Information injection-pump assembly
ZEXEL
106692-4120
1066924120

Rating:
Cross reference number
ZEXEL
106692-4120
1066924120
Zexel num
Bosch num
Firm num
Name
Calibration Data:
Adjustment conditions
Test oil
1404 Test oil ISO4113 or {SAEJ967d}
1404 Test oil ISO4113 or {SAEJ967d}
Test oil temperature
degC
40
40
45
Nozzle and nozzle holder
105780-8130
Bosch type code
EFEP215A
Nozzle
105780-0050
Bosch type code
DN6TD119NP1T
Nozzle holder
105780-2090
Bosch type code
EFEP215
Opening pressure
MPa
17.2
Opening pressure
kgf/cm2
175
Injection pipe
Outer diameter - inner diameter - length (mm) mm 8-3-600
Outer diameter - inner diameter - length (mm) mm 8-3-600
Tester oil delivery pressure
kPa
157
157
157
Tester oil delivery pressure
kgf/cm2
1.6
1.6
1.6
Direction of rotation (viewed from drive side)
Left L
Left L
Injection timing adjustment
Direction of rotation (viewed from drive side)
Left L
Left L
Injection order
1-5-3-6-
2-4
Pre-stroke
mm
2.4
2.35
2.45
Beginning of injection position
Drive side NO.1
Drive side NO.1
Difference between angles 1
Cal 1-5 deg. 60 59.5 60.5
Cal 1-5 deg. 60 59.5 60.5
Difference between angles 2
Cal 1-3 deg. 120 119.5 120.5
Cal 1-3 deg. 120 119.5 120.5
Difference between angles 3
Cal 1-6 deg. 180 179.5 180.5
Cal 1-6 deg. 180 179.5 180.5
Difference between angles 4
Cyl.1-2 deg. 240 239.5 240.5
Cyl.1-2 deg. 240 239.5 240.5
Difference between angles 5
Cal 1-4 deg. 300 299.5 300.5
Cal 1-4 deg. 300 299.5 300.5
Injection quantity adjustment
Adjusting point
A
Rack position
14.5
Pump speed
r/min
900
900
900
Each cylinder's injection qty
mm3/st.
472.5
467.5
477.5
Basic
*
Fixing the lever
*
Injection quantity adjustment_02
Adjusting point
B
Rack position
5.4+-0.5
Pump speed
r/min
400
400
400
Average injection quantity
mm3/st.
39.5
34.5
44.5
Max. variation between cylinders
%
0
-10
10
Fixing the rack
*
Test data Ex:
Governor adjustment
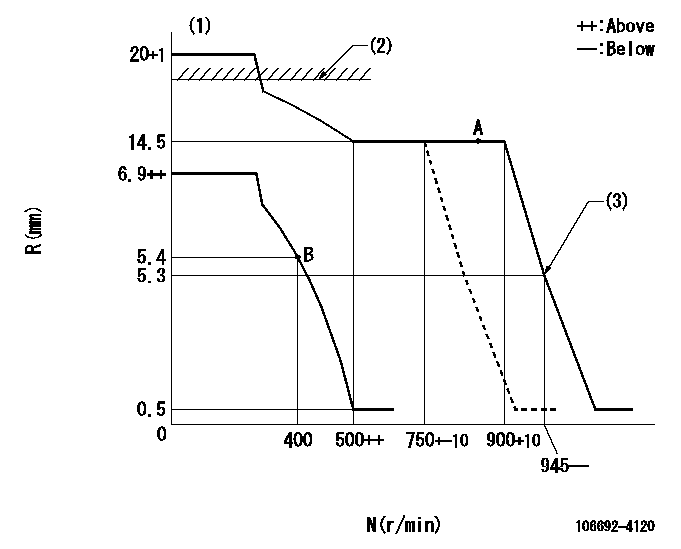
N:Pump speed
R:Rack position (mm)
(1)Notch fixed: K
(2)RACK LIMIT: RAL
(3)Idle sub spring setting: L1.
----------
K=13 RAL=16+0.2mm L1=5.3-0.5mm
----------
----------
K=13 RAL=16+0.2mm L1=5.3-0.5mm
----------
Speed control lever angle
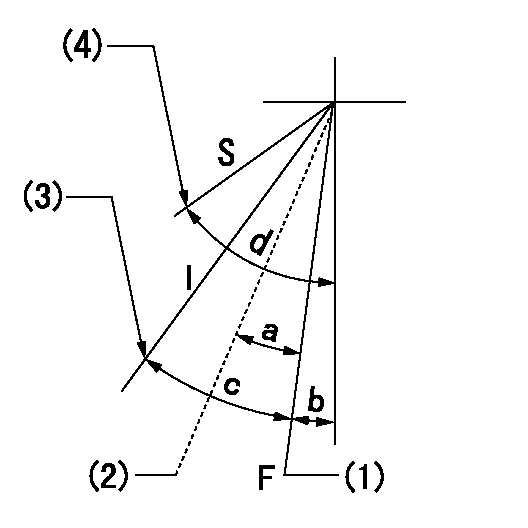
F:Full speed
I:Idle
S:Stop
(1)Set the pump speed at aa. ( At delivery )
(2)Pump speed = bb
(3)Stopper bolt setting
(4)After confirming stopping, set at idling for delivery.
----------
aa=900r/min bb=750r/min
----------
a=(9deg)+-5deg b=6deg+-5deg c=35deg+-5deg d=58deg+-3deg
----------
aa=900r/min bb=750r/min
----------
a=(9deg)+-5deg b=6deg+-5deg c=35deg+-5deg d=58deg+-3deg
Stop lever angle
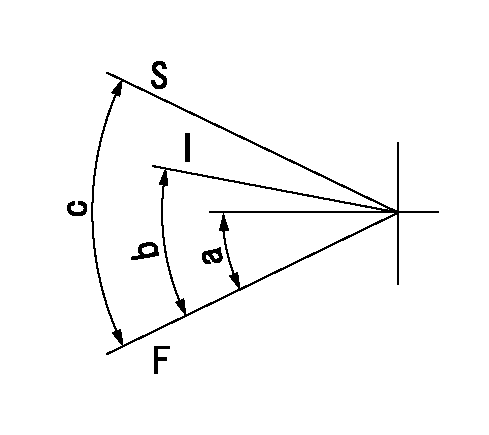
F:Full load
I:Idle
S:Stop
----------
----------
a=26.5deg+-5deg b=(35deg)+-5deg c=53deg+-5deg
----------
----------
a=26.5deg+-5deg b=(35deg)+-5deg c=53deg+-5deg
Timing setting
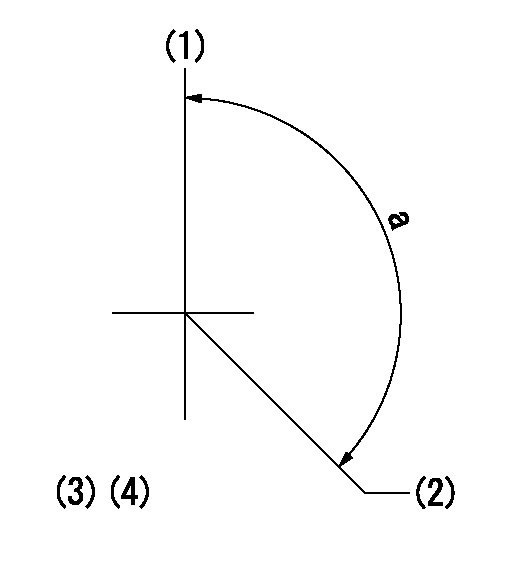
(1)Pump vertical direction
(2)Position of spline gear's aligning mark at No 1 cylinder's beginning of injection (key position)
(3)-
(4)-
----------
----------
a=(130deg)
----------
----------
a=(130deg)
Information:
Introduction
Do not perform any procedure in this Special Instruction until you read this information and you understand this information.Certain engine components may need to be cleaned if soot is found in the system beyond the Diesel Particulate Filter (DPF). The contaminated components can be cleaned with hot water and soap by hand washing or in a parts washer. Do not use solvents. Special care must be taken with handling components of the Clean Gas Induction (CGI) cooler.Safety Section
Sulfuric Acid Burn Hazard, may cause serious personal injury.The clean gas induction cooler may contain a small amount of sulfuric acid. The use of fuel with sulfur levels greater than 15 ppm may increase the amount of sulfuric acid formed. The sulfuric acid may spill from the CGI cooler during service of the engine and may travel to other downstream components. The sulfuric acid will burn the eyes, skin and clothing on contact. Always wear the appropriate personal protective equipment (PPE) that is noted on a material safety data sheet (MSDS) for sulfuric acid. Always follow the directions for first aid that are noted on a material safety data sheet (MSDS) for sulfuric acid.
Hot engine components can cause injury from burns. Before performing maintenance on the engine, allow the engine and the components to cool.
Wear goggles, gloves, protective clothing, and a National Institute for Occupational Safety and Health (NIOSH) approved P95 or N95 half-face respirator when handling a used Diesel Particulate Filter or Catalytic Converter Muffler. Failure to do so could result in personal injury.
Care must be taken to ensure that fluids are contained during performance of inspection, maintenance, testing, adjusting and repair of the product. Be prepared to collect the fluid with suitable containers before opening any compartment or disassembling any component containing fluids.Refer to Special Publication, NENG2500, "Caterpillar Dealer Service Tool Catalog" for tools and supplies suitable to collect and contain fluids on Caterpillar products.Dispose of all fluids according to local regulations and mandates.
Required Tools
Table 1
Part Number    Part Description    Qty    
9N-6379     Air Cleaner Adapter Boot     1    
4P-2706     Protection Cap     1    Cleaning Procedure
Start at the DPF outlet and inspect the components downstream of the CGI pipe until excessive soot is no longer found. If necessary, clean these components .
If soot is found at the entrance to the CGI cooler, remove the CGI cooler from the engine. Refer to Disassembly and Assembly, RENR9706, "Clean Gas Induction Cooler - Remove and Install", "Removal Procedure" in order to properly remove the CGI cooler.
After removing the CGI cooler, immediately submerge the CGI cooler into the hot soapy water.
Remove the 9N-6379 Air Cleaner Adapter Boot and the 4P-2706 Protection Cap from the ends of the CGI cooler.
Allow the water to circulate through the CGI cooler in order to dilute any sulfuric acid that may be present. Clean out the soot.
Continue to inspect the following components downstream of the CGI cooler until excessive soot is no longer found: the CGI mixing valve, the
Do not perform any procedure in this Special Instruction until you read this information and you understand this information.Certain engine components may need to be cleaned if soot is found in the system beyond the Diesel Particulate Filter (DPF). The contaminated components can be cleaned with hot water and soap by hand washing or in a parts washer. Do not use solvents. Special care must be taken with handling components of the Clean Gas Induction (CGI) cooler.Safety Section
Sulfuric Acid Burn Hazard, may cause serious personal injury.The clean gas induction cooler may contain a small amount of sulfuric acid. The use of fuel with sulfur levels greater than 15 ppm may increase the amount of sulfuric acid formed. The sulfuric acid may spill from the CGI cooler during service of the engine and may travel to other downstream components. The sulfuric acid will burn the eyes, skin and clothing on contact. Always wear the appropriate personal protective equipment (PPE) that is noted on a material safety data sheet (MSDS) for sulfuric acid. Always follow the directions for first aid that are noted on a material safety data sheet (MSDS) for sulfuric acid.
Hot engine components can cause injury from burns. Before performing maintenance on the engine, allow the engine and the components to cool.
Wear goggles, gloves, protective clothing, and a National Institute for Occupational Safety and Health (NIOSH) approved P95 or N95 half-face respirator when handling a used Diesel Particulate Filter or Catalytic Converter Muffler. Failure to do so could result in personal injury.
Care must be taken to ensure that fluids are contained during performance of inspection, maintenance, testing, adjusting and repair of the product. Be prepared to collect the fluid with suitable containers before opening any compartment or disassembling any component containing fluids.Refer to Special Publication, NENG2500, "Caterpillar Dealer Service Tool Catalog" for tools and supplies suitable to collect and contain fluids on Caterpillar products.Dispose of all fluids according to local regulations and mandates.
Required Tools
Table 1
Part Number    Part Description    Qty    
9N-6379     Air Cleaner Adapter Boot     1    
4P-2706     Protection Cap     1    Cleaning Procedure
Start at the DPF outlet and inspect the components downstream of the CGI pipe until excessive soot is no longer found. If necessary, clean these components .
If soot is found at the entrance to the CGI cooler, remove the CGI cooler from the engine. Refer to Disassembly and Assembly, RENR9706, "Clean Gas Induction Cooler - Remove and Install", "Removal Procedure" in order to properly remove the CGI cooler.
After removing the CGI cooler, immediately submerge the CGI cooler into the hot soapy water.
Remove the 9N-6379 Air Cleaner Adapter Boot and the 4P-2706 Protection Cap from the ends of the CGI cooler.
Allow the water to circulate through the CGI cooler in order to dilute any sulfuric acid that may be present. Clean out the soot.
Continue to inspect the following components downstream of the CGI cooler until excessive soot is no longer found: the CGI mixing valve, the