Information injection-pump assembly
BOSCH
9 400 617 686
9400617686
ZEXEL
106684-4470
1066844470
MITSUBISHI-HEAV
3266500120
3266500120
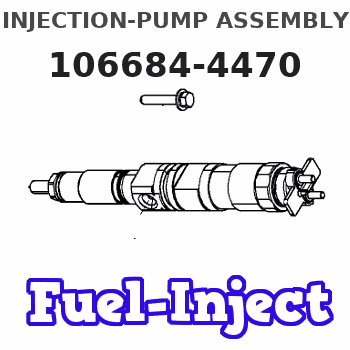
Rating:
Service parts 106684-4470 INJECTION-PUMP ASSEMBLY:
1.
_
3.
GOVERNOR
5.
AUTOM. ADVANCE MECHANIS
8.
_
9.
_
11.
Nozzle and Holder
12.
Open Pre:MPa(Kqf/cm2)
29.4{300}
15.
NOZZLE SET
Include in #1:
106684-4470
as INJECTION-PUMP ASSEMBLY
Cross reference number
BOSCH
9 400 617 686
9400617686
ZEXEL
106684-4470
1066844470
MITSUBISHI-HEAV
3266500120
3266500120
Zexel num
Bosch num
Firm num
Name
106684-4470
9 400 617 686
3266500120 MITSUBISHI-HEAV
INJECTION-PUMP ASSEMBLY
S12A2 K 14CA INJECTION PUMP ASSY PE6P,6PD PE
S12A2 K 14CA INJECTION PUMP ASSY PE6P,6PD PE
Calibration Data:
Adjustment conditions
Test oil
1404 Test oil ISO4113 or {SAEJ967d}
1404 Test oil ISO4113 or {SAEJ967d}
Test oil temperature
degC
40
40
45
Nozzle and nozzle holder
105780-8130
Bosch type code
EFEP215A
Nozzle
105780-0050
Bosch type code
DN6TD119NP1T
Nozzle holder
105780-2090
Bosch type code
EFEP215
Opening pressure
MPa
17.2
Opening pressure
kgf/cm2
175
Injection pipe
Outer diameter - inner diameter - length (mm) mm 8-4-1000
Outer diameter - inner diameter - length (mm) mm 8-4-1000
Overflow valve
131424-3420
Overflow valve opening pressure
kPa
255
221
289
Overflow valve opening pressure
kgf/cm2
2.6
2.25
2.95
Tester oil delivery pressure
kPa
255
255
255
Tester oil delivery pressure
kgf/cm2
2.6
2.6
2.6
Direction of rotation (viewed from drive side)
Left L
Left L
Injection timing adjustment
Direction of rotation (viewed from drive side)
Left L
Left L
Injection order
1-5-3-6-
2-4
Pre-stroke
mm
3
2.95
3.05
Beginning of injection position
Opposite to the driving side NO.1
Opposite to the driving side NO.1
Difference between angles 1
Cal 1-5 deg. 60 59.5 60.5
Cal 1-5 deg. 60 59.5 60.5
Difference between angles 2
Cal 1-3 deg. 120 119.5 120.5
Cal 1-3 deg. 120 119.5 120.5
Difference between angles 3
Cal 1-6 deg. 180 179.5 180.5
Cal 1-6 deg. 180 179.5 180.5
Difference between angles 4
Cyl.1-2 deg. 240 239.5 240.5
Cyl.1-2 deg. 240 239.5 240.5
Difference between angles 5
Cal 1-4 deg. 300 299.5 300.5
Cal 1-4 deg. 300 299.5 300.5
Injection quantity adjustment
Adjusting point
A
Rack position
10.9
Pump speed
r/min
900
900
900
Average injection quantity
mm3/st.
350
341
359
Max. variation between cylinders
%
0
-3
3
Basic
*
Fixing the rack
*
Rack limit
*
Injection quantity adjustment_02
Adjusting point
-
Rack position
6.1+-0.5
Pump speed
r/min
350
350
350
Average injection quantity
mm3/st.
24.5
21.5
27.5
Max. variation between cylinders
%
0
-10
10
Fixing the rack
*
Test data Ex:
0000001501 RACK SENSOR
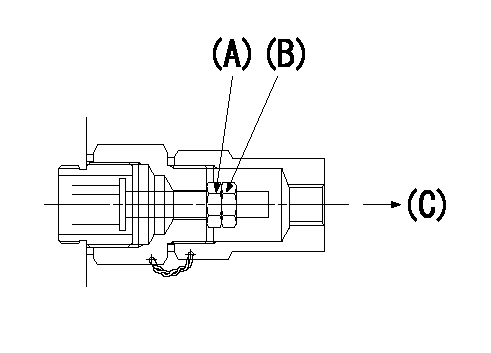
Nut A
(B) Nut
(C) Injection quantity decrease direction
1. Driven side rack limit mechanism adjustment procedure (for row R)
(1)Set the rack limit at adjusting point A using the two nuts (A) and (B) on the driven side end of the rack.
----------
----------
----------
----------
Timing setting

(1)Pump vertical direction
(2)Coupling's key groove position at No 1 cylinder's beginning of injection
(3)-
(4)-
----------
----------
a=(20deg)
----------
----------
a=(20deg)
Information:
ELC cooling systems can withstand contamination of up to ten percent of conventional HD coolant/antifreeze. If the contamination exceeds ten percent of the total system capacity, perform either one of the following two procedures:* Drain the cooling system. Flush the system with clean water. Refill the system with ELC.* Maintain the cooling system as if the system is filled with conventional HD coolant/antifreeze.Commercial Extended Life Coolant
If Caterpillar extended life coolant is not used, select a commercial extended life coolant that meets the Caterpillar EC-1 specification. Do not use a product that is labeled as an extended life coolant but does not meet the Caterpillar EC-1 specification. Follow the coolant maintenance guidelines of the commercial extended life coolant supplier. In all cases, use distilled or deionized water or use water that has the properties listed in the Caterpillar Water Quality Limits chart.Caterpillar Diesel Engine Antifreeze/Coolant (DEAC)
For cooling systems using conventional HD coolant, Caterpillar recommends the use of Caterpillar Diesel Engine Antifreeze/Coolant (DEAC). DEAC is an alkaline type, single-phase, ethylene glycol-based antifreeze/coolant. DEAC contains inorganic corrosion inhibitors and anti-foaming agents.Contact your Caterpillar dealer for part numbers and available container sizes.Caterpillar DEAC is available premixed with distilled water in a 50/50 concentration. If DEAC concentrate is used, Caterpillar recommends mixing the concentrate with distilled or deionized water. If distilled or deionized water is not available, use water that has the properties listed in the Caterpillar Water Quality Limits chart.Caterpillar Supplemental Coolant Additive (SCA)
Caterpillar Supplemental Coolant Additive (SCA) is effective in preventing corrosion on all metals. Caterpillar SCA also prevents the formation of mineral deposits, prevents liner cavitation, and eliminates coolant foaming.Caterpillar DEAC is formulated with the correct level of Caterpillar SCA. Additional SCA is NOT needed when the cooling system is initially filled with DEAC.Contact your Caterpillar dealer for part numbers and available container sizes.Commercial Heavy Duty (HD) Coolant/Antifreeze and SCA
If Caterpillar DEAC is not used, select a low silicate commercial HD coolant/antifreeze that meets ASTM D5345 or D4985 specifications.When a commercial HD coolant/antifreeze is used, the cooling system should be treated with three to six percent Caterpillar SCA by volume. Refer to the Caterpillar SCA Requirements for Heavy Duty Coolant/Antifreeze chart. If Caterpillar SCA is not used, select a commercial SCA. The commercial SCA must provide a minimum of 1200 mg/L or 1200 ppm (70 grains/US gal) nitrites in the final coolant mixture. Follow the coolant maintenance guidelines of the commercial SCA supplier.HD coolant/antifreezes that meet ASTM D5345 or D4985 specifications DO require SCA treatment at initial fill, and on a maintenance basis.When mixing concentrated coolants, use distilled or deionized water or use water that has the properties listed in the Caterpillar Water Quality Limits chart.Heavy Duty Coolant/Antifreeze Cooling System Maintenance
Never operate an engine without thermostats in the cooling system. Thermostats maintain the engine coolant at the proper operating temperature. Cooling system problems can develop without thermostats.
Check the coolant/antifreeze solution (glycol content) frequently to ensure adequate anti-boil and anti-freeze protection. Caterpillar recommends the use of a refractometer for checking the
If Caterpillar extended life coolant is not used, select a commercial extended life coolant that meets the Caterpillar EC-1 specification. Do not use a product that is labeled as an extended life coolant but does not meet the Caterpillar EC-1 specification. Follow the coolant maintenance guidelines of the commercial extended life coolant supplier. In all cases, use distilled or deionized water or use water that has the properties listed in the Caterpillar Water Quality Limits chart.Caterpillar Diesel Engine Antifreeze/Coolant (DEAC)
For cooling systems using conventional HD coolant, Caterpillar recommends the use of Caterpillar Diesel Engine Antifreeze/Coolant (DEAC). DEAC is an alkaline type, single-phase, ethylene glycol-based antifreeze/coolant. DEAC contains inorganic corrosion inhibitors and anti-foaming agents.Contact your Caterpillar dealer for part numbers and available container sizes.Caterpillar DEAC is available premixed with distilled water in a 50/50 concentration. If DEAC concentrate is used, Caterpillar recommends mixing the concentrate with distilled or deionized water. If distilled or deionized water is not available, use water that has the properties listed in the Caterpillar Water Quality Limits chart.Caterpillar Supplemental Coolant Additive (SCA)
Caterpillar Supplemental Coolant Additive (SCA) is effective in preventing corrosion on all metals. Caterpillar SCA also prevents the formation of mineral deposits, prevents liner cavitation, and eliminates coolant foaming.Caterpillar DEAC is formulated with the correct level of Caterpillar SCA. Additional SCA is NOT needed when the cooling system is initially filled with DEAC.Contact your Caterpillar dealer for part numbers and available container sizes.Commercial Heavy Duty (HD) Coolant/Antifreeze and SCA
If Caterpillar DEAC is not used, select a low silicate commercial HD coolant/antifreeze that meets ASTM D5345 or D4985 specifications.When a commercial HD coolant/antifreeze is used, the cooling system should be treated with three to six percent Caterpillar SCA by volume. Refer to the Caterpillar SCA Requirements for Heavy Duty Coolant/Antifreeze chart. If Caterpillar SCA is not used, select a commercial SCA. The commercial SCA must provide a minimum of 1200 mg/L or 1200 ppm (70 grains/US gal) nitrites in the final coolant mixture. Follow the coolant maintenance guidelines of the commercial SCA supplier.HD coolant/antifreezes that meet ASTM D5345 or D4985 specifications DO require SCA treatment at initial fill, and on a maintenance basis.When mixing concentrated coolants, use distilled or deionized water or use water that has the properties listed in the Caterpillar Water Quality Limits chart.Heavy Duty Coolant/Antifreeze Cooling System Maintenance
Never operate an engine without thermostats in the cooling system. Thermostats maintain the engine coolant at the proper operating temperature. Cooling system problems can develop without thermostats.
Check the coolant/antifreeze solution (glycol content) frequently to ensure adequate anti-boil and anti-freeze protection. Caterpillar recommends the use of a refractometer for checking the
Have questions with 106684-4470?
Group cross 106684-4470 ZEXEL
Komatsu
Komatsu
Komatsu
Komatsu
Komatsu
Mitsubishi-Heav
106684-4470
9 400 617 686
3266500120
INJECTION-PUMP ASSEMBLY
S12A2
S12A2