Information injection-pump assembly
BOSCH
9 400 619 960
9400619960
ZEXEL
106682-9801
1066829801
KOMATSU
6152751340
6152751340
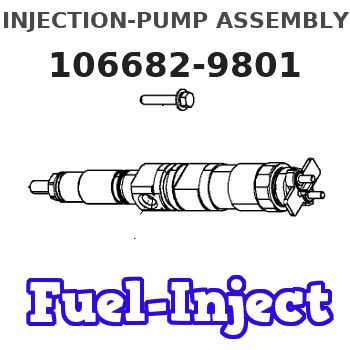
Rating:
Service parts 106682-9801 INJECTION-PUMP ASSEMBLY:
1.
_
5.
AUTOM. ADVANCE MECHANIS
8.
_
9.
_
11.
Nozzle and Holder
12.
Open Pre:MPa(Kqf/cm2)
26.0{265}
15.
NOZZLE SET
Include in #1:
106682-9801
as INJECTION-PUMP ASSEMBLY
Cross reference number
BOSCH
9 400 619 960
9400619960
ZEXEL
106682-9801
1066829801
KOMATSU
6152751340
6152751340
Zexel num
Bosch num
Firm num
Name
Calibration Data:
Adjustment conditions
Test oil
1404 Test oil ISO4113 or {SAEJ967d}
1404 Test oil ISO4113 or {SAEJ967d}
Test oil temperature
degC
40
40
45
Nozzle and nozzle holder
105780-8130
Bosch type code
EFEP215A
Nozzle
105780-0050
Bosch type code
DN6TD119NP1T
Nozzle holder
105780-2090
Bosch type code
EFEP215
Opening pressure
MPa
17.2
Opening pressure
kgf/cm2
175
Injection pipe
Outer diameter - inner diameter - length (mm) mm 8-4-1000
Outer diameter - inner diameter - length (mm) mm 8-4-1000
Overflow valve
131425-1620
Overflow valve opening pressure
kPa
255
255
255
Overflow valve opening pressure
kgf/cm2
2.6
2.6
2.6
Tester oil delivery pressure
kPa
157
157
157
Tester oil delivery pressure
kgf/cm2
1.6
1.6
1.6
Direction of rotation (viewed from drive side)
Left L
Left L
Injection timing adjustment
Direction of rotation (viewed from drive side)
Left L
Left L
Injection order
1-5-3-6-
2-4
Pre-stroke
mm
2.8
2.75
2.85
Beginning of injection position
Drive side NO.1
Drive side NO.1
Difference between angles 1
Cal 1-5 deg. 60 59.5 60.5
Cal 1-5 deg. 60 59.5 60.5
Difference between angles 2
Cal 1-3 deg. 120 119.5 120.5
Cal 1-3 deg. 120 119.5 120.5
Difference between angles 3
Cal 1-6 deg. 180 179.5 180.5
Cal 1-6 deg. 180 179.5 180.5
Difference between angles 4
Cyl.1-2 deg. 240 239.5 240.5
Cyl.1-2 deg. 240 239.5 240.5
Difference between angles 5
Cal 1-4 deg. 300 299.5 300.5
Cal 1-4 deg. 300 299.5 300.5
Injection quantity adjustment
Adjusting point
A
Rack position
17.2
Pump speed
r/min
1150
1150
1150
Average injection quantity
mm3/st.
437
434
440
Max. variation between cylinders
%
0
-3
3
Basic
*
Fixing the lever
*
Boost pressure
kPa
131
131
Boost pressure
mmHg
980
980
Injection quantity adjustment_02
Adjusting point
C
Rack position
9.2+-0.5
Pump speed
r/min
270
270
270
Average injection quantity
mm3/st.
20
18
22
Max. variation between cylinders
%
0
-15
15
Fixing the rack
*
Boost pressure
kPa
0
0
0
Boost pressure
mmHg
0
0
0
Boost compensator adjustment
Pump speed
r/min
600
600
600
Rack position
R1-3.9
Boost pressure
kPa
30.7
28
33.4
Boost pressure
mmHg
230
210
250
Boost compensator adjustment_02
Pump speed
r/min
600
600
600
Rack position
R1(17.2)
Boost pressure
kPa
117
110.3
123.7
Boost pressure
mmHg
880
830
930
Test data Ex:
Governor adjustment
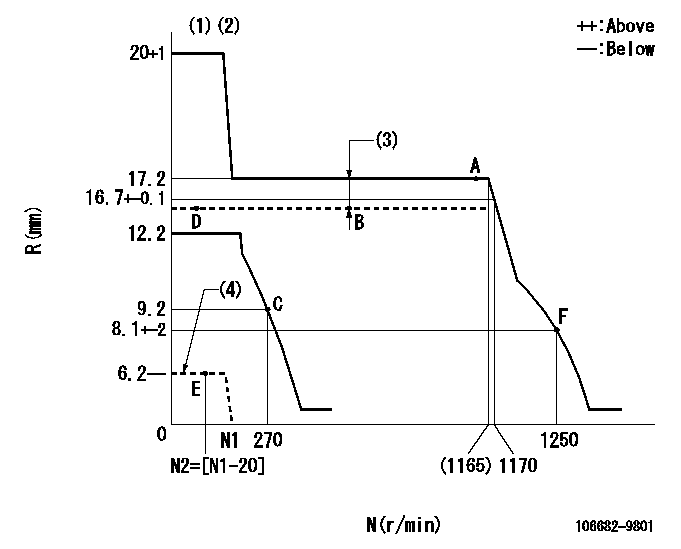
N:Pump speed
R:Rack position (mm)
(1)Target notch: K
(2)Tolerance for racks not indicated: +-0.05mm.
(3)Boost compensator stroke: BCL
(4)Stop lever at stopping (with the stop lever at full)
----------
K=11 BCL=3.9+-0.1mm
----------
----------
K=11 BCL=3.9+-0.1mm
----------
Speed control lever angle
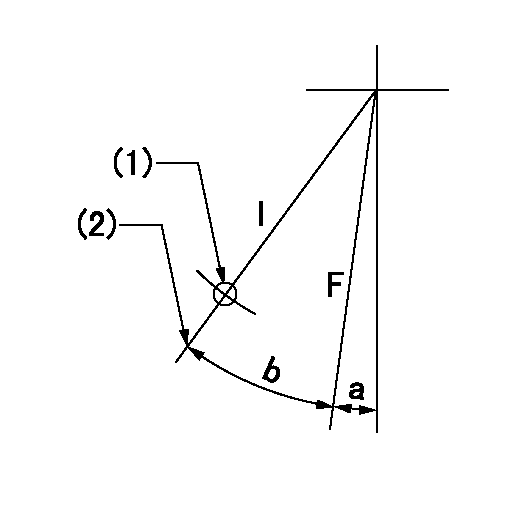
F:Full speed
I:Idle
(1)Use the hole at R = aa
(2)Stopper bolt setting
----------
aa=90mm
----------
a=3deg+-5deg b=38deg+-5deg
----------
aa=90mm
----------
a=3deg+-5deg b=38deg+-5deg
Stop lever angle
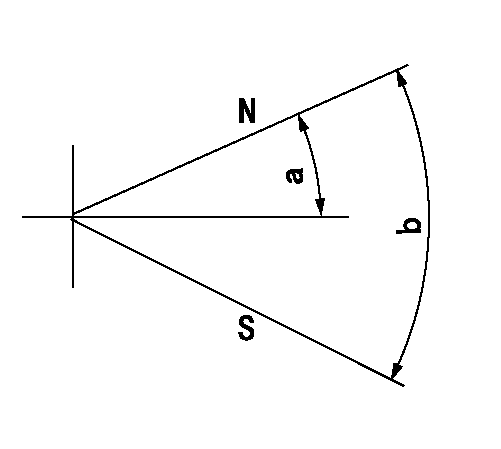
N:Pump normal
S:Stop the pump.
----------
----------
a=19deg+-5deg b=53deg+-5deg
----------
----------
a=19deg+-5deg b=53deg+-5deg
Timing setting
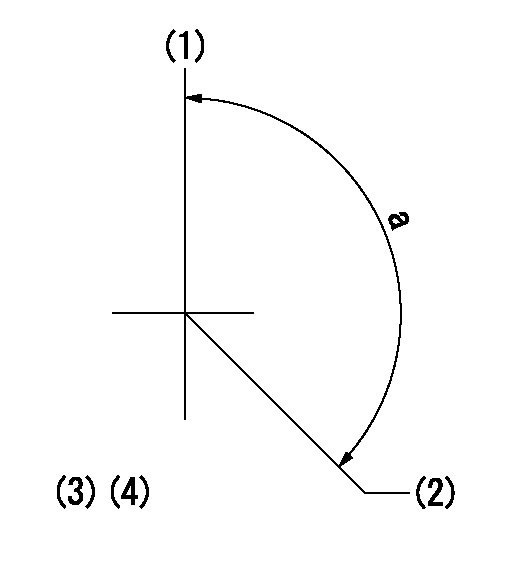
(1)Pump vertical direction
(2)Coupling's key groove position at No 1 cylinder's beginning of injection
(3)-
(4)-
----------
----------
a=(150deg)
----------
----------
a=(150deg)
Information:
USE FUEL CONSUMPTION, SERVICE HOURS OR TIME INTERVAL, WHICHEVER COMES FIRST. Performance of all lubrication and maintenance items in the Maintenance Schedule is the owners' responsibility.Daily
Walk-Around Inspection - Inspect for leaks and loose connections Engine Crankcase - Check oil level Cooling System - Check coolant level Air Cleaner Indicator - Test Air Starting Motor (If Equipped) - Check/fill oiler bowlEvery 11 845 L (3125 gal) of Fuel or 125 Hours*
Scheduled Oil Sampling (S O S) Analysis - Obtain sample Engine Oil & Filters - Change oil and oil filter(s) 1 Fuel System - Drain water/sediment Cooling System - Test Crankcase Breathers - Clean Engine Valve Lash (At First Oil Change Only) - Check/AdjustEvery 23 690 L (6250 gal) of Fuel or 250 Hours*
Batteries - Clean/Check electrolyte level Belts, Hoses and Clamps - Inspect/Replace if necessary Engine Air Cleaners - Replace Engine Speed Sensors - Inspect/clean magnetic pick-upEvery 94 750 L (25,000 gal) of Fuel or 1000 Hours*
Engine Protection Devices - Inspect for proper operation (Check at least twice per year) Engine Valve Lash - Check/Adjust Turbochargers - Inspect for proper operation Engine Mounts and Crankshaft Vibration Damper - Inspect/checkEvery 213 190 L (56,250 gal) of Fuel or 2250 Hours or Every Year*
Connecting Rod Bearings - Replace 2Every 284 250 L (75,000 gal) of Fuel or 3000 Hours or Two Years*
Cooling System - Clean/Flush/replace thermostats and gasketsOverhaul Every 511 650 L (135,000 gal) of Fuel or 5400 Hours*
To minimize downtime and provide you with the lowest cost and highest value, Caterpillar recommends that the engine be overhauled before failure by scheduling an overhaul with your Caterpillar dealer. Refer to the Overhaul section in this manual on page 85. Top End Overhaul After Failure Overhaul Starting Motor - Inspect for proper operation Alternator - Inspect for proper operation Engine Speed Sensors - Inspect/clean/test*First Perform Previous Service Hour Items1For ratings less than 630 hp and a 70 percent load factor approximately one half of the operating time, the oil change interval may be extended to every 250 hours.2For ratings less than 630 hp and a 70 percent load factor approximately one half of the operating time, replacing the connecting rod bearings may be extended to every 4500 hours. Caterpillar suggests that fuel consumption be used as the preferred method of determining maintenance intervals. Fuel consumption/hours will vary depending on the proper application of your engine rating and adherence to recommended maintenance procedures.
Walk-Around Inspection - Inspect for leaks and loose connections Engine Crankcase - Check oil level Cooling System - Check coolant level Air Cleaner Indicator - Test Air Starting Motor (If Equipped) - Check/fill oiler bowlEvery 11 845 L (3125 gal) of Fuel or 125 Hours*
Scheduled Oil Sampling (S O S) Analysis - Obtain sample Engine Oil & Filters - Change oil and oil filter(s) 1 Fuel System - Drain water/sediment Cooling System - Test Crankcase Breathers - Clean Engine Valve Lash (At First Oil Change Only) - Check/AdjustEvery 23 690 L (6250 gal) of Fuel or 250 Hours*
Batteries - Clean/Check electrolyte level Belts, Hoses and Clamps - Inspect/Replace if necessary Engine Air Cleaners - Replace Engine Speed Sensors - Inspect/clean magnetic pick-upEvery 94 750 L (25,000 gal) of Fuel or 1000 Hours*
Engine Protection Devices - Inspect for proper operation (Check at least twice per year) Engine Valve Lash - Check/Adjust Turbochargers - Inspect for proper operation Engine Mounts and Crankshaft Vibration Damper - Inspect/checkEvery 213 190 L (56,250 gal) of Fuel or 2250 Hours or Every Year*
Connecting Rod Bearings - Replace 2Every 284 250 L (75,000 gal) of Fuel or 3000 Hours or Two Years*
Cooling System - Clean/Flush/replace thermostats and gasketsOverhaul Every 511 650 L (135,000 gal) of Fuel or 5400 Hours*
To minimize downtime and provide you with the lowest cost and highest value, Caterpillar recommends that the engine be overhauled before failure by scheduling an overhaul with your Caterpillar dealer. Refer to the Overhaul section in this manual on page 85. Top End Overhaul After Failure Overhaul Starting Motor - Inspect for proper operation Alternator - Inspect for proper operation Engine Speed Sensors - Inspect/clean/test*First Perform Previous Service Hour Items1For ratings less than 630 hp and a 70 percent load factor approximately one half of the operating time, the oil change interval may be extended to every 250 hours.2For ratings less than 630 hp and a 70 percent load factor approximately one half of the operating time, replacing the connecting rod bearings may be extended to every 4500 hours. Caterpillar suggests that fuel consumption be used as the preferred method of determining maintenance intervals. Fuel consumption/hours will vary depending on the proper application of your engine rating and adherence to recommended maintenance procedures.