Information injection-pump assembly
BOSCH
9 400 613 396
9400613396
ZEXEL
106691-4120
1066914120
KOMATSU
6156711220
6156711220
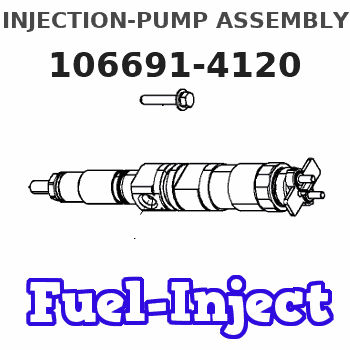
Rating:
Service parts 106691-4120 INJECTION-PUMP ASSEMBLY:
1.
_
7.
COUPLING PLATE
8.
_
9.
_
11.
Nozzle and Holder
12.
Open Pre:MPa(Kqf/cm2)
24.5{250}
15.
NOZZLE SET
Include in #1:
106691-4120
as INJECTION-PUMP ASSEMBLY
Cross reference number
BOSCH
9 400 613 396
9400613396
ZEXEL
106691-4120
1066914120
KOMATSU
6156711220
6156711220
Zexel num
Bosch num
Firm num
Name
106691-4120
9 400 613 396
6156711220 KOMATSU
INJECTION-PUMP ASSEMBLY
SAA6D125 K 14CA INJECTION PUMP ASSY PE6P,6PD PE
SAA6D125 K 14CA INJECTION PUMP ASSY PE6P,6PD PE
Calibration Data:
Adjustment conditions
Test oil
1404 Test oil ISO4113 or {SAEJ967d}
1404 Test oil ISO4113 or {SAEJ967d}
Test oil temperature
degC
40
40
45
Nozzle and nozzle holder
105780-8140
Bosch type code
EF8511/9A
Nozzle
105780-0000
Bosch type code
DN12SD12T
Nozzle holder
105780-2080
Bosch type code
EF8511/9
Opening pressure
MPa
17.2
Opening pressure
kgf/cm2
175
Injection pipe
Outer diameter - inner diameter - length (mm) mm 8-3-600
Outer diameter - inner diameter - length (mm) mm 8-3-600
Overflow valve
134424-4120
Overflow valve opening pressure
kPa
255
221
289
Overflow valve opening pressure
kgf/cm2
2.6
2.25
2.95
Tester oil delivery pressure
kPa
255
255
255
Tester oil delivery pressure
kgf/cm2
2.6
2.6
2.6
Direction of rotation (viewed from drive side)
Left L
Left L
Injection timing adjustment
Direction of rotation (viewed from drive side)
Left L
Left L
Injection order
1-5-3-6-
2-4
Pre-stroke
mm
3.75
3.7
3.8
Rack position
Point A or more. R=A++
Point A or more. R=A++
Beginning of injection position
Drive side NO.1
Drive side NO.1
Difference between angles 1
Cal 1-5 deg. 60 59.5 60.5
Cal 1-5 deg. 60 59.5 60.5
Difference between angles 2
Cal 1-3 deg. 120 119.5 120.5
Cal 1-3 deg. 120 119.5 120.5
Difference between angles 3
Cal 1-6 deg. 180 179.5 180.5
Cal 1-6 deg. 180 179.5 180.5
Difference between angles 4
Cyl.1-2 deg. 240 239.5 240.5
Cyl.1-2 deg. 240 239.5 240.5
Difference between angles 5
Cal 1-4 deg. 300 299.5 300.5
Cal 1-4 deg. 300 299.5 300.5
Injection quantity adjustment
Adjusting point
A
Rack position
12.2
Pump speed
r/min
1000
1000
1000
Average injection quantity
mm3/st.
132
130
134
Max. variation between cylinders
%
0
-3
3
Basic
*
Fixing the lever
*
Boost pressure
kPa
34.7
34.7
Boost pressure
mmHg
260
260
Injection quantity adjustment_02
Adjusting point
-
Rack position
8.2+-0.5
Pump speed
r/min
400
400
400
Average injection quantity
mm3/st.
21
19.5
22.5
Max. variation between cylinders
%
0
-15
15
Fixing the rack
*
Boost pressure
kPa
0
0
0
Boost pressure
mmHg
0
0
0
Remarks
Adjust only variation between cylinders; adjust governor according to governor specifications.
Adjust only variation between cylinders; adjust governor according to governor specifications.
Injection quantity adjustment_03
Adjusting point
E
Rack position
12.4++
Pump speed
r/min
100
100
100
Average injection quantity
mm3/st.
155
145
165
Fixing the lever
*
Boost pressure
kPa
0
0
0
Boost pressure
mmHg
0
0
0
Rack limit
*
Boost compensator adjustment
Pump speed
r/min
500
500
500
Rack position
10.8
Boost pressure
kPa
6.7
5.4
8
Boost pressure
mmHg
50
40
60
Boost compensator adjustment_02
Pump speed
r/min
500
500
500
Rack position
11.7
Boost pressure
kPa
21.3
21.3
21.3
Boost pressure
mmHg
160
160
160
Timer adjustment
Pump speed
r/min
780--
Advance angle
deg.
0
0
0
Remarks
Start
Start
Timer adjustment_02
Pump speed
r/min
730
Advance angle
deg.
0.5
Timer adjustment_03
Pump speed
r/min
950
Advance angle
deg.
2
1.7
2.3
Remarks
Finish
Finish
Test data Ex:
Governor adjustment
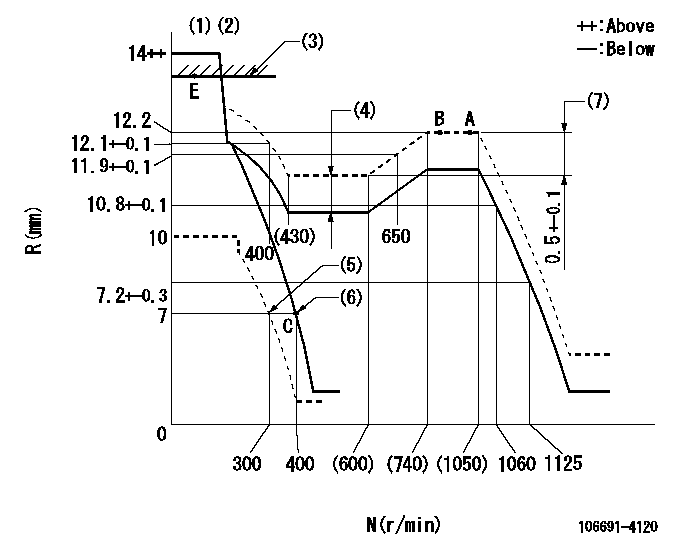
N:Pump speed
R:Rack position (mm)
(1)Target notch: K
(2)Tolerance for racks not indicated: +-0.05mm.
(3)RACK LIMIT
(4)Boost compensator stroke: BCL
(5)Set idle sub-spring
(6)Main spring setting
(7)Rack difference between N = N1 and N = N2
----------
K=16 BCL=0.9+-0.1mm N1=1000r/min N2=500r/min
----------
----------
K=16 BCL=0.9+-0.1mm N1=1000r/min N2=500r/min
----------
Speed control lever angle
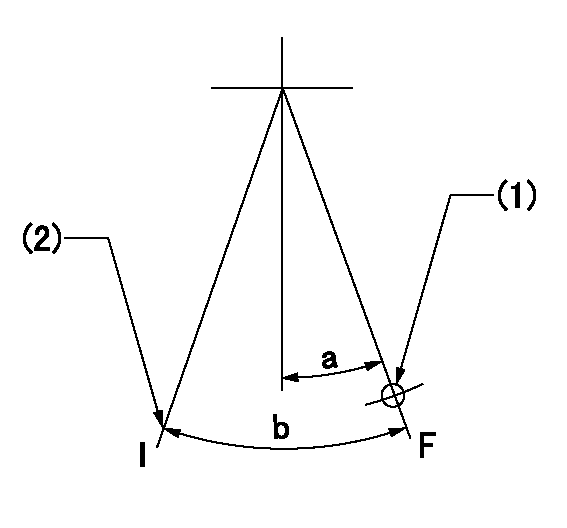
F:Full speed
I:Idle
(1)Use the hole at R = aa
(2)Stopper bolt setting
----------
aa=69mm
----------
a=19deg+-5deg b=28deg+-5deg
----------
aa=69mm
----------
a=19deg+-5deg b=28deg+-5deg
Stop lever angle

N:Pump normal
S:Stop the pump.
(1)Rack position = aa, speed = bb.
(2)Normal
----------
aa=1-0.5mm bb=0r/min
----------
a=33deg+-5deg b=70deg+-5deg
----------
aa=1-0.5mm bb=0r/min
----------
a=33deg+-5deg b=70deg+-5deg
0000001501 TAMPER PROOF

Tamperproofing-equipped boost compensator cover installation procedure
(A) After adjusting the boost compensator, tighten the bolts to remove the heads.
(1)Before adjusting the governor and the boost compensator, tighten the screw to the specified torque.
(Tightening torque T = T1 maximum)
(2)After adjusting the governor and the boost compensator, tighten to the specified torque to break off the bolt heads.
(Tightening torque T = T2)
----------
T1=2.5N-m(0.25kgf-m) T2=2.9~4.4N-m(0.3~0.45kgf-m)
----------
----------
T1=2.5N-m(0.25kgf-m) T2=2.9~4.4N-m(0.3~0.45kgf-m)
----------
Timing setting
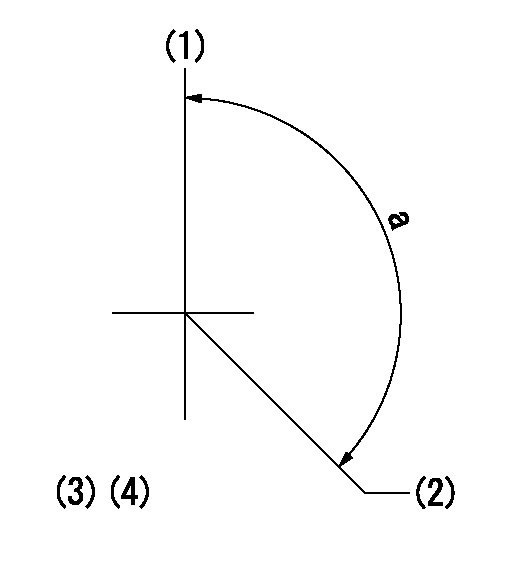
(1)Pump vertical direction
(2)Coupling's key groove position at No 1 cylinder's beginning of injection
(3)B.T.D.C.: aa
(4)-
----------
aa=7.5deg
----------
a=(140deg)
----------
aa=7.5deg
----------
a=(140deg)
Information:
Illustration 1 g00669441
CCM to Host Equipment Direct Connection (1) CCM (2) CCM RS-232C port (3) Computer RS-232C port (4) Host equipmentMake sure that the following equipment is available:
A personal computer. Refer to "Caterpillar CCM PC For Windows: Getting Started Manual" for specifications on the PC.
The proper RS-232C cables are required for the particular installation. Refer to the Operation and Maintenance Manual, "RS-232C Cable Requirements".
The CCM PC Software for Windows. This software is available from Caterpillar.ProcedurePerform the following procedure to initialize communication with the host equipment that is connected directly to the CCM.Note: The host equipment and the CCM should be turned OFF before you change the cables to the serial ports.
The CCM should be installed with all of the wiring. Refer to Operations and Maintenance Manual, "General Wiring Diagram" and "RS-232C Cable Requirements".
Determine the parameters for communication for the installation. The default rate of communication (bits per second or bps) is 9600. The remaining default settings from the factory are no parity, 8 data bits, and 1 stop bit. These parameters will work well in most installations. Use the Operations and Maintenance Manual, "Communication Parameters - Identify" to determine the parameters of communication that are stored in the CCM.
Load the CCM PC For Windows software into the PC. Refer to the "Caterpillar CCM PC For Windows: Getting Started Manual". Start the CCM PC program and connect to the CCM.
Go to the Data Link pull-down menu. Select ECM, CCM. Go to the CCM configuration screen in the Utilities menu. Set the parameters for communication to match the values that were chosen in step 2.
Use the CCM configuration screen to set the Connection Type to Direct Connection. The CCM is now set at the determined communication configuration.Note: If the PC is required to communicate with the CCM, go to the Phone Book pull-down menu and select Add or Edit. Set the communication parameters of the PC to the values that were chosen in Step 2.Note: The electronic controller of each engine must be programmed with the correct engine number for identification on the CCM. The electronic controller is programmed to Engine Number 1 at the factory. Refer to Operation and Maintenance Manual, SEBU6874, "Engine Number - Program".Note: After the CCM has been connected to the PC, refer to the "CCM PC Software Users Manual". This manual contains instructions on monitoring and on controlling the engine remotely.Note: Two conditions must be met before the electronic engine controller will allow control by the CCM. The Engine Control Switch must be in the AUTO position, and the remote initiate contacts must be open. The engine may be monitored with the ECS in any position.Note: For an EMCP II application, the CCM cannot control the generator set if the GSC is in Service Mode. The generator set can only be monitored.
Have questions with 106691-4120?
Group cross 106691-4120 ZEXEL
Yanmar
Komatsu
106691-4120
9 400 613 396
6156711220
INJECTION-PUMP ASSEMBLY
SAA6D125
SAA6D125