Information injection-pump assembly
ZEXEL
106693-1170
1066931170
ISUZU
1156016091
1156016091
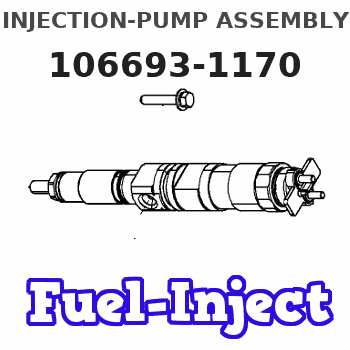
Rating:
Service parts 106693-1170 INJECTION-PUMP ASSEMBLY:
1.
_
7.
COUPLING PLATE
8.
_
9.
_
11.
Nozzle and Holder
1-15300-041-2
12.
Open Pre:MPa(Kqf/cm2)
22.1{225}
15.
NOZZLE SET
Include in #1:
106693-1170
as INJECTION-PUMP ASSEMBLY
Cross reference number
ZEXEL
106693-1170
1066931170
ISUZU
1156016091
1156016091
Zexel num
Bosch num
Firm num
Name
Calibration Data:
Adjustment conditions
Test oil
1404 Test oil ISO4113 or {SAEJ967d}
1404 Test oil ISO4113 or {SAEJ967d}
Test oil temperature
degC
40
40
45
Nozzle and nozzle holder
105780-8140
Bosch type code
EF8511/9A
Nozzle
105780-0000
Bosch type code
DN12SD12T
Nozzle holder
105780-2080
Bosch type code
EF8511/9
Opening pressure
MPa
17.2
Opening pressure
kgf/cm2
175
Injection pipe
Outer diameter - inner diameter - length (mm) mm 8-3-600
Outer diameter - inner diameter - length (mm) mm 8-3-600
Overflow valve
131424-0220
Overflow valve opening pressure
kPa
127
107
147
Overflow valve opening pressure
kgf/cm2
1.3
1.1
1.5
Tester oil delivery pressure
kPa
157
157
157
Tester oil delivery pressure
kgf/cm2
1.6
1.6
1.6
Direction of rotation (viewed from drive side)
Right R
Right R
Injection timing adjustment
Direction of rotation (viewed from drive side)
Right R
Right R
Injection order
1-4-2-6-
3-5
Pre-stroke
mm
3
2.95
3.05
Beginning of injection position
Drive side NO.1
Drive side NO.1
Difference between angles 1
Cal 1-4 deg. 60 59.5 60.5
Cal 1-4 deg. 60 59.5 60.5
Difference between angles 2
Cyl.1-2 deg. 120 119.5 120.5
Cyl.1-2 deg. 120 119.5 120.5
Difference between angles 3
Cal 1-6 deg. 180 179.5 180.5
Cal 1-6 deg. 180 179.5 180.5
Difference between angles 4
Cal 1-3 deg. 240 239.5 240.5
Cal 1-3 deg. 240 239.5 240.5
Difference between angles 5
Cal 1-5 deg. 300 299.5 300.5
Cal 1-5 deg. 300 299.5 300.5
Injection quantity adjustment
Adjusting point
A
Rack position
8.9
Pump speed
r/min
650
650
650
Average injection quantity
mm3/st.
133.9
131.9
135.9
Max. variation between cylinders
%
0
-3
3
Basic
*
Fixing the lever
*
Injection quantity adjustment_02
Adjusting point
B
Rack position
5.3+-0.5
Pump speed
r/min
225
225
225
Average injection quantity
mm3/st.
12.6
9.4
15.8
Max. variation between cylinders
%
0
-13
13
Fixing the rack
*
Timer adjustment
Pump speed
r/min
500
Advance angle
deg.
0.3
Timer adjustment_02
Pump speed
r/min
700
Advance angle
deg.
1
0.1
1
Timer adjustment_03
Pump speed
r/min
900
Advance angle
deg.
1.2
0.7
1.7
Timer adjustment_04
Pump speed
r/min
1100
Advance angle
deg.
2
1.5
2.5
Remarks
Finish
Finish
Test data Ex:
Governor adjustment

N:Pump speed
R:Rack position (mm)
(1)Lever ratio: RT
(2)Target shim dimension: TH
(3)Damper spring setting: DL
(4)Excess fuel setting for starting: SXL
(5)Rack difference between N = N1 and N = N2
----------
RT=1 TH=2.7mm DL=3.7-0.5mm SXL=9.2+0.2mm N1=1100r/min N2=650r/min
----------
----------
RT=1 TH=2.7mm DL=3.7-0.5mm SXL=9.2+0.2mm N1=1100r/min N2=650r/min
----------
Speed control lever angle
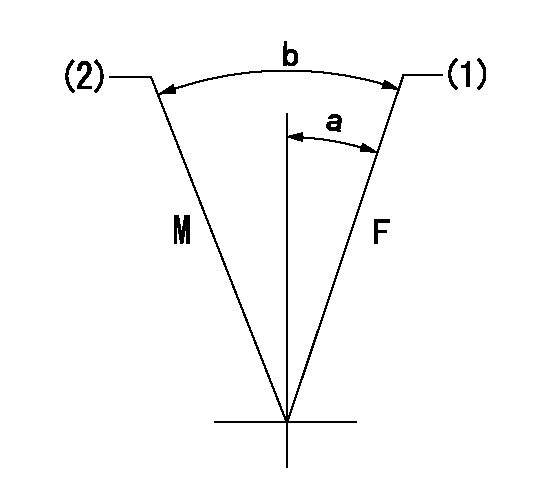
F:Full speed
M:Minimum-maximum speed
(1)Set the pump speed at aa. ( At delivery )
(2)Set the speed at bb. Set using two nuts.
----------
aa=1100r/min bb=550r/min
----------
a=1.5deg+-5deg b=8.5deg+-5deg
----------
aa=1100r/min bb=550r/min
----------
a=1.5deg+-5deg b=8.5deg+-5deg
0000000901

F:Full load
I:Idle
(1)Stopper bolt setting
(2)Attach the return spring to the upper hole and adjust.
----------
----------
a=30deg+-5deg b=31deg+-3deg
----------
----------
a=30deg+-5deg b=31deg+-3deg
Stop lever angle
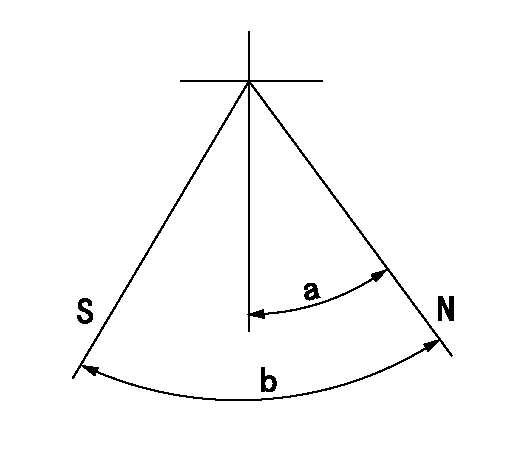
N:Pump normal
S:Stop the pump.
----------
----------
a=32deg+-5deg b=64deg+-5deg
----------
----------
a=32deg+-5deg b=64deg+-5deg
Timing setting
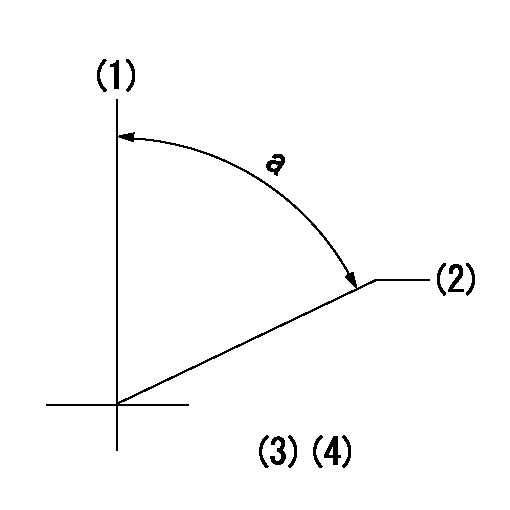
(1)Pump vertical direction
(2)Position of timer's threaded hole at No 1 cylinder's beginning of injection
(3)B.T.D.C.: aa
(4)-
----------
aa=21deg
----------
a=(70deg)
----------
aa=21deg
----------
a=(70deg)
Information:
Important
Clean the oil supply line to the compressor and run the engine for a few seconds to be sure the oil supply is flowing freely.Connect oil and/or air pipes, ensuring that the air cleaner or filter is clean and properly installed.Check after Installation
With the compressor running, check for noisy operation and oil and air leaks.Dismantling
Marking before dismantling
The compressor should have the following items marked to show the correct relationship prior to dismantling.1. Position of cylinder head in relation to cylinder and crankcase.2. Position of end-cover(s) in relation to crankcase.3. Position of crankshaft in relation to crankcase.Removing and Dismantling Cylinder Head and Cylinder
Remove the unloader cap and copper washer and withdraw the unloader plunger assembly and spring.Remove the delivery valve cap and copper washer, and remove delivery valve spring and seat retaining spring.Unscrew the four nuts and washers from cylinder head studs and lift off cylinder head. Remove the joint.Remove the delivery valve and screw out the valve seat.Withdraw inlet valve spring guide. (A simple extractor can be made from two 1/4 in U.N.F. bolts and a strip of metal formed to bridge the guide). Remove the inlet valve spring, inlet valve and valve seat.Withdraw cylinder and remove the joint.Removing and Dismantling Piston and Connecting Rod Assemblies
Remove the compressor mounting bracket and joint.Turn the crankshaft to B.D.C. position and release the tabs of the locking strap. Unscrew the two bolts and remove the connecting rod cap. Withdraw piston assembly and replace connecting rod cap.Remove the piston rings from the piston. If the piston is to be detached from the connecting rod, release one gudgeon pin retaining circlip and press the gudgeon pin from the piston and connecting rod.Removing Crankshaft
Remove compressor drive gear.Remove drive key from crankshaft.Unscrew the four setscrews or nuts together with washers securing the rear end-cover to crankcase. Withdraw the end-cover, plain bearing, thrust washer and joint.Unscrew the four setscrews or nuts securing the drive end-cover, and withdraw the end-cover complete with crankshaft and joint. Tap crankshaft with bearing from drive end-cover.Cleaning
Ensure that all carbon is removed from the cylinder head. Check that the air passages in the head and the oilways in the crankcase, where applicable, rear end-cover and crankshaft are clear and clean.Clean inlet and discharge valves, not damaged or worn excessively, by lapping them on a sheet of crocus cloth held on a flat surface.Inspection of Parts
Cylinder
Check cylinder bore for excessive wear, out-of-round or scoring. If scored or out-of-round more than 0.002 in (0,05 mm) or tapered more than 0.003 in (0,08 mm) cylinder should be rebored. The original cylinder bore is to the limits 2.6255/2.6265 in (66,69/66,71 mm) and the clearance for the piston is 0.002/0.003 in (0,05/0,08 mm). Check for wear in cylinder bore and rectify in accordance with following table:-Piston and Connecting Rod
Inspect piston for scores, cracks or damage of any kind. Check fit of rings in ring grooves, clearance should be 0.0005/0.0025 in (0,01/0,06 mm). Install rings in cylinder and check that gaps are 0.002/0.007 in (0,08/0,18 mm). Check fit
Clean the oil supply line to the compressor and run the engine for a few seconds to be sure the oil supply is flowing freely.Connect oil and/or air pipes, ensuring that the air cleaner or filter is clean and properly installed.Check after Installation
With the compressor running, check for noisy operation and oil and air leaks.Dismantling
Marking before dismantling
The compressor should have the following items marked to show the correct relationship prior to dismantling.1. Position of cylinder head in relation to cylinder and crankcase.2. Position of end-cover(s) in relation to crankcase.3. Position of crankshaft in relation to crankcase.Removing and Dismantling Cylinder Head and Cylinder
Remove the unloader cap and copper washer and withdraw the unloader plunger assembly and spring.Remove the delivery valve cap and copper washer, and remove delivery valve spring and seat retaining spring.Unscrew the four nuts and washers from cylinder head studs and lift off cylinder head. Remove the joint.Remove the delivery valve and screw out the valve seat.Withdraw inlet valve spring guide. (A simple extractor can be made from two 1/4 in U.N.F. bolts and a strip of metal formed to bridge the guide). Remove the inlet valve spring, inlet valve and valve seat.Withdraw cylinder and remove the joint.Removing and Dismantling Piston and Connecting Rod Assemblies
Remove the compressor mounting bracket and joint.Turn the crankshaft to B.D.C. position and release the tabs of the locking strap. Unscrew the two bolts and remove the connecting rod cap. Withdraw piston assembly and replace connecting rod cap.Remove the piston rings from the piston. If the piston is to be detached from the connecting rod, release one gudgeon pin retaining circlip and press the gudgeon pin from the piston and connecting rod.Removing Crankshaft
Remove compressor drive gear.Remove drive key from crankshaft.Unscrew the four setscrews or nuts together with washers securing the rear end-cover to crankcase. Withdraw the end-cover, plain bearing, thrust washer and joint.Unscrew the four setscrews or nuts securing the drive end-cover, and withdraw the end-cover complete with crankshaft and joint. Tap crankshaft with bearing from drive end-cover.Cleaning
Ensure that all carbon is removed from the cylinder head. Check that the air passages in the head and the oilways in the crankcase, where applicable, rear end-cover and crankshaft are clear and clean.Clean inlet and discharge valves, not damaged or worn excessively, by lapping them on a sheet of crocus cloth held on a flat surface.Inspection of Parts
Cylinder
Check cylinder bore for excessive wear, out-of-round or scoring. If scored or out-of-round more than 0.002 in (0,05 mm) or tapered more than 0.003 in (0,08 mm) cylinder should be rebored. The original cylinder bore is to the limits 2.6255/2.6265 in (66,69/66,71 mm) and the clearance for the piston is 0.002/0.003 in (0,05/0,08 mm). Check for wear in cylinder bore and rectify in accordance with following table:-Piston and Connecting Rod
Inspect piston for scores, cracks or damage of any kind. Check fit of rings in ring grooves, clearance should be 0.0005/0.0025 in (0,01/0,06 mm). Install rings in cylinder and check that gaps are 0.002/0.007 in (0,08/0,18 mm). Check fit