Information injection-pump assembly
BOSCH
9 400 610 129
9400610129
ZEXEL
106692-4692
1066924692
KOMATSU
6151711771
6151711771
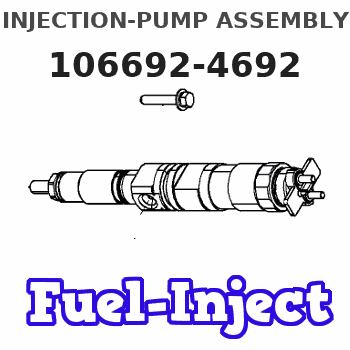
Rating:
You can express buy:
Service parts 106692-4692 INJECTION-PUMP ASSEMBLY:
1.
_
5.
AUTOM. ADVANCE MECHANIS
7.
COUPLING PLATE
8.
_
9.
_
11.
Nozzle and Holder
6151-11-3101
12.
Open Pre:MPa(Kqf/cm2)
24.5{250}
15.
NOZZLE SET
Include in #1:
106692-4692
as INJECTION-PUMP ASSEMBLY
Cross reference number
Zexel num
Bosch num
Firm num
Name
106692-4692
9 400 610 129
6151711771 KOMATSU
INJECTION-PUMP ASSEMBLY
S6D125 K 14CA INJECTION PUMP ASSY PE6P,6PD PE
S6D125 K 14CA INJECTION PUMP ASSY PE6P,6PD PE
Information:
If the procedure did not correct the issue, contact your Cat dealer Technical Communicator (TC). For further assistance, your TC can confer with the Dealer Solutions Network (DSN).E1156(1) - Filter intake pressure greater than 10 kPa (1.50 psi) for more than 10 seconds. Refer to Table13 for troubleshooting.E1156(2) - Filter intake pressure greater than 15 kPa (2.25 psi) for more than 10 seconds. Refer to Table13 for troubleshooting.A faulty sensor may cause this diagnostic code. First determine that the sensor is not faulty.
Table 13
Troubleshooting Test Steps Values Results
1. Check for Associated Diagnostic Codes.
A. Establish communication between the Cat® Electronic Technician (ET) and the engine Electronic Control Module (ECM).
B. Troubleshoot any associated diagnostic codes that are present before continuing with this procedure.
Associated Diagnostic Codes
Result: An associated diagnostic code is not present.
Proceed to Test Step 2.
Result: An associated diagnostic code is active or logged.
1. Troubleshoot the associated diagnostic code before continuing with this procedure.
2. Service Maintenance.
A. Determine the most recent cleaning of the Wall Flow Filter (WFF).
Cleaning Interval
Result: The WFF was cleaned within the last 1000 hours.
Proceed to Test Step 3.
Result: The WFF was not cleaned within the last 1000 hours.
Proceed to Test Step 4.
3. Check for Contamination.
A. Reset all active codes and clear all logged codes.
B. Remove the WFF.
C. Check for contamination on the face of the WFF.
Contamination
Result: There is no sign of oil, fuel, or coolant on the WFF.
Proceed to Test Step 4.
Result: There is oil, fuel, or coolant on the WFF.
1. Diagnose the cause of the contamination.
2. The engine must be run with no load at 1400 rpm for at least 15 minutes, or until there is no white smoke.
3. If white smoke continues, or if the diagnostic code remains active, proceed to Test Step 5.
4. Clean the WFF.
A. Clean the WFF. Refer to "Wall Flow Diesel Particulate Filter - Clean".
B. Reset all active codes and clear all logged codes.
Clean was successful
Result: Cleaning the WFF was successful.
Return the machine to service.
Result: Cleaning the WFF was not successful.
1. Troubleshoot any diagnostic codes that are present, if no codes are present, proceed to Test Step 6.
5. Replace the WFF.
Replacement was successful
Result: Replacing the WFF was successful.
Return the machine to service.
If the procedure did not correct the issue, contact your Cat dealer Technical Communicator (TC). For further assistance, your TC can confer with the Dealer Solutions Network (DSN).Exhaust Temperature Is High
Certain operating conditions may cause the exhaust temperature to increase to a level that may damage engine components.Probable Causes
Boost Leak
Engine operating conditions
High altitude
Obstructed aftercooler
Table 14
Troubleshooting Test Steps Values Results
1. Check for Boost Leakage.
A. Apply a light load to the engine and check for boost leakage.
Boost Leaks
Result: Boost leakage was found.
Repair: Repair the leaks. Return the machine to service.
Result: Boost leakage was not found.
Proceed to Test Step 2.
2. Check the Engine Operating Conditions.
A. Check the histogram to determine if the high exhaust temperature was due to normal operation.
When possible, interview the operator. Determine if the engine is being operated under heavy load. Ensure that the engine is being operated at the
Table 13
Troubleshooting Test Steps Values Results
1. Check for Associated Diagnostic Codes.
A. Establish communication between the Cat® Electronic Technician (ET) and the engine Electronic Control Module (ECM).
B. Troubleshoot any associated diagnostic codes that are present before continuing with this procedure.
Associated Diagnostic Codes
Result: An associated diagnostic code is not present.
Proceed to Test Step 2.
Result: An associated diagnostic code is active or logged.
1. Troubleshoot the associated diagnostic code before continuing with this procedure.
2. Service Maintenance.
A. Determine the most recent cleaning of the Wall Flow Filter (WFF).
Cleaning Interval
Result: The WFF was cleaned within the last 1000 hours.
Proceed to Test Step 3.
Result: The WFF was not cleaned within the last 1000 hours.
Proceed to Test Step 4.
3. Check for Contamination.
A. Reset all active codes and clear all logged codes.
B. Remove the WFF.
C. Check for contamination on the face of the WFF.
Contamination
Result: There is no sign of oil, fuel, or coolant on the WFF.
Proceed to Test Step 4.
Result: There is oil, fuel, or coolant on the WFF.
1. Diagnose the cause of the contamination.
2. The engine must be run with no load at 1400 rpm for at least 15 minutes, or until there is no white smoke.
3. If white smoke continues, or if the diagnostic code remains active, proceed to Test Step 5.
4. Clean the WFF.
A. Clean the WFF. Refer to "Wall Flow Diesel Particulate Filter - Clean".
B. Reset all active codes and clear all logged codes.
Clean was successful
Result: Cleaning the WFF was successful.
Return the machine to service.
Result: Cleaning the WFF was not successful.
1. Troubleshoot any diagnostic codes that are present, if no codes are present, proceed to Test Step 6.
5. Replace the WFF.
Replacement was successful
Result: Replacing the WFF was successful.
Return the machine to service.
If the procedure did not correct the issue, contact your Cat dealer Technical Communicator (TC). For further assistance, your TC can confer with the Dealer Solutions Network (DSN).Exhaust Temperature Is High
Certain operating conditions may cause the exhaust temperature to increase to a level that may damage engine components.Probable Causes
Boost Leak
Engine operating conditions
High altitude
Obstructed aftercooler
Table 14
Troubleshooting Test Steps Values Results
1. Check for Boost Leakage.
A. Apply a light load to the engine and check for boost leakage.
Boost Leaks
Result: Boost leakage was found.
Repair: Repair the leaks. Return the machine to service.
Result: Boost leakage was not found.
Proceed to Test Step 2.
2. Check the Engine Operating Conditions.
A. Check the histogram to determine if the high exhaust temperature was due to normal operation.
When possible, interview the operator. Determine if the engine is being operated under heavy load. Ensure that the engine is being operated at the
Have questions with 106692-4692?
Group cross 106692-4692 ZEXEL
Komatsu
Komatsu
Komatsu
Komatsu
106692-4692
9 400 610 129
6151711771
INJECTION-PUMP ASSEMBLY
S6D125
S6D125