Information injection-pump assembly
ZEXEL
106871-2380
1068712380
MITSUBISHI
ME066463
me066463
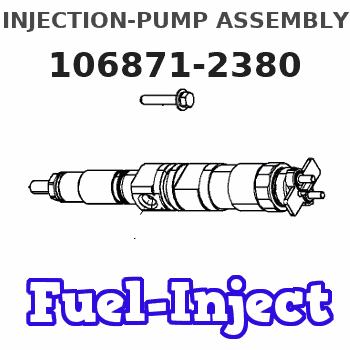
Rating:
Cross reference number
ZEXEL
106871-2380
1068712380
MITSUBISHI
ME066463
me066463
Zexel num
Bosch num
Firm num
Name
106871-2380
ME066463 MITSUBISHI
INJECTION-PUMP ASSEMBLY
8DC9 * K
8DC9 * K
Calibration Data:
Adjustment conditions
Test oil
1404 Test oil ISO4113 or {SAEJ967d}
1404 Test oil ISO4113 or {SAEJ967d}
Test oil temperature
degC
40
40
45
Nozzle and nozzle holder
105780-8140
Bosch type code
EF8511/9A
Nozzle
105780-0000
Bosch type code
DN12SD12T
Nozzle holder
105780-2080
Bosch type code
EF8511/9
Opening pressure
MPa
17.2
Opening pressure
kgf/cm2
175
Injection pipe
Outer diameter - inner diameter - length (mm) mm 8-3-600
Outer diameter - inner diameter - length (mm) mm 8-3-600
Overflow valve opening pressure
kPa
157
123
191
Overflow valve opening pressure
kgf/cm2
1.6
1.25
1.95
Tester oil delivery pressure
kPa
157
157
157
Tester oil delivery pressure
kgf/cm2
1.6
1.6
1.6
Direction of rotation (viewed from drive side)
Right R
Right R
Injection timing adjustment
Direction of rotation (viewed from drive side)
Right R
Right R
Injection order
1-2-7-3-
4-5-6-8
Pre-stroke
mm
4.8
4.75
4.85
Beginning of injection position
Governor side NO.1
Governor side NO.1
Difference between angles 1
Cyl.1-2 deg. 45 44.5 45.5
Cyl.1-2 deg. 45 44.5 45.5
Difference between angles 2
Cal 1-7 deg. 90 89.5 90.5
Cal 1-7 deg. 90 89.5 90.5
Difference between angles 3
Cal 1-3 deg. 135 134.5 135.5
Cal 1-3 deg. 135 134.5 135.5
Difference between angles 4
Cal 1-4 deg. 180 179.5 180.5
Cal 1-4 deg. 180 179.5 180.5
Difference between angles 5
Cal 1-5 deg. 225 224.5 225.5
Cal 1-5 deg. 225 224.5 225.5
Difference between angles 6
Cal 1-6 deg. 270 269.5 270.5
Cal 1-6 deg. 270 269.5 270.5
Difference between angles 7
Cal 1-8 deg. 315 314.5 315.5
Cal 1-8 deg. 315 314.5 315.5
Injection quantity adjustment
Adjusting point
-
Rack position
10.4
Pump speed
r/min
700
700
700
Each cylinder's injection qty
mm3/st.
119
115.4
122.6
Basic
*
Fixing the rack
*
Standard for adjustment of the maximum variation between cylinders
*
Injection quantity adjustment_02
Adjusting point
C
Rack position
6.8+-0.5
Pump speed
r/min
225
225
225
Each cylinder's injection qty
mm3/st.
20
17
23
Fixing the rack
*
Standard for adjustment of the maximum variation between cylinders
*
Injection quantity adjustment_03
Adjusting point
A
Rack position
R1(10.4)
Pump speed
r/min
700
700
700
Average injection quantity
mm3/st.
119
118
120
Basic
*
Fixing the lever
*
Injection quantity adjustment_04
Adjusting point
B
Rack position
R1(10.4)
Pump speed
r/min
1100
1100
1100
Average injection quantity
mm3/st.
125
119.8
130.2
Difference in delivery
mm3/st.
10.4
10.4
10.4
Fixing the lever
*
Injection quantity adjustment_05
Adjusting point
E
Rack position
-
Pump speed
r/min
100
100
100
Average injection quantity
mm3/st.
160
140
180
Fixing the lever
*
Remarks
After startup boost setting
After startup boost setting
Timer adjustment
Pump speed
r/min
950--
Advance angle
deg.
0
0
0
Remarks
Start
Start
Timer adjustment_02
Pump speed
r/min
900
Advance angle
deg.
0.5
Timer adjustment_03
Pump speed
r/min
1000
Advance angle
deg.
1.8
1.1
2.5
Timer adjustment_04
Pump speed
r/min
1100
Advance angle
deg.
3.5
3.5
Timer adjustment_05
Pump speed
r/min
1150
Advance angle
deg.
6.5
6
7
Remarks
Finish
Finish
Test data Ex:
Governor adjustment
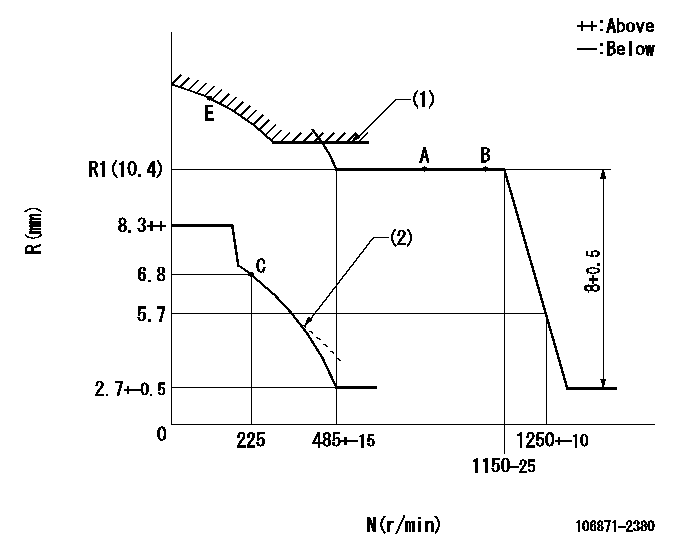
N:Pump speed
R:Rack position (mm)
(1)Excess fuel setting for starting: SXL
(2)Beginning of damper spring operation: DL
----------
SXL=11.3+-0.1mm DL=5-0.2mm
----------
----------
SXL=11.3+-0.1mm DL=5-0.2mm
----------
Speed control lever angle

F:Full speed
----------
----------
a=21deg+-5deg
----------
----------
a=21deg+-5deg
0000000901

F:Full load
I:Idle
(1)Stopper bolt setting
----------
----------
a=10deg+-5deg b=28deg+-3deg
----------
----------
a=10deg+-5deg b=28deg+-3deg
Stop lever angle
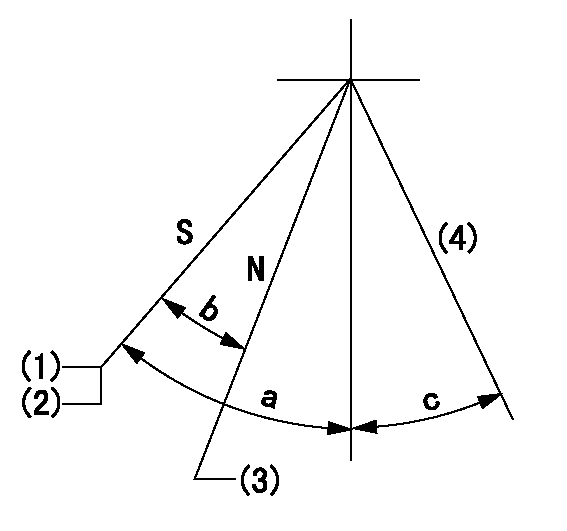
N:Pump normal
S:Stop the pump.
(1)Rack position = aa
(2)Stopper bolt setting
(3)Rack position bb
(4)Free (at shipping)
----------
aa=4.7-0.5mm bb=12.4mm
----------
a=43deg+7deg-5deg b=21.5deg+-5deg c=(10.5deg)
----------
aa=4.7-0.5mm bb=12.4mm
----------
a=43deg+7deg-5deg b=21.5deg+-5deg c=(10.5deg)
0000001501 MICRO SWITCH
Adjustment of the micro-switch
Adjust the bolt to obtain the following lever position when the micro-switch is ON.
(1)Speed N1
(2)Rack position Ra
----------
N1=325+-5r/min Ra=6.3mm
----------
----------
N1=325+-5r/min Ra=6.3mm
----------
Information:
PARTS NEEDED
Qty
Part Number Description
4 8T2223 BOLT-SOCKET HD
1 8T9524 SEAL-O-RING
1 20R5566 INJECTOR GP-FUEL
1 2287089 SEAL-O-RING-ORFS
1 2287100 SEAL-O-RING-STOR
1 2287108 SEAL-O-RING-STOR
1 2300940 SEAL-PIP
1 2697852 SEAL-O-RING
1 3170808 SEAL-O-RING
In order to allow equitable parts availability to all participating dealers, please limit your initial parts order to not exceed 1% of dealership population. This is an initial order recommendation only, and the ultimate responsibility for ordering the total number of parts needed to satisfy the program lies with the dealer.
ACTION REQUIRED
Perform a Fuel Status Verification Test (FSVT). Follow all procedures outlined in KENR5398.
Replace injectors showing INJ-2, INJ-7 or INJ-12 codes. Schedule the replacement in line with the 1500 hour recommendation described in KENR5398.
Refer to KENR6052 for removal and installation instructions.
To qualify for this program:
Machine must be operating the most current software release in SIS Web.
Machine must be operating with the Clean Fuel Module (CFM) installed and activated.
Attach a Product Status Report to the claim form.
Provide injector replacement tracking sheet copy for specific machine SN on claim.
Conduct a review of the maintenance history of the machine to ensure no High Pressure Fuel Pump failure occurred within 250 service hours of an injector failure. If a high pressure fuel pump has failed, inspect the 2D inline filter for damage and/or debris.
Must have fuel samples from month of failure with passing (green/no action suggested) fuel quality report. Program Administrator will audit if fuel sample program is being executed per agreement.
Failure to provide the requested information and/or the failed injector could result in a claim being debited or rejected.
SERVICE CLAIM ALLOWANCES
Product smu/age whichever comes first Caterpillar Dealer Suggested Customer Suggested
Parts % Labor Hrs% Parts % Labor Hrs% Parts % Labor Hrs%
0-6000 hrs,
0-12 mo 100.0% 100.0% 0.0% 0.0% 0.0% 0.0%
6001-12000 hrs,
13-24 mo 100.0% 50.0% 0.0% 0.0% 0.0% 50.0%
This is a 2.0-hour job
If there has been a previous repair, part age/hours will apply. Retain a copy of the previous repair invoice in the dealer's records for audit purposes, and specify repair date and machine hours in the "Additional Comments" section of the warranty claim.
PARTS DISPOSITION
Hold all fuel injectors for a Parts Return Request (PRR). A Parts Return Request (PRR) will be issued to you through the Send-It-Back process after the claim is submitted. Make sure to list the service letter program number on the packing slip and include the closed work order paperwork. Handle all other parts in accordance with your Warranty Bulletin on warranty parts handling.
If a Parts Return Request (PRR) is not issued to you after 30 days through the Send-It-Back process, handle the parts in accordance with your warranty bulletin on warranty parts handling.
Have questions with 106871-2380?
Group cross 106871-2380 ZEXEL
Mitsubishi
106871-2380
ME066463
INJECTION-PUMP ASSEMBLY
8DC9
8DC9