Information injection-pump assembly
ZEXEL
106871-2961
1068712961
MITSUBISHI
ME060445
me060445
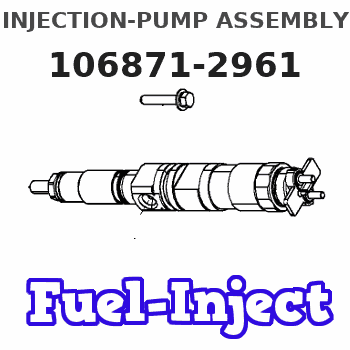
Rating:
Service parts 106871-2961 INJECTION-PUMP ASSEMBLY:
1.
_
7.
COUPLING PLATE
8.
_
9.
_
11.
Nozzle and Holder
12.
Open Pre:MPa(Kqf/cm2)
17.7(180)/21.6(220)
15.
NOZZLE SET
Include in #1:
106871-2961
as INJECTION-PUMP ASSEMBLY
Cross reference number
ZEXEL
106871-2961
1068712961
MITSUBISHI
ME060445
me060445
Zexel num
Bosch num
Firm num
Name
106871-2961
ME060445 MITSUBISHI
INJECTION-PUMP ASSEMBLY
8DC11 * K
8DC11 * K
Calibration Data:
Adjustment conditions
Test oil
1404 Test oil ISO4113 or {SAEJ967d}
1404 Test oil ISO4113 or {SAEJ967d}
Test oil temperature
degC
40
40
45
Nozzle and nozzle holder
105780-8140
Bosch type code
EF8511/9A
Nozzle
105780-0000
Bosch type code
DN12SD12T
Nozzle holder
105780-2080
Bosch type code
EF8511/9
Opening pressure
MPa
17.2
Opening pressure
kgf/cm2
175
Injection pipe
Outer diameter - inner diameter - length (mm) mm 8-3-600
Outer diameter - inner diameter - length (mm) mm 8-3-600
Overflow valve opening pressure
kPa
157
123
191
Overflow valve opening pressure
kgf/cm2
1.6
1.25
1.95
Tester oil delivery pressure
kPa
157
157
157
Tester oil delivery pressure
kgf/cm2
1.6
1.6
1.6
Direction of rotation (viewed from drive side)
Right R
Right R
Injection timing adjustment
Direction of rotation (viewed from drive side)
Right R
Right R
Injection order
1-2-7-3-
4-5-6-8
Pre-stroke
mm
4.8
4.75
4.85
Beginning of injection position
Governor side NO.1
Governor side NO.1
Difference between angles 1
Cyl.1-2 deg. 45 44.5 45.5
Cyl.1-2 deg. 45 44.5 45.5
Difference between angles 2
Cal 1-7 deg. 90 89.5 90.5
Cal 1-7 deg. 90 89.5 90.5
Difference between angles 3
Cal 1-3 deg. 135 134.5 135.5
Cal 1-3 deg. 135 134.5 135.5
Difference between angles 4
Cal 1-4 deg. 180 179.5 180.5
Cal 1-4 deg. 180 179.5 180.5
Difference between angles 5
Cal 1-5 deg. 225 224.5 225.5
Cal 1-5 deg. 225 224.5 225.5
Difference between angles 6
Cal 1-6 deg. 270 269.5 270.5
Cal 1-6 deg. 270 269.5 270.5
Difference between angles 7
Cal 1-8 deg. 315 314.5 315.5
Cal 1-8 deg. 315 314.5 315.5
Injection quantity adjustment
Adjusting point
-
Rack position
10
Pump speed
r/min
700
700
700
Each cylinder's injection qty
mm3/st.
129
125.1
132.9
Basic
*
Fixing the rack
*
Standard for adjustment of the maximum variation between cylinders
*
Injection quantity adjustment_02
Adjusting point
C
Rack position
6.1+-0.5
Pump speed
r/min
225
225
225
Each cylinder's injection qty
mm3/st.
20
17
23
Fixing the rack
*
Standard for adjustment of the maximum variation between cylinders
*
Injection quantity adjustment_03
Adjusting point
A
Rack position
R1(10)
Pump speed
r/min
700
700
700
Average injection quantity
mm3/st.
129
128
130
Basic
*
Fixing the lever
*
Injection quantity adjustment_04
Adjusting point
B
Rack position
R1(10)
Pump speed
r/min
1100
1100
1100
Average injection quantity
mm3/st.
131.7
126.3
137.1
Difference in delivery
mm3/st.
10.8
10.8
10.8
Fixing the lever
*
Injection quantity adjustment_05
Adjusting point
E
Rack position
-
Pump speed
r/min
100
100
100
Average injection quantity
mm3/st.
160
120
200
Fixing the lever
*
Remarks
After startup boost setting
After startup boost setting
Timer adjustment
Pump speed
r/min
-
Advance angle
deg.
0
0
0
Remarks
Measure speed (beginning of operation).
Measure speed (beginning of operation).
Timer adjustment_02
Pump speed
r/min
1100
Advance angle
deg.
5
4.5
5.5
Remarks
Finish
Finish
Test data Ex:
Governor adjustment
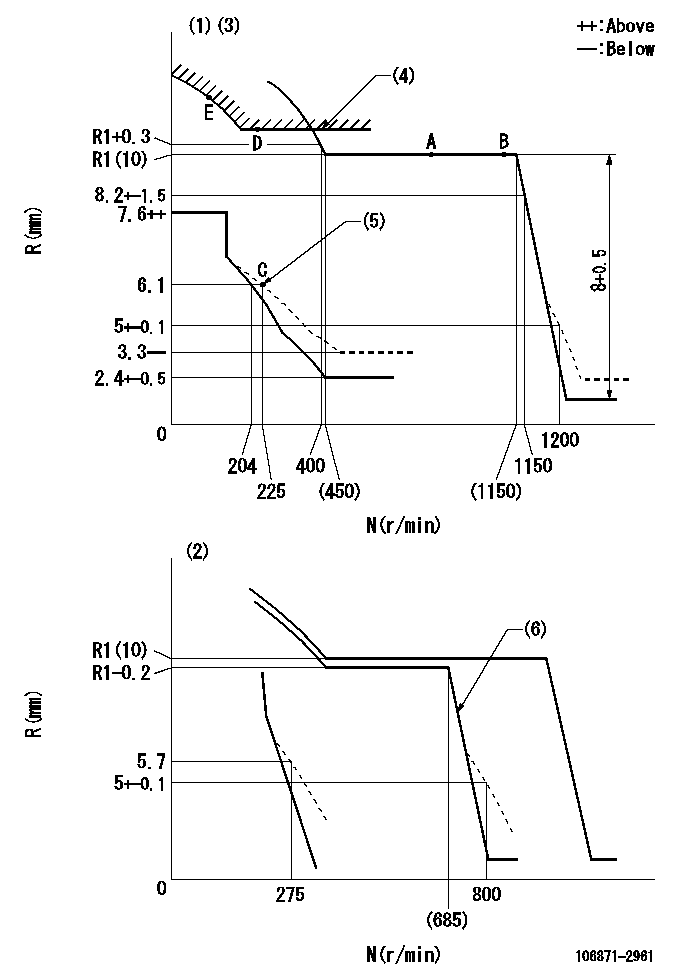
N:Pump speed
R:Rack position (mm)
(1)Adjust with speed control lever at full position (minimum-maximum speed specification)
(2)Adjust with the load control lever in the full position (variable speed specification).
(3)Tolerance for racks not indicated: +-0.05mm.
(4)Excess fuel setting for starting: SXL
(5)Damper spring setting
(6)When air cylinder is operating.
----------
SXL=12.7+-0.1mm
----------
----------
SXL=12.7+-0.1mm
----------
Speed control lever angle
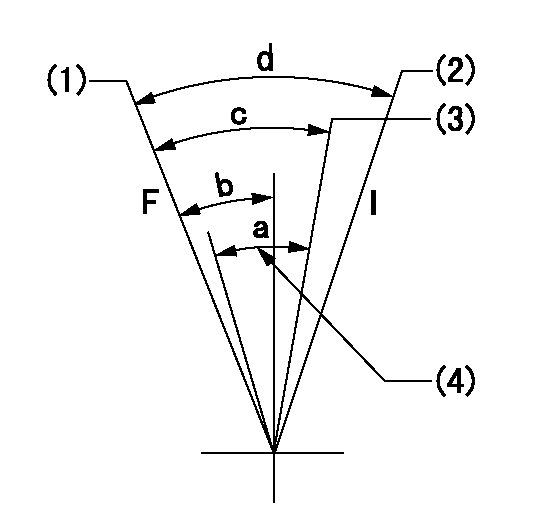
F:Full speed
I:Idle
(1)Pump speed = aa
(2)Pump speed = bb
(3)Pump speed cc
(4)Air cylinder's adjustable range
----------
aa=1200r/min bb=275r/min cc=800r/min
----------
a=(12deg) b=(7.5deg)+-5deg c=(12deg)+-5deg d=(22deg)+-5deg
----------
aa=1200r/min bb=275r/min cc=800r/min
----------
a=(12deg) b=(7.5deg)+-5deg c=(12deg)+-5deg d=(22deg)+-5deg
0000000901
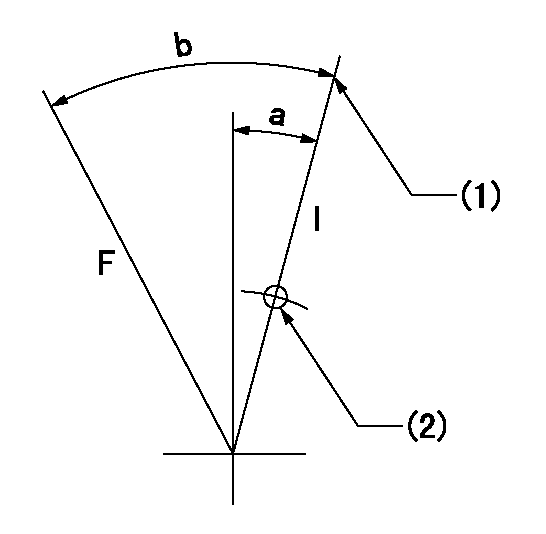
F:Full load
I:Idle
(1)Stopper bolt setting
(2)Use the hole at R = aa
----------
aa=55mm
----------
a=10deg+-5deg b=28deg+-3deg
----------
aa=55mm
----------
a=10deg+-5deg b=28deg+-3deg
Stop lever angle
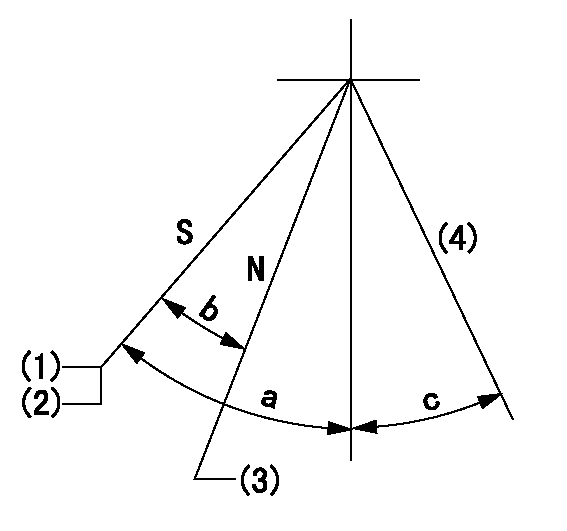
N:Engine manufacturer's normal use
S:Stop the pump.
(1)Rack position = aa
(2)Stopper bolt setting
(3)Rack position bb
(4)Free (at shipping)
----------
aa=4-0.5mm bb=11.7mm
----------
a=43deg+7deg-5deg b=21.5deg+-5deg c=(10.5deg)
----------
aa=4-0.5mm bb=11.7mm
----------
a=43deg+7deg-5deg b=21.5deg+-5deg c=(10.5deg)
0000001501 2-STAGE CHANGEOVER DEVICE

RFD governor 2 stage changeover mechanism adjustment outline
(A) Bolt
(B) bolt
(c) Nut
(D) Return spring
(E) Bolt
(F) Bolt
(G) Screw
(H) Bolt
(I) Load lever
(J) Speed lever
(K) Air cylinder
(M Air inlet
Figure 1 is only for reference. Lever shape, etc, may vary.
1. Minimum-maximum speed specification adjustment (when running)
(a) Without applying air to the air cylinder, loosen bolts (A) and (B).
(1)High speed return L setting
(a) In the speed range Nf~Nf - 300r/min, adjust using the speed adjusting bolt to determine the temporary beginning of high speed control speed.
(b) Determine the rack position in the vicinity of Rf using the full load lever.
(c) Increase speed and confirm return distance L.
(d) Adjust using the tension lever bolt to obtain L.
(2)Setting full load rack position Rf
(a) Move the load control lever to the full side.
(b) Adjust the full load adjusting bolt so that Rf can be obtained, then fix.
(3)Setting the beginning of high speed operation Nf
(a) Adjust using bolt (E) so that Nf can be obtained, and then fix.
(4)Idle control setting (Re, Ni, Rc)
(a) Set the speed at Ns + 200r/min and move the load control lever to the idle side.
(b) Fix the lever in the position where Re can be obtained.
(c) Next, decrease speed to Ni and screw in the idle spring.
(d) Adjust to obtain rack position Ri.
(e) Increase the speed and after confirming that the rack position is Re at Ns, set the speed at 0.
(f) Confirm protrusion position Rc at idle.
(5)Damper spring adjustment
(a) Increase speed and set the speed at the rack position Rd - 0.1 mm
(b) Set using the damper spring so that the rack position Rd can be obtained.
(c) When Rd is not specified, Rd = Ri - 0.5 mm.
(6)High speed droop confirmation
(a) Return the load control lever to the full load lever position.
(b) Increase the speed and confirm that Rf can be obtained at Nf r/min.
(c) Confirm that speed is Nh at rack position Rh.
2. Variable speed specification adjustment (at operation)
(a) Remove return spring (D).
(b) Apply air pressure of 245~294 kPa {2.5~3 kg/cm2} to the air cylinder.
(c) Perform the following adjustment in this condition.
(1)Setting full load rack position Rf'
(a) Pull the load lever to the idle side.
(b) Obtain rack position Rf' using the nut (C). (Pump speed is Nf'-50 r/min.)
(2)Setting full speed Nf'
(a) Adjust using bolt (B) so that Nf can be obtained, and then fix.
(3)Low speed side setting
(a) At 350r/min, set bolt (F) at beginning of governor operation position, then fix.
3. Bolt (A) adjustment
(1)Install return spring (D) and perform the adjustments below at air pressure 0.
(a) Set at speed Nf using bolt (E).
(b) Screw in bolt (A).
(c) Screw in 1 more turn from the speed lever contact position
(d) Fix bolt (A).
(e) At this time confirm that the air cylinder's shaft moves approximately 1 mm towards the governor.
4. Lever operation confirmation using the air cylinder
(1)Apply 588 kPa {6 kg/cm2} air pressure to the air cylinder.
(2)Confirm that the cylinder piston is moved 50 mm by the spring (D).
----------
----------
----------
----------
0000001601 MICRO SWITCH
Adjustment of the micro-switch
Adjust the bolt to obtain the following lever position when the micro-switch is ON.
(1)Speed N1
(2)Rack position Ra
----------
N1=325r/min Ra=5.6+-0.1mm
----------
----------
N1=325r/min Ra=5.6+-0.1mm
----------
Timing setting

(1)Pump vertical direction
(2)Coupling's key groove position at No 1 cylinder's beginning of injection
(3)-
(4)-
----------
----------
a=(40deg)
----------
----------
a=(40deg)
Information:
Problem 4
The starting motor remains engaged or the starting motor continues to run after the engine is running.
Check the components of the starting circuit.
Measure the voltages at terminal (TS-26) of the junction box and at terminal (ESS-12) of the electronic speed switch while the engine is running. Result
The voltage at both terminals is zero volts.The problem is in the starting motor (SM), the pinion solenoid (PS), or the magnetic switch (MS). Repair the faulty component. STOP.
The voltage at terminal (ESS-12) is between 15 volts and 32 volts. The voltage at terminal (TS-26) is above 15 volts or below 15 volts but not zero volts.The contacts for the crank terminate (CT) switch of the electronic speed switch (ESS) do not open. Refer to Testing and Adjusting, "Crank Terminate Speed Calibration". If the ESS is not faulty, check diode (D3). Refer to Testing and Adjusting, "Diode Test".
The voltage at both terminals is between 15 volts and 32 volts.The voltage at the terminals is greater than zero volts. During the normal operation of the start/stop switch, the start/stop switch opens across the contacts of the START position. Also, the start/stop switch closes across the contacts of the RUN position. The switch closes when the toggle or the lever of the switch moves from the START position to the RUN position. Repair the switch if the voltage is zero.
The voltage at terminal (ESS-12) is not zero.The CT contacts of the ESS are not opening. Refer to Testing and Adjusting, "Crank Terminate Speed Calibration".Problem 5
The engine shutdown occurs after the engine runs for more than 3 minutes.
Check the overspeed setting on the electronic speed switch (ESS).
Observe the indicator lamp on the ESS.
Reset the air shutoff lever, if equipped. Result
The indicator lamp on the ESS is turned on.Overspeed is indicated as the cause of the engine shutdown. Press the "RESET" button of the ESS. Find the cause of the overspeed. Refer to Testing and Adjusting, "Overspeed Verification Test" and Testing and Adjusting, "Overspeed Calibration". If the overspeed is adjusted properly and the problem persists, check the shielded cable. Only the shield should be connected to terminal 2 on the ESS. STOP.
The indicator lamp is turned off.Go to Step 2.
Check the oil pressure switches.
Connect a jumper between terminals (TS-9) and (TS-14) of the junction box.
Start the engine. Result
The engine starts and the engine runs.The problem is in the oil pressure switches. Go to Step 7 of "Problem 3".
The engine starts but engine shutdown occurs immediately.Go to Step 1 of "Problem 3".
The engine starts and the engine runs but engine shutdown occurs after the engine runs for more than 3 minutes.Go to Step 3.
The engine cranks but the engine does not start.Go to Step 1 of "Problem 1".Note: If the water temperature contactor switch causes overheating go to Step 8 of "Problem 1". If the water temperature contactor switch is not the problem, go to Step 1of "Problem 1".
Check the slave relay (SR1).
Disconnect the jumper from terminals (TS-9) and (TD-14).
Connect a jumper between terminals (TS-14) and
The starting motor remains engaged or the starting motor continues to run after the engine is running.
Check the components of the starting circuit.
Measure the voltages at terminal (TS-26) of the junction box and at terminal (ESS-12) of the electronic speed switch while the engine is running. Result
The voltage at both terminals is zero volts.The problem is in the starting motor (SM), the pinion solenoid (PS), or the magnetic switch (MS). Repair the faulty component. STOP.
The voltage at terminal (ESS-12) is between 15 volts and 32 volts. The voltage at terminal (TS-26) is above 15 volts or below 15 volts but not zero volts.The contacts for the crank terminate (CT) switch of the electronic speed switch (ESS) do not open. Refer to Testing and Adjusting, "Crank Terminate Speed Calibration". If the ESS is not faulty, check diode (D3). Refer to Testing and Adjusting, "Diode Test".
The voltage at both terminals is between 15 volts and 32 volts.The voltage at the terminals is greater than zero volts. During the normal operation of the start/stop switch, the start/stop switch opens across the contacts of the START position. Also, the start/stop switch closes across the contacts of the RUN position. The switch closes when the toggle or the lever of the switch moves from the START position to the RUN position. Repair the switch if the voltage is zero.
The voltage at terminal (ESS-12) is not zero.The CT contacts of the ESS are not opening. Refer to Testing and Adjusting, "Crank Terminate Speed Calibration".Problem 5
The engine shutdown occurs after the engine runs for more than 3 minutes.
Check the overspeed setting on the electronic speed switch (ESS).
Observe the indicator lamp on the ESS.
Reset the air shutoff lever, if equipped. Result
The indicator lamp on the ESS is turned on.Overspeed is indicated as the cause of the engine shutdown. Press the "RESET" button of the ESS. Find the cause of the overspeed. Refer to Testing and Adjusting, "Overspeed Verification Test" and Testing and Adjusting, "Overspeed Calibration". If the overspeed is adjusted properly and the problem persists, check the shielded cable. Only the shield should be connected to terminal 2 on the ESS. STOP.
The indicator lamp is turned off.Go to Step 2.
Check the oil pressure switches.
Connect a jumper between terminals (TS-9) and (TS-14) of the junction box.
Start the engine. Result
The engine starts and the engine runs.The problem is in the oil pressure switches. Go to Step 7 of "Problem 3".
The engine starts but engine shutdown occurs immediately.Go to Step 1 of "Problem 3".
The engine starts and the engine runs but engine shutdown occurs after the engine runs for more than 3 minutes.Go to Step 3.
The engine cranks but the engine does not start.Go to Step 1 of "Problem 1".Note: If the water temperature contactor switch causes overheating go to Step 8 of "Problem 1". If the water temperature contactor switch is not the problem, go to Step 1of "Problem 1".
Check the slave relay (SR1).
Disconnect the jumper from terminals (TS-9) and (TD-14).
Connect a jumper between terminals (TS-14) and
Have questions with 106871-2961?
Group cross 106871-2961 ZEXEL
Mitsubishi
Mitsubishi
Mitsubishi
106871-2961
ME060445
INJECTION-PUMP ASSEMBLY
8DC11
8DC11