Information injection-pump assembly
BOSCH
9 400 617 692
9400617692
ZEXEL
106684-4540
1066844540
MITSUBISHI-HEAV
3266500210
3266500210
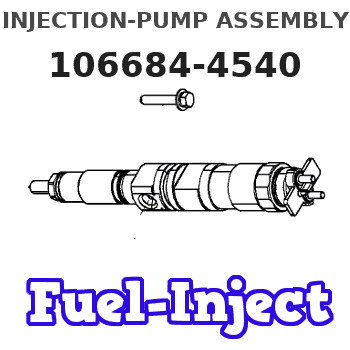
Rating:
Cross reference number
BOSCH
9 400 617 692
9400617692
ZEXEL
106684-4540
1066844540
MITSUBISHI-HEAV
3266500210
3266500210
Zexel num
Bosch num
Firm num
Name
9 400 617 692
3266500210 MITSUBISHI-HEAV
INJECTION-PUMP ASSEMBLY
S12A2 * K 14CA PE6P,6PD PE
S12A2 * K 14CA PE6P,6PD PE
Calibration Data:
Adjustment conditions
Test oil
1404 Test oil ISO4113 or {SAEJ967d}
1404 Test oil ISO4113 or {SAEJ967d}
Test oil temperature
degC
40
40
45
Nozzle and nozzle holder
105780-8130
Bosch type code
EFEP215A
Nozzle
105780-0050
Bosch type code
DN6TD119NP1T
Nozzle holder
105780-2090
Bosch type code
EFEP215
Opening pressure
MPa
17.2
Opening pressure
kgf/cm2
175
Injection pipe
Outer diameter - inner diameter - length (mm) mm 8-4-1000
Outer diameter - inner diameter - length (mm) mm 8-4-1000
Overflow valve
131424-3420
Overflow valve opening pressure
kPa
255
221
289
Overflow valve opening pressure
kgf/cm2
2.6
2.25
2.95
Tester oil delivery pressure
kPa
255
255
255
Tester oil delivery pressure
kgf/cm2
2.6
2.6
2.6
Direction of rotation (viewed from drive side)
Left L
Left L
Injection timing adjustment
Direction of rotation (viewed from drive side)
Left L
Left L
Injection order
1-5-3-6-
2-4
Pre-stroke
mm
2.8
2.75
2.85
Beginning of injection position
Opposite to the driving side NO.1
Opposite to the driving side NO.1
Difference between angles 1
Cal 1-5 deg. 60 59.5 60.5
Cal 1-5 deg. 60 59.5 60.5
Difference between angles 2
Cal 1-3 deg. 120 119.5 120.5
Cal 1-3 deg. 120 119.5 120.5
Difference between angles 3
Cal 1-6 deg. 180 179.5 180.5
Cal 1-6 deg. 180 179.5 180.5
Difference between angles 4
Cyl.1-2 deg. 240 239.5 240.5
Cyl.1-2 deg. 240 239.5 240.5
Difference between angles 5
Cal 1-4 deg. 300 299.5 300.5
Cal 1-4 deg. 300 299.5 300.5
Injection quantity adjustment
Adjusting point
A
Rack position
14.1
Pump speed
r/min
750
750
750
Average injection quantity
mm3/st.
520
511
529
Max. variation between cylinders
%
0
-3
3
Basic
*
Fixing the rack
*
Rack limit
*
Injection quantity adjustment_02
Adjusting point
-
Rack position
6.9+-0.5
Pump speed
r/min
375
375
375
Average injection quantity
mm3/st.
33
30
36
Max. variation between cylinders
%
0
-10
10
Fixing the rack
*
Test data Ex:
0000001501 RACK SENSOR
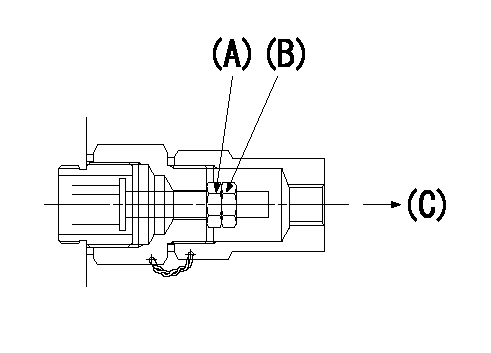
Nut A
(B) Nut
(C) Injection quantity decrease direction
1. Driven side rack limit mechanism adjustment procedure (for row R)
(1)Set the rack limit at adjusting point A using the two nuts (A) and (B) on the driven side end of the rack.
----------
----------
----------
----------
0000001601 RACK SENSOR
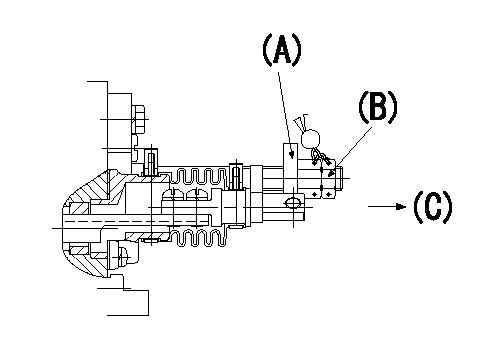
Plate A
(B) Nut
(C) Injection quantity increase direction
1. Drive side rack limit mechanism adjustment procedure (for row L)
(1)Set the rack limit at adjusting point A using the plate (A) above the drive side rack and the nut (B).
----------
----------
----------
----------
Timing setting

(1)Pump vertical direction
(2)Coupling's key groove position at No 1 cylinder's beginning of injection
(3)-
(4)-
----------
----------
a=(20deg)
----------
----------
a=(20deg)
Information:
Cleaning Air Filter Elements
The primary element (Caterpillar air filters) can be cleaned several times before replacement. The element, when cleaned, should be thoroughly checked for rips or tears in the filter material.Replace the primary element at least every year regardless of the number of operating hours the element has accumulated.
Do not clean filter elements by bumping or tapping.Do not use filter elements with damaged pleats, gaskets or seals. Engine damage could result.
Filter elements can be cleaned with air pressure, 205 kPa (30 psi) maximum, or water pressure, 280 kPa (40 psi) maximum, or detergent washing. Have spare elements on hand to use while cleaning used elements.* Direct air or water along the length of the pleats inside and outside of filter element. The element can be washed in warm water and nonsudsing household detergent, such as automatic dishwasher detergent. Rinse inside and outside the pleats. The filter should then be thoroughly air dried and inspected. * Inspect the filter elements after cleaning for any rips, tears or damage. Insert a light inside of the clean, dry element. Do not use a filter element with damaged pleats, gaskets or seals. Discard the element if damaged. * Wrap and store the clean filter elements in a clean, dry place.For more information on air cleaner element cleaning, refer to SEBF8062, Guideline for Reusable Parts-Cleaning and Inspection of Air Filters.Belts
Check/Adjust
Inspect the condition and adjustment of alternator and accessory drive belts. Examine all drive belts for wear and replace if they show any signs of wear. Loose or worn pulley grooves cause belt slippage and low accessory drive speed. If belts are too loose, they vibrate enough to cause unnecessary wear on the belts and pulleys and possibly slip enough to cause overheating.If belts are too tight, unnecessary stresses are placed upon the pulley bearings and belts which might shorten the life of both.If one belt in a set requires replacement, always install a new matched set of belts. Never replace just the worn belt. If only the worn belt is replaced, the new belt will carry all the load, as it will not be stretched as much as the older belts. All the belts will fail in rapid succession.Remove the belt guard. Inspect the condition and adjustment of alternator belts and accessory drive belts (if equipped).To check the belt tension, apply 110 Newton (25 lb) force, perpendicular to the belt, midway between the driving and driven pulley. Measure the belt deflection. Correctly adjusted belts will deflect 15 to 20 mm (9/16 to 7/8 inch).If the belt does not require replacement or adjustment, install the belt guard. If the belt requires adjustment or replacement, perform the following procedure to adjust the belt tension.
Typical belt assembly mounting bolt (1) and adjusting nuts (2).1. Loosen the mounting bolt (1) and the locknut on the adjusting bolt.2. Turn the adjusting nuts (2) to increase or decrease the belt tension.3. Tighten the adjusting bolt locknut. Tighten the mounting bolts. Refer to the Torque Specifications in
The primary element (Caterpillar air filters) can be cleaned several times before replacement. The element, when cleaned, should be thoroughly checked for rips or tears in the filter material.Replace the primary element at least every year regardless of the number of operating hours the element has accumulated.
Do not clean filter elements by bumping or tapping.Do not use filter elements with damaged pleats, gaskets or seals. Engine damage could result.
Filter elements can be cleaned with air pressure, 205 kPa (30 psi) maximum, or water pressure, 280 kPa (40 psi) maximum, or detergent washing. Have spare elements on hand to use while cleaning used elements.* Direct air or water along the length of the pleats inside and outside of filter element. The element can be washed in warm water and nonsudsing household detergent, such as automatic dishwasher detergent. Rinse inside and outside the pleats. The filter should then be thoroughly air dried and inspected. * Inspect the filter elements after cleaning for any rips, tears or damage. Insert a light inside of the clean, dry element. Do not use a filter element with damaged pleats, gaskets or seals. Discard the element if damaged. * Wrap and store the clean filter elements in a clean, dry place.For more information on air cleaner element cleaning, refer to SEBF8062, Guideline for Reusable Parts-Cleaning and Inspection of Air Filters.Belts
Check/Adjust
Inspect the condition and adjustment of alternator and accessory drive belts. Examine all drive belts for wear and replace if they show any signs of wear. Loose or worn pulley grooves cause belt slippage and low accessory drive speed. If belts are too loose, they vibrate enough to cause unnecessary wear on the belts and pulleys and possibly slip enough to cause overheating.If belts are too tight, unnecessary stresses are placed upon the pulley bearings and belts which might shorten the life of both.If one belt in a set requires replacement, always install a new matched set of belts. Never replace just the worn belt. If only the worn belt is replaced, the new belt will carry all the load, as it will not be stretched as much as the older belts. All the belts will fail in rapid succession.Remove the belt guard. Inspect the condition and adjustment of alternator belts and accessory drive belts (if equipped).To check the belt tension, apply 110 Newton (25 lb) force, perpendicular to the belt, midway between the driving and driven pulley. Measure the belt deflection. Correctly adjusted belts will deflect 15 to 20 mm (9/16 to 7/8 inch).If the belt does not require replacement or adjustment, install the belt guard. If the belt requires adjustment or replacement, perform the following procedure to adjust the belt tension.
Typical belt assembly mounting bolt (1) and adjusting nuts (2).1. Loosen the mounting bolt (1) and the locknut on the adjusting bolt.2. Turn the adjusting nuts (2) to increase or decrease the belt tension.3. Tighten the adjusting bolt locknut. Tighten the mounting bolts. Refer to the Torque Specifications in