Information injection-pump assembly
BOSCH
9 400 610 995
9400610995
ZEXEL
106691-0590
1066910590
NISSAN-DIESEL
1679096577
1679096577
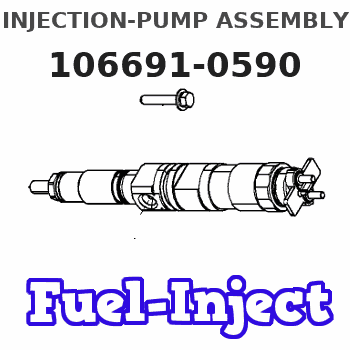
Rating:
Service parts 106691-0590 INJECTION-PUMP ASSEMBLY:
1.
_
7.
COUPLING PLATE
8.
_
9.
_
11.
Nozzle and Holder
16600-96511
12.
Open Pre:MPa(Kqf/cm2)
22.6{230}
15.
NOZZLE SET
Include in #1:
106691-0590
as INJECTION-PUMP ASSEMBLY
Cross reference number
BOSCH
9 400 610 995
9400610995
ZEXEL
106691-0590
1066910590
NISSAN-DIESEL
1679096577
1679096577
Zexel num
Bosch num
Firm num
Name
106691-0590
9 400 610 995
1679096577 NISSAN-DIESEL
INJECTION-PUMP ASSEMBLY
PE6T * K 14CA INJECTION PUMP ASSY PE6P,6PD PE
PE6T * K 14CA INJECTION PUMP ASSY PE6P,6PD PE
Calibration Data:
Adjustment conditions
Test oil
1404 Test oil ISO4113 or {SAEJ967d}
1404 Test oil ISO4113 or {SAEJ967d}
Test oil temperature
degC
40
40
45
Nozzle and nozzle holder
105780-8140
Bosch type code
EF8511/9A
Nozzle
105780-0000
Bosch type code
DN12SD12T
Nozzle holder
105780-2080
Bosch type code
EF8511/9
Opening pressure
MPa
17.2
Opening pressure
kgf/cm2
175
Injection pipe
Outer diameter - inner diameter - length (mm) mm 8-3-600
Outer diameter - inner diameter - length (mm) mm 8-3-600
Overflow valve
132424-0620
Overflow valve opening pressure
kPa
157
123
191
Overflow valve opening pressure
kgf/cm2
1.6
1.25
1.95
Tester oil delivery pressure
kPa
157
157
157
Tester oil delivery pressure
kgf/cm2
1.6
1.6
1.6
Direction of rotation (viewed from drive side)
Right R
Right R
Injection timing adjustment
Direction of rotation (viewed from drive side)
Right R
Right R
Injection order
1-4-2-6-
3-5
Pre-stroke
mm
3.65
3.6
3.7
Beginning of injection position
Drive side NO.1
Drive side NO.1
Difference between angles 1
Cal 1-4 deg. 60 59.5 60.5
Cal 1-4 deg. 60 59.5 60.5
Difference between angles 2
Cyl.1-2 deg. 120 119.5 120.5
Cyl.1-2 deg. 120 119.5 120.5
Difference between angles 3
Cal 1-6 deg. 180 179.5 180.5
Cal 1-6 deg. 180 179.5 180.5
Difference between angles 4
Cal 1-3 deg. 240 239.5 240.5
Cal 1-3 deg. 240 239.5 240.5
Difference between angles 5
Cal 1-5 deg. 300 299.5 300.5
Cal 1-5 deg. 300 299.5 300.5
Injection quantity adjustment
Adjusting point
A
Rack position
10
Pump speed
r/min
650
650
650
Average injection quantity
mm3/st.
146.1
144.1
148.1
Max. variation between cylinders
%
0
-4
4
Basic
*
Fixing the lever
*
Boost pressure
kPa
23.3
23.3
Boost pressure
mmHg
175
175
Injection quantity adjustment_02
Adjusting point
B
Rack position
10
Pump speed
r/min
1050
1050
1050
Average injection quantity
mm3/st.
147.9
141.9
153.9
Fixing the lever
*
Boost pressure
kPa
23.3
23.3
Boost pressure
mmHg
175
175
Injection quantity adjustment_03
Adjusting point
C
Rack position
9.8
Pump speed
r/min
300
300
300
Average injection quantity
mm3/st.
134.1
131.1
137.1
Max. variation between cylinders
%
0
-4
4
Fixing the lever
*
Boost pressure
kPa
0
0
0
Boost pressure
mmHg
0
0
0
Injection quantity adjustment_04
Adjusting point
D
Rack position
6+-0.5
Pump speed
r/min
360
360
360
Average injection quantity
mm3/st.
25.8
24.8
26.8
Max. variation between cylinders
%
0
-10
10
Fixing the rack
*
Boost pressure
kPa
0
0
0
Boost pressure
mmHg
0
0
0
Boost compensator adjustment
Pump speed
r/min
300
300
300
Rack position
9.8
Boost pressure
kPa
6.7
4
9.4
Boost pressure
mmHg
50
30
70
Boost compensator adjustment_02
Pump speed
r/min
300
300
300
Rack position
10
Boost pressure
kPa
8
8
8
Boost pressure
mmHg
60
60
60
Boost compensator adjustment_03
Pump speed
r/min
300
300
300
Rack position
10.7+-0.
1
Boost pressure
kPa
12.7
12.7
12.7
Boost pressure
mmHg
95
95
95
Boost compensator adjustment_04
Pump speed
r/min
300
300
300
Rack position
(11.4)
Boost pressure
kPa
18
18
18
Boost pressure
mmHg
135
135
135
Timer adjustment
Pump speed
r/min
900+80
Advance angle
deg.
0
0
0
Remarks
Start
Start
Timer adjustment_02
Pump speed
r/min
1080
Advance angle
deg.
1
0.5
1.5
Remarks
Finish
Finish
Test data Ex:
Governor adjustment
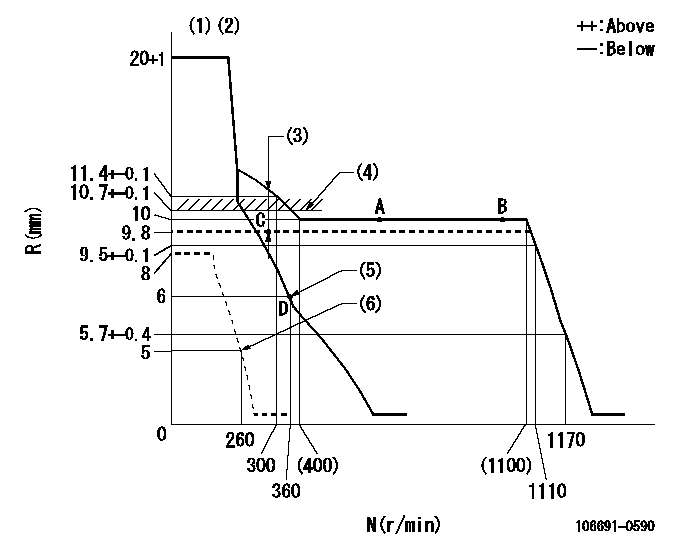
N:Pump speed
R:Rack position (mm)
(1)Target notch: K
(2)Tolerance for racks not indicated: +-0.05mm.
(3)Boost compensator stroke: BCL
(4)Excessive fuel lever setting (boost pressure 0)
(5)Main spring setting
(6)Set idle sub-spring
----------
K=12 BCL=(1.6)mm
----------
----------
K=12 BCL=(1.6)mm
----------
Speed control lever angle
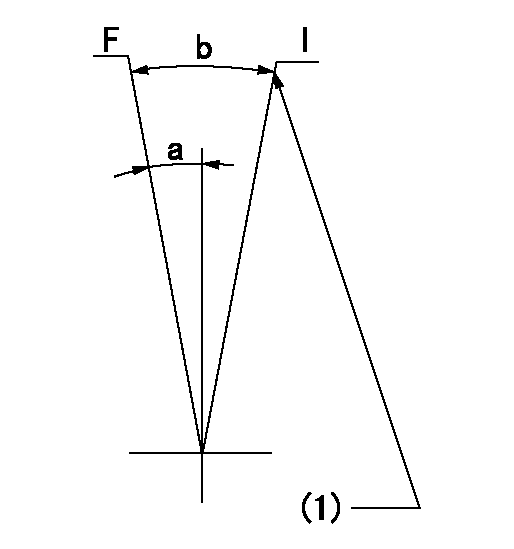
F:Full speed
I:Idle
(1)Stopper bolt setting
----------
----------
a=3deg+-5deg b=17deg+-5deg
----------
----------
a=3deg+-5deg b=17deg+-5deg
Stop lever angle

N:Pump normal
S:Stop the pump.
----------
----------
a=26deg+-5deg b=53deg+-5deg
----------
----------
a=26deg+-5deg b=53deg+-5deg
0000001101

N:Normal
B:When boosted
(1)Rack position = aa (at boost pressure bb)
----------
aa=10.7+-0.1mm bb=0
----------
a=(8deg) b=(18deg)
----------
aa=10.7+-0.1mm bb=0
----------
a=(8deg) b=(18deg)
0000001501 GOV FULL LOAD ADJUSTMENT

Title1:Full load stopper adjustment
Title2:Governor set speed
LABEL1:Distinguishing
LABEL2:Pump speed (r/min)
LABEL3:Ave. injection quantity (mm3/st)
LABEL4:Max. var. bet. cyl.
LABEL5:Remarks
LABEL6:Distinguishing
LABEL7:Governor set speed (r/min)
LABEL8:Maximum no-load speed (r/min)
LABEL9:Remarks
(1)Adjustment conditions are the same as those for measuring injection quantity.
(2)At high idle rack position L
----------
L=5.7mm
----------
a1=B a2=- a3=- a4=- r1=650r/min r2=- r3=- r4=- Q1=146.1+-2mm3/st Q2=- Q3=- Q4=- c1=+-4% c2=- c3=- c4=- a5=22 a6=21 a7=- a8=- a9=- a10=- a11=- a12=- a13=- a14=- a15=- r5=1100r/min r6=1050r/min r7=- r8=- r9=- r10=- r11=- r12=- r13=- r14=- r15=- R5=1170+-27r/min R6=1120+-26r/min R7=- R8=- R9=- R10=- R11=- R12=- R13=- R14=- R15=-
----------
L=5.7mm
----------
a1=B a2=- a3=- a4=- r1=650r/min r2=- r3=- r4=- Q1=146.1+-2mm3/st Q2=- Q3=- Q4=- c1=+-4% c2=- c3=- c4=- a5=22 a6=21 a7=- a8=- a9=- a10=- a11=- a12=- a13=- a14=- a15=- r5=1100r/min r6=1050r/min r7=- r8=- r9=- r10=- r11=- r12=- r13=- r14=- r15=- R5=1170+-27r/min R6=1120+-26r/min R7=- R8=- R9=- R10=- R11=- R12=- R13=- R14=- R15=-
Timing setting

(1)Pump vertical direction
(2)Coupling's key groove position at No 1 cylinder's beginning of injection
(3)-
(4)-
----------
----------
a=(20deg)
----------
----------
a=(20deg)
Information:
Introduction
This Special Instruction contains the necessary procedure in order to install unit injectors for 3114, 3116, and 3126 MUI engines.Removal and Installation Procedure
Note: To avoid damage to the unit injector during removal of the unit injector from the cylinder head, refer to the Service Manual for the removal procedure of the unit injector.Use the latest process for servicing the unit injector sleeves in the cylinder head before you install replacement unit injectors. Refer to the Service Manual and other service news articles in order to find the latest service information, including new tools and procedures.Before a new unit injector or a remanufactured unit injector is installed into an engine, take adequate precautions in order to clean the internal fuel lines and the unit injector sleeve. Also, install a new Caterpillar high efficiency fuel filter.Lubricate the injector rack bar with clean diesel fuel or 1U-8265 Penetrating Oil .
Illustration 1 g02144296
Incorrect testing procedure for the tappet springDo not depress the tappet spring. Refer to Illustration 1. Do not force the injector rack bar in and out since this action may damage the internal parts of the unit injector. A tight rack on a unit injector that is not installed in the engine is not an indication of a faulty unit injector. Forcing the injector rack bar in and out may cause the unit injector to become damaged. Forcing the injector rack bar in and out may possibly void all the warranty.Do not test the unit injectors prior to engine installation. The unit injectors are tested 100% at the factory and Pop Testing may contaminate the unit injector.Before you install the unit injector, apply clean engine oil on the O-ring seals for ease of installation.Install the unit injector according to the procedure in the Service Manual by using 173-1530 Injector Seating Tool . Tighten the unit injector clamp retaining bolt to a torque of 12 3 N m (9 2 lb ft).Verify the following parameters and settings according to the procedures in the Service Manual: unit injector synchronization, fuel setting, fuel timing and valve lash. Adjust the parameters and settings in order to meet specifications only.
This Special Instruction contains the necessary procedure in order to install unit injectors for 3114, 3116, and 3126 MUI engines.Removal and Installation Procedure
Note: To avoid damage to the unit injector during removal of the unit injector from the cylinder head, refer to the Service Manual for the removal procedure of the unit injector.Use the latest process for servicing the unit injector sleeves in the cylinder head before you install replacement unit injectors. Refer to the Service Manual and other service news articles in order to find the latest service information, including new tools and procedures.Before a new unit injector or a remanufactured unit injector is installed into an engine, take adequate precautions in order to clean the internal fuel lines and the unit injector sleeve. Also, install a new Caterpillar high efficiency fuel filter.Lubricate the injector rack bar with clean diesel fuel or 1U-8265 Penetrating Oil .
Illustration 1 g02144296
Incorrect testing procedure for the tappet springDo not depress the tappet spring. Refer to Illustration 1. Do not force the injector rack bar in and out since this action may damage the internal parts of the unit injector. A tight rack on a unit injector that is not installed in the engine is not an indication of a faulty unit injector. Forcing the injector rack bar in and out may cause the unit injector to become damaged. Forcing the injector rack bar in and out may possibly void all the warranty.Do not test the unit injectors prior to engine installation. The unit injectors are tested 100% at the factory and Pop Testing may contaminate the unit injector.Before you install the unit injector, apply clean engine oil on the O-ring seals for ease of installation.Install the unit injector according to the procedure in the Service Manual by using 173-1530 Injector Seating Tool . Tighten the unit injector clamp retaining bolt to a torque of 12 3 N m (9 2 lb ft).Verify the following parameters and settings according to the procedures in the Service Manual: unit injector synchronization, fuel setting, fuel timing and valve lash. Adjust the parameters and settings in order to meet specifications only.
Have questions with 106691-0590?
Group cross 106691-0590 ZEXEL
Nissan-Diesel
Nissan-Diesel
Nissan-Diesel
Nissan-Diesel
106691-0590
9 400 610 995
1679096577
INJECTION-PUMP ASSEMBLY
PE6T
PE6T