Information injection-pump assembly
ZEXEL
106871-0050
1068710050
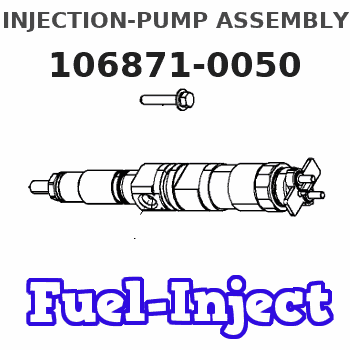
Rating:
Service parts 106871-0050 INJECTION-PUMP ASSEMBLY:
1.
_
6.
COUPLING PLATE
7.
COUPLING PLATE
8.
_
9.
_
11.
Nozzle and Holder
16600-97005
12.
Open Pre:MPa(Kqf/cm2)
22.6{230}
15.
NOZZLE SET
Include in #1:
106871-0050
as INJECTION-PUMP ASSEMBLY
Cross reference number
ZEXEL
106871-0050
1068710050
Zexel num
Bosch num
Firm num
Name
106871-0050
INJECTION-PUMP ASSEMBLY
Calibration Data:
Adjustment conditions
Test oil
1404 Test oil ISO4113 or {SAEJ967d}
1404 Test oil ISO4113 or {SAEJ967d}
Test oil temperature
degC
40
40
45
Nozzle
105015-3440
Nozzle holder
105031-4210
Opening pressure
MPa
22.6
Opening pressure
kgf/cm2
230
Injection pipe
Outer diameter - inner diameter - length (mm) mm 6-2.2-1010
Outer diameter - inner diameter - length (mm) mm 6-2.2-1010
Overflow valve
132424-0620
Overflow valve opening pressure
kPa
157
123
191
Overflow valve opening pressure
kgf/cm2
1.6
1.25
1.95
Tester oil delivery pressure
kPa
157
157
157
Tester oil delivery pressure
kgf/cm2
1.6
1.6
1.6
Direction of rotation (viewed from drive side)
Right R
Right R
Injection timing adjustment
Direction of rotation (viewed from drive side)
Right R
Right R
Injection order
1-8-7-5-
4-3-6-2
Pre-stroke
mm
3.65
3.6
3.7
Beginning of injection position
Governor side NO.1
Governor side NO.1
Difference between angles 1
Cal 1-8 deg. 45 44.5 45.5
Cal 1-8 deg. 45 44.5 45.5
Difference between angles 2
Cal 1-7 deg. 90 89.5 90.5
Cal 1-7 deg. 90 89.5 90.5
Difference between angles 3
Cal 1-5 deg. 135 134.5 135.5
Cal 1-5 deg. 135 134.5 135.5
Difference between angles 4
Cal 1-4 deg. 180 179.5 180.5
Cal 1-4 deg. 180 179.5 180.5
Difference between angles 5
Cal 1-3 deg. 225 224.5 225.5
Cal 1-3 deg. 225 224.5 225.5
Difference between angles 6
Cal 1-6 deg. 270 269.5 270.5
Cal 1-6 deg. 270 269.5 270.5
Difference between angles 7
Cyl.1-2 deg. 315 314.5 315.5
Cyl.1-2 deg. 315 314.5 315.5
Injection quantity adjustment
Adjusting point
A
Rack position
11.3
Pump speed
r/min
850
850
850
Average injection quantity
mm3/st.
142
140
144
Max. variation between cylinders
%
0
-4
4
Fixing the lever
*
Injection quantity adjustment_02
Adjusting point
B
Rack position
11.3
Pump speed
r/min
750
750
750
Average injection quantity
mm3/st.
144
142
146
Max. variation between cylinders
%
0
-4
4
Basic
*
Fixing the lever
*
Injection quantity adjustment_03
Adjusting point
C
Rack position
6+-0.5
Pump speed
r/min
300
300
300
Average injection quantity
mm3/st.
20
18
22
Max. variation between cylinders
%
0
-10
10
Fixing the rack
*
Timer adjustment
Pump speed
r/min
300+-50
Advance angle
deg.
0
0
0
Remarks
Start
Start
Timer adjustment_02
Pump speed
r/min
600
Advance angle
deg.
1.7
1.2
2.2
Timer adjustment_03
Pump speed
r/min
900
Advance angle
deg.
3.4
2.9
3.9
Timer adjustment_04
Pump speed
r/min
1250+50
Advance angle
deg.
5.5
5
6
Remarks
Finish
Finish
Test data Ex:
Governor adjustment
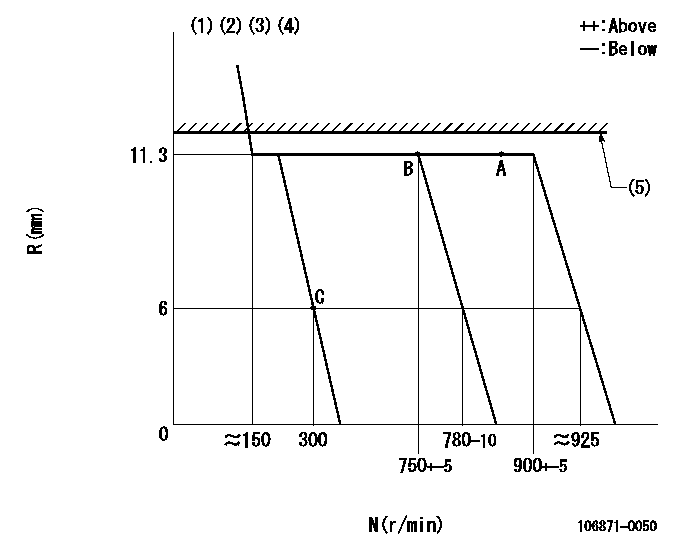
N:Pump speed
R:Rack position (mm)
(1)Target notch: K
(2)Solenoid operation confirmation: Set the speed control lever in the full speed position. At pump speed N1 when the solenoid is operated, confirm that the idle rack position is R1 or less.
(3)Idle spring not operating.
(4)Idle sub-spring does not operate.
(5)RACK LIMIT: RAL
----------
K=10 N1=100r/min R1=-1mm RAL=12+-0.1mm
----------
----------
K=10 N1=100r/min R1=-1mm RAL=12+-0.1mm
----------
Speed control lever angle
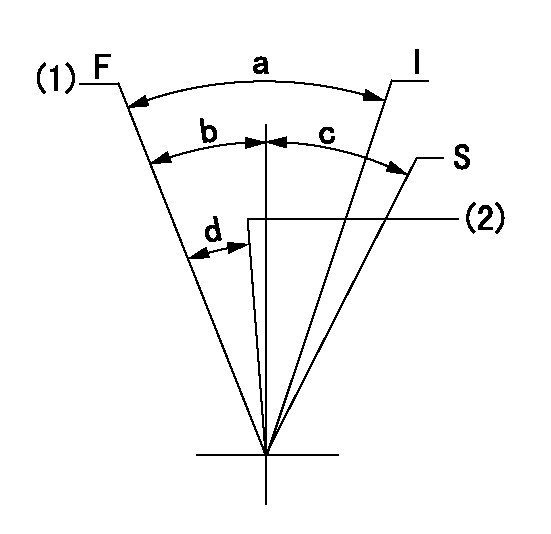
F:Full speed
I:Idle
S:Stop
(1)Pump speed = aa
(2)Pump speed = bb
----------
aa=900r/min bb=750r/min
----------
a=27.5deg+-5deg b=7.5deg+-5deg c=(32deg+-5deg) d=7deg+-5deg
----------
aa=900r/min bb=750r/min
----------
a=27.5deg+-5deg b=7.5deg+-5deg c=(32deg+-5deg) d=7deg+-5deg
Stop lever angle

N:Pump normal
S:Stop the pump.
----------
----------
a=(29deg) b=(47deg)
----------
----------
a=(29deg) b=(47deg)
Information:
You must read and understand the warnings and instructions contained in the Safety section of this manual, before performing any operation or maintenance procedures.Cooling System
Do not perform this maintenance until you read and understand the material in the Safety and Cooling System Specifications sections of this publication.
Drain/Flush/Replace Coolant (Long Life Coolant/Antifreeze Only)
Caterpillar Long Life Coolant/Antifreeze should be replaced every 6,000 Service Hours or 4 Years, whichever comes first. Only clean water is needed to clean and flush the cooling system when LLCA is drained and replaced.Drain
1. Stop the engine and allow the engine to cool. Loosen the coolant filler cap slowly to relieve any pressure, and remove the cap.2. Remove the radiator drain plug, or open the radiator drain valve (if equipped). Remove the block and oil cooler drain plugs. Remove the drain plug from the bottom of the water pump housing. Allow the coolant to drain.
Dispose of used engine coolant properly or recycle. Various methods have been proposed to reclaim used coolant for reuse in engine cooling systems. The full distillation procedure is the only method acceptable by Caterpillar to reclaim the used coolant. Contact your Caterpillar for information regarding disposal and recycling of used coolant.
For information regarding disposal and recycling of used coolant:Contact Caterpillar Service Technology Group:Outside Illinois: 1-800-542-TOOLInside Illinois: 1-800-541-TOOLCanada: 1-800-523-TOOLFlush
4. Flush the cooling system with clean water to remove any debris.5. Clean and install all drain plugs and/or close the drain valve(s).6. Fill the cooling system with clean water. Install the filler cap. Operate the engine until warm 49 to 66°C (150 to 120°F).7. Stop the engine and allow the engine to cool. Loosen the coolant filler cap slowly to relieve any pressure, and remove the cap. Remove the cooling system drain plug(s) or open the drain valve. Allow the water to drain. Flush the cooling system with clean water.8. Repeat steps 6 and 7.Fill
9. Fill the cooling system with LLCA. Refer to the refill capacities chart in this manual for the amount of LLCA needed to refill your system.10. Start and run the engine with the filler cap removed. Allow the LLCA to warm, the thermostat to open, and the coolant level to stabilize. Add LLCA if necessary to bring the coolant to the proper level.11. Check the condition of the filler cap gasket. If the gasket is damaged, discard the old filler cap and install a new filler cap. If the gasket is not damaged, use a 9S8140 Service Tool (available from your Caterpillar dealer) to pressure test the filler cap. The correct filler cap pressure is stamped on the face of the filler cap. If the filler cap does not hold the correct pressure, install a new filler cap.12. Start the engine and inspect for coolant leaks and proper operating temperature.
Do not perform this maintenance until you read and understand the material in the Safety and Cooling System Specifications sections of this publication.
Drain/Flush/Replace Coolant (Long Life Coolant/Antifreeze Only)
Caterpillar Long Life Coolant/Antifreeze should be replaced every 6,000 Service Hours or 4 Years, whichever comes first. Only clean water is needed to clean and flush the cooling system when LLCA is drained and replaced.Drain
1. Stop the engine and allow the engine to cool. Loosen the coolant filler cap slowly to relieve any pressure, and remove the cap.2. Remove the radiator drain plug, or open the radiator drain valve (if equipped). Remove the block and oil cooler drain plugs. Remove the drain plug from the bottom of the water pump housing. Allow the coolant to drain.
Dispose of used engine coolant properly or recycle. Various methods have been proposed to reclaim used coolant for reuse in engine cooling systems. The full distillation procedure is the only method acceptable by Caterpillar to reclaim the used coolant. Contact your Caterpillar for information regarding disposal and recycling of used coolant.
For information regarding disposal and recycling of used coolant:Contact Caterpillar Service Technology Group:Outside Illinois: 1-800-542-TOOLInside Illinois: 1-800-541-TOOLCanada: 1-800-523-TOOLFlush
4. Flush the cooling system with clean water to remove any debris.5. Clean and install all drain plugs and/or close the drain valve(s).6. Fill the cooling system with clean water. Install the filler cap. Operate the engine until warm 49 to 66°C (150 to 120°F).7. Stop the engine and allow the engine to cool. Loosen the coolant filler cap slowly to relieve any pressure, and remove the cap. Remove the cooling system drain plug(s) or open the drain valve. Allow the water to drain. Flush the cooling system with clean water.8. Repeat steps 6 and 7.Fill
9. Fill the cooling system with LLCA. Refer to the refill capacities chart in this manual for the amount of LLCA needed to refill your system.10. Start and run the engine with the filler cap removed. Allow the LLCA to warm, the thermostat to open, and the coolant level to stabilize. Add LLCA if necessary to bring the coolant to the proper level.11. Check the condition of the filler cap gasket. If the gasket is damaged, discard the old filler cap and install a new filler cap. If the gasket is not damaged, use a 9S8140 Service Tool (available from your Caterpillar dealer) to pressure test the filler cap. The correct filler cap pressure is stamped on the face of the filler cap. If the filler cap does not hold the correct pressure, install a new filler cap.12. Start the engine and inspect for coolant leaks and proper operating temperature.
Have questions with 106871-0050?
Group cross 106871-0050 ZEXEL
Nissan-Diesel
Nissan-Diesel
106871-0050
INJECTION-PUMP ASSEMBLY