Information injection-pump assembly
BOSCH
F 019 Z20 223
f019z20223
ZEXEL
106685-4530
1066854530
MITSUBISHI-HEAV
34A6500110
34a6500110
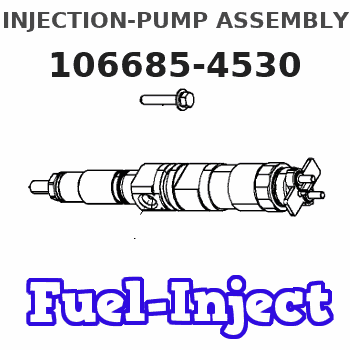
Rating:
Service parts 106685-4530 INJECTION-PUMP ASSEMBLY:
1.
_
5.
AUTOM. ADVANCE MECHANIS
8.
_
9.
_
11.
Nozzle and Holder
12.
Open Pre:MPa(Kqf/cm2)
29.4(300)
15.
NOZZLE SET
Include in #1:
106685-4530
as INJECTION-PUMP ASSEMBLY
Cross reference number
BOSCH
F 019 Z20 223
f019z20223
ZEXEL
106685-4530
1066854530
MITSUBISHI-HEAV
34A6500110
34a6500110
Zexel num
Bosch num
Firm num
Name
F 019 Z20 223
34A6500110 MITSUBISHI-HEAV
INJECTION-PUMP ASSEMBLY
S6B3 * K 14CA INJECTION PUMP ASSY PE6P,6PD PE
S6B3 * K 14CA INJECTION PUMP ASSY PE6P,6PD PE
Calibration Data:
Adjustment conditions
Test oil
1404 Test oil ISO4113 or {SAEJ967d}
1404 Test oil ISO4113 or {SAEJ967d}
Test oil temperature
degC
40
40
45
Nozzle and nozzle holder
105780-8130
Bosch type code
EFEP215A
Nozzle
105780-0050
Bosch type code
DN6TD119NP1T
Nozzle holder
105780-2090
Bosch type code
EFEP215
Opening pressure
MPa
17.2
Opening pressure
kgf/cm2
175
Injection pipe
Outer diameter - inner diameter - length (mm) mm 8-4-1000
Outer diameter - inner diameter - length (mm) mm 8-4-1000
Overflow valve
131425-1720
Overflow valve opening pressure
kPa
255
221
289
Overflow valve opening pressure
kgf/cm2
2.6
2.25
2.95
Tester oil delivery pressure
kPa
255
255
255
Tester oil delivery pressure
kgf/cm2
2.6
2.6
2.6
Direction of rotation (viewed from drive side)
Left L
Left L
Injection timing adjustment
Direction of rotation (viewed from drive side)
Left L
Left L
Injection order
1-5-3-6-
2-4
Pre-stroke
mm
3.5
3.45
3.55
Beginning of injection position
Governor side NO.1
Governor side NO.1
Difference between angles 1
Cal 1-5 deg. 60 59.5 60.5
Cal 1-5 deg. 60 59.5 60.5
Difference between angles 2
Cal 1-3 deg. 120 119.5 120.5
Cal 1-3 deg. 120 119.5 120.5
Difference between angles 3
Cal 1-6 deg. 180 179.5 180.5
Cal 1-6 deg. 180 179.5 180.5
Difference between angles 4
Cyl.1-2 deg. 240 239.5 240.5
Cyl.1-2 deg. 240 239.5 240.5
Difference between angles 5
Cal 1-4 deg. 300 299.5 300.5
Cal 1-4 deg. 300 299.5 300.5
Injection quantity adjustment
Adjusting point
A
Rack position
13.4
Pump speed
r/min
1000
1000
1000
Average injection quantity
mm3/st.
404
395
413
Max. variation between cylinders
%
0
-3
3
Basic
*
Fixing the lever
*
Boost pressure
kPa
93.3
93.3
Boost pressure
mmHg
700
700
Injection quantity adjustment_02
Adjusting point
-
Rack position
8.3+-0.5
Pump speed
r/min
300
300
300
Average injection quantity
mm3/st.
30
27
33
Max. variation between cylinders
%
0
-10
10
Fixing the rack
*
Boost pressure
kPa
0
0
0
Boost pressure
mmHg
0
0
0
Remarks
Adjust only variation between cylinders; adjust governor according to governor specifications.
Adjust only variation between cylinders; adjust governor according to governor specifications.
Boost compensator adjustment
Pump speed
r/min
750
750
750
Rack position
R1-3.2
Boost pressure
kPa
32
29.3
34.7
Boost pressure
mmHg
240
220
260
Boost compensator adjustment_02
Pump speed
r/min
750
750
750
Rack position
R1(13.4)
Boost pressure
kPa
80
73.3
86.7
Boost pressure
mmHg
600
550
650
Test data Ex:
Governor adjustment
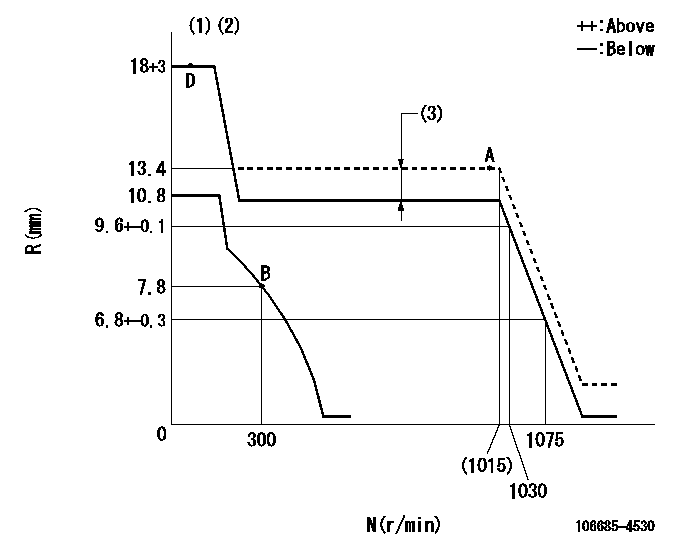
N:Pump speed
R:Rack position (mm)
(1)Target notch: K
(2)Tolerance for racks not indicated: +-0.05mm.
(3)Boost compensator stroke: BCL
----------
K=14 BCL=3.2+-0.1mm
----------
----------
K=14 BCL=3.2+-0.1mm
----------
Speed control lever angle

F:Full speed
I:Idle
(1)Stopper bolt setting
(2)At the center of the lever key groove
----------
----------
a=9deg+-5deg b=28.5deg+-5deg
----------
----------
a=9deg+-5deg b=28.5deg+-5deg
Stop lever angle

N:Pump normal
S:Stop the pump.
(1)Pump speed aa, rack position bb
----------
aa=0r/min bb=1-0.5mm
----------
a=33deg+-5deg b=(73deg)
----------
aa=0r/min bb=1-0.5mm
----------
a=33deg+-5deg b=(73deg)
Timing setting

(1)Pump vertical direction
(2)Coupling's key groove position at No 1 cylinder's beginning of injection
(3)-
(4)-
----------
----------
a=(20deg)
----------
----------
a=(20deg)
Information:
1. Disconnect plug P14 from receptacle J14. The locking ring helps identify P14 from J14. Check the connections for damaged wires or pins and corrosion. Also check that the pins are at the proper height in the connector. Check that the wires and pins are tight in the connectors by pulling (slightly) on each wire of each connector (including the breakout "T").2. Install 8T8694 Adapter (five pin breakout "T") between J14 and P14. Twist the locking rings to secure the connections.3. Connect the voltmeter as shown. Check for the appropriate voltages between the lettered "T" pins as explained in Steps 4 through 7.4. Pin A (+) to pin B (ground) system voltage should be approximately 12 volts DC with key on (no accessories). Minimum voltage is 11.0 volts DC. Diagnosis - Using the truck wiring schematic, check wires A and B and connections from J14 through the truck wiring harness back to the battery for proper voltage.5. If the voltage check between pins A and B is less than 11.0 volts with the key on, check the voltage drop from pin B to the negative battery post while cranking. For this test, the common lead (black) should be connected to the negative battery post first. Then place the positive (red) lead into pin B. (Pin B is chassis ground.) Voltage should be less than .5 volts DC when cranking. Diagnosis - If the voltage drop is greater than .5 volts DC, check wire B and connections (including the battery post connections) from J14 to battery negative. Follow the truck wiring schematic to trace the electrical path from J14 to chassis ground. Step 6 checks the proper functioning of the truck wiring, vehicle speed sensor and vehicle speed buffer. If proper vehicle speed is present on the appropriate status screens of the 3176 (7X1055) DDT or the (8T8697) ECAP service tools during road test than Step 6 is not necessary.6. Pin C to pin B:* 0 volts when stopped.* Up to 2.3 volts DC with the transmission output shaft turning and the speedometer disconnected (open circuit).
Remove the axle shafts or disconnect the drive shaft from the transmission to perform this test. See the truck manufacturer's instructions for the correct procedure(s).
Diagnosis: Remove magnetic pickup (vehicle speed sensor) from transmission. If pickup has collected significant metal debris, wipe it clean. Check the magnetic pickup per the manufactures specifications. Install a properly functioning magnetic pickup to the proper depth and reconnect to the vehicle speed buffer. Repeat Step 6. The problem may reappear if transmission fluid is contaminated. Change transmission fluid if necessary.* Check wires and connectors for damage or corrosion from the magnetic pickup to vehicle speed buffer.* Replace vehicle speed buffer (Caterpillar supplied part).
Vehicle Speed Buffer (1) Magnetic Pickup (2) in transmission.7. Pin D to pin B (static check):* Disconnect the magnetic pickup (in transmission) from the input wires of the vehicle speed buffer. With the key on, the voltage should be 4.5-7.5 volts DC. Diagnosis - If the
Remove the axle shafts or disconnect the drive shaft from the transmission to perform this test. See the truck manufacturer's instructions for the correct procedure(s).
Diagnosis: Remove magnetic pickup (vehicle speed sensor) from transmission. If pickup has collected significant metal debris, wipe it clean. Check the magnetic pickup per the manufactures specifications. Install a properly functioning magnetic pickup to the proper depth and reconnect to the vehicle speed buffer. Repeat Step 6. The problem may reappear if transmission fluid is contaminated. Change transmission fluid if necessary.* Check wires and connectors for damage or corrosion from the magnetic pickup to vehicle speed buffer.* Replace vehicle speed buffer (Caterpillar supplied part).
Vehicle Speed Buffer (1) Magnetic Pickup (2) in transmission.7. Pin D to pin B (static check):* Disconnect the magnetic pickup (in transmission) from the input wires of the vehicle speed buffer. With the key on, the voltage should be 4.5-7.5 volts DC. Diagnosis - If the