligned (centered) with respect to the outer spring. Remove sharp edges (A) from the inside diameter of the flat surface on the springs to ensure springs seat properly.
Illustration 46 g06346577
Rack control and limiting sleeve.
Use Again - if wear on contact surfaces cannot be felt with a seal pick.Riser Shaft and Pin
Illustration 47 g06346580
Riser shaft.
Use Again - if there is no wear step on the shaft, which can be felt with a seal pick. If a step is present, it will generally occur near the center of the shaft.
Illustration 48 g06346583
Normal wear on pin at end of riser shaft.
Use Again
Illustration 49 g06346588
Pin with material eroded away near the center relief.
Do Not Use AgainFlyweight and Dowel
Illustration 50 g06346593
Flyweight toe with gouges near dowel hole.
Do Not Use Again - if wear marks can be felt with a seal pick.
Illustration 51 g06346599
Flyweight toe wear.
Do Not Use Again
Illustration 52 g06346602
Flyweight toe wear.
Do Not Use Again - if there are any signs of "flat spots". Worn flyweight toes may be highly polished so that flat spots are difficult to feel. Hold the flyweight toe surface in bright light and watch for changes in reflection in worn areas. Use a new flyweight toe for comparison.
Illustration 53 g06346609
Acceptable wear on flyweight dowel.
Use Again - if wear cannot be felt with a seal pick.
Illustration 54 g06346611
Heavy wear on flyweight dowel.
Do Not Use AgainNote: Examine the dowel seating area on the flyweight carrier. If there is any apparent wear, reinstall dowels in the unused positions, 90 degrees from original position.Bearing Assembly
Illustration 55 g06346614
The bearing (white collar) shown in position on the FARC diaphragm retainer (Type V, VI, and VII Governors) shows wear.
Do Not Use AgainGovernor Spring Seat
Illustration 56 g06346615
Governor spring seat with typical wear.
Use Again - if there are no gouges to surfaces (1) on the spring seating area.Spring Pack
Illustration 57 g06346618
End view of governor spring pack.
Use Again - after realignment.Note the off-center position of the internal springs with respect to the outside spring. This can cause governor instability, which results in surging. Rotate the springs on their seat so that the inner springs are aligned (centered) with respect to the outer spring. Remove sharp edges (A) from the inside diameter of the flat surface on the springs to ensure springs seat properly.