Information injection-pump assembly
BOSCH
9 400 610 976
9400610976
ZEXEL
106682-9312
1066829312
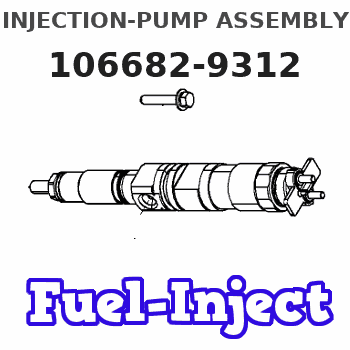
Rating:
Service parts 106682-9312 INJECTION-PUMP ASSEMBLY:
1.
_
5.
AUTOM. ADVANCE MECHANIS
7.
COUPLING PLATE
8.
_
9.
_
11.
Nozzle and Holder
6162-15-3100
12.
Open Pre:MPa(Kqf/cm2)
26.0{265}
15.
NOZZLE SET
Include in #1:
106682-9312
as INJECTION-PUMP ASSEMBLY
Cross reference number
BOSCH
9 400 610 976
9400610976
ZEXEL
106682-9312
1066829312
Zexel num
Bosch num
Firm num
Name
Calibration Data:
Adjustment conditions
Test oil
1404 Test oil ISO41113 or {SAEJ967d}
1404 Test oil ISO41113 or {SAEJ967d}
Test oil temperature
degC
40
40
45
Nozzle and nozzle holder
105780-8130
Bosch type code
EFEP215A
Nozzle
105780-0050
Bosch type code
DN6TD119NP1T
Nozzle holder
105780-2090
Bosch type code
EFEP215
Opening pressure
MPa
17.2
Opening pressure
kgf/cm2
175
Injection pipe
Outer diameter - inner diameter - length (mm) mm 8-4-1000
Outer diameter - inner diameter - length (mm) mm 8-4-1000
Overflow valve
131425-1620
Overflow valve opening pressure
kPa
255
221
289
Overflow valve opening pressure
kgf/cm2
2.6
2.25
2.95
Tester oil delivery pressure
kPa
157
157
157
Tester oil delivery pressure
kgf/cm2
1.6
1.6
1.6
Direction of rotation (viewed from drive side)
Left L
Left L
Injection timing adjustment
Direction of rotation (viewed from drive side)
Left L
Left L
Injection order
1-5-3-6-
2-4
Pre-stroke
mm
2.8
2.75
2.85
Beginning of injection position
Drive side NO.1
Drive side NO.1
Difference between angles 1
Cal 1-5 deg. 60 59.5 60.5
Cal 1-5 deg. 60 59.5 60.5
Difference between angles 2
Cal 1-3 deg. 120 119.5 120.5
Cal 1-3 deg. 120 119.5 120.5
Difference between angles 3
Cal 1-6 deg. 180 179.5 180.5
Cal 1-6 deg. 180 179.5 180.5
Difference between angles 4
Cyl.1-2 deg. 240 239.5 240.5
Cyl.1-2 deg. 240 239.5 240.5
Difference between angles 5
Cal 1-4 deg. 300 299.5 300.5
Cal 1-4 deg. 300 299.5 300.5
Injection quantity adjustment
Adjusting point
A
Rack position
14.6
Pump speed
r/min
900
900
900
Average injection quantity
mm3/st.
506
501
511
Max. variation between cylinders
%
0
-3
3
Basic
*
Fixing the lever
*
Boost pressure
kPa
84
84
Boost pressure
mmHg
630
630
Injection quantity adjustment_02
Adjusting point
C
Rack position
7.3+-0.5
Pump speed
r/min
375
375
375
Average injection quantity
mm3/st.
24
19
29
Max. variation between cylinders
%
0
-15
15
Fixing the rack
*
Boost pressure
kPa
0
0
0
Boost pressure
mmHg
0
0
0
Boost compensator adjustment
Pump speed
r/min
600
600
600
Rack position
R1-3.5
Boost pressure
kPa
24
17.3
30.7
Boost pressure
mmHg
180
130
230
Boost compensator adjustment_02
Pump speed
r/min
600
600
600
Rack position
R1(15.2)
Boost pressure
kPa
74.6
71.9
77.3
Boost pressure
mmHg
560
540
580
Test data Ex:
Governor adjustment
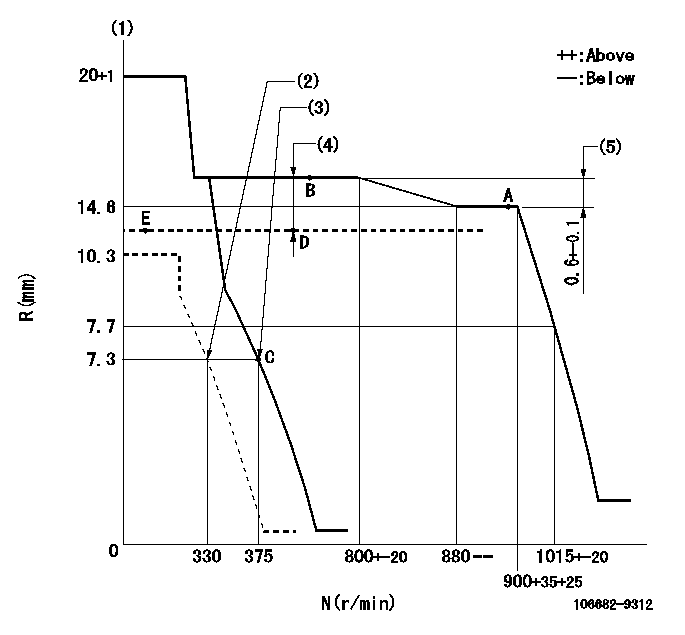
N:Pump speed
R:Rack position (mm)
(1)Target notch: K
(2)Set idle sub-spring
(3)Main spring setting
(4)Boost compensator stroke: BCL
(5)Rack difference between N = N1 and N = N2
----------
K=15 BCL=3.5+-0.1mm N1=900r/min N2=650r/min
----------
----------
K=15 BCL=3.5+-0.1mm N1=900r/min N2=650r/min
----------
Speed control lever angle
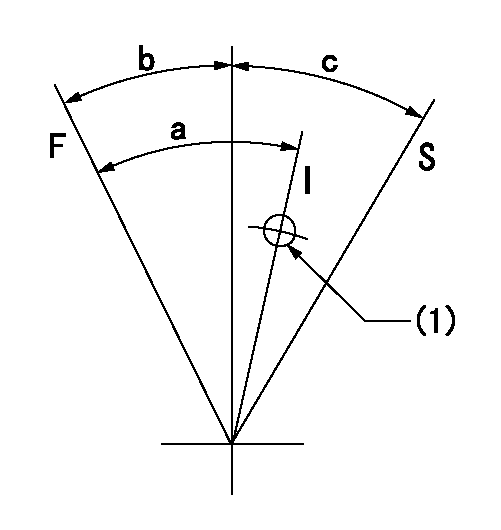
F:Full speed
I:Idle
S:Stop
(1)Use the hole at R = aa
----------
aa=115mm
----------
a=25deg+-5deg b=11deg+-5deg c=27deg+-3deg
----------
aa=115mm
----------
a=25deg+-5deg b=11deg+-5deg c=27deg+-3deg
0000001501 LEVER
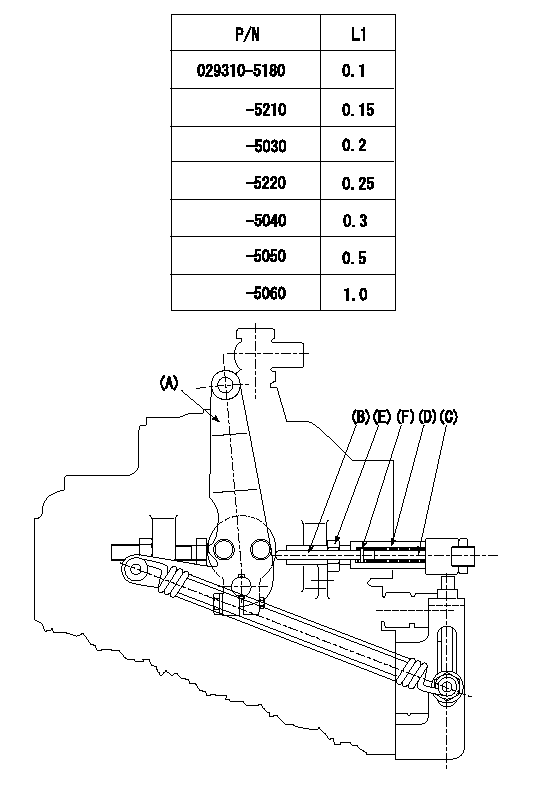
Speed lever adjustment
1. (1) For idling hold the speed lever (a) against the push rod (B).
(2)At this time, confirm that the spring (C) is not bent by the operating torque of the speed lever.
2. (1) To stop, bend the spring (C) using the speed lever.
(2)Position the rack at L2. (Adjustment is performed using the shim (F).)
(3)Set and fix using lock nut (E) so that it contacts the guide screw (D).
3. Confirm that the speed lever returns to the idling position when pulled in the stop direction and then released.
----------
L2=0.2~2mm
----------
----------
L2=0.2~2mm
----------
Timing setting

(1)Pump vertical direction
(2)Coupling's key groove position at No 1 cylinder's beginning of injection
(3)-
(4)-
----------
----------
a=(40deg)
----------
----------
a=(40deg)
Information:
(1) Thickness of spacer plate ... 8.585 0.025 mm (.3379 .0009 in)Thickness of gasket that is placed between spacer plate and cylinder block ... 0.208 0.025 mm (.0081 .0009 in)Height of liner over spacer plate, under installation pressure ... 0.13 0.08 mm (.005 .003 in)(2) Height of four dowels above top surface of cylinder block:End dowels (Put 7M7456 Bearing Mount Compound on two end dowels at installation) ... 18.5 0.5 mm (.73 .02 in)Middle dowels ... 16.0 0.5 mm (.63 .02 in)(3) Dimension (new) from centerline of crankshaft bearing bore to top of block (top deck) ... 425.45 0.15 mm (16.750 .006 in)Minimum dimension from centerline of crankshaft bearing bore to top of block (top deck) ... 425.02 mm (16.733 in) The flatness across the whole contact surface of the block must be within 0.10 mm (.004 in) and within 0.05 mm (.002 in) for any 177 mm (7.0 in) section of the surface. The surface finish specification is 3.2 micrometers (125 micro-inches) maximum.(4) Bore in block for camshaft bearings ... 76.835 0.018 mm (3.0250 .0007 in) Install bearings with the oil holes in the bearings on the horizontal centerline. Make sure the bearing joint position is above the oil holes.(5) Bore in the block for the main bearings: Standard, original size (new) ... 129.891 0.013 mm (5.1138 .0005 in)0.64 mm (.025 in) larger than original size ... 130.526 0.013 mm (5.1388 .0005 in)(6) Distance from front of rear face of cylinder block to end of dowels ... 19.1 0.05 mm (.75 .02 in)(7) Width of main bearing cap ... 215.900 0.013 mm (8.5000 .0005 in)Width of block for main bearing cap ... 215.900 0.013 mm (8.5000 .0005 in)Clearance between main bearing cap and cylinder block ... 0.025 mm (.0009 in) tight to 0.025 mm (.0009 in) loose
Tightening Procedure For Main Bearings(8) Torque for the bolts that hold the caps for the main bearings: Install the main bearing caps with the marks (arrow) toward the front of the engine. Install each cap in the correct position by putting the number stamped on the bottom of the cap toward the corresponding number cast on left side of the cylinder block at the pan rail.a. Put 2P2506 Thread Lubricant on the threads of the bolts.b. Tighten the bolts first on the bearing tab side of the cap to ... 260 14 N m (190 10 lb ft)c. Tighten the bolts on the opposite side to ... 260 14 N m (190 10 lb ft)d. Put a mark on each bolt and cap.e. Tighten the bolts on the opposite side, from the mark ... 120 5°f. Tighten the bolts on the bearing tab side of the cap, from the mark ... 120 5°(9) Dimension (new) from centerline of crankshaft bearing bore to bottom of block (pan rails) ... 165.10 0.10
Tightening Procedure For Main Bearings(8) Torque for the bolts that hold the caps for the main bearings: Install the main bearing caps with the marks (arrow) toward the front of the engine. Install each cap in the correct position by putting the number stamped on the bottom of the cap toward the corresponding number cast on left side of the cylinder block at the pan rail.a. Put 2P2506 Thread Lubricant on the threads of the bolts.b. Tighten the bolts first on the bearing tab side of the cap to ... 260 14 N m (190 10 lb ft)c. Tighten the bolts on the opposite side to ... 260 14 N m (190 10 lb ft)d. Put a mark on each bolt and cap.e. Tighten the bolts on the opposite side, from the mark ... 120 5°f. Tighten the bolts on the bearing tab side of the cap, from the mark ... 120 5°(9) Dimension (new) from centerline of crankshaft bearing bore to bottom of block (pan rails) ... 165.10 0.10