Information injection-pump assembly
ZEXEL
106693-6260
1066936260
ISUZU
8943920361
8943920361
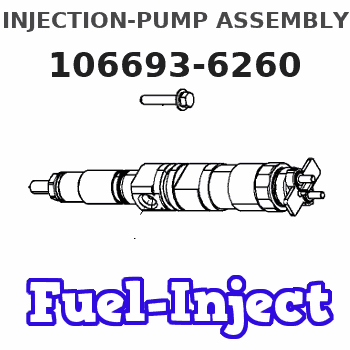
Rating:
Service parts 106693-6260 INJECTION-PUMP ASSEMBLY:
1.
_
7.
COUPLING PLATE
8.
_
9.
_
11.
Nozzle and Holder
8-94390-519-0
12.
Open Pre:MPa(Kqf/cm2)
15.7{160}/22.1{225}
14.
NOZZLE
Include in #1:
106693-6260
as INJECTION-PUMP ASSEMBLY
Cross reference number
ZEXEL
106693-6260
1066936260
ISUZU
8943920361
8943920361
Zexel num
Bosch num
Firm num
Name
Calibration Data:
Adjustment conditions
Test oil
1404 Test oil ISO4113 or {SAEJ967d}
1404 Test oil ISO4113 or {SAEJ967d}
Test oil temperature
degC
40
40
45
Nozzle and nozzle holder
105780-8250
Bosch type code
1 688 901 101
Nozzle
105780-0120
Bosch type code
1 688 901 990
Nozzle holder
105780-2190
Opening pressure
MPa
20.7
Opening pressure
kgf/cm2
211
Injection pipe
Outer diameter - inner diameter - length (mm) mm 8-3-600
Outer diameter - inner diameter - length (mm) mm 8-3-600
Overflow valve
131424-8620
Overflow valve opening pressure
kPa
206
172
240
Overflow valve opening pressure
kgf/cm2
2.1
1.75
2.45
Tester oil delivery pressure
kPa
255
255
255
Tester oil delivery pressure
kgf/cm2
2.6
2.6
2.6
Direction of rotation (viewed from drive side)
Left L
Left L
Injection timing adjustment
Direction of rotation (viewed from drive side)
Left L
Left L
Injection order
1-5-3-6-
2-4
Pre-stroke
mm
3.6
3.57
3.63
Rack position
Point A R=A
Point A R=A
Beginning of injection position
Governor side NO.1
Governor side NO.1
Difference between angles 1
Cal 1-5 deg. 60 59.75 60.25
Cal 1-5 deg. 60 59.75 60.25
Difference between angles 2
Cal 1-3 deg. 120 119.75 120.25
Cal 1-3 deg. 120 119.75 120.25
Difference between angles 3
Cal 1-6 deg. 180 179.75 180.25
Cal 1-6 deg. 180 179.75 180.25
Difference between angles 4
Cyl.1-2 deg. 240 239.75 240.25
Cyl.1-2 deg. 240 239.75 240.25
Difference between angles 5
Cal 1-4 deg. 300 299.75 300.25
Cal 1-4 deg. 300 299.75 300.25
Injection quantity adjustment
Adjusting point
-
Rack position
11.3
Pump speed
r/min
700
700
700
Average injection quantity
mm3/st.
100
98
102
Max. variation between cylinders
%
0
-4
4
Basic
*
Fixing the rack
*
Standard for adjustment of the maximum variation between cylinders
*
Injection quantity adjustment_02
Adjusting point
Z
Rack position
8+-0.5
Pump speed
r/min
470
470
470
Average injection quantity
mm3/st.
12.5
9.3
15.7
Max. variation between cylinders
%
0
-13
13
Fixing the rack
*
Standard for adjustment of the maximum variation between cylinders
*
Injection quantity adjustment_03
Adjusting point
A
Rack position
R1(11.3)
Pump speed
r/min
700
700
700
Average injection quantity
mm3/st.
100
99
101
Basic
*
Fixing the lever
*
Boost pressure
kPa
57.3
57.3
Boost pressure
mmHg
430
430
Injection quantity adjustment_04
Adjusting point
B
Rack position
R1+0.5
Pump speed
r/min
1350
1350
1350
Average injection quantity
mm3/st.
90.5
86.5
94.5
Fixing the lever
*
Boost pressure
kPa
57.3
57.3
Boost pressure
mmHg
430
430
Boost compensator adjustment
Pump speed
r/min
500
500
500
Rack position
R2-1.25
Boost pressure
kPa
12
10.7
13.3
Boost pressure
mmHg
90
80
100
Boost compensator adjustment_02
Pump speed
r/min
500
500
500
Rack position
R2(R1-0.
15)
Boost pressure
kPa
44
44
44
Boost pressure
mmHg
330
330
330
Timer adjustment
Pump speed
r/min
900--
Advance angle
deg.
0
0
0
Load
3/5
Remarks
Start
Start
Timer adjustment_02
Pump speed
r/min
850
Advance angle
deg.
0.3
Load
3/5
Timer adjustment_03
Pump speed
r/min
-
Advance angle
deg.
1.5
1
2
Load
3/5
Remarks
Measure the actual speed.
Measure the actual speed.
Timer adjustment_04
Pump speed
r/min
1075
Advance angle
deg.
1.5
1
2
Load
4/5
Timer adjustment_05
Pump speed
r/min
1350
Advance angle
deg.
5.5
5
6
Load
4/5
Remarks
Finish
Finish
Test data Ex:
Governor adjustment

N:Pump speed
R:Rack position (mm)
(1)Torque cam stamping: T1
(2)Tolerance for racks not indicated: +-0.05mm.
(3)Boost compensator stroke: BCL
----------
T1=AD83 BCL=1.25+-0.1mm
----------
----------
T1=AD83 BCL=1.25+-0.1mm
----------
Speed control lever angle

F:Full speed
I:Idle
(1)Use the pin at R = aa
(2)Stopper bolt set position 'H'
----------
aa=40mm
----------
a=20deg+-5deg b=37deg+-3deg
----------
aa=40mm
----------
a=20deg+-5deg b=37deg+-3deg
Stop lever angle

N:Pump normal
S:Stop the pump.
(1)Use the pin at R = aa
(2)Set the stopper bolt at rack position = bb, speed = cc and confirm non-injection.
----------
aa=40mm bb=1.5+-0.3mm cc=0r/min
----------
a=12deg+-5deg b=44deg+-5deg
----------
aa=40mm bb=1.5+-0.3mm cc=0r/min
----------
a=12deg+-5deg b=44deg+-5deg
0000001501 AIR CYLINDER

1. (1) Set the speed lever to idle.
(2)Screw in air cylinder (A)
(3)Set the clearance from the speed lever (B) at approximately L.
----------
L=(1)mm
----------
----------
L=(1)mm
----------
Timing setting

(1)Pump vertical direction
(2)Position of timer's threaded hole at No 1 cylinder's beginning of injection
(3)B.T.D.C.: aa
(4)-
----------
aa=7deg
----------
a=(50deg)
----------
aa=7deg
----------
a=(50deg)
Information:
In this service manual, the Mitsubishi Diesel Engine (standard model for land use) specifications, maintenance standards and adjustment procedure as well as service procedures such as disassembly, inspection, repair and reassembly are arranged in groups for quick reference. There are separate manuals for the fuel injection pump, governor and turbocharger.A short summary of each group is given in the General Contents, and there is also a table of contents at the beginning of each group.Regarding engine operation and periodical maintenance, refer to the Operation & Maintenance Manual. For component parts and ordering of service parts, refer to the Parts Catalog. Structure and function of the engine are described in various training manuals.Methods of Indication
(1) Parts shown in illustrations and described in text are numbered to correspond with the sequence of disassembly.(2) Inspections to be conducted during disassembly are indicated in a box
in disassembled views.(3) Maintenance standards for inspection and repair are described in text where they are relevant, are also listed in Group 1 in the General Contents.(4) The sequence in which parts are to be assembled is summarized below each assembled view. Such as:
(5) The following marks are used in this manual to emphasize important safety cautions.
Indicates a highly hazardous situation which, if not avoided, can result in death or serious injury.
Indicates a potentially hazardous situation which, if not avoided, can result in death or serious injury.
Indicates a potentially hazardous situation which, if not avoided, can result in minor or moderate injury.
Indicates a potentially hazardous situation which, if not avoided, can result in property damage. Note: Indicates important information or information which is useful for engine operation or maintenance.(6) Tightening torque under wet conditions is indicated as, "[Wet]". When so indicated, apply engine oil to the threaded portion of the fastener. Unless indicated as such, the tightening torque is to be assumed in the dry condition.Terms Used in This Manual
Nominal value - Indicates the standard dimension of a part to be measured.Standard - Indicates the dimension of a part, the clearance between parts, or the standard performance. Since the value is indicated in a range needed for inspection, it is different from the design value.Limit - A part must be repaired or replaced with a new part when it reaches the limit value.Abbreviations, Standard, Etc.
* BTDC = Before Top Dead Center* ATDC = After Top Dead Center* BBDC = Before Bottom Dead Center* ABDC = After Bottom Dead Center* TIR = Total Indicated Reading* API = American Petroleum Institute* ASTM = American Society for Testing and Materials* JIS = Japanese Industrial Standards* LLC = Long Life Coolant* MIL = Military Specifications and Standards (U.S.)* MSDS = Material Safety Data Sheet* SAE = Society of Automotive Engineers (U.S.)Units of Measurement
Measurements are based on the International System of Units (SI), and their converted metric values are indicated in parentheses ( ). For metric conversion, the following rates are used.* Pressure: 1 MPa = 10.197 kgf/cm2* Torque: 1 N m = 0.10197 kgf m* Force: 1 N
(1) Parts shown in illustrations and described in text are numbered to correspond with the sequence of disassembly.(2) Inspections to be conducted during disassembly are indicated in a box
in disassembled views.(3) Maintenance standards for inspection and repair are described in text where they are relevant, are also listed in Group 1 in the General Contents.(4) The sequence in which parts are to be assembled is summarized below each assembled view. Such as:
(5) The following marks are used in this manual to emphasize important safety cautions.
Indicates a highly hazardous situation which, if not avoided, can result in death or serious injury.
Indicates a potentially hazardous situation which, if not avoided, can result in death or serious injury.
Indicates a potentially hazardous situation which, if not avoided, can result in minor or moderate injury.
Indicates a potentially hazardous situation which, if not avoided, can result in property damage. Note: Indicates important information or information which is useful for engine operation or maintenance.(6) Tightening torque under wet conditions is indicated as, "[Wet]". When so indicated, apply engine oil to the threaded portion of the fastener. Unless indicated as such, the tightening torque is to be assumed in the dry condition.Terms Used in This Manual
Nominal value - Indicates the standard dimension of a part to be measured.Standard - Indicates the dimension of a part, the clearance between parts, or the standard performance. Since the value is indicated in a range needed for inspection, it is different from the design value.Limit - A part must be repaired or replaced with a new part when it reaches the limit value.Abbreviations, Standard, Etc.
* BTDC = Before Top Dead Center* ATDC = After Top Dead Center* BBDC = Before Bottom Dead Center* ABDC = After Bottom Dead Center* TIR = Total Indicated Reading* API = American Petroleum Institute* ASTM = American Society for Testing and Materials* JIS = Japanese Industrial Standards* LLC = Long Life Coolant* MIL = Military Specifications and Standards (U.S.)* MSDS = Material Safety Data Sheet* SAE = Society of Automotive Engineers (U.S.)Units of Measurement
Measurements are based on the International System of Units (SI), and their converted metric values are indicated in parentheses ( ). For metric conversion, the following rates are used.* Pressure: 1 MPa = 10.197 kgf/cm2* Torque: 1 N m = 0.10197 kgf m* Force: 1 N