Information injection-pump assembly
BOSCH
9 400 611 906
9400611906
ZEXEL
106684-4320
1066844320
MITSUBISHI-HEAV
35A6501320
35a6501320
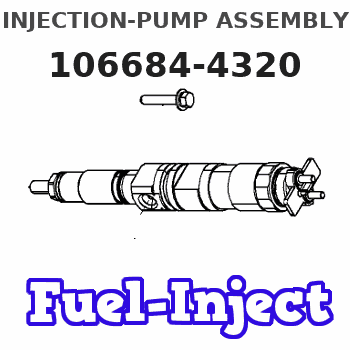
Rating:
Service parts 106684-4320 INJECTION-PUMP ASSEMBLY:
1.
_
3.
GOVERNOR
5.
AUTOM. ADVANCE MECHANIS
8.
_
9.
_
11.
Nozzle and Holder
35A61-00080
12.
Open Pre:MPa(Kqf/cm2)
21.6{220}
14.
NOZZLE
15.
NOZZLE SET
Include in #1:
106684-4320
as INJECTION-PUMP ASSEMBLY
Cross reference number
BOSCH
9 400 611 906
9400611906
ZEXEL
106684-4320
1066844320
MITSUBISHI-HEAV
35A6501320
35a6501320
Zexel num
Bosch num
Firm num
Name
Calibration Data:
Adjustment conditions
Test oil
1404 Test oil ISO4113 or {SAEJ967d}
1404 Test oil ISO4113 or {SAEJ967d}
Test oil temperature
degC
40
40
45
Nozzle and nozzle holder
105780-8130
Bosch type code
EFEP215A
Nozzle
105780-0050
Bosch type code
DN6TD119NP1T
Nozzle holder
105780-2090
Bosch type code
EFEP215
Opening pressure
MPa
17.2
Opening pressure
kgf/cm2
175
Injection pipe
Outer diameter - inner diameter - length (mm) mm 8-4-1000
Outer diameter - inner diameter - length (mm) mm 8-4-1000
Overflow valve
131424-3420
Overflow valve opening pressure
kPa
255
221
289
Overflow valve opening pressure
kgf/cm2
2.6
2.25
2.95
Tester oil delivery pressure
kPa
157
157
157
Tester oil delivery pressure
kgf/cm2
1.6
1.6
1.6
Direction of rotation (viewed from drive side)
Left L
Left L
Injection timing adjustment
Direction of rotation (viewed from drive side)
Left L
Left L
Injection order
1-5-3-6-
2-4
Pre-stroke
mm
2.8
2.75
2.85
Beginning of injection position
Opposite to the driving side NO.1
Opposite to the driving side NO.1
Difference between angles 1
Cal 1-5 deg. 60 59.5 60.5
Cal 1-5 deg. 60 59.5 60.5
Difference between angles 2
Cal 1-3 deg. 120 119.5 120.5
Cal 1-3 deg. 120 119.5 120.5
Difference between angles 3
Cal 1-6 deg. 180 179.5 180.5
Cal 1-6 deg. 180 179.5 180.5
Difference between angles 4
Cyl.1-2 deg. 240 239.5 240.5
Cyl.1-2 deg. 240 239.5 240.5
Difference between angles 5
Cal 1-4 deg. 300 299.5 300.5
Cal 1-4 deg. 300 299.5 300.5
Injection quantity adjustment
Adjusting point
A
Rack position
13.6
Pump speed
r/min
900
900
900
Average injection quantity
mm3/st.
415
406
424
Max. variation between cylinders
%
0
-3
3
Basic
*
Fixing the rack
*
Rack limit
*
Injection quantity adjustment_02
Adjusting point
B
Rack position
6.5+-0.5
Pump speed
r/min
250
250
250
Average injection quantity
mm3/st.
30.5
27.5
33.5
Max. variation between cylinders
%
0
-10
10
Fixing the rack
*
Test data Ex:
Timing setting

(1)Pump vertical direction
(2)Coupling's key groove position at No 1 cylinder's beginning of injection
(3)-
(4)-
----------
----------
a=(20deg)
----------
----------
a=(20deg)
Information:
Fuel System Information
Fill the fuel tank at the end of each day of operation to drive out moist air and to prevent condensation. Do not fill the tank to the top. Fuel expands as it gets warm and may overflow.Do not fill fuel filters with fuel before installing them. Contaminated fuel will cause accelerated wear to fuel system parts.
Fuel Recommendations
Use only fuel as recommended in this section. The fuels recommended for use in Caterpillar engines are No.2-D diesel fuel and No.2 fuel oil, although No. 1 grades are acceptable. The following fuel specifications are some of the worldwide fuels which also meet the requirements. The following fuel characteristics should be considered when procuring fuel for use in Caterpillar diesel engines. Caterpillar Diesel Engines are capable of burning a wide range of distillate fuels. The use of clean, stable blends of distillate fuel which meet the following requirements will provide quality engine service life. Cetane Number
The minimum cetane number required for average starting conditions for the direct injection engine is 40. A higher cetane value may be required for high altitude operation or cold weather starting.Filterability
Clean fuels should have no more than 0.1% of sediment and water. Storage of fuel for extended periods of time can cause fuel oxidation with solids forming, causing filtering problems.Pour Point
The pour point of the fuel should be at least 10°F (6°C) below the lowest ambient temperature at which the engines must start and operate. The lower pour point of No.1 or No.1-D fuel may be necessary in extremely cold weather.Cloud Point
The cloud point should be below the lowest ambient temperature at which the engines must start and operate to prevent the fuel filter elements from plugging with wax crystals. Refer to topic, Fuel Problems in Cold Weather Operation, for additional information.Sulfur
Fuels containing 0.5% or less sulfur may be used with recommended crankcase oil drain intervals using API CD, CE or CF-4 performance oils. With sulfur above the 0.5% level, use API CD, CE or CF-4 oils with an ASTM D-2896 Total Base Number (TBN) of 20 times the fuel sulfur for normal oil drain intervals. Regular oil analysis (S O S) will provide information to monitor oil properties and engine wear metals to maintain successful engine protection and establish oil drain intervals.Viscosity
The viscosity of any fluid is a measure of resistance to flow. Fuel viscosity is important because it provides lubrication for fuel system components and also its effects on fuel atomization. The viscosity limits have been provided to meet both of these effects.Additives
Fuel additives are generally not recommended nor needed for the specified fuels listed. Cetane improvers can be used as necessary for the direct injection engine requirements. Biocides may be needed to eliminate microorganism growth in storage tanks. In cold conditions, treatment for entrained water may also be necessary.Consult your fuel supplier about the use of additives to prevent incompatibility among additives already in the fuel and the additives to be used. Other fuel types may be burned in the engine
Fill the fuel tank at the end of each day of operation to drive out moist air and to prevent condensation. Do not fill the tank to the top. Fuel expands as it gets warm and may overflow.Do not fill fuel filters with fuel before installing them. Contaminated fuel will cause accelerated wear to fuel system parts.
Fuel Recommendations
Use only fuel as recommended in this section. The fuels recommended for use in Caterpillar engines are No.2-D diesel fuel and No.2 fuel oil, although No. 1 grades are acceptable. The following fuel specifications are some of the worldwide fuels which also meet the requirements. The following fuel characteristics should be considered when procuring fuel for use in Caterpillar diesel engines. Caterpillar Diesel Engines are capable of burning a wide range of distillate fuels. The use of clean, stable blends of distillate fuel which meet the following requirements will provide quality engine service life. Cetane Number
The minimum cetane number required for average starting conditions for the direct injection engine is 40. A higher cetane value may be required for high altitude operation or cold weather starting.Filterability
Clean fuels should have no more than 0.1% of sediment and water. Storage of fuel for extended periods of time can cause fuel oxidation with solids forming, causing filtering problems.Pour Point
The pour point of the fuel should be at least 10°F (6°C) below the lowest ambient temperature at which the engines must start and operate. The lower pour point of No.1 or No.1-D fuel may be necessary in extremely cold weather.Cloud Point
The cloud point should be below the lowest ambient temperature at which the engines must start and operate to prevent the fuel filter elements from plugging with wax crystals. Refer to topic, Fuel Problems in Cold Weather Operation, for additional information.Sulfur
Fuels containing 0.5% or less sulfur may be used with recommended crankcase oil drain intervals using API CD, CE or CF-4 performance oils. With sulfur above the 0.5% level, use API CD, CE or CF-4 oils with an ASTM D-2896 Total Base Number (TBN) of 20 times the fuel sulfur for normal oil drain intervals. Regular oil analysis (S O S) will provide information to monitor oil properties and engine wear metals to maintain successful engine protection and establish oil drain intervals.Viscosity
The viscosity of any fluid is a measure of resistance to flow. Fuel viscosity is important because it provides lubrication for fuel system components and also its effects on fuel atomization. The viscosity limits have been provided to meet both of these effects.Additives
Fuel additives are generally not recommended nor needed for the specified fuels listed. Cetane improvers can be used as necessary for the direct injection engine requirements. Biocides may be needed to eliminate microorganism growth in storage tanks. In cold conditions, treatment for entrained water may also be necessary.Consult your fuel supplier about the use of additives to prevent incompatibility among additives already in the fuel and the additives to be used. Other fuel types may be burned in the engine