Information injection-pump assembly
BOSCH
9 400 613 132
9400613132
ZEXEL
106871-2420
1068712420
MITSUBISHI
ME066501
me066501
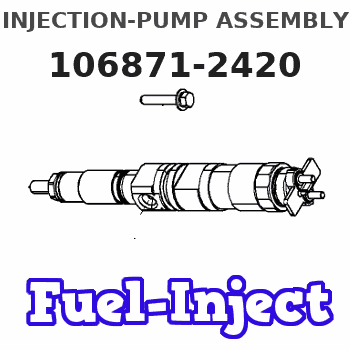
Rating:
Service parts 106871-2420 INJECTION-PUMP ASSEMBLY:
1.
_
7.
COUPLING PLATE
8.
_
9.
_
11.
Nozzle and Holder
31261-30020
12.
Open Pre:MPa(Kqf/cm2)
21.6{220}
15.
NOZZLE SET
Include in #1:
106871-2420
as INJECTION-PUMP ASSEMBLY
Cross reference number
BOSCH
9 400 613 132
9400613132
ZEXEL
106871-2420
1068712420
MITSUBISHI
ME066501
me066501
Zexel num
Bosch num
Firm num
Name
106871-2420
9 400 613 132
ME066501 MITSUBISHI
INJECTION-PUMP ASSEMBLY
8DC8 K 14CD INJECTION PUMP ASSY PE8P PE
8DC8 K 14CD INJECTION PUMP ASSY PE8P PE
Calibration Data:
Adjustment conditions
Test oil
1404 Test oil ISO4113 or {SAEJ967d}
1404 Test oil ISO4113 or {SAEJ967d}
Test oil temperature
degC
40
40
45
Nozzle and nozzle holder
105780-8140
Bosch type code
EF8511/9A
Nozzle
105780-0000
Bosch type code
DN12SD12T
Nozzle holder
105780-2080
Bosch type code
EF8511/9
Opening pressure
MPa
17.2
Opening pressure
kgf/cm2
175
Injection pipe
Outer diameter - inner diameter - length (mm) mm 8-3-600
Outer diameter - inner diameter - length (mm) mm 8-3-600
Overflow valve opening pressure
kPa
157
123
191
Overflow valve opening pressure
kgf/cm2
1.6
1.25
1.95
Tester oil delivery pressure
kPa
157
157
157
Tester oil delivery pressure
kgf/cm2
1.6
1.6
1.6
Direction of rotation (viewed from drive side)
Right R
Right R
Injection timing adjustment
Direction of rotation (viewed from drive side)
Right R
Right R
Injection order
1-2-7-3-
4-5-6-8
Pre-stroke
mm
4.8
4.75
4.85
Beginning of injection position
Governor side NO.1
Governor side NO.1
Difference between angles 1
Cyl.1-2 deg. 45 44.5 45.5
Cyl.1-2 deg. 45 44.5 45.5
Difference between angles 2
Cal 1-7 deg. 90 89.5 90.5
Cal 1-7 deg. 90 89.5 90.5
Difference between angles 3
Cal 1-3 deg. 135 134.5 135.5
Cal 1-3 deg. 135 134.5 135.5
Difference between angles 4
Cal 1-4 deg. 180 179.5 180.5
Cal 1-4 deg. 180 179.5 180.5
Difference between angles 5
Cal 1-5 deg. 225 224.5 225.5
Cal 1-5 deg. 225 224.5 225.5
Difference between angles 6
Cal 1-6 deg. 270 269.5 270.5
Cal 1-6 deg. 270 269.5 270.5
Difference between angles 7
Cal 1-8 deg. 315 314.5 315.5
Cal 1-8 deg. 315 314.5 315.5
Injection quantity adjustment
Adjusting point
-
Rack position
9
Pump speed
r/min
700
700
700
Each cylinder's injection qty
mm3/st.
85
82.4
87.6
Basic
*
Fixing the rack
*
Standard for adjustment of the maximum variation between cylinders
*
Injection quantity adjustment_02
Adjusting point
C
Rack position
6.8+-0.5
Pump speed
r/min
200
200
200
Each cylinder's injection qty
mm3/st.
20
17
23
Fixing the rack
*
Standard for adjustment of the maximum variation between cylinders
*
Injection quantity adjustment_03
Adjusting point
A
Rack position
R1(9)
Pump speed
r/min
700
700
700
Average injection quantity
mm3/st.
85
84
86
Fixing the lever
*
Injection quantity adjustment_04
Adjusting point
B
Rack position
R1(9)
Pump speed
r/min
1100
1100
1100
Average injection quantity
mm3/st.
97
93.1
100.9
Difference in delivery
mm3/st.
7.8
7.8
7.8
Fixing the lever
*
Injection quantity adjustment_05
Adjusting point
E
Rack position
-
Pump speed
r/min
100
100
100
Average injection quantity
mm3/st.
130
90
170
Fixing the lever
*
Remarks
After startup boost setting
After startup boost setting
Timer adjustment
Pump speed
r/min
600+-50
Advance angle
deg.
0
0
0
Remarks
Start
Start
Timer adjustment_02
Pump speed
r/min
700
Advance angle
deg.
0.7
0.2
1.2
Timer adjustment_03
Pump speed
r/min
850
Advance angle
deg.
2
1.5
2.5
Timer adjustment_04
Pump speed
r/min
1000
Advance angle
deg.
3.6
3.1
4.1
Timer adjustment_05
Pump speed
r/min
1150
Advance angle
deg.
5.5
5
6
Remarks
Finish
Finish
Test data Ex:
Governor adjustment
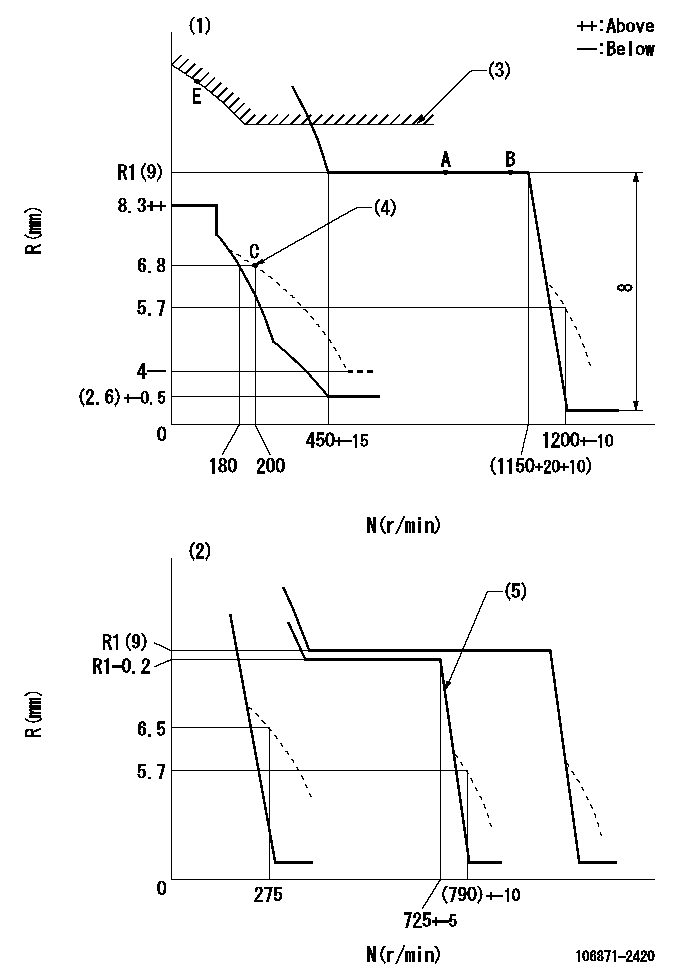
N:Pump speed
R:Rack position (mm)
(1)Adjust with speed control lever at full position (minimum-maximum speed specification)
(2)Adjust with the load control lever in the full position (variable speed specification).
(3)Excess fuel setting for starting: SXL
(4)Damper spring setting
(5)When air cylinder is operating.
----------
SXL=R1+3+2.8mm
----------
----------
SXL=R1+3+2.8mm
----------
Speed control lever angle
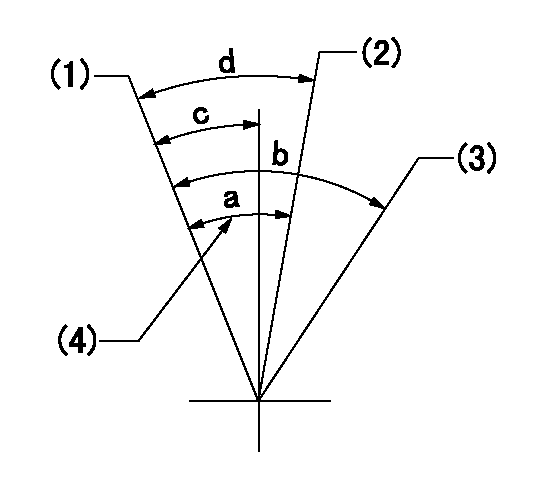
F:Full speed
I:Idle
(1)(Pump speed = aa)
(2)Pump speed = bb
(3)Pump speed cc
(4)Possible adjusting range
----------
aa=1150r/min bb=725r/min cc=275r/min
----------
a=13deg b=(20deg)+-5deg c=8deg+-5deg d=13deg+-5deg
----------
aa=1150r/min bb=725r/min cc=275r/min
----------
a=13deg b=(20deg)+-5deg c=8deg+-5deg d=13deg+-5deg
0000000901

F:Full load
I:Idle
(1)Stopper bolt setting
----------
----------
a=10deg+-5deg b=(23.5deg)+-3deg
----------
----------
a=10deg+-5deg b=(23.5deg)+-3deg
Stop lever angle
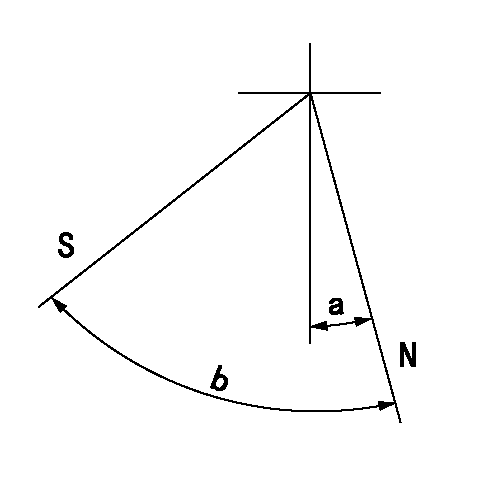
N:Pump normal
S:Stop the pump.
----------
----------
a=10deg+-5deg b=64deg+-5deg
----------
----------
a=10deg+-5deg b=64deg+-5deg
0000001501 2-STAGE CHANGEOVER DEVICE

RFD governor 2 stage changeover mechanism adjustment outline
(A) Bolt
(B) bolt
(c) Nut
(D) Return spring
(E) Bolt
(F) Bolt
(G) Screw
(H) Bolt
(I) Load lever
(J) Speed lever
(K) Air cylinder
(M Air inlet
Figure 1 is only for reference. Lever shape, etc, may vary.
1. Minimum-maximum speed specification adjustment (when running)
(a) Without applying air to the air cylinder, loosen bolts (A) and (B).
(1)High speed return L setting
(a) In the speed range Nf~Nf - 300r/min, adjust using the speed adjusting bolt to determine the temporary beginning of high speed control speed.
(b) Determine the rack position in the vicinity of Rf using the full load lever.
(c) Increase speed and confirm return distance L.
(d) Adjust using the tension lever bolt to obtain L.
(2)Setting full load rack position Rf
(a) Move the load control lever to the full side.
(b) Adjust the full load adjusting bolt so that Rf can be obtained, then fix.
(3)Setting the beginning of high speed operation Nf
(a) Adjust using bolt (E) so that Nf can be obtained, and then fix.
(4)Idle control setting (Re, Ni, Rc)
(a) Set the speed at Ns + 200r/min and move the load control lever to the idle side.
(b) Fix the lever in the position where Re can be obtained.
(c) Next, decrease speed to Ni and screw in the idle spring.
(d) Adjust to obtain rack position Ri.
(e) Increase the speed and after confirming that the rack position is Re at Ns, set the speed at 0.
(f) Confirm protrusion position Rc at idle.
(5)Damper spring adjustment
(a) Increase speed and set the speed at the rack position Rd - 0.1 mm
(b) Set using the damper spring so that the rack position Rd can be obtained.
(c) When Rd is not specified, Rd = Ri - 0.5 mm.
(6)High speed droop confirmation
(a) Return the load control lever to the full load lever position.
(b) Increase the speed and confirm that Rf can be obtained at Nf r/min.
(c) Confirm that speed is Nh at rack position Rh.
2. Variable speed specification adjustment (at operation)
(a) Remove return spring (D).
(b) Apply air pressure of 245~294 kPa {2.5~3 kg/cm2} to the air cylinder.
(c) Perform the following adjustment in this condition.
(1)Setting full load rack position Rf'
(a) Pull the load lever to the idle side.
(b) Obtain rack position Rf' using the nut (C). (Pump speed is Nf'-50 r/min.)
(2)Setting full speed Nf'
(a) Adjust using bolt (B) so that Nf can be obtained, and then fix.
(3)Low speed side setting
(a) At 350r/min, set bolt (F) at beginning of governor operation position, then fix.
3. Bolt (A) adjustment
(1)Install return spring (D) and perform the adjustments below at air pressure 0.
(a) Set at speed Nf using bolt (E).
(b) Screw in bolt (A).
(c) Screw in 1 more turn from the speed lever contact position
(d) Fix bolt (A).
(e) At this time confirm that the air cylinder's shaft moves approximately 1 mm towards the governor.
4. Lever operation confirmation using the air cylinder
(1)Apply 588 kPa {6 kg/cm2} air pressure to the air cylinder.
(2)Confirm that the cylinder piston is moved 50 mm by the spring (D).
----------
----------
----------
----------
0000001601 MICRO SWITCH
Adjustment of the micro-switch
Adjust the bolt to obtain the following lever position when the micro-switch is ON.
(1)Speed N1
(2)Rack position Ra
----------
N1=325+-5r/min Ra=6.3mm
----------
----------
N1=325+-5r/min Ra=6.3mm
----------
Information:
FACE="Courier New">CONFIDENTIAL
TECHNICAL INFORMATION BULLETIN March 27, 2002
Engines 3516 (25Z, 5SJ, 7KM, CMD, 4XF)
3516B (1HZ, 7RN, 5AN, FDN, BDP,
6HN)
Component Code: 1404SUBJECT: Generator Stator Adapter Cracking on 3516 Diesel Generator Set
PROBLEM:
Certain SR4B single bearing generators may develop cracks in the adapter assembly. The generator adapter is the welded assembly, part of the generator stator, consisting of the front adapter ring that bolts to the flywheel housing and the individual support bars welded to this adapter ring. Several different weld failure modes exist for the generator adapter. First, there may be cracks along the top weld leg between the adapter supports and the front adapter ring. Second, there may be cracks at the toe of the welds joining the adapter support bars to the front ring. These cracks appear in the heat-affected zone of the welds and propagate into the front adapter ring of the generator. The third failure mode is radial cracks between the end ring of the generator adapter and the stator housing. This type of crack most likely occurs after the support welds have failed. After the support welds have failed, the cracks at the toe of the support bars propagate into the ring and create a stress riser.
SOLUTION:
Caterpillar is redesigning the current product and is also working on a solution that will address the existing units in the field. At this time, it is NOT recommended to immediately replace cracked generator stators, nor is it recommended to re-weld the cracked adapters as a field repair. Rather, a crack observation and evaluation process should be established for each individual case. It is anticipated that the first recognizable cracks on suspect generators (cracks size of 0.25" and larger) may appear as early as 300 hours. If any of the above-described cracks are found, the servicing dealer should contact Caterpillar Service. The servicing dealer should also assist in periodic inspection of the cracks in an effort to determine the next action.
Contact (if different from sender): Miro Halicek (770) 233-5877 or Marc Sylvester (770) 233-5630.
COPYRIGHT 2002 CATERPILLAR
ALL RIGHTS RESERVED
TECHNICAL INFORMATION BULLETIN March 27, 2002
Engines 3516 (25Z, 5SJ, 7KM, CMD, 4XF)
3516B (1HZ, 7RN, 5AN, FDN, BDP,
6HN)
Component Code: 1404SUBJECT: Generator Stator Adapter Cracking on 3516 Diesel Generator Set
PROBLEM:
Certain SR4B single bearing generators may develop cracks in the adapter assembly. The generator adapter is the welded assembly, part of the generator stator, consisting of the front adapter ring that bolts to the flywheel housing and the individual support bars welded to this adapter ring. Several different weld failure modes exist for the generator adapter. First, there may be cracks along the top weld leg between the adapter supports and the front adapter ring. Second, there may be cracks at the toe of the welds joining the adapter support bars to the front ring. These cracks appear in the heat-affected zone of the welds and propagate into the front adapter ring of the generator. The third failure mode is radial cracks between the end ring of the generator adapter and the stator housing. This type of crack most likely occurs after the support welds have failed. After the support welds have failed, the cracks at the toe of the support bars propagate into the ring and create a stress riser.
SOLUTION:
Caterpillar is redesigning the current product and is also working on a solution that will address the existing units in the field. At this time, it is NOT recommended to immediately replace cracked generator stators, nor is it recommended to re-weld the cracked adapters as a field repair. Rather, a crack observation and evaluation process should be established for each individual case. It is anticipated that the first recognizable cracks on suspect generators (cracks size of 0.25" and larger) may appear as early as 300 hours. If any of the above-described cracks are found, the servicing dealer should contact Caterpillar Service. The servicing dealer should also assist in periodic inspection of the cracks in an effort to determine the next action.
Contact (if different from sender): Miro Halicek (770) 233-5877 or Marc Sylvester (770) 233-5630.
COPYRIGHT 2002 CATERPILLAR
ALL RIGHTS RESERVED
Have questions with 106871-2420?
Group cross 106871-2420 ZEXEL
Mitsubishi
106871-2420
9 400 613 132
ME066501
INJECTION-PUMP ASSEMBLY
8DC8
8DC8