Information injection-pump assembly
BOSCH
9 400 618 003
9400618003
ZEXEL
106861-2640
1068612640
MITSUBISHI
ME441199
me441199

Rating:
Service parts 106861-2640 INJECTION-PUMP ASSEMBLY:
1.
_
7.
COUPLING PLATE
8.
_
9.
_
11.
Nozzle and Holder
12.
Open Pre:MPa(Kqf/cm2)
21.6{220}
15.
NOZZLE SET
Include in #1:
106861-2640
as INJECTION-PUMP ASSEMBLY
Cross reference number
BOSCH
9 400 618 003
9400618003
ZEXEL
106861-2640
1068612640
MITSUBISHI
ME441199
me441199
Zexel num
Bosch num
Firm num
Name
106861-2640
9 400 618 003
ME441199 MITSUBISHI
INJECTION-PUMP ASSEMBLY
8DC9T K 14CD INJECTION PUMP ASSY PE8P PE
8DC9T K 14CD INJECTION PUMP ASSY PE8P PE
Calibration Data:
Adjustment conditions
Test oil
1404 Test oil ISO4113 or {SAEJ967d}
1404 Test oil ISO4113 or {SAEJ967d}
Test oil temperature
degC
40
40
45
Nozzle and nozzle holder
105780-8140
Bosch type code
EF8511/9A
Nozzle
105780-0000
Bosch type code
DN12SD12T
Nozzle holder
105780-2080
Bosch type code
EF8511/9
Opening pressure
MPa
17.2
Opening pressure
kgf/cm2
175
Injection pipe
Outer diameter - inner diameter - length (mm) mm 8-3-600
Outer diameter - inner diameter - length (mm) mm 8-3-600
Overflow valve
131424-4620
Overflow valve opening pressure
kPa
255
255
255
Overflow valve opening pressure
kgf/cm2
2.6
2.6
2.6
Tester oil delivery pressure
kPa
157
157
157
Tester oil delivery pressure
kgf/cm2
1.6
1.6
1.6
Direction of rotation (viewed from drive side)
Right R
Right R
Injection timing adjustment
Direction of rotation (viewed from drive side)
Right R
Right R
Injection order
1-2-7-3-
4-5-6-8
Pre-stroke
mm
4.8
4.75
4.85
Beginning of injection position
Governor side NO.1
Governor side NO.1
Difference between angles 1
Cyl.1-2 deg. 45 44.5 45.5
Cyl.1-2 deg. 45 44.5 45.5
Difference between angles 2
Cal 1-7 deg. 90 89.5 90.5
Cal 1-7 deg. 90 89.5 90.5
Difference between angles 3
Cal 1-3 deg. 135 134.5 135.5
Cal 1-3 deg. 135 134.5 135.5
Difference between angles 4
Cal 1-4 deg. 180 179.5 180.5
Cal 1-4 deg. 180 179.5 180.5
Difference between angles 5
Cal 1-5 deg. 225 224.5 225.5
Cal 1-5 deg. 225 224.5 225.5
Difference between angles 6
Cal 1-6 deg. 270 269.5 270.5
Cal 1-6 deg. 270 269.5 270.5
Difference between angles 7
Cal 1-8 deg. 315 314.5 315.5
Cal 1-8 deg. 315 314.5 315.5
Injection quantity adjustment
Adjusting point
A
Rack position
9.6
Pump speed
r/min
700
700
700
Average injection quantity
mm3/st.
137.5
134.5
140.5
Max. variation between cylinders
%
0
-3
3
Basic
*
Fixing the lever
*
Injection quantity adjustment_02
Adjusting point
C
Rack position
6.3+-0.5
Pump speed
r/min
225
225
225
Average injection quantity
mm3/st.
12
9.4
14.6
Max. variation between cylinders
%
0
-15
15
Fixing the rack
*
Injection quantity adjustment_03
Adjusting point
D
Rack position
-
Pump speed
r/min
200
200
200
Average injection quantity
mm3/st.
205
185
225
Fixing the lever
*
Remarks
After startup boost setting
After startup boost setting
Timer adjustment
Pump speed
r/min
1100++
Advance angle
deg.
0
0
0
Remarks
Do not advance until starting N = 1100.
Do not advance until starting N = 1100.
Timer adjustment_02
Pump speed
r/min
-
Advance angle
deg.
3.5
3.5
3.5
Remarks
Measure the actual speed, stop
Measure the actual speed, stop
Test data Ex:
Governor adjustment
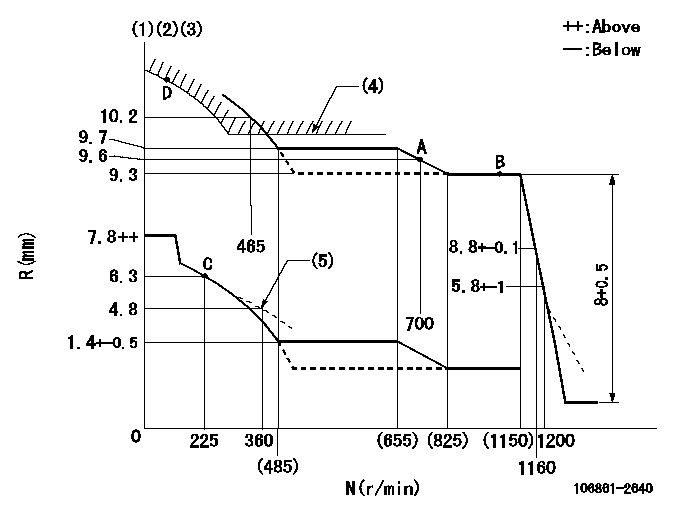
N:Pump speed
R:Rack position (mm)
(1)Lever ratio: RT
(2)Target shim dimension: TH
(3)Tolerance for racks not indicated: +-0.05mm.
(4)Excess fuel setting for starting: SXL
(5)Damper spring setting
----------
RT=1 TH=2.9mm SXL=9.8+-0.1mm
----------
----------
RT=1 TH=2.9mm SXL=9.8+-0.1mm
----------
Speed control lever angle

F:Full speed
----------
----------
a=(13.5deg)+-5deg
----------
----------
a=(13.5deg)+-5deg
0000000901

F:Full load
I:Idle
(1)Stopper bolt setting
----------
----------
a=10deg+-5deg b=31deg+-3deg
----------
----------
a=10deg+-5deg b=31deg+-3deg
Stop lever angle
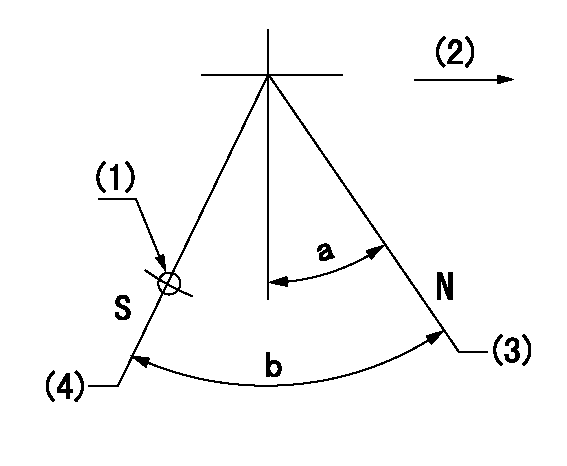
N:Pump normal
S:Stop the pump.
(1)Use the hole at R = aa
(2)Drive side
(3)-
(4)Rack position = bb, set the stopper bolt.
----------
aa=32mm bb=3.5-0.5mm
----------
a=10.5deg+-5deg b=57.5deg+7deg-5deg
----------
aa=32mm bb=3.5-0.5mm
----------
a=10.5deg+-5deg b=57.5deg+7deg-5deg
0000001501 MICRO SWITCH
Adjustment of the micro-switch
Adjust the bolt to obtain the following lever position when the micro-switch is ON.
(1)Speed N1
(2)Rack position Ra
----------
N1=325r/min Ra=6+-0.1mm
----------
----------
N1=325r/min Ra=6+-0.1mm
----------
0000001601 RACK SENSOR

V1:Supply voltage
V2f:Full side output voltage
V2i:Idle side output voltage
(A) Black
(B) Yellow
(C) Red
(D) Trimmer
(E): Shaft
(F) Nut
(G) Load lever
1. Load sensor adjustment
(1)Connect as shown in the above diagram and apply supply voltage V1.
(2)Hold the load lever (G) against the full side.
(3)Turn the shaft so that the voltage between (A) and (B) is V2.
(4)Hold the load lever (G) against the idle side.
(5)Adjust (D) so that the voltage between (A) and (B) is V2i.
(6)Repeat the above adjustments.
(7)Tighten the nut (F) at the point satisfying the standards.
(8)Hold the load lever against the full side stopper and the idle side stopper.
(9)At this time, confirm that the full side output voltage is V2f and the idle side output voltage is V2i.
----------
V1=5+-0.02V V2f=0.15+0.03V V2i=2.35-0.03V
----------
----------
V1=5+-0.02V V2f=0.15+0.03V V2i=2.35-0.03V
----------
Timing setting

(1)Pump vertical direction
(2)Coupling's key groove position at No 1 cylinder's beginning of injection
(3)-
(4)-
----------
----------
a=(40deg)
----------
----------
a=(40deg)
Information:
Crankshaft Grinding Specifications
The dimensions and finish for grinding crankshafts are as follows:Diameter (A) for connecting rod bearing journals is;.010 in. (0.25 mm) Undersize ... 2.7396 .0006 in.(69.586 0.015 mm).020 in. (0.51 mm) Undersize ... 2.7296 .0006 in.(69.332 0.015 mm).050 in. (1.27 mm) Undersize ... 2.6996 .0006 in.(68.570 0.015 mm)Surface finish must be 10 micro inches (0.25 micrometers) or less.Radius (B) must be .100 .010 in. (2.54 0.25 mm).Surface finish must be 63 micro inches (1.6 micrometers) or less.The radius must blend smoothly with the newly machined journals.
DIMENSIONS FOR GRINDING
A. Diameter of connecting rod bearing journals. B. Radius on connecting rod bearing journals. C. Width to grind journals for the connecting rods. D. Diameter of main bearing journals. E. Radius on main bearing journals. F. Width to grind journals for the main bearings.Width (C) is 2.314 .003 in. (58.77 0.08 mm)Diameter (D) for main bearing journals is:.010 in. (0.25 mm) Undersize ... 3.4895 .0006 in.(88.633 0.015 mm).020 in. (0.51 mm) Undersize ... 3.4795 .0006 in.(88.379 0.015 mm).050 in. (1.27 mm) Undersize ... 3.4495 .0006 in.(87.617 0.015 mm)Surface finish must be 10 micro inches (0.25 micrometers) or less.Radius (E) must be .095 .010 in. (2.41 0.25 mm)Surface finish must be 63 micro inches (1.6 micrometers) or less.The radius must blend smoothly with the newly machined journals.Width (F) is 1.258 .002 in. (31.95 0.05 mm) for number 4 main bearing journal. Surface finish on the thrust faces of the number 4 main must be 18 micro inches (0.45 micrometers) or less.Width (F) is 1.268 + .020 - .010 in. (32.21 + 0.51 - 0.25 mm) for number 2, 3, and 5 main bearing journals.There is no width (F) for number 1 main bearing journal.When grinding a crankshaft, no material can be removed from the crankshaft webs or counterweights.Crankshaft Gear Removal
Remove the gear using an 8B7548 Push Puller, 8B7551 Bearing Pulling Attachment, 8B75621 Step Plate, and 8H684 Ratchet Box Wrench.
PULLING CRANKSHAFT GEARThe 1P820 Hydraulic Puller Group can also be used to pull gear from crankshaft. Tools required are 1P820 Hydraulic Puller Group, 8B7551 Bearing Pulling Attachment, 8B7549 Puller legs (two), 8B7561 Step Plate, 3H465 Plate (four), 1B4207 Nut (two), and 5P3100 Pump Group.
USING HYDRAULIC PULLERCrankshaft Gear Installation
1. Install the key in keyway of crankshaft. Remove all burrs from key and keyway inside of crankshaft gear.2. Heat gear to 500°F (260°C) maximum.3. Install gear on crankshaft with timing mark on gear facing front of crankshaft.Crankshaft Front Oil Seal Removal
Remove the crankshaft front pulley. Use the 1P3075 Puller Group to remove the crankshaft front oil seal.
REMOVING FRONT OIL SEAL (Typical Example)Remove Crankshaft Rear Seal And Wear Sleeve
Remove the crankshaft rear oil seal with the 1P3075 Puller Group.
REMOVING REAR OIL SEALInstall a 5P7338 Distorter Ring from the 5P7318 Wear Sleeve Distorter Group, in the rear seal bore.
REMOVING REAR WEAR SLEEVE (Typical Example)Install 5P7312 Distorter between distorter ring and wear sleeve. Turn the distorter until the
The dimensions and finish for grinding crankshafts are as follows:Diameter (A) for connecting rod bearing journals is;.010 in. (0.25 mm) Undersize ... 2.7396 .0006 in.(69.586 0.015 mm).020 in. (0.51 mm) Undersize ... 2.7296 .0006 in.(69.332 0.015 mm).050 in. (1.27 mm) Undersize ... 2.6996 .0006 in.(68.570 0.015 mm)Surface finish must be 10 micro inches (0.25 micrometers) or less.Radius (B) must be .100 .010 in. (2.54 0.25 mm).Surface finish must be 63 micro inches (1.6 micrometers) or less.The radius must blend smoothly with the newly machined journals.
DIMENSIONS FOR GRINDING
A. Diameter of connecting rod bearing journals. B. Radius on connecting rod bearing journals. C. Width to grind journals for the connecting rods. D. Diameter of main bearing journals. E. Radius on main bearing journals. F. Width to grind journals for the main bearings.Width (C) is 2.314 .003 in. (58.77 0.08 mm)Diameter (D) for main bearing journals is:.010 in. (0.25 mm) Undersize ... 3.4895 .0006 in.(88.633 0.015 mm).020 in. (0.51 mm) Undersize ... 3.4795 .0006 in.(88.379 0.015 mm).050 in. (1.27 mm) Undersize ... 3.4495 .0006 in.(87.617 0.015 mm)Surface finish must be 10 micro inches (0.25 micrometers) or less.Radius (E) must be .095 .010 in. (2.41 0.25 mm)Surface finish must be 63 micro inches (1.6 micrometers) or less.The radius must blend smoothly with the newly machined journals.Width (F) is 1.258 .002 in. (31.95 0.05 mm) for number 4 main bearing journal. Surface finish on the thrust faces of the number 4 main must be 18 micro inches (0.45 micrometers) or less.Width (F) is 1.268 + .020 - .010 in. (32.21 + 0.51 - 0.25 mm) for number 2, 3, and 5 main bearing journals.There is no width (F) for number 1 main bearing journal.When grinding a crankshaft, no material can be removed from the crankshaft webs or counterweights.Crankshaft Gear Removal
Remove the gear using an 8B7548 Push Puller, 8B7551 Bearing Pulling Attachment, 8B75621 Step Plate, and 8H684 Ratchet Box Wrench.
PULLING CRANKSHAFT GEARThe 1P820 Hydraulic Puller Group can also be used to pull gear from crankshaft. Tools required are 1P820 Hydraulic Puller Group, 8B7551 Bearing Pulling Attachment, 8B7549 Puller legs (two), 8B7561 Step Plate, 3H465 Plate (four), 1B4207 Nut (two), and 5P3100 Pump Group.
USING HYDRAULIC PULLERCrankshaft Gear Installation
1. Install the key in keyway of crankshaft. Remove all burrs from key and keyway inside of crankshaft gear.2. Heat gear to 500°F (260°C) maximum.3. Install gear on crankshaft with timing mark on gear facing front of crankshaft.Crankshaft Front Oil Seal Removal
Remove the crankshaft front pulley. Use the 1P3075 Puller Group to remove the crankshaft front oil seal.
REMOVING FRONT OIL SEAL (Typical Example)Remove Crankshaft Rear Seal And Wear Sleeve
Remove the crankshaft rear oil seal with the 1P3075 Puller Group.
REMOVING REAR OIL SEALInstall a 5P7338 Distorter Ring from the 5P7318 Wear Sleeve Distorter Group, in the rear seal bore.
REMOVING REAR WEAR SLEEVE (Typical Example)Install 5P7312 Distorter between distorter ring and wear sleeve. Turn the distorter until the
Have questions with 106861-2640?
Group cross 106861-2640 ZEXEL
Mitsubishi
Mitsubishi
Mitsubishi
106861-2640
9 400 618 003
ME441199
INJECTION-PUMP ASSEMBLY
8DC9T
8DC9T