Information injection-pump assembly
BOSCH
9 400 617 809
9400617809
ZEXEL
106692-1210
1066921210
ISUZU
1156021030
1156021030
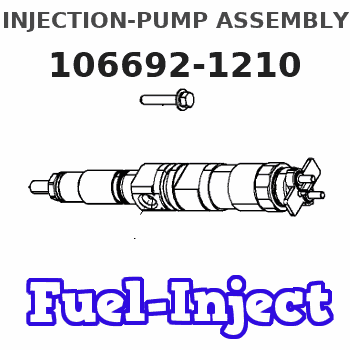
Rating:
Service parts 106692-1210 INJECTION-PUMP ASSEMBLY:
1.
_
5.
AUTOM. ADVANCE MECHANIS
8.
_
9.
_
11.
Nozzle and Holder
12.
Open Pre:MPa(Kqf/cm2)
22.1{225}
15.
NOZZLE SET
Include in #1:
106692-1210
as INJECTION-PUMP ASSEMBLY
Cross reference number
BOSCH
9 400 617 809
9400617809
ZEXEL
106692-1210
1066921210
ISUZU
1156021030
1156021030
Zexel num
Bosch num
Firm num
Name
106692-1210
9 400 617 809
1156021030 ISUZU
INJECTION-PUMP ASSEMBLY
6RB1T K 14CA INJECTION PUMP ASSY PE6P,6PD PE
6RB1T K 14CA INJECTION PUMP ASSY PE6P,6PD PE
Calibration Data:
Adjustment conditions
Test oil
1404 Test oil ISO4113 or {SAEJ967d}
1404 Test oil ISO4113 or {SAEJ967d}
Test oil temperature
degC
40
40
45
Nozzle and nozzle holder
105780-8140
Bosch type code
EF8511/9A
Nozzle
105780-0000
Bosch type code
DN12SD12T
Nozzle holder
105780-2080
Bosch type code
EF8511/9
Opening pressure
MPa
17.2
Opening pressure
kgf/cm2
175
Injection pipe
Outer diameter - inner diameter - length (mm) mm 8-3-600
Outer diameter - inner diameter - length (mm) mm 8-3-600
Overflow valve opening pressure
kPa
157
123
191
Overflow valve opening pressure
kgf/cm2
1.6
1.25
1.95
Tester oil delivery pressure
kPa
157
157
157
Tester oil delivery pressure
kgf/cm2
1.6
1.6
1.6
Direction of rotation (viewed from drive side)
Right R
Right R
Injection timing adjustment
Direction of rotation (viewed from drive side)
Right R
Right R
Injection order
1-4-2-6-
3-5
Pre-stroke
mm
3
2.95
3.05
Beginning of injection position
Drive side NO.1
Drive side NO.1
Difference between angles 1
Cal 1-4 deg. 60 59.5 60.5
Cal 1-4 deg. 60 59.5 60.5
Difference between angles 2
Cyl.1-2 deg. 120 119.5 120.5
Cyl.1-2 deg. 120 119.5 120.5
Difference between angles 3
Cal 1-6 deg. 180 179.5 180.5
Cal 1-6 deg. 180 179.5 180.5
Difference between angles 4
Cal 1-3 deg. 240 239.5 240.5
Cal 1-3 deg. 240 239.5 240.5
Difference between angles 5
Cal 1-5 deg. 300 299.5 300.5
Cal 1-5 deg. 300 299.5 300.5
Injection quantity adjustment
Adjusting point
A
Rack position
9.8
Pump speed
r/min
900
900
900
Average injection quantity
mm3/st.
174.5
172.5
176.5
Max. variation between cylinders
%
0
-3
3
Basic
*
Fixing the lever
*
Injection quantity adjustment_02
Adjusting point
B
Rack position
5.2+-0.5
Pump speed
r/min
325
325
325
Average injection quantity
mm3/st.
11.4
8.2
14.6
Max. variation between cylinders
%
0
-13
13
Fixing the rack
*
Injection quantity adjustment_03
Adjusting point
C
Rack position
-
Pump speed
r/min
150
150
150
Average injection quantity
mm3/st.
160
160
Fixing the lever
*
Rack limit
*
Test data Ex:
Governor adjustment
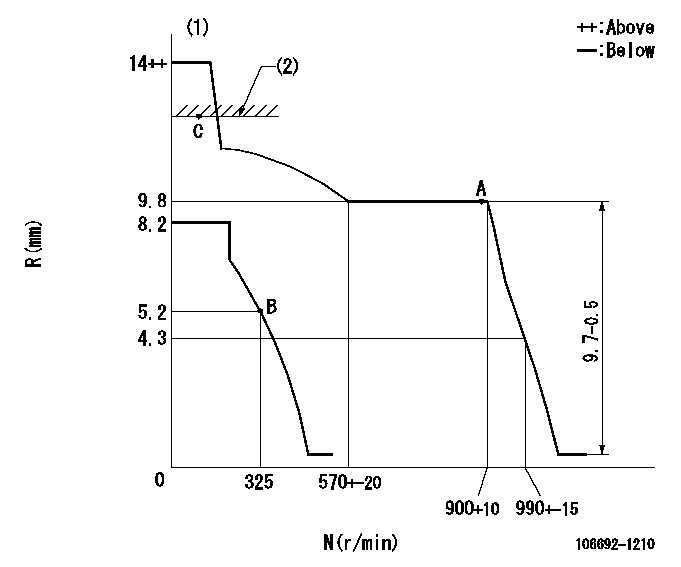
N:Pump speed
R:Rack position (mm)
(1)Target notch: K
(2)RACK LIMIT
----------
K=6
----------
----------
K=6
----------
Speed control lever angle
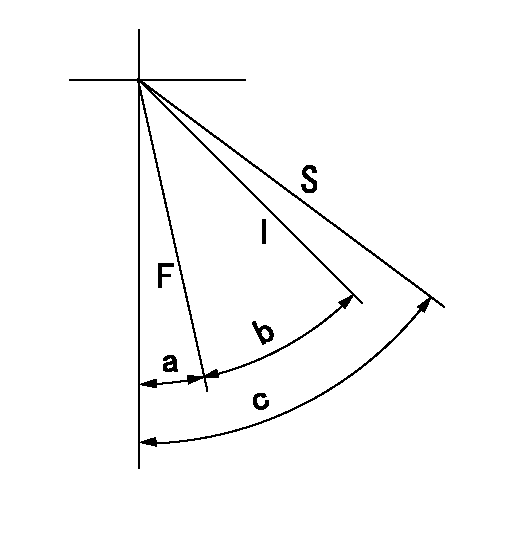
F:Full speed
I:Idle
S:Stop
----------
----------
a=0deg+-5deg b=25deg+-5deg c=32deg+-3deg
----------
----------
a=0deg+-5deg b=25deg+-5deg c=32deg+-3deg
Stop lever angle
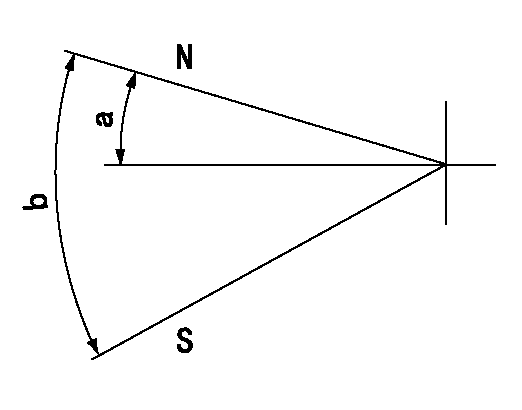
N:Pump normal
S:Stop the pump.
----------
----------
a=12deg+-5deg b=46deg+-5deg
----------
----------
a=12deg+-5deg b=46deg+-5deg
Information:
Removal Procedure for the Fuel Injection Pump
Table 1
Required Tools    
Tool     Part Number and Part Description     Qty    
A     267-2647 Stop Plug     1    
B     9S-4180 Plug     1    
Remove the air compressor. Refer to Disassembly and Assembly, "Air Compressor - Remove and Install".Note: Cleanliness is a critical factor. Before you begin the removal procedure, the exterior of the components should be thoroughly cleaned. This will help to prevent dirt from entering the internal mechanism.
Contact with high pressure fuel may cause personal injury or death. Wait 60 seconds after the engine has stopped to allow fuel pressure to purge before any service or repair is performed on the engine fuel lines.
Care must be taken to ensure that fluids are contained during performance of inspection, maintenance, testing, adjusting and repair of the product. Be prepared to collect the fluid with suitable containers before opening any compartment or disassembling any component containing fluids.Dispose of all fluids according to local regulations and mandates.
Keep all parts clean from contaminants.Contaminants may cause rapid wear and shortened component life.
Contact with high pressure fuel may cause fluid penetration and burn hazards. High pressure fuel spray may cause a fire hazard. Failure to follow these inspection, maintenance and service instructions may cause personal injury or death.
Ensure that the No. 1 cylinder is at the top center compression stroke. Refer to Testing and Adjusting, "Finding Top Center Position for No. 1 Piston".
Illustration 11 g01352511
Remove tube assembly (1), tube assembly (3), and tube assembly (4) .
Disconnect tube assembly (5) and tube assembly (6). Remove bolts (2) .
Remove Tooling (B) and install Tooling (A) .
Illustration 12 g01352571
Disconnect harness assemblies (8). Remove nuts (9) and the support assembly.
Remove bolts (10). Slide fuel injection pump (11) out of the front housing and disconnect hose assembly (7). Remove fuel injection pump (11) by pulling straight out of the front housing.Installation Procedure for the Fuel Injection Pump
Table 2
Required Tools    
Tool     Part Number and Part Description     Qty    
A     267-2647 Stop Plug     1    
B     9S-4180 Plug     1    
Keep all parts clean from contaminants.Contaminants may cause rapid wear and shortened component life.
Ensure that the No. 1 cylinder is at the top center compression stroke. Refer to Testing and Adjusting, "Finding Top Center Position for No. 1 Piston".
Illustration 13 g01352571
Note: Ensure that Tooling (A) is installed prior to installation of the fuel injection pump.
Align fuel injection pump (11) in the correct orientation relative to the front housing. Connect hose assembly (7) .
Install fuel injection pump (11). Move fuel injection pump (11) straight into the front housing in order to properly engage the gear. Install bolts (10) .
Install the support assembly and nuts (9). Connect harness assemblies (8) .
Illustration 14 g01352511
Remove Tooling (A) and install Tooling (B). Tighten Tooling (B) to a torque of 4.5 0.5 N m (40.0 4.0 lb in).
Install bolts (2). Connect tube assembly (6) and tube assembly (5)
Table 1
Required Tools    
Tool     Part Number and Part Description     Qty    
A     267-2647 Stop Plug     1    
B     9S-4180 Plug     1    
Remove the air compressor. Refer to Disassembly and Assembly, "Air Compressor - Remove and Install".Note: Cleanliness is a critical factor. Before you begin the removal procedure, the exterior of the components should be thoroughly cleaned. This will help to prevent dirt from entering the internal mechanism.
Contact with high pressure fuel may cause personal injury or death. Wait 60 seconds after the engine has stopped to allow fuel pressure to purge before any service or repair is performed on the engine fuel lines.
Care must be taken to ensure that fluids are contained during performance of inspection, maintenance, testing, adjusting and repair of the product. Be prepared to collect the fluid with suitable containers before opening any compartment or disassembling any component containing fluids.Dispose of all fluids according to local regulations and mandates.
Keep all parts clean from contaminants.Contaminants may cause rapid wear and shortened component life.
Contact with high pressure fuel may cause fluid penetration and burn hazards. High pressure fuel spray may cause a fire hazard. Failure to follow these inspection, maintenance and service instructions may cause personal injury or death.
Ensure that the No. 1 cylinder is at the top center compression stroke. Refer to Testing and Adjusting, "Finding Top Center Position for No. 1 Piston".
Illustration 11 g01352511
Remove tube assembly (1), tube assembly (3), and tube assembly (4) .
Disconnect tube assembly (5) and tube assembly (6). Remove bolts (2) .
Remove Tooling (B) and install Tooling (A) .
Illustration 12 g01352571
Disconnect harness assemblies (8). Remove nuts (9) and the support assembly.
Remove bolts (10). Slide fuel injection pump (11) out of the front housing and disconnect hose assembly (7). Remove fuel injection pump (11) by pulling straight out of the front housing.Installation Procedure for the Fuel Injection Pump
Table 2
Required Tools    
Tool     Part Number and Part Description     Qty    
A     267-2647 Stop Plug     1    
B     9S-4180 Plug     1    
Keep all parts clean from contaminants.Contaminants may cause rapid wear and shortened component life.
Ensure that the No. 1 cylinder is at the top center compression stroke. Refer to Testing and Adjusting, "Finding Top Center Position for No. 1 Piston".
Illustration 13 g01352571
Note: Ensure that Tooling (A) is installed prior to installation of the fuel injection pump.
Align fuel injection pump (11) in the correct orientation relative to the front housing. Connect hose assembly (7) .
Install fuel injection pump (11). Move fuel injection pump (11) straight into the front housing in order to properly engage the gear. Install bolts (10) .
Install the support assembly and nuts (9). Connect harness assemblies (8) .
Illustration 14 g01352511
Remove Tooling (A) and install Tooling (B). Tighten Tooling (B) to a torque of 4.5 0.5 N m (40.0 4.0 lb in).
Install bolts (2). Connect tube assembly (6) and tube assembly (5)
Have questions with 106692-1210?
Group cross 106692-1210 ZEXEL
Isuzu
106692-1210
9 400 617 809
1156021030
INJECTION-PUMP ASSEMBLY
6RB1T
6RB1T