Information injection-pump assembly
ZEXEL
106692-4860
1066924860
YANMAR
12665451012
12665451012
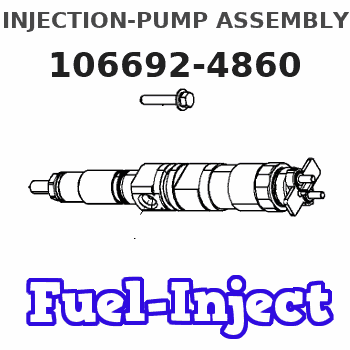
Rating:
Service parts 106692-4860 INJECTION-PUMP ASSEMBLY:
1.
_
5.
AUTOM. ADVANCE MECHANIS
6.
COUPLING PLATE
7.
COUPLING PLATE
8.
_
9.
_
11.
Nozzle and Holder
12.
Open Pre:MPa(Kqf/cm2)
22.6{230}
15.
NOZZLE SET
Include in #1:
106692-4860
as INJECTION-PUMP ASSEMBLY
Cross reference number
ZEXEL
106692-4860
1066924860
YANMAR
12665451012
12665451012
Zexel num
Bosch num
Firm num
Name
Calibration Data:
Adjustment conditions
Test oil
1404 Test oil ISO4113 or {SAEJ967d}
1404 Test oil ISO4113 or {SAEJ967d}
Test oil temperature
degC
40
40
45
Nozzle and nozzle holder
105780-8140
Bosch type code
EF8511/9A
Nozzle
105780-0000
Bosch type code
DN12SD12T
Nozzle holder
105780-2080
Bosch type code
EF8511/9
Opening pressure
MPa
17.2
Opening pressure
kgf/cm2
175
Injection pipe
Outer diameter - inner diameter - length (mm) mm 8-3-600
Outer diameter - inner diameter - length (mm) mm 8-3-600
Overflow valve
132424-0620
Overflow valve opening pressure
kPa
157
123
191
Overflow valve opening pressure
kgf/cm2
1.6
1.25
1.95
Tester oil delivery pressure
kPa
157
157
157
Tester oil delivery pressure
kgf/cm2
1.6
1.6
1.6
Direction of rotation (viewed from drive side)
Right R
Right R
Injection timing adjustment
Direction of rotation (viewed from drive side)
Right R
Right R
Injection order
1-4-2-6-
3-5
Pre-stroke
mm
2.9
2.85
2.95
Beginning of injection position
Drive side NO.1
Drive side NO.1
Difference between angles 1
Cal 1-4 deg. 60 59.5 60.5
Cal 1-4 deg. 60 59.5 60.5
Difference between angles 2
Cyl.1-2 deg. 120 119.5 120.5
Cyl.1-2 deg. 120 119.5 120.5
Difference between angles 3
Cal 1-6 deg. 180 179.5 180.5
Cal 1-6 deg. 180 179.5 180.5
Difference between angles 4
Cal 1-3 deg. 240 239.5 240.5
Cal 1-3 deg. 240 239.5 240.5
Difference between angles 5
Cal 1-5 deg. 300 299.5 300.5
Cal 1-5 deg. 300 299.5 300.5
Injection quantity adjustment
Adjusting point
A
Rack position
12
Pump speed
r/min
900
900
900
Each cylinder's injection qty
mm3/st.
197.5
193.5
201.5
Basic
*
Fixing the rack
*
Injection quantity adjustment_02
Adjusting point
B
Rack position
6.6+-0.5
Pump speed
r/min
200
200
200
Each cylinder's injection qty
mm3/st.
19.3
17.4
21.2
Fixing the rack
*
Test data Ex:
Governor adjustment
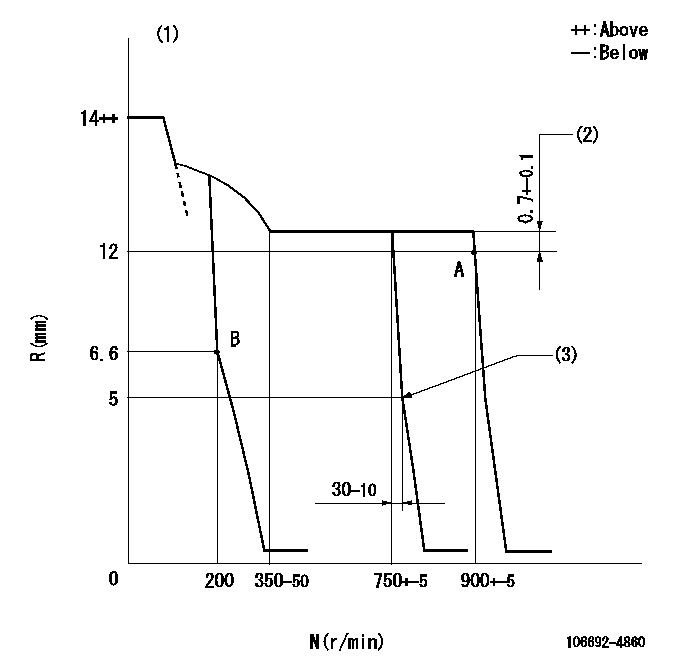
N:Pump speed
R:Rack position (mm)
(1)Target notch: K
(2)Rack difference between N = N1 and N = N2
(3)Idle sub spring setting: L1.
----------
K=11 N1=900r/min N2=750r/min L1=5-0.5mm
----------
----------
K=11 N1=900r/min N2=750r/min L1=5-0.5mm
----------
Speed control lever angle
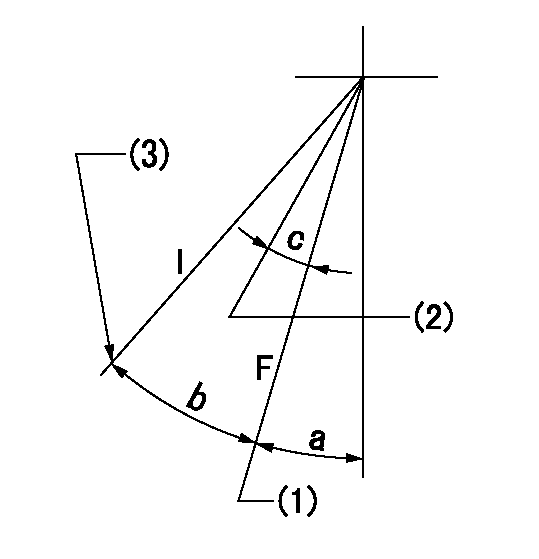
F:Full speed
I:Idle
(1)Set the pump speed at aa
(2)Set the pump speed at bb.
(3)Stopper bolt setting
----------
aa=900r/min bb=750r/min
----------
a=16deg+-5deg b=35deg+-5deg c=8deg+-5deg
----------
aa=900r/min bb=750r/min
----------
a=16deg+-5deg b=35deg+-5deg c=8deg+-5deg
Stop lever angle

N:Pump normal
S:Stop the pump.
----------
----------
a=20deg+-5deg b=53deg+-5deg
----------
----------
a=20deg+-5deg b=53deg+-5deg
Timing setting
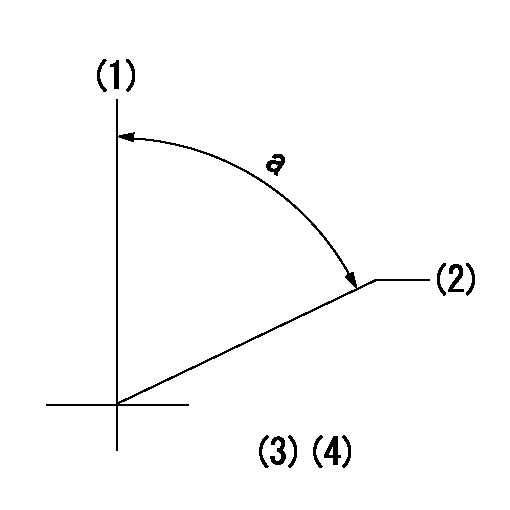
(1)Pump vertical direction
(2)Position of camshaft's key groove at No 1 cylinder's beginning of injection
(3)-
(4)-
----------
----------
a=(50deg)
----------
----------
a=(50deg)
Information:
Ensure that all components are free of contaminants before installing. Contaminants may cause premature wear and reduced component service life.
Note: Disposition and Recycling - Common components of exhaust aftertreatment devices include, but are not limited to, cordierite, silicon carbide, iron zeolite, vanadium, platinum, and palladium. After the devices are used in an engine exhaust flow they can include some by-products that result from combustion. Follow applicable Federal, State, and local regulations when handling or discarding used aftertreatment devices
Illustration 1 g03842051
Note: Prior to removal of the catalyst, identify the position of the catalysts and airflow direction. Ensure that the catalyst part number position and the air flow direction remain the same.
Remove Diesel Particulate Filter (DPF) hatch cover (1) nuts, bolts, and washers.
Remove hatch cover (1) from the reactor unit.
Remove gasket assembly from the sealing surface of the hatch cover.
Carefully remove DPF catalyst assembly by removing the V band clamps. If necessary, repeat for other PDF catalysts. Take note of DPF air flow direction and location for reassembly.
Carefully install DPF catalyst into the cabinet with new gaskets. Verify correct position and air flow direction of the DPF.
DPF should always be installed in the direction shown in illustration 1. The long end of the DPF should be installed in the sleeve of the reactor and secured with the proper V band clamps.
For verified applications, replacement DPFs must have the proper tags and meet all documentation requirements.
Apply final torque to V band clamps. Refer to Specifications, SENR3130, "Torque Specifications" for the proper torque.
Replace all inner backing strip gaskets on the DPF catalyst cover.
Install DPF cover assembly.
Replace all damaged bolts.
Apply final torque to all bolts in a circular pattern. Refer to Specifications, SENR3130, "Torque Specifications" for the proper torque.
Verify that all bolts are at the proper torque value.