Information injection-pump assembly
ZEXEL
106871-2120
1068712120
MITSUBISHI
ME068643
me068643
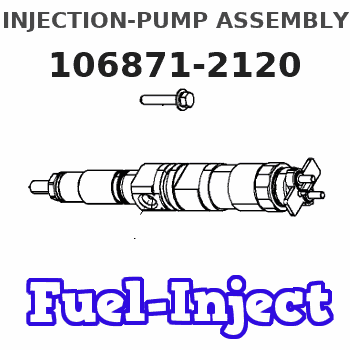
Rating:
Cross reference number
ZEXEL
106871-2120
1068712120
MITSUBISHI
ME068643
me068643
Zexel num
Bosch num
Firm num
Name
106871-2120
ME068643 MITSUBISHI
INJECTION-PUMP ASSEMBLY
8DC90C * K
8DC90C * K
Calibration Data:
Adjustment conditions
Test oil
1404 Test oil ISO4113 or {SAEJ967d}
1404 Test oil ISO4113 or {SAEJ967d}
Test oil temperature
degC
40
40
45
Nozzle and nozzle holder
105780-8140
Bosch type code
EF8511/9A
Nozzle
105780-0000
Bosch type code
DN12SD12T
Nozzle holder
105780-2080
Bosch type code
EF8511/9
Opening pressure
MPa
17.2
Opening pressure
kgf/cm2
175
Injection pipe
Outer diameter - inner diameter - length (mm) mm 8-3-600
Outer diameter - inner diameter - length (mm) mm 8-3-600
Overflow valve
134424-1120
Overflow valve opening pressure
kPa
157
123
191
Overflow valve opening pressure
kgf/cm2
1.6
1.25
1.95
Tester oil delivery pressure
kPa
157
157
157
Tester oil delivery pressure
kgf/cm2
1.6
1.6
1.6
Direction of rotation (viewed from drive side)
Right R
Right R
Injection timing adjustment
Direction of rotation (viewed from drive side)
Right R
Right R
Injection order
1-2-7-3-
4-5-6-8
Pre-stroke
mm
4.8
4.75
4.85
Beginning of injection position
Governor side NO.1
Governor side NO.1
Difference between angles 1
Cyl.1-2 deg. 45 44.5 45.5
Cyl.1-2 deg. 45 44.5 45.5
Difference between angles 2
Cal 1-7 deg. 90 89.5 90.5
Cal 1-7 deg. 90 89.5 90.5
Difference between angles 3
Cal 1-3 deg. 135 134.5 135.5
Cal 1-3 deg. 135 134.5 135.5
Difference between angles 4
Cal 1-4 deg. 180 179.5 180.5
Cal 1-4 deg. 180 179.5 180.5
Difference between angles 5
Cal 1-5 deg. 225 224.5 225.5
Cal 1-5 deg. 225 224.5 225.5
Difference between angles 6
Cal 1-6 deg. 270 269.5 270.5
Cal 1-6 deg. 270 269.5 270.5
Difference between angles 7
Cal 1-8 deg. 315 314.5 315.5
Cal 1-8 deg. 315 314.5 315.5
Injection quantity adjustment
Adjusting point
A
Rack position
9.9
Pump speed
r/min
1100
1100
1100
Average injection quantity
mm3/st.
120.6
116
125.2
Max. variation between cylinders
%
0
-4
4
Fixing the lever
*
Injection quantity adjustment_02
Adjusting point
B
Rack position
9.9
Pump speed
r/min
700
700
700
Average injection quantity
mm3/st.
113.4
109.9
116.9
Max. variation between cylinders
%
0
-3
3
Basic
*
Fixing the lever
*
Injection quantity adjustment_03
Adjusting point
C
Rack position
6.5+-0.5
Pump speed
r/min
200
200
200
Average injection quantity
mm3/st.
15
12.4
17.6
Max. variation between cylinders
%
0
-15
15
Fixing the rack
*
Injection quantity adjustment_04
Adjusting point
D
Rack position
12.2+-0.
5
Pump speed
r/min
100
100
100
Average injection quantity
mm3/st.
110
110
Fixing the lever
*
Remarks
After startup boost setting
After startup boost setting
Timer adjustment
Pump speed
r/min
600+-50
Advance angle
deg.
0
0
0
Remarks
Start
Start
Timer adjustment_02
Pump speed
r/min
700
Advance angle
deg.
0.7
0.2
1.2
Timer adjustment_03
Pump speed
r/min
850
Advance angle
deg.
2
1.5
2.5
Timer adjustment_04
Pump speed
r/min
1000
Advance angle
deg.
3.6
3.1
4.1
Timer adjustment_05
Pump speed
r/min
1150
Advance angle
deg.
5.5
5
6
Remarks
Finish
Finish
Test data Ex:
Governor adjustment
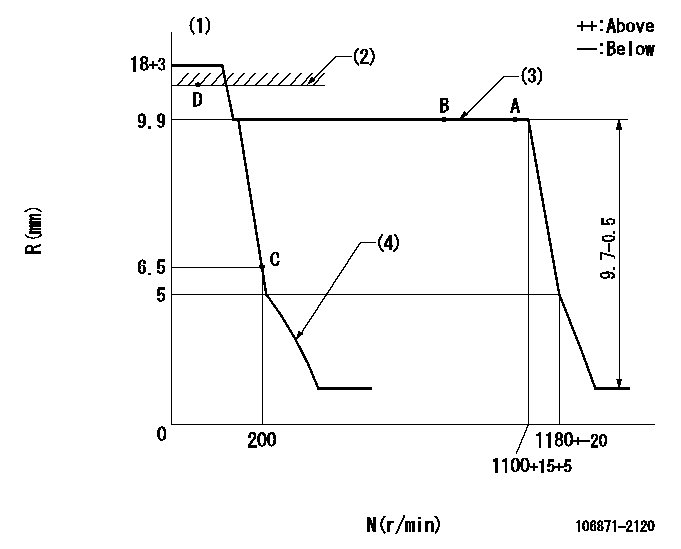
N:Pump speed
R:Rack position (mm)
(1)Target notch: K
(2)RACK LIMIT: RAL
(3)Deliver with the torque spring and the torque control spring not operating.
(4)Idle sub spring setting: L1.
----------
K=13 RAL=(12.2)mm L1=5-0.5mm
----------
----------
K=13 RAL=(12.2)mm L1=5-0.5mm
----------
Speed control lever angle
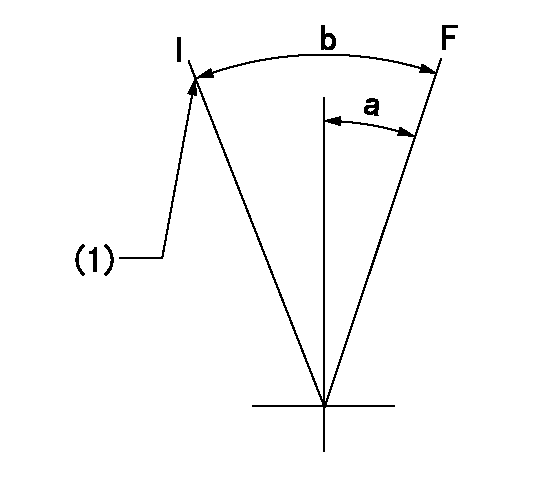
F:Full speed
I:Idle
(1)Stopper bolt setting
----------
----------
a=11deg+-5deg b=24deg+-5deg
----------
----------
a=11deg+-5deg b=24deg+-5deg
Stop lever angle
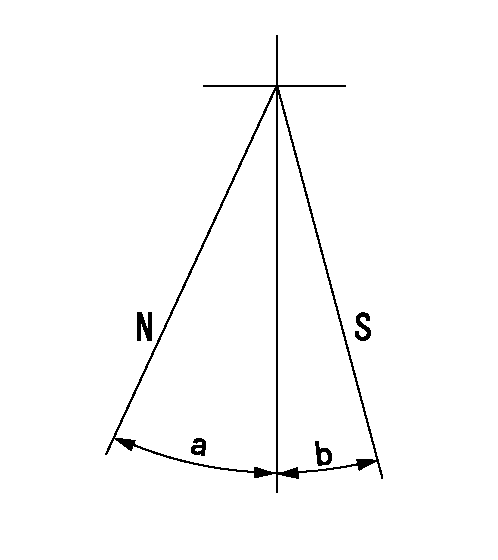
N:Pump normal
S:Stop the pump.
----------
----------
a=(26deg) b=(27deg)
----------
----------
a=(26deg) b=(27deg)
Information:
PARTS DISPOSITION
Handle the parts in accordance with your Warranty Bulletin on warranty parts handling.
Rework Procedure
Diesel Exhaust Fluid Pressure Line Removal Process:
1. Follow the Disassembly and Assembly, UENR4468, for Diesel Exhaust Fluid Lines ? Remove and Install, steps 1 to 9 to remove the DEF pressure line.
2. Remove p-clips (3) and (4) on the plate attached to the hydraulic tank and on the sound wall support leg. Keep the bolt and washer from p-clip (4) as it will be used to install the new pressure line (Image1.1.1).
Image1.1.1
3. Remove p-clip (8) from the inside of the frame and p-clips (10,12) inside of the DEF enclosure from the diesel exhaust fluid pressure line (11) (Image1.2.1).
4. Cut cable ties (9,13) near the PETU from the diesel exhaust fluid pressure line (11) (Image1.2.1).
5. Pull the diesel exhaust fluid pressure line (11) out of the machine (Image1.2.1).
Image1.2.1
After Failure Only, DEF Injector Replacement ? Remove and Install:
1. Remove DEF injector and replace. Follow Disassembly and Assembly, UENR6559, for DEF Injector and Mounting - Remove and Install.
New Diesel Exhaust Fluid Pressure Line Preparation:
1. Lay the 3.65 m pressure line out straight on a flat surface
2. Measure 308 mm from the mating point of the line and the connector and mark the location
3. Measure 631 mm from the mating point of the line and the connector and mark the location
4. Measure 996 mm from the mating point of the line and the connector and mark the location
5. Measure 1386 mm from the mating point of the line and the connector and mark the location
6. Place p-clip (6D-4246) on the line with its edge on the 1st mark
7. Place p-clip (336-8614) on the line with its edge on the 2nd mark
8. Place p-clip (336-8614) on the line with its edge on the 3rd mark
9. Place p-clip (336-8614) on the line with its edge on the 4th mark
Note: Keep lines capped when measuring and placing the p-clips
Image1.4.1
Machine Preparation:
1. Remove bracket (1) from machine. Keep the bolt and washer as it will be used when installing the new pressure line (Image1.5.1).
2. Drill an 11 mm diameter hole in the hood support. Refer to Image1.5.2 for location and Image1.5.3 for dimensions.
3. Remove the bolt and washer on the hydraulic tank support plate and keep as it will be used when installing the new diesel exhaust fluid pressure line (Image1.5.4).
Image1.5.1
Image1.5.2
Image1.5.3
Image1.5.4
Installation Process:
1. Remove plugs from the new diesel exhaust fluid pressure line
2. Attach p-clip 6D-4246 (1) and hose to the newly drilled 11 mm hole in the hood support using hardware nut 344-5675 (qty. 1), washer 8T-4121 (qty. 2), and bolt 8T-4195 (qty. 1). Once attached, the p-clip should be oriented at 15 degrees from vertical pointing downwards. Torque hardware to 55 N*m (Image1.6.1).
Image1.6.1
3. Attach p-clip 336-8614 (2) to the hydraulic tank and secure using the removed hardware (bolt: 8T-4136 and washer: 7X-7729) from step 3 of the machine preparation. Once attached, the p-clip should be oriented at 30 degrees from vertical pointing upwards to maintain the upwards slope of the line towards the hydraulic tank. Torque hardware to 55 N*m once p-clip is oriented correctly (Image1.7.1.).
Image1.7.1
4. Connect the diesel exhaust fluid line to
Have questions with 106871-2120?
Group cross 106871-2120 ZEXEL
Mitsubishi
106871-2120
ME068643
INJECTION-PUMP ASSEMBLY
8DC90C
8DC90C