Information injection-pump assembly
ZEXEL
106692-9151
1066929151
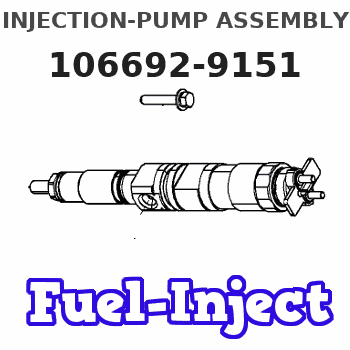
Rating:
Service parts 106692-9151 INJECTION-PUMP ASSEMBLY:
1.
_
5.
AUTOM. ADVANCE MECHANIS
6.
COUPLING PLATE
7.
COUPLING PLATE
8.
_
9.
_
10.
NOZZLE AND HOLDER ASSY
11.
Nozzle and Holder
12.
Open Pre:MPa(Kqf/cm2)
13.
NOZZLE-HOLDER
14.
NOZZLE
15.
NOZZLE SET
Include in #1:
106692-9151
as INJECTION-PUMP ASSEMBLY
Cross reference number
ZEXEL
106692-9151
1066929151
Zexel num
Bosch num
Firm num
Name
106692-9151
INJECTION-PUMP ASSEMBLY
Calibration Data:
Adjustment conditions
Test oil
1404 Test oil ISO4113 or {SAEJ967d}
1404 Test oil ISO4113 or {SAEJ967d}
Test oil temperature
degC
40
40
45
Nozzle and nozzle holder
105780-8140
Bosch type code
EF8511/9A
Nozzle
105780-0000
Bosch type code
DN12SD12T
Nozzle holder
105780-2080
Bosch type code
EF8511/9
Opening pressure
MPa
17.2
Opening pressure
kgf/cm2
175
Injection pipe
Outer diameter - inner diameter - length (mm) mm 8-3-600
Outer diameter - inner diameter - length (mm) mm 8-3-600
Overflow valve
131424-1520
Overflow valve opening pressure
kPa
157
123
191
Overflow valve opening pressure
kgf/cm2
1.6
1.25
1.95
Tester oil delivery pressure
kPa
157
157
157
Tester oil delivery pressure
kgf/cm2
1.6
1.6
1.6
Direction of rotation (viewed from drive side)
Right R
Right R
Injection timing adjustment
Direction of rotation (viewed from drive side)
Right R
Right R
Injection order
1-4-2-6-
3-5
Pre-stroke
mm
2.9
2.85
2.95
Beginning of injection position
Drive side NO.1
Drive side NO.1
Difference between angles 1
Cal 1-4 deg. 60 59.5 60.5
Cal 1-4 deg. 60 59.5 60.5
Difference between angles 2
Cyl.1-2 deg. 120 119.5 120.5
Cyl.1-2 deg. 120 119.5 120.5
Difference between angles 3
Cal 1-6 deg. 180 179.5 180.5
Cal 1-6 deg. 180 179.5 180.5
Difference between angles 4
Cal 1-3 deg. 240 239.5 240.5
Cal 1-3 deg. 240 239.5 240.5
Difference between angles 5
Cal 1-5 deg. 300 299.5 300.5
Cal 1-5 deg. 300 299.5 300.5
Injection quantity adjustment
Adjusting point
A
Rack position
8.8
Pump speed
r/min
900
900
900
Each cylinder's injection qty
mm3/st.
125
122.5
127.5
Basic
*
Fixing the rack
*
Injection quantity adjustment_02
Adjusting point
B
Rack position
5.3+-0.5
Pump speed
r/min
200
200
200
Each cylinder's injection qty
mm3/st.
27.5
24.7
30.3
Fixing the rack
*
Test data Ex:
Governor adjustment
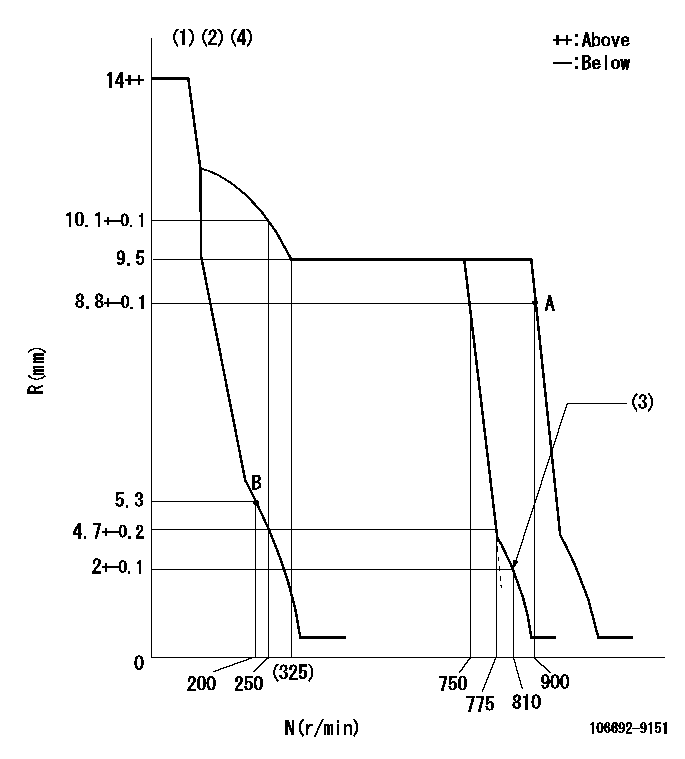
N:Pump speed
R:Rack position (mm)
(1)Target notch: K
(2)Tolerance for racks not indicated: +-0.05mm.
(3)Set idle sub-spring
(4)Confirm that the rack is pulled back to R = R1 or less at solenoid operation (N = 0).
----------
K=15 R1=4.8mm
----------
----------
K=15 R1=4.8mm
----------
Speed control lever angle
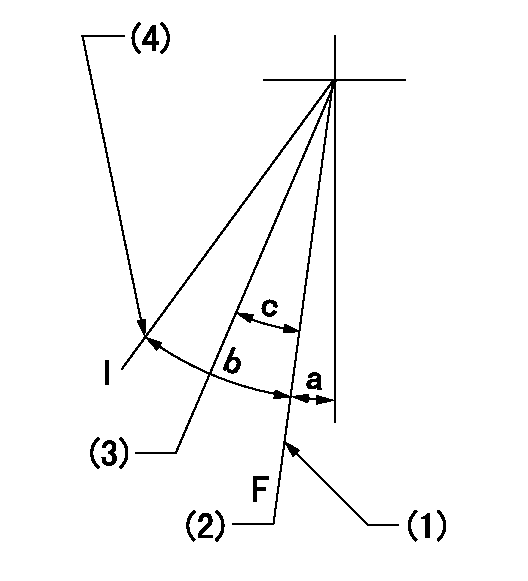
F:Full speed
I:Idle
(1)Stopper bolt setting
(2)Set the pump speed at aa
(3)Set the pump speed at bb.
(4)Stopper bolt setting
----------
aa=900r/min bb=750r/min
----------
a=13deg+-5deg b=33deg+-5deg c=8deg+-5deg
----------
aa=900r/min bb=750r/min
----------
a=13deg+-5deg b=33deg+-5deg c=8deg+-5deg
Stop lever angle

N:Pump normal
S:Stop the pump.
----------
----------
a=20deg+-5deg b=53deg+-5deg
----------
----------
a=20deg+-5deg b=53deg+-5deg
Timing setting
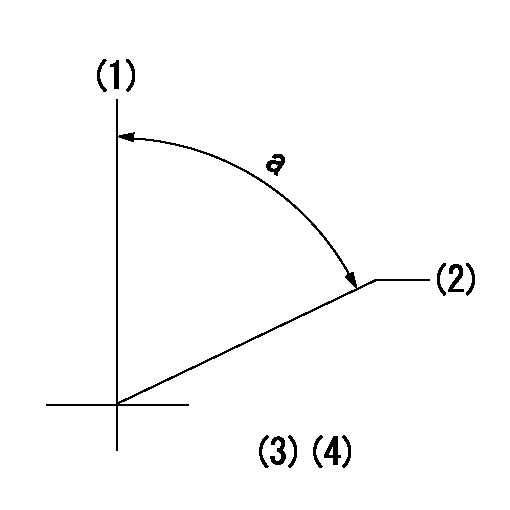
(1)Pump vertical direction
(2)Position of camshaft's key groove at No 1 cylinder's beginning of injection
(3)-
(4)-
----------
----------
a=(50deg)
----------
----------
a=(50deg)
Information:
Additional Parts Needed for Installation
Fluid Property Sensor Mounting Bracket
A mounting bracket must be fabricated to support the Fluid Property Sensor. Since the kit can be used on a large range of engines in both stationary and machine applications, no universal mounting bracket design is possible. A bracket must be field fabricated to allow mounting of the sensor to a structural component of the machine. Leave room for electrical connection and room at each end for Engine Lubricating Oil line connections.Fittings and Adapters
Due to the large range of engines that this system may be used on, a list of all Engine Lubrication Oil line fittings, sizes, styles, and adapters are not possible. As a starting point, the inlet and outlet of the sensor adapter is a 37 degree Flare for 1" oil lines. This must be adapted to the correct size oil line tubing required for each engine. It is likely that the supply and return fuel lines will be of different sizes. It is recommended that the oil line tubing be new and in good condition. The tubing MUST be clean inside. Any small particles that are carried from the inlet hose through the transducer from the system and dislodge the particles. If hoses are equipped with O-ring fittings, the O-rings must be new.Wiring Diagram
Note: During Installation, it is important to protect wiring in key locations. Key locations are any area where the wiring could be nicked or cut and come in contact with the chassis. Avoid installation practices where there could be excessive flexing, chafing, or cutting of the wiring.
Illustration 1 g06137996
Fluid Property Sensor Wiring Schematic
Installation
Machine Preparation
Move the machine to a smooth, level location, and away from other working machines and personnel.
Lower the implements to the ground.
Stop the engine.
Engage the parking brake for the machine.
Place the disconnect switch in the OFF position.
Follow all LOTO instructions for the machine.Installation of the Fluid Property Sensor
The Fluid Property Sensor must be located on a field fabricated bracket in a location of the installer's choice. When selecting a mounting location, the installer must mount the sensor in an area off the engine to reduce vibration of the sensor as well as accessibility of sensor and electrical connection. Electrical connections should avoid sharp bends at connectors, sharp edges, and chafing surfaces. Harnesses should be supported at no less than 30.48 cm (12 inch) intervals. The Fluid Property Sensor must be installed with the orifice opening in the upright position as shown in Illustration 2.
Illustration 2 g06138010
Fluid Property Sensor Installation
(A) Oil Pump
(B) Oil Filter
(C) Engine Oil Gallery
(D) Isolation Valve
(E) Oil Flow
(F) Fluid Property Sensor Orientation
(G) Oil Reservoir
(H) Oil Strainer
(I) Engine Oil SumpInstallation of the Electrical Harnesses
Note: During installation, it is important to protect wiring in key locations. Key locations are any area where the wiring could be nicked or cut and come in contact with the chassis. Avoid installation practices where there could be excessive flexing, chafing, or cutting of the wiring.
Install the 514-3811 Instl GP-Field (Fluid Property Harness) on Fluid Property Sensor.
Route harness back
Fluid Property Sensor Mounting Bracket
A mounting bracket must be fabricated to support the Fluid Property Sensor. Since the kit can be used on a large range of engines in both stationary and machine applications, no universal mounting bracket design is possible. A bracket must be field fabricated to allow mounting of the sensor to a structural component of the machine. Leave room for electrical connection and room at each end for Engine Lubricating Oil line connections.Fittings and Adapters
Due to the large range of engines that this system may be used on, a list of all Engine Lubrication Oil line fittings, sizes, styles, and adapters are not possible. As a starting point, the inlet and outlet of the sensor adapter is a 37 degree Flare for 1" oil lines. This must be adapted to the correct size oil line tubing required for each engine. It is likely that the supply and return fuel lines will be of different sizes. It is recommended that the oil line tubing be new and in good condition. The tubing MUST be clean inside. Any small particles that are carried from the inlet hose through the transducer from the system and dislodge the particles. If hoses are equipped with O-ring fittings, the O-rings must be new.Wiring Diagram
Note: During Installation, it is important to protect wiring in key locations. Key locations are any area where the wiring could be nicked or cut and come in contact with the chassis. Avoid installation practices where there could be excessive flexing, chafing, or cutting of the wiring.
Illustration 1 g06137996
Fluid Property Sensor Wiring Schematic
Installation
Machine Preparation
Move the machine to a smooth, level location, and away from other working machines and personnel.
Lower the implements to the ground.
Stop the engine.
Engage the parking brake for the machine.
Place the disconnect switch in the OFF position.
Follow all LOTO instructions for the machine.Installation of the Fluid Property Sensor
The Fluid Property Sensor must be located on a field fabricated bracket in a location of the installer's choice. When selecting a mounting location, the installer must mount the sensor in an area off the engine to reduce vibration of the sensor as well as accessibility of sensor and electrical connection. Electrical connections should avoid sharp bends at connectors, sharp edges, and chafing surfaces. Harnesses should be supported at no less than 30.48 cm (12 inch) intervals. The Fluid Property Sensor must be installed with the orifice opening in the upright position as shown in Illustration 2.
Illustration 2 g06138010
Fluid Property Sensor Installation
(A) Oil Pump
(B) Oil Filter
(C) Engine Oil Gallery
(D) Isolation Valve
(E) Oil Flow
(F) Fluid Property Sensor Orientation
(G) Oil Reservoir
(H) Oil Strainer
(I) Engine Oil SumpInstallation of the Electrical Harnesses
Note: During installation, it is important to protect wiring in key locations. Key locations are any area where the wiring could be nicked or cut and come in contact with the chassis. Avoid installation practices where there could be excessive flexing, chafing, or cutting of the wiring.
Install the 514-3811 Instl GP-Field (Fluid Property Harness) on Fluid Property Sensor.
Route harness back
Have questions with 106692-9151?
Group cross 106692-9151 ZEXEL
Komatsu
Yanmar
Yanmar
Yanmar
Yanmar
106692-9151
INJECTION-PUMP ASSEMBLY